
Kathleen D. Mercado, MBA
PEX Project Manager at Club Car- Claim this Profile
Click to upgrade to our gold package
for the full feature experience.
-
Spanish -
-
English -
Topline Score
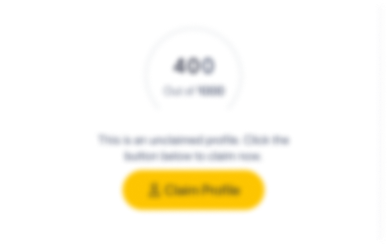
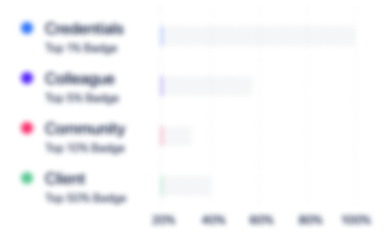
Bio


Credentials
-
Green Belt
TBM -
Lean Leader
Vention Medical -
Project Management
University of Dallas
Experience
-
Club Car
-
Motor Vehicle Manufacturing
-
700 & Above Employee
-
PEX Project Manager
-
Jun 2021 - Present
-
-
Manufacturing Process Quality Engineer
-
Nov 2018 - Jun 2021
- Responsible for leading all production processes and quality engineering activities to support production including day to day production, new product launches, process improvements and Sustaining Engineering - Utilize problem solving techniques to lead projects to improve safety, quality, delivery and productivity.- Lead and manage a team of MPQE technicians on daily manufacturing support for the UFF manufacturing lines and CCDC- Collaborate with NPD and Sustaining Engineering to identify improvements in terms of ergonomics, quality control and design for manufacturability- Lead a cross-functional CFIT (Customer Focus Improvement Team) for the UFF driving initiatives that generate improvements in overall quality including DSI reduction, ICQ and FPY improvements- Provide manufacturing and quality support to Press and Weld shops- Responsible for Capital Projects in UFF and Press Shop to improve processes, productivity and capacity - Manage work instructions in Apriso including updates, sustaining and creation on new ones based on NPD - Conduct RCA for customer complaint and implement corrective actions to avoid reoccurrences on quality defects
-
-
-
RAB Lighting
-
United States
-
Appliances, Electrical, and Electronics Manufacturing
-
100 - 200 Employee
-
Continuous Improvement Leader
-
Feb 2017 - Jun 2018
- Responsible for driving change and developing RAB Lighting’s culture of lean and continuous improvement - Facilitate lean events, coaching lean champions, and helping others solve problems at the source using Root cause analysis and PDCA cycle. - Work with the several managers and functional leaders to develop plans and implement improvements via A3’s, Kaizen events facilitation and projects.- Provide Lean/Continuous Improvement training for the entire site, including salary and hourly employees.- Support several departments with the creation of KPI’s as part of their Lean Daily Management boards, including coaching on how to conduct LDM meetings - Lead the revamp of the Lean 5S Enterprise program across the entire site including warehouse, manufacturing and office areas. - Lead a strategic deployment initiative to increase lean and continuous improvement engagement within the manufacturing personnel by facilitating kaizen events on products to improve their overall assembly process. Events resulted in cost savings of more than $250,000. - Successfully completed the Lean Champions Program through training and the development of an A3 for the Pick bin management resulting in an 86% process improvement with over $50,000 in savings.
-
-
-
-
Operational Excellence Manager
-
Feb 2016 - Dec 2016
- Developed the site Op-Ex action plan and coordinated execution getting all functional areas involved. - Identify opportunities, analyze existing processes, present proposals and execute Kaizen events- Implemented overall site visual management strategy and weekly scorecard to track KPI’s to identify opportunities to improve overall plant productivity.- Developed, implemented and lead the 5S plant program including training materials, project identification and audits. - Provide support for daily operations by allocating resources, production planning and decision making - Lead a project to reduce changeover time in order to improve OEE. Reduced changeover time from 8 hours to 5 hours using lean manufacturing tools and methodologies like SMED, 5S and visual management. - Prepared detailed production trackers to provide visibility on performance metrics (Downtime, Output, OEE, Changeover, People Productivity among others) to facilitate daily management. - Manage all quality, productivity and financial metrics including monthly reporting to senior management.
-
-
-
Weiss-Aug Group
-
United States
-
Manufacturing
-
1 - 100 Employee
-
Continuous Improvement Engineer
-
Sep 2014 - Dec 2015
- Responsible for developing a Lean Manufacturing training program, coaching and mentoring employees at all levels in the organization to create a Lean & Continuous Improvement culture- Identify opportunities, analyze existing processes, present proposals and execute Kaizen events- Facilitate Kaizen events to eliminate waste and add value in manufacturing and transactional processes - Lead several Kaizen Event and improved productivity (UPP-output) of molding cells by 15-20% implementing standard work, visual factory, one-piece flow and layout improvements. Calculated savings of $15,000 to $25,000 per year.- Lead several Kaizen events to eliminate extra handling and processing of products between manufacturing, packaging and shipping.- Lead several Kaizen Events resulting in reduced labor hours between manufacturing and packaging. Calculated savings of $9,000- $15,000 per year.- Implemented and lead the 5S plant program including training materials and audit sheets creation- Create and maintain process documentation including Standard Work Instructions and Technical Process Specifications per ISO standards and requirements.- Provide training to all personnel as it relates to process documentation and manufacturing procedures- Facilitate and lead root cause analysis (8D) for customers’ complaints including corrective action implementation and effectiveness verification/validation supporting the QMS. - Provide manufacturing engineering support for daily operations and new product launches
-
-
-
Vention Medical
-
United States
-
Medical Equipment Manufacturing
-
100 - 200 Employee
-
Business Excellence Site Leader
-
Aug 2011 - Aug 2014
- Provided Regional Lean Six Sigma leadership and support to create a culture of Continuous Improvement across all levels - Regional Program Manager of VIP (Value Improvement Program) strategic initiative with estimated savings of $1.2 million in 2012 and $1 million in 2013- Used Kaizen methodologies to identified opportunities, analyzed existing process, proposed and executed process improvements.- Facilitated kaizen events to eliminate waste and add value to the business in manufacturing and transactional processes – 2 Kaizen events on average per month.- Executed several Kaizen events with external suppliers and customers to improve product/process- Lead a Kaizen Event with key customers and identified quality and cost reduction improvement projects with achievements of $2.9 million in business savings- Improved on-time delivery service (OTD metric) by 22% through kaizen event with primary customer- Lead a kaizen to create and implement a Work Order Management Process and achieved a 24% of work order closure improvement - Lead a series of Kaizen events for main assembly production line improving output from 30 UPP to 35 UPP daily – estimated savings of $60,000 annually- Lead a Kaizen event and implemented a one-piece flow technique to increase throughput by 10% in an insert molding cell - estimated savings of $20,000 annually- Prepared detailed plans to track project progress and performance to assure timely completion and achievement of all project deliverables including financial goals and targets- Managed all quality, productivity and financial metrics for two sites (NJ & CT) - Responsible for lean manufacturing training to employees across sites – 5s, standard work, PDCA, error-proofing, value stream mapping, 5 whys and waste identification- Implemented 5S corporate program in the northeast campus (NJ and CT sites)
-
-
-
Owens Corning
-
United States
-
Wholesale Building Materials
-
700 & Above Employee
-
Manufacturing Engineer
-
Mar 2010 - Jul 2011
- Supported the Technical and Quality Department to assure product complies with specifications/standards and satisfy customers- Improved plant KPI’s through continuous improvement projects. - Created and maintained process documentation including Standard Operating Procedures (SOP’s) and Standard Work for critical tasks. - Trained personnel as it relates to process documentation, procedures and quality defects.- Updated all product/quality specifications and check sheets for the quality control lab- Reduced sheet temperature variation and improved process capability from 0.35 to 1.04 - Installed laser printing at wrapper machine to increase throughput by 28%- Completed an FMEA for the installation for a new shingle machine equipment- Facilitated Kaizen event and improved changeover process by 7% implementing SMED methodology
-
-
Associate Engineer-EDP
-
Jan 2009 - Mar 2010
- Rotated through the different manufacturing and administrative departments of the company and developed and implemented continuous improvement projects as part of an Engineering Development Program- Worked and graduated as an Engineering Development Participant in the Irving Roofing Plant. The purpose of the program is to prepare new hire engineers for future placements. Participants have to acquire and demonstrate the knowledge and skills they develop during the program duration upon graduation.- Created and maintained process documentation including Standard Operating Procedures (SOP’s) and Standard Work. Trained personnel as it relates to process documentation and procedures.- Visited customers and analyzed quality claims - Participated on TPM teams and safety committee - Installed a double-arm to increase wrapper throughput from 31 to 40 bundles per minute
-
-
-
Boston Scientific
-
United States
-
Medical Equipment Manufacturing
-
700 & Above Employee
-
Industrial Engineer COOP
-
Jan 2008 - Aug 2008
- Conducted a Lean Project in the Drug Manufacturing line to improve productivity by 20%, throughput by 15% and optimizing space by 33%- Time studies, line balance, layout design and other lean manufacturing tools were applied and implemented in manufacturing areas- Create and maintain process documentation including Standard Operating Procedures (SOP’s) and Standard Work. Train personnel as it relates to process documentation and procedures. - Conducted a Lean Project in the Drug Manufacturing line to improve productivity by 20%, throughput by 15% and optimizing space by 33%- Time studies, line balance, layout design and other lean manufacturing tools were applied and implemented in manufacturing areas- Create and maintain process documentation including Standard Operating Procedures (SOP’s) and Standard Work. Train personnel as it relates to process documentation and procedures.
-
-
-
Pfizer
-
United States
-
Pharmaceutical Manufacturing
-
700 & Above Employee
-
Industrial Engineer
-
Jun 2007 - Aug 2007
- Worked in the Barceloneta Transfer Project supporting Pfizer Network Strategy decision to transfer Barceloneta’s Packaging Process to Vega Baja site. - Performed Technical Services and Validation Process including protocols documentation and execution at the Packaging Department. - Worked in the Barceloneta Transfer Project supporting Pfizer Network Strategy decision to transfer Barceloneta’s Packaging Process to Vega Baja site. - Performed Technical Services and Validation Process including protocols documentation and execution at the Packaging Department.
-
-
Education
-
University of Puerto Rico-Mayaguez
Bachelor of Science - BS, Industrial Engineering -
The University of Dallas
MBA, Project Management
Community
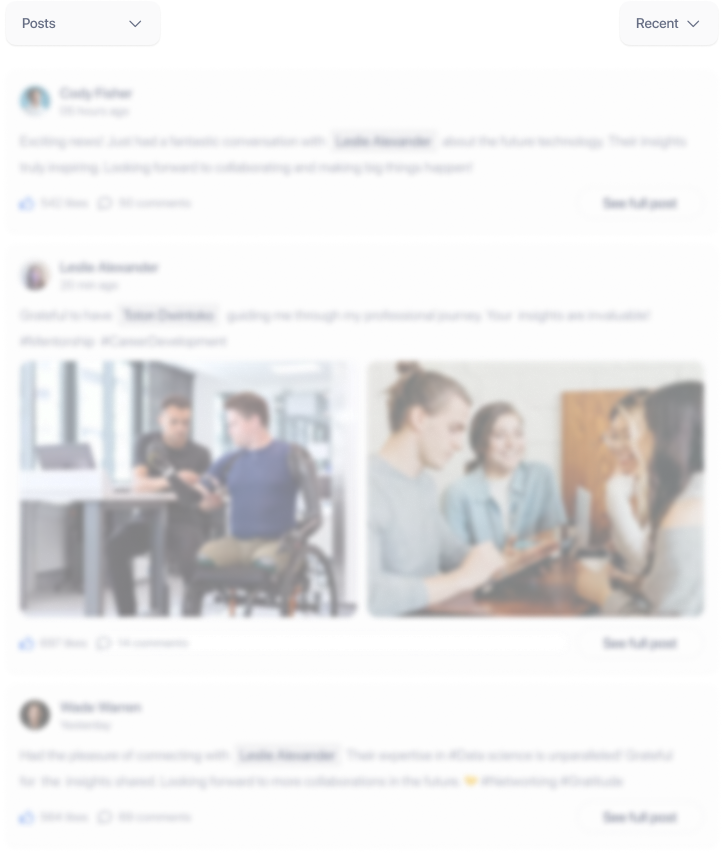