Keith Sylvester
Supplier Quality Manager at HALE PRODUCTS, INC.- Claim this Profile
Click to upgrade to our gold package
for the full feature experience.
-
English -
Topline Score
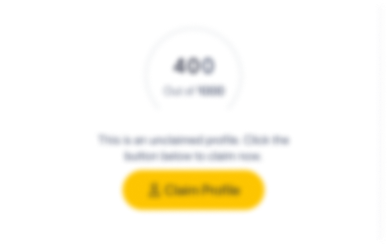
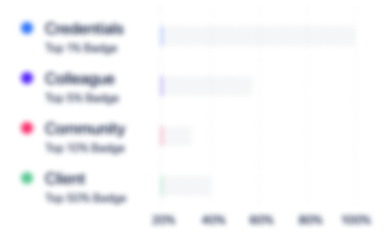
Bio


Experience
-
HALE PRODUCTS, INC.
-
United States
-
Machinery Manufacturing
-
1 - 100 Employee
-
Supplier Quality Manager
-
Feb 2022 - Present
-
-
-
Kohler Co.
-
United States
-
Manufacturing
-
700 & Above Employee
-
Quality Manager
-
May 2020 - Feb 2022
Cast Iron Foundry
-
-
Quality Supervisor
-
Apr 2017 - May 2020
-
-
-
Parker Hannifin
-
United States
-
Industrial Machinery Manufacturing
-
700 & Above Employee
-
Quality Supervisor
-
Dec 2013 - Mar 2017
Quality Supervisor – Responsible for ~20 associates working in the Inspection and NDT (Non-Destructive Testing) groups. Goals include reducing RPPM (Rejected Parts per Million) by improving Inspection and NDT efficiency and quality, increased throughput through training, problem solving, and development of standard work, and improved On Time Delivery and LISC (Line Items Shipped Complete) through scheduling and resource management. High Performance Work teams o Lead my… Show more Quality Supervisor – Responsible for ~20 associates working in the Inspection and NDT (Non-Destructive Testing) groups. Goals include reducing RPPM (Rejected Parts per Million) by improving Inspection and NDT efficiency and quality, increased throughput through training, problem solving, and development of standard work, and improved On Time Delivery and LISC (Line Items Shipped Complete) through scheduling and resource management. High Performance Work teams o Lead my empowered employees teams as coach and facilitator o Participate with my peers as empowered employees and perform problem solving Problem solving o 5-Why, Ishikawa, A3, DMAIC, 8D, CAPA (Corrective and Preventative Action), 10 Step Kaizen (continuous improvement) Value stream mapping Hiring / Firing Create Expectations and monitoring performance to these expectations Performance Reviews Manage on-site customer inspector Takt time planning Submit package for Capital Expenditure (AFE – Authorization for Expenditure) o Create value stream map (current & future state) and cost justification (ROI) o Currently have AFE in process for $1.2 million to replace two X-ray units Manage priorities with limited resources Create cross-training plans Handle personnel issues o Use Parker processes to provide verbal warnings, written warnings, Performance Commitment Plans, Decision Making Time Off, and finally Termination
-
-
Sr Quality Engineer
-
Jun 2011 - Dec 2013
Gas Turbine Fuel Systems Division Moncks Corner, SC Quality Engineer, Sr. responsible for combustion sytems and components sold to Siemens Power Generation with strict emphasis on customer satisfaction and scrap reduction through process yield improvements. The responsibilities of this position entail the life of the product from cradle to grave (contract review, design reviews, supplier AS9102 First Articles, supplier corrective actions, internal process review, internal manufacturing… Show more Gas Turbine Fuel Systems Division Moncks Corner, SC Quality Engineer, Sr. responsible for combustion sytems and components sold to Siemens Power Generation with strict emphasis on customer satisfaction and scrap reduction through process yield improvements. The responsibilities of this position entail the life of the product from cradle to grave (contract review, design reviews, supplier AS9102 First Articles, supplier corrective actions, internal process review, internal manufacturing documentation and drawing review and approval, internal corrective actions, Siemens PPQ [APQP / PPAP] submittals and approvals, submission of customer nonconformances through their Quality Notification System in SetP, customer corrective actions through 8D or CAPA process, etc…) Work very closely with both Siemens and Parker manufacturing and design engineering to realize product launch and continuous improvement activities whether they are drawing or processing changes to improve yield and reduce customer nonconformances. Attend daily production meetings to assist the Siemens support housing and pilot nozzle teams with day to day issues.
-
-
Sr Quality Engineer
-
Aug 2008 - Jun 2011
Hydraulic Systems Division Kalamazoo, MI Supplier Quality Assurance Engineer responsible primarily for Source Controlled Component suppliers. Review AS9102 First Article Inspection Reports for completeness, accuracy, and conformity to the drawing and AS requirements. Review and approve/reject supplier Corrective Action Requests. Assist suppliers with drawing interpretation/understanding as required. Submit Sustaining Engineering Work Requests in order to clarify prints and ensure that… Show more Hydraulic Systems Division Kalamazoo, MI Supplier Quality Assurance Engineer responsible primarily for Source Controlled Component suppliers. Review AS9102 First Article Inspection Reports for completeness, accuracy, and conformity to the drawing and AS requirements. Review and approve/reject supplier Corrective Action Requests. Assist suppliers with drawing interpretation/understanding as required. Submit Sustaining Engineering Work Requests in order to clarify prints and ensure that all dimensions and notes meet the requirements of the part yet are able to be manufactured easily, reliably, and repeatedly by our supply chain. Assist suppliers in the use of the Purchased Product Verification Requirement system to ensure that all paperwork is correct prior to shipment of product to HSD. Assist source inspectors in drawing interpretation/clarification prior to buy-off of product at our suppliers. Provide necessary information regarding supplier non-conformances to the rest of the team in the event of a Notice of Escape and work through the process/product improvement that acts as the corrective action. Managed the project on the Boeing 787 Heat Exchanger resulting from the leak found at MHI with the Boeing Seattle team, Boeing Long Island team, and Parker HSD team including program management, systems engineering, and customer quality. Present information twice per month to upper level staff regarding recent (previous month) supplier issues which affected production or shipment to/through Parker HSD. Review and assist suppliers in the improvement of processes and process control to improve throughput and overall quality. Assist the Lean initiative to improve the CRG-FAR-CAR systems through the creation of the RCCA database.
-
-
-
TRW
-
Business Consulting and Services
-
1 - 100 Employee
-
Quality Engineer
-
Feb 2007 - Aug 2008
Customer Quality Engineer responsible for Toyota TPMS (Tire Pressure Monitoring System) products. Update APQP (Advance Product Quality Planning) documents including PFMEA, Control Plans, and Process Flow maps. Monitor Toyota’s online NCT (Non-Conformance Ticket) and PPM tracking systems (eQPR and SKPI). Host Quality Alert meetings to initiate root-cause identification, containment and countermeasure activities for any and all Toyota TPMS related non-conformances discovered internally or at… Show more Customer Quality Engineer responsible for Toyota TPMS (Tire Pressure Monitoring System) products. Update APQP (Advance Product Quality Planning) documents including PFMEA, Control Plans, and Process Flow maps. Monitor Toyota’s online NCT (Non-Conformance Ticket) and PPM tracking systems (eQPR and SKPI). Host Quality Alert meetings to initiate root-cause identification, containment and countermeasure activities for any and all Toyota TPMS related non-conformances discovered internally or at customer locations. Follow Toyota SQAM guidelines in regards to all supplier requested changes, internal process/product changes, customer requested changes, and customer non-conformances. Coordinate necessary DV/PV trial activities with production floor and design group to ensure that all change points are properly tested to verify compliance with all tolerances and requirements stated on component and finished good drawings. Took part in Gate Reviews according to GDPIM guidelines for Toyota TPMS products. Assisted in validating new equipment released to the production floor by developing and implementing Validation Plans, G54, E211, and Dual Launch Netting. Assisted with Six Sigma Black Belt projects including Value Stream Mapping of the Toyota TPMS product line. Show less Customer Quality Engineer responsible for Toyota TPMS (Tire Pressure Monitoring System) products. Update APQP (Advance Product Quality Planning) documents including PFMEA, Control Plans, and Process Flow maps. Monitor Toyota’s online NCT (Non-Conformance Ticket) and PPM tracking systems (eQPR and SKPI). Host Quality Alert meetings to initiate root-cause identification, containment and countermeasure activities for any and all Toyota TPMS related non-conformances discovered internally or at… Show more Customer Quality Engineer responsible for Toyota TPMS (Tire Pressure Monitoring System) products. Update APQP (Advance Product Quality Planning) documents including PFMEA, Control Plans, and Process Flow maps. Monitor Toyota’s online NCT (Non-Conformance Ticket) and PPM tracking systems (eQPR and SKPI). Host Quality Alert meetings to initiate root-cause identification, containment and countermeasure activities for any and all Toyota TPMS related non-conformances discovered internally or at customer locations. Follow Toyota SQAM guidelines in regards to all supplier requested changes, internal process/product changes, customer requested changes, and customer non-conformances. Coordinate necessary DV/PV trial activities with production floor and design group to ensure that all change points are properly tested to verify compliance with all tolerances and requirements stated on component and finished good drawings. Took part in Gate Reviews according to GDPIM guidelines for Toyota TPMS products. Assisted in validating new equipment released to the production floor by developing and implementing Validation Plans, G54, E211, and Dual Launch Netting. Assisted with Six Sigma Black Belt projects including Value Stream Mapping of the Toyota TPMS product line. Show less
-
-
-
ASMO Manufacturing
-
United States
-
Automotive
-
1 - 100 Employee
-
Quality Engineer
-
Apr 2005 - Feb 2007
Quality Engineer – Create Manufacturing Quality Charts, Inspection Records (both Internal and Customer Specific), perform Process and System Audits to ensure that all Quality procedures and practices are being followed by Production, inspect parts, New Product Readiness (create Part Evaluation Plans, Supplier Parts Master Plans, Toyota Inspection Standards, perform Vehicle Evaluations, Design and Drawing Review, Japanese and American Trial Activities, Durability and Reliability testing… Show more Quality Engineer – Create Manufacturing Quality Charts, Inspection Records (both Internal and Customer Specific), perform Process and System Audits to ensure that all Quality procedures and practices are being followed by Production, inspect parts, New Product Readiness (create Part Evaluation Plans, Supplier Parts Master Plans, Toyota Inspection Standards, perform Vehicle Evaluations, Design and Drawing Review, Japanese and American Trial Activities, Durability and Reliability testing according to Toyota Standards [TSC]), all Toyota specific testing and/or documentation according to Toyota Supplier Quality Assurance Manual, handled all Toyota Quality Problem Reports by holding meetings with production to determine the 5 Whys of both Occurrence and Detection and implement Countermeasure Activities to counteract the root causes and finally by issuing the Countermeasure Reply to Toyota, issued Quality Alert Memos to production and design in order to enhance awareness to any defect found either internally or at the customer, assisted in setup of Quality systems and procedures as well as testing station and all documentation necessary for Quality department at a new Texas facility, handle Design Changes started internally or by Toyota (after Engineering Change Instructions are issued I update the ECI Logs, Sample Datasheets, and Inspection Records as well as create a PEP and Process Change Requests if applicable), performed Customer Satisfaction Visits as well as visits to discuss recent defect occurrences and explain ASMO’s countermeasure activities, implemented procedures internally at ASMO to improve the detection capabilities of Quality Defects and lower known problem area defect occurrences. Show less Quality Engineer – Create Manufacturing Quality Charts, Inspection Records (both Internal and Customer Specific), perform Process and System Audits to ensure that all Quality procedures and practices are being followed by Production, inspect parts, New Product Readiness (create Part Evaluation Plans, Supplier Parts Master Plans, Toyota Inspection Standards, perform Vehicle Evaluations, Design and Drawing Review, Japanese and American Trial Activities, Durability and Reliability testing… Show more Quality Engineer – Create Manufacturing Quality Charts, Inspection Records (both Internal and Customer Specific), perform Process and System Audits to ensure that all Quality procedures and practices are being followed by Production, inspect parts, New Product Readiness (create Part Evaluation Plans, Supplier Parts Master Plans, Toyota Inspection Standards, perform Vehicle Evaluations, Design and Drawing Review, Japanese and American Trial Activities, Durability and Reliability testing according to Toyota Standards [TSC]), all Toyota specific testing and/or documentation according to Toyota Supplier Quality Assurance Manual, handled all Toyota Quality Problem Reports by holding meetings with production to determine the 5 Whys of both Occurrence and Detection and implement Countermeasure Activities to counteract the root causes and finally by issuing the Countermeasure Reply to Toyota, issued Quality Alert Memos to production and design in order to enhance awareness to any defect found either internally or at the customer, assisted in setup of Quality systems and procedures as well as testing station and all documentation necessary for Quality department at a new Texas facility, handle Design Changes started internally or by Toyota (after Engineering Change Instructions are issued I update the ECI Logs, Sample Datasheets, and Inspection Records as well as create a PEP and Process Change Requests if applicable), performed Customer Satisfaction Visits as well as visits to discuss recent defect occurrences and explain ASMO’s countermeasure activities, implemented procedures internally at ASMO to improve the detection capabilities of Quality Defects and lower known problem area defect occurrences. Show less
-
-
-
LECO
-
Spain
-
Business Consulting and Services
-
Electrical Engineering Intern
-
Jun 2000 - Aug 2001
Electrical Engineering Co-op – Tested, modified, assembled, disassembled and helped design circuit boards and instruments. Electrical Engineering Co-op – Tested, modified, assembled, disassembled and helped design circuit boards and instruments.
-
-
Education
-
Michigan Technological University
Bachelor of Science (BS), Electrical Engineering -
Midland High School
Diploma
Community
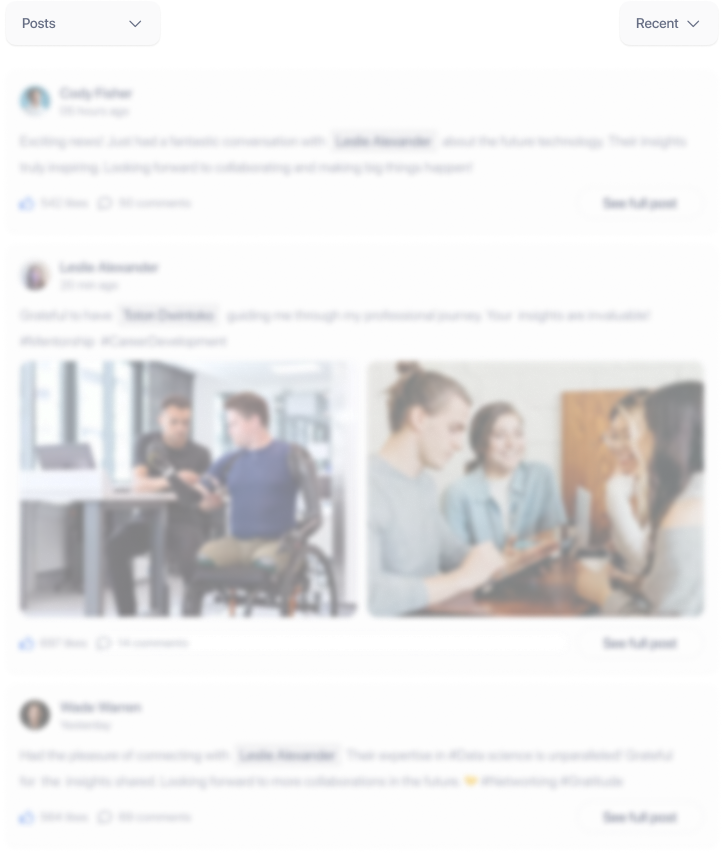