Kaveh Moraghebi
Sr. Director of Quality at ALOM- Claim this Profile
Click to upgrade to our gold package
for the full feature experience.
Topline Score
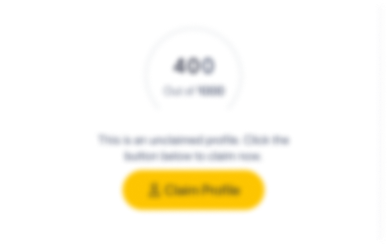
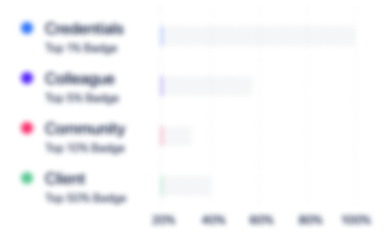
Bio

MOHAMMAD SAFARI- P.Eng., M.Eng., C.E.T.
Details of original recommendation: "Kaveh was interested in teamwork environment. He was an active and motivated person who could manage time and priorities in critical conditions. Kaveh also was successful for establishing Quality system for variety suppliers which are working for Iran khodro and he could rise up their quality level."

Nima Shamsaei
It gives me immense pleasure in recommending my long time friend Mr. Kaveh Moraghebi. I know him since 1995, when we both pursuing out education at Isafahan University of Technology. Kaveh not only was a successful student, but he was also involved in many student activities and organizations. However, our professional relationship was started in 2005, when Kaveh was a trainer and guide in the implementation Quality Management Systems based on ISO/TS 16949 and Lean Six Sigma initiatives for SAIPA, one of the two big automakers in Iran. I was serving as the manager of the part design department at the moment. He is a bright and hardworking businessman and gentleman who is an expert in Quality Management tools & systems. Therefore, I recommend Kaveh without any reservation for any quality management position.

MOHAMMAD SAFARI- P.Eng., M.Eng., C.E.T.
Details of original recommendation: "Kaveh was interested in teamwork environment. He was an active and motivated person who could manage time and priorities in critical conditions. Kaveh also was successful for establishing Quality system for variety suppliers which are working for Iran khodro and he could rise up their quality level."

Nima Shamsaei
It gives me immense pleasure in recommending my long time friend Mr. Kaveh Moraghebi. I know him since 1995, when we both pursuing out education at Isafahan University of Technology. Kaveh not only was a successful student, but he was also involved in many student activities and organizations. However, our professional relationship was started in 2005, when Kaveh was a trainer and guide in the implementation Quality Management Systems based on ISO/TS 16949 and Lean Six Sigma initiatives for SAIPA, one of the two big automakers in Iran. I was serving as the manager of the part design department at the moment. He is a bright and hardworking businessman and gentleman who is an expert in Quality Management tools & systems. Therefore, I recommend Kaveh without any reservation for any quality management position.

MOHAMMAD SAFARI- P.Eng., M.Eng., C.E.T.
Details of original recommendation: "Kaveh was interested in teamwork environment. He was an active and motivated person who could manage time and priorities in critical conditions. Kaveh also was successful for establishing Quality system for variety suppliers which are working for Iran khodro and he could rise up their quality level."

Nima Shamsaei
It gives me immense pleasure in recommending my long time friend Mr. Kaveh Moraghebi. I know him since 1995, when we both pursuing out education at Isafahan University of Technology. Kaveh not only was a successful student, but he was also involved in many student activities and organizations. However, our professional relationship was started in 2005, when Kaveh was a trainer and guide in the implementation Quality Management Systems based on ISO/TS 16949 and Lean Six Sigma initiatives for SAIPA, one of the two big automakers in Iran. I was serving as the manager of the part design department at the moment. He is a bright and hardworking businessman and gentleman who is an expert in Quality Management tools & systems. Therefore, I recommend Kaveh without any reservation for any quality management position.

MOHAMMAD SAFARI- P.Eng., M.Eng., C.E.T.
Details of original recommendation: "Kaveh was interested in teamwork environment. He was an active and motivated person who could manage time and priorities in critical conditions. Kaveh also was successful for establishing Quality system for variety suppliers which are working for Iran khodro and he could rise up their quality level."

Nima Shamsaei
It gives me immense pleasure in recommending my long time friend Mr. Kaveh Moraghebi. I know him since 1995, when we both pursuing out education at Isafahan University of Technology. Kaveh not only was a successful student, but he was also involved in many student activities and organizations. However, our professional relationship was started in 2005, when Kaveh was a trainer and guide in the implementation Quality Management Systems based on ISO/TS 16949 and Lean Six Sigma initiatives for SAIPA, one of the two big automakers in Iran. I was serving as the manager of the part design department at the moment. He is a bright and hardworking businessman and gentleman who is an expert in Quality Management tools & systems. Therefore, I recommend Kaveh without any reservation for any quality management position.

Credentials
-
ISO 13485:2016 Lead Auditor (TPECS)
bsi.Feb, 2019- Oct, 2024 -
Six Sigma Green Belt
ASQDec, 2012- Oct, 2024
Experience
-
ALOM
-
United States
-
Truck Transportation
-
1 - 100 Employee
-
Sr. Director of Quality
-
Sep 2018 - Present
• Establishes, implements, and communicates the strategic direction of the organization’s quality and sustainability divisions. • Develops new quality standards utilizing manual and automate test procedures to support the overall company and product strategy. • Leads external/ compliance audit activities and plans, coordinates and conducts multi-site quality & regulatory internal audits. • Architects’ supplier quality strategy, processes and associated documentation and system(s). • Leads and ensures appropriate execution of the supplier assessment, performance evaluation and qualification process for the Advanced Product Quality Process (APQP) framework. • Works closely with operation and business teams to communicate any problem’s impact using 8D method & CAPA. • Developed and implemented balanced scorecard metrics and monthly performance reviews. • Responsible for management and maintenance of ISO 9001, TL 9000, ISO 13485, and IATF 16949 Quality Management Systems and ISO 14001 Environmental Management System. • Revamped entire quality system to meet 21 CFR 820 cGMP requirements for class II medical device and passed FDA QSIT with no observation. Show less
-
-
-
Bay Area Compliance Laboratories Corp.
-
United States
-
Electrical/Electronic Manufacturing
-
1 - 100 Employee
-
Quality Assurance Manager
-
Oct 2010 - Sep 2018
• Managed and maintained laboratories quality system based on ISO 17025 and ISO 17065 requirements. • Implemented quality system based on requirements of OSHA Nationally Recognized Testing. Laboratory and Standard Council of Canada and got approval from both NRTL and SCC for product Safety Certification in US and Canada. • Managed and monitored activities of a team of 12 responsible for quality system, document control, calibration, maintenance and project management. • Performed system, design, and process FMEA and risk analysis to make sure all designed test equipment meets the standards and the test methods are valid. • Trained employees in proper operations, processes, and procedures of quality management systems. • Performed internal quality systems audits to determine compliance with quality systems requirements. • Implemented Six Sigma methodology in Lighting Lab, resulting in 22% reduction in testing lead time and 8% decrease in customer complaints. • Managed and monitored BACL’s Laboratories (internationally) on QMS Level. Show less
-
-
-
Get Kaizened, Inc.
-
United States
-
Business Consulting and Services
-
1 - 100 Employee
-
Project Manager
-
Nov 2009 - Oct 2010
• Completed consulting for 5 companies in semiconductor, and medical device industries, implementing QMS (ISO 9001, ISO 14385 & ISO/TS 16949) and EMS (ISO 14001) • Managed Kaizen teams to identify opportunities for improvement in manufacturing processes, eliminate waste (Muda), and implement Kaizen initiatives • Trained, led, and coordinated managers and shop floor employees in a unionized manufacturing environment on multiple projects (Jishuken, 5S, Chaku-Chaku, Lean manufacturing) • Designed and updated all plant layouts to achieve better visibility, efficiency and effectiveness • Developed and implemented cost-reducing initiatives for plant layout, capacity studies, direct labor standards, maximizing employee efficiency, Total Productive Maintenance (TPM) and Overall Equipment Effectiveness (OEE) Show less
-
-
-
TUV NORD
-
1 - 100 Employee
-
Lead Auditor & Lecturer
-
Oct 2007 - Sep 2009
• Conducted more than 300 audit days for clients in ISO 9000 & ISO 14000 disciplines • Provided more than 40 quality management system training courses & environmental management system courses based on ISO 9001 &ISO 14001 • Provided training courses in quality engineering tools such as Statistical Process Control (SPC), Measurement System Analysis (MSA), Quality Function Deployment (QFD), Cost Of Quality (COQ), Failure Mode and Effects Analysis (FMEA), Advanced Product Quality Planning(APQP) Show less
-
-
-
-
Quality Director
-
Aug 2004 - Oct 2007
• Created, developed, implemented, audited and obtained certification for ISO 9001 and ISO/TS 16949 Quality Management Systems • Managed Advanced Product Quality Planning (APQP) activities to ensure production readiness for New Product Introduction (NPI) • Led the development of Process Failure Mode and Effect Analysis (PFMEA) to identify critical risks in the production processes and updating Control Plans • Contributed Quality-related ideas with 93% implementation rate • Implemented Six Sigma methodology in paint shop, resulting in 13% reduction in paint consumption and 9% increase in quality improvement Show less
-
-
-
-
QA Manager & Management Representative
-
May 2002 - Aug 2004
• Created, developed, implemented, audited and obtained certification for ISO 9001 and ISO/TS 16949 Quality Management Systems • Ensured 100% on-time completion for 12 major projects by partnering with business development team regarding customer requirements to minimize potential risks in design and manufacturing processes, which saved the corporation in excess of $135,000 annually • Reviewed customer’s technical specifications to assist in the development and preparation of proposals and pricing; conducted price analysis and cost of quality • Led 14-person systems engineering team to develop and maintain complex systems utilizing Critical to Customer items (CTC) & Quality Function Deployment (QFD) trading techniques, thereby ensuring the system meeting customer needs and requirements • Created, developed, implemented, audited and obtained certification for an ISO/TS 16949 Quality Management System. • Provide training to the Supplier for problem resolution and continuous improvements (supplier development plan) Show less
-
-
-
Kerman Khodro,
-
Iran
-
Automation Machinery Manufacturing
-
1 - 100 Employee
-
Process Engineer
-
Sep 1997 - May 2002
• Responsible for measuring, analyzing and reporting the current product quality level and the quality level of manufacturing processes of the body shop, paint shop and assembly up to the finished vehicle and improving all critical areas, resulting in improving the First Time Quality by 53% • Designed and improved Quality Assurance processes determining an optimal process, for repeatability and reproduce-ability to improve the Cost of Quality by 48% • Dealt with Customers’ complaints and Quality Problem Reports (QPRs) and resolved 100% of the issues to their satisfaction! • Responsible for the overall success of the control plans to assure critical features are monitored & improved upon in the assembly/production process. • Prepared technical documents and statistics for quality regulation and tracking Show less
-
-
Education
-
Isfahan University of Technology
BS, Mechanical Engineering (Heat & Fluids)
Community
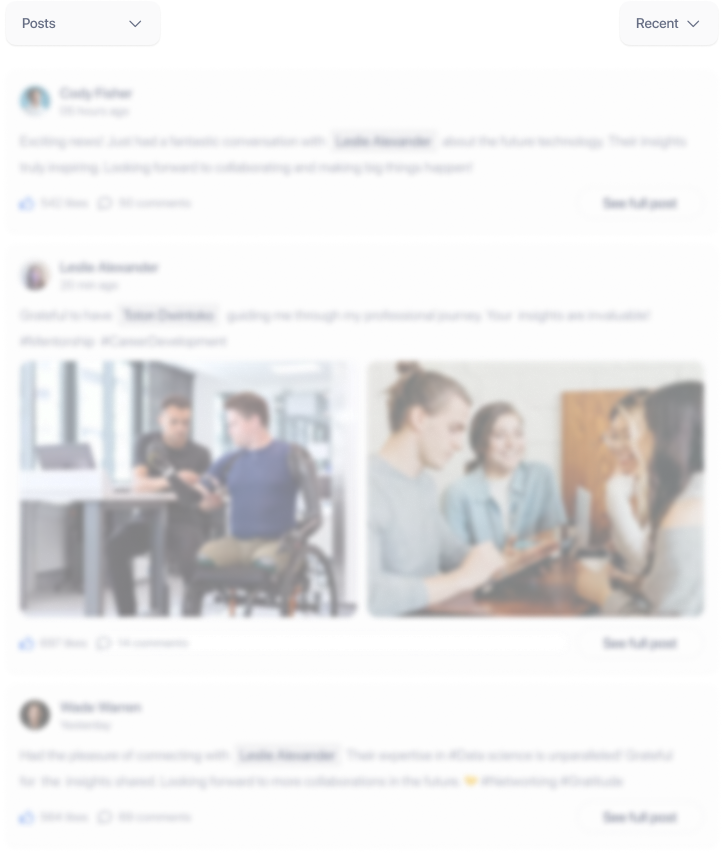