Keith Hebenstreit
Mechanical Engineer at Magnetic Analysis Corporation- Claim this Profile
Click to upgrade to our gold package
for the full feature experience.
Topline Score
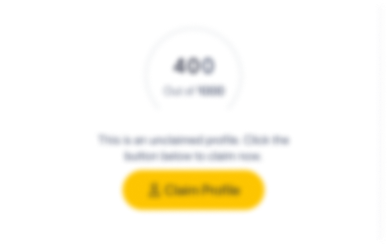
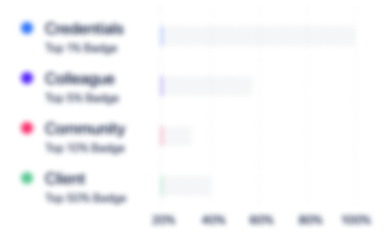
Bio


Experience
-
Magnetic Analysis Corporation
-
United States
-
Machinery Manufacturing
-
1 - 100 Employee
-
Mechanical Engineer
-
Mar 2015 - Present
Designing, developing, and implementing eddy current, electromagnetic, flux leakage, and ultrasonic inspection equipment for NDT (Non-destructive testing) on metals worldwide. Designing, developing, and implementing eddy current, electromagnetic, flux leakage, and ultrasonic inspection equipment for NDT (Non-destructive testing) on metals worldwide.
-
-
-
Binghamton University
-
Higher Education
-
700 & Above Employee
-
Mechanical Engineering Masters Student/Graduate Teaching Assistant
-
Jul 2013 - Dec 2014
Concentration: Thermofluids Teaching Assistant for ME 381 (Computer Aided Engineering-Creo 2.0), ME 392 (Machine Design) Concentration: Thermofluids Teaching Assistant for ME 381 (Computer Aided Engineering-Creo 2.0), ME 392 (Machine Design)
-
-
-
NASA-NYS Space Grant Fellowship
-
Binghamton University
-
NASA-NYS Space Grant Fellowship Researcher
-
Sep 2012 - May 2013
Collaborated with Professor Frank Cardullo and an electrical engineering colleague (Adam Morgan) to develop a simulation program for the European Robotic Arm (ERA) space manipulator that is proposed for the International Space Station. The model was based on a PhD Dissertation titled "The Design of a Man-Machine Interface for a Space Manipulator" by Paulus Breedveld, November 19th, 1996. Developed lengthy MATLAB code to model the dynamics of the six degree of freedom end effector motion upon human instruction through a space ball. The equations of motion were based on those found in the dissertation. This MATLAB code was to be used in accordance with a GUI created by Adam Morgan to complete the simulation. The project required more time and is currently being continued by two new undergraduate students who I have briefed and am still in contact with.
-
-
-
Binghamton University
-
Higher Education
-
700 & Above Employee
-
Undergraduate Mechanical Engineering Student
-
Aug 2009 - May 2013
Team leader of a senior design project called "Data Acquisition Package for the AMOS II Driving Simulator". My team designed and developed a data acquisition package that was deployed onto the driving simulator and used to measure various physical parameters of the operator such as postural sway, force applied to the brake pedal, and involuntary eye motion or Optokinetic Nystagmus. Completely designed and tested for an independent design project (According to the ASTM Standard Test Methods for Evaluating Design and Performance Characteristics of Selectorized Strength Equipment) a piece of fitness equipment using Pro/Mechanica. All joints and connections were tested using Finite Element Analysis and additional impact loading and fatigue life analyses were conducted to test failure conditions.Worked on projects using Pro-Engineer such as a 22 part Centering Attachment assembly and the re-design of the Landing Gear for an airplane in which Pro/Mechanism and Pro/Mechanica were used to do a Finite Element Analysis on all linkages and connections.
-
-
Undergraduate Research Assistant
-
Jan 2012 - May 2012
Conducted dissolutive wetting experiments using a Goniometer with Professor Timothy Singler.Analyzed contact angles and the coffee-ring effect resulting from dripping saturated water with variable concentrations of salt onto polished salt crystals.
-
-
-
National Institute of Standards and Technology (NIST)
-
United States
-
Research Services
-
700 & Above Employee
-
Summer Undergraduate Research Fellowship
-
May 2012 - Aug 2012
Designed three in process measurements systems (Machine Vision, Thermal Imaging, and an Ultrasonic Porosity Monitor) for deployment onto the Direct Metal Laser Sintering machine at NIST as part of NIST’s Additive Manufacturing 3-D Printing Project. Programmed the necessary MATLAB code and LabVIEW VI files required for the data acquisition for each measurement process. Formulated a relationship between the ultrasonic wave speed and porosity of Cobalt-Chrome samples for use in collaboration with the ultrasonic porosity monitor and for publication in a NIST Technical Note titled "Porosity Measurements and Analysis for Metal Additive Manufacturing Process Control." http://nvlpubs.nist.gov/nistpubs/jres/119/jres.119.019.pdf Developed a calibration method for the Direct Metal Laser Sintering machine based on NIST’s own standard test artifact. Strengthened communication experience by delivering a twenty minute lecture and acquired valuable research experience by successfully completing an independent research project.
-
-
-
John Woodruff Architect
-
New Rochelle, NY
-
Assistant
-
Sep 2008 - Apr 2009
Used CAD programs to develop architectural drawings. Used CAD programs to develop architectural drawings.
-
-
Education
-
State University of New York at Binghamton
Master's degree, Mechanical Engineering -
State University of New York at Binghamton
Bachelors Degree, Mechanical Engineering -
New Rochelle High School
Advanced Regents Diploma
Community
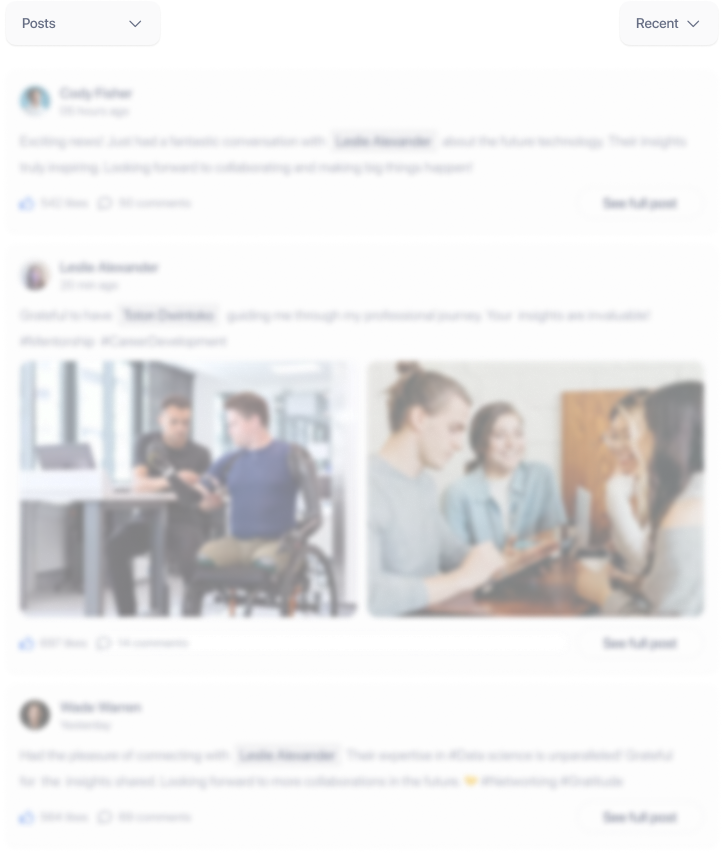