William Kearns
Director of Tooling and Process Integration at LaCasse & Weston Inc- Claim this Profile
Click to upgrade to our gold package
for the full feature experience.
-
Spanish Professional working proficiency
Topline Score
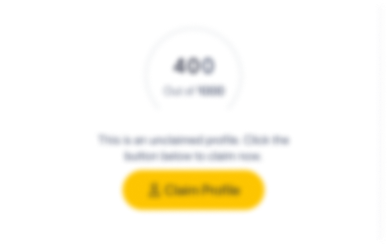
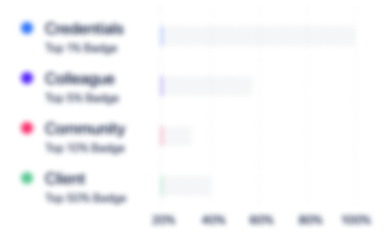
Bio


Credentials
-
CSWA
Connecticut SOLIDWORKS User GroupMay, 2014- Oct, 2024 -
Associate Member
Midwest Manufacturing LeadersJan, 2013- Oct, 2024 -
Associate Member
TAPPIJan, 2010- Oct, 2024 -
Certified Member (CM)
Institute of Packaging ProfessionalsAug, 2005- Oct, 2024 -
Certified Member (CM)
International Molded Fiber AssociationJan, 2005- Oct, 2024
Experience
-
LaCasse & Weston Inc
-
Industrial Machinery Manufacturing
-
1 - 100 Employee
-
Director of Tooling and Process Integration
-
Jul 2019 - Present
-
-
-
EnviroPAK Corporation
-
Packaging & Containers
-
1 - 100 Employee
-
Production Responsibilities and Essential Functions
-
Oct 2015 - Jul 2019
Production Responsibilities and Essential Functions• Hands-on supervision of Production, Quality, Maintenance, Engineering and Tooling departments. o 6 Department Managers o 20+ Direct Reports o 80+ Total Employees• Daily analysis of key metrics to ensure production numbers align with company goals. o Maintain overall uptime efficiency of 90% across three production lines. o Work directly with customers to establish and maintain acceptable lead times. o Strategically implement overtime when needed.• Implement cost-savings opportunities across all departments. o Realigned raw material needs with monthly production, resulting in a 20% decrease of raw material on the floor and annual cost savings (2018). o Successfully created and implemented a company policy to eliminated all cell phones and other electronics from the workplace, resulting in increased productivity (2017). o Collaborated with engineering firm to develop options for production automation, resulting in potential cost savings of $200k (2019).• Quality o Continuous improvement of quality controls across multiple departments. o Review all quality issues and conduct necessary internal audits. o Maintain Corrective Action Reports and communicate solutions to the customer.
-
-
Operational Responsibilities
-
Oct 2015 - Jul 2019
• Analyze monthly Profit & Loss report to identify any major financial deviations from the budget. • Negotiate and finalize required building maintenance contracts: plumbing, electrical, HVAC, landscaping, security, information technology, etc. • Maintain company’s environmental compliance with local, state and federal officials.• Maintain company’s OSHA compliance. • Work with Department of Labor managing unemployment and workman’s compensation claims.• Record and monitor daily usage of water, natural gas and electricity.o Work with local and state agencies to capitalize on cost savings programs for utilities.
-
-
Strategic Initiatives and High-Level Operations
-
Oct 2015 - Jul 2019
• Working with overseas engineers, developed a quality assurance program for all products arriving from international vendors. o Traveled to Southeast Asia, Mexico, and the United Kingdom to ensure QA program was implemented correctly, resulting in zero quality issues since 2017.• Managed the company’s expansion to new out of state facility, including lease agreements, tenant improvements, purchase of multimillion-dollar equipment, and design of multi-site operational policy (2019).
-
-
Operations Manager
-
Oct 2015 - Jul 2019
Employee Health and Safety, Asset Management, Capital Budgeting, Claims Management, Facility Management, Labor Relations, Production Scheduling, Mergers and Acquisitions, Warehouse Management, Shipping and Receiving, Training and Development, and Quality Control.
-
-
Engineering and Tooling Manager
-
Apr 2013 - Oct 2015
Managed new opportunities, beginning with conceptual design and culminating with the production of finished goods. Collaborated with customers to ensure demands were met and scope of project did not exceed agreed-upon terms. Using SolidWorks CAD software, created new customer designs to meet expectations of fit, form, and function. Using SolidCAM software, programmed in-house CNC machines to create prototype and production tooling. Approved and maintained the departmental budget. Decreased overall lead times by 20% over a 12-month period.
-
-
New Product Design and Tooling
-
Feb 2003 - Apr 2013
Developed new products and corresponding tooling. Worked directly with the tooling department to ensure projects were completed on time and under budget.
-
-
Education
-
Blackburn College
Bachelor of Arts (B.A.), Communications
Community
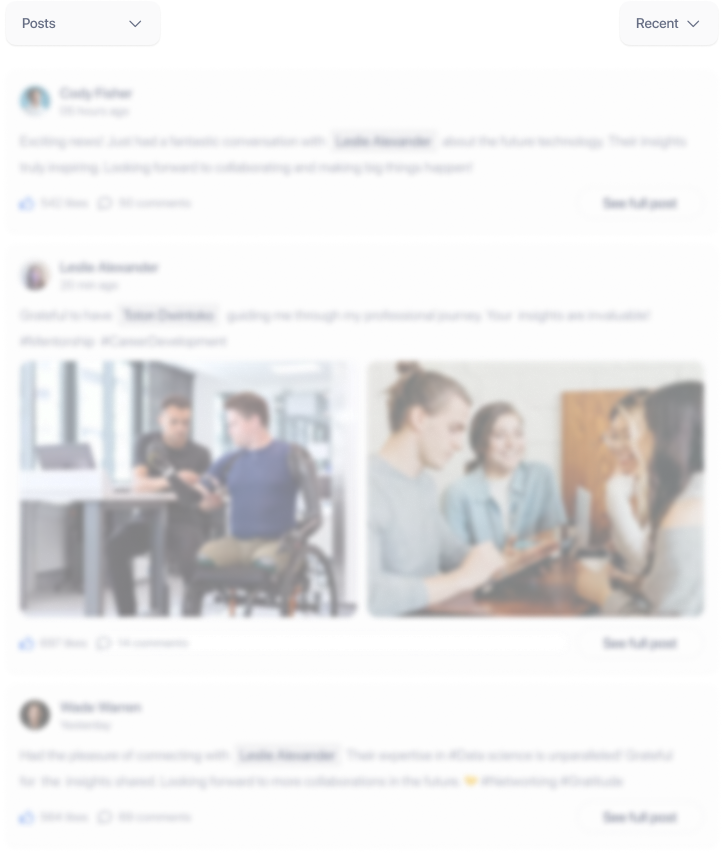