Keith Finnerin
Procurement Manager at BayWa r.e. Solar Systems LLC- Claim this Profile
Click to upgrade to our gold package
for the full feature experience.
Topline Score
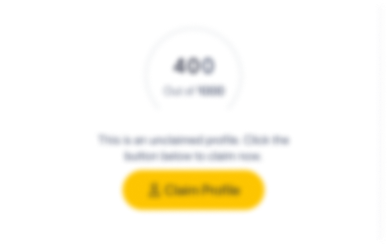
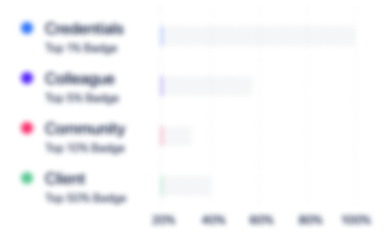
Bio
0
/5.0 / Based on 0 ratingsFilter reviews by:
Experience
-
-
Procurement Manager
-
Jan 2018 - Present
Responsible for planning future orders from sales history, forecasts, Sales input and market trends for Enphase, Panasonic, Hanwha Qcell, Longi, JA, Silfab and Trina. Control inventory levels at six warehouses across the country to have the right product at the right place at the right time. Run various reports in NetSuite and export to Excel to analyze the data to develop the best plan of action for Purchasing and Inventory Management decisions.Work with Sales and Operations Teams to develop accurate messaging around product allocation, constraint, lead times, and other procurement-related issues.Led weekly Inventory Health meetings to analyze current and future inventory shortages and overstock conditions. Work with Sales on the disposition of end of life skus.
-
-
-
EarthCruiser Overland Vehicles
-
Motor Vehicle Manufacturing
-
1 - 100 Employee
-
Supply Chain Manager
-
Aug 2017 - Dec 2017
Conduct weekly inventory cross checks and software audits to ensure all parts needed for EarthCruiser builds are present and material for upcoming builds have been ordered according to lead times and production schedule.Use finished goods delivery dates and JobBoss software to create MRP reports to purchase all components on time.Create and manage Kanban levels and Vendor Managed Inventory Program.Communicate effectively with office and production staff regarding matters related to purchasing, inventory control and receiving.Collaborate with Engineers and Production Leeds on primary and secondary vendor sourcing.Purchase all 1200 parts and hundreds of supplies for the Production staff.Work with Accounting to correct any vendor discrepancies.
-
-
-
Ebay Store
-
United Kingdom
-
Software Development
-
1 - 100 Employee
-
Owner
-
Apr 2009 - Aug 2017
-
-
-
PCC Structurals
-
United States
-
Manufacturing
-
Buyer
-
Apr 2008 - Apr 2009
Quarterly planning and purchasing of all bulk materials including Wax and Alumina Oxide materials.Support all departments material needs by purchasing consumables at the best value for their needs.Constantly seeking cost reductions for all materials during the purchasing process.Purchase order management to verify receivings and to check for on time deliveries. Quarterly planning and purchasing of all bulk materials including Wax and Alumina Oxide materials.Support all departments material needs by purchasing consumables at the best value for their needs.Constantly seeking cost reductions for all materials during the purchasing process.Purchase order management to verify receivings and to check for on time deliveries.
-
-
-
Bright Wood
-
Canada
-
Construction
-
Senior Buyer
-
Feb 2002 - Mar 2005
Procure Millwork products Domestically and Internationally (South America, China & Mexico) for 30 Huttigbranches across the country.Negotiate prices for product lines with suppliers depending on the branch’s needs and market conditions.Obtain purchasing needs from analyzing sales history, current usage and trends.Manage inventory levels of all millwork products based seasonality and market conditions.Maintain and update ordering controls as dictated by business conditions.Utilize SX.e (NexTrend) and Trac-It (Oracle) software systems.
-
-
-
Iomega
-
United States
-
Computer Hardware Manufacturing
-
1 - 100 Employee
-
Material Planning and Inventory Control Manager
-
Jul 1999 - Dec 2001
Managed the Material Planning Team and Inventory Supervisor/Inventory Control Clerks.Negotiated Forecast with Sales, Operations, and Global Planning Managers.Directed Production Scheduling based on forecast, orders and capacity planning to achieveOn-Time-Shipments of 95%.Managed the Master Production Schedule to drive correct requirements, through Oracle MRP, to thePurchasing department for Just-In-Time deliveries.Purchased components from Global suppliers – Malaysia, Taiwan, Belgium and USA.Instituted the use of the “Discrete Job Shortage Report” to capture shortages due to components being usedon multiple work orders.Maintained 98.5% Inventory Accuracy through cycle counting and verification of all inventory movementsbetween departments.Oversaw the administration of a $50 million Inventory.Strategic Planning to transition the outsourcing of Material Planning and Production Scheduling functions tothird party company due to closure of facility at end of year 2001.
-
-
-
Boeing
-
United States
-
Aviation and Aerospace Component Manufacturing
-
1 - 100 Employee
-
Materials Management Analyst II
-
May 1997 - Jul 1999
Launched the BAAN ERP system as part of the implementation team.Surplus Project Manager responsible for disposition of $8M of surplus and obsolete inventory.Utilized Simplified Materials Management to order B and C parts by Kanban system.Supported Engineering through Root Cause Analysis and correction of Bills of Material. Launched the BAAN ERP system as part of the implementation team.Surplus Project Manager responsible for disposition of $8M of surplus and obsolete inventory.Utilized Simplified Materials Management to order B and C parts by Kanban system.Supported Engineering through Root Cause Analysis and correction of Bills of Material.
-
-
-
Costco
-
Consumer Services
-
Buyer
-
Aug 1988 - May 1997
Directed up to 8 Associate Buyers on managing inventories at Depots and dealing with vendors.Negotiated and Purchased over 150 items including commodities and perishable products.Responsible for Forecasting, Planning, and tracking all holiday and seasonal items for over 200 locationsnationwide.Increased holiday and seasonal sales 50% to 150% (varies by store).Developed costing system for accurate Gross Margins in AS400 system.Integrated Auto-Replenishment ordering system for Bakery departments.Managed Regional Produce Inventories and Logistics.
-
-
Education
-
Central Washington University
Bachelor's degree, Business Administration and Management, General -
APICS
Certified, Certified in Production and Inventory Management
Community
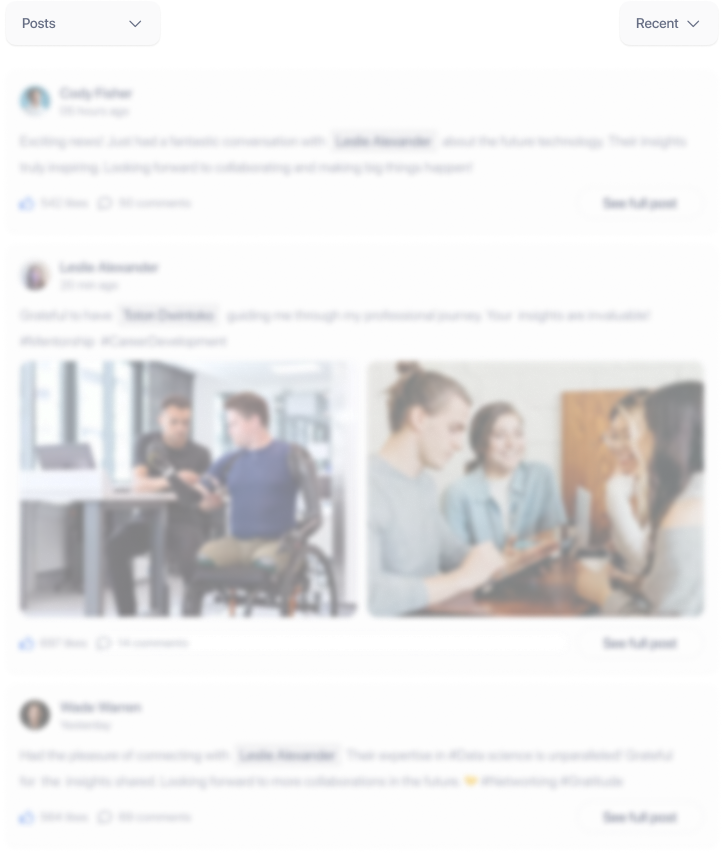