Kathirvel Mani
Deputy General Manager Operations at Harita Seating Systems Limited- Claim this Profile
Click to upgrade to our gold package
for the full feature experience.
Topline Score
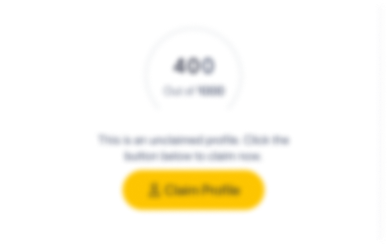
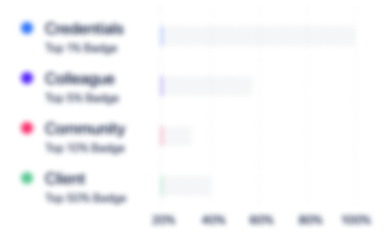
Bio


Experience
-
Harita Seating Systems Limited
-
Automotive
-
100 - 200 Employee
-
Deputy General Manager Operations
-
Aug 2016 - Present
Hosur, Tamil Nadu, India Plant Operations @ Pantnagar, UTK & Hosur, TN – 6 years 6 months: Managing operations & supply chain of Tier1 manufacturing plant for an annual sale of Rs. 250+ Cr. delivering 420+ customer routes with 280+ Products, ~3000 BOPs from 110+ Suppliers by effectively PODC a team of 50+ E&Ms, 600+ Associates constantly emphasizing on the organizational priorities: • Seasoned in handling repetitive, discreate and continuous process manufacturing for domestic & export businesses having… Show more Plant Operations @ Pantnagar, UTK & Hosur, TN – 6 years 6 months: Managing operations & supply chain of Tier1 manufacturing plant for an annual sale of Rs. 250+ Cr. delivering 420+ customer routes with 280+ Products, ~3000 BOPs from 110+ Suppliers by effectively PODC a team of 50+ E&Ms, 600+ Associates constantly emphasizing on the organizational priorities: • Seasoned in handling repetitive, discreate and continuous process manufacturing for domestic & export businesses having requirements pattern of Non-repeat, Forecast, Consumption based, Just in time, Just in sequence DOL supplies. • Pragmatic knowledge in handling Domestic (across India) & Export (US, Europe, Australia) OEM, OES, STUs covering Offroad, Commercial Vehicles, Buses segment. Comprehending knowledge on India & China supplier base and commodities of automobiles industry. • Exposed to commodities like Sheet Metal Fabrication, PU Foam, Fabric / Vinyl, Casting, Forging, Machining, Plastic & Rubber, Investment casting and Indirect. Key Result Areas : • Sustained Zero reportable accident status >10 years, Achieved Zero lost time incident status for >2 years, Recognized as best among plants for “Safety Index”. • Won customer awards on “Overall Performance” from JD, TAFE, Quality award from AL, Kobelco, Delivery award from Volvo. Achieved Zero CELR status with all key customers. • Improved productivity by > 30 % YOY. • Optimized manufacturing cost by > 15 % YOY through CR/PIP projects • Mobilized team for Highest sale >10 % monthly consecutively for 3 months
-
-
Senior Manager - OPEX & Supplier Development
-
Apr 2009 - Jul 2016
Hosur, Tamil Nadu, India Systemically transform Flow of Material & Information, Quality of Product, Process & System across supply chain to build stability in Order fulfillment, consistency in Quality. • Defined tier structure and established Planning & Execution system for Procurement, Production and delivery process. Implemented Heijunka to optimize resources, Kanban (both Repeat, Sequential) to visualize flow of material within & across Procurement, Production & Delivery Flow • Revisited Plant & Line layout to… Show more Systemically transform Flow of Material & Information, Quality of Product, Process & System across supply chain to build stability in Order fulfillment, consistency in Quality. • Defined tier structure and established Planning & Execution system for Procurement, Production and delivery process. Implemented Heijunka to optimize resources, Kanban (both Repeat, Sequential) to visualize flow of material within & across Procurement, Production & Delivery Flow • Revisited Plant & Line layout to reduce BCT, Space and streamline single piece flow • Identified projects to eliminate 7 Lean wastes • Monitored supplier QDCS performance, prepared & executed development / drop plan. Audited supplier QS to upgrade certification to TS16949 standard • Improved Cp, Cpk for critical characteristics in BOPs. Audited process adherence for special processes like welding, plating, powder coating, CED coating, thermoforming etc. • Implemented Kaizen (CAPA) for IH / Customer quality complaints. Assisted technically to improve Quality of Kaizen. Monitored reoccurrence and implemented Mistake proofing. Improved quality of CAPA & process orientation at supplier end. Key Result Areas : • Sustained Zero reportable accident status >10 years, Achieved Zero lost time incident status for >2 years, Recognized as best among plants for “Safety Index”. • Won customer awards on “Overall Performance” from JD, TAFE, Quality award from AL, Kobelco, Delivery award from Volvo. Achieved Zero CELR status with all key customers. Reduced BOR ppm by 70% and improved BO DOL by 3 times. Enabled 6 preferred suppliers to upgrade QMS from IS09001 to TS16949 system. • Productivity improvement by 81% @ In-house & 441% @ supplier end: • Optimized manufacturing cost by > 15 % YOY through CR/PIP projects • Won Atmanirbhar award 2021 – Excellence in Exports, Excellence in NPD • Published “Leaping ahead with VSME” book in 2017 under CII &JICA CSM project.
-
-
Assistant Manager Purchase & Sourcing
-
Oct 1996 - Mar 2009
Hosur, Tamil Nadu, India ★ As a leader, I've increased productivity by implementing effective time and task management strategies and employing the best relationship management techniques. ➤ KEY RESULT AREAS ● Evaluated RFQ/drawings/specifications and studied India/BCC sourcing. ● Technical interaction with vendors and competency assessment. RFQ, supplier quote, Priced components and tools. QMS & CSR-compliant supplier audit. ● Utilizing NPI, prepared Tool/Mold/Die budget. Obtained tool and process… Show more ★ As a leader, I've increased productivity by implementing effective time and task management strategies and employing the best relationship management techniques. ➤ KEY RESULT AREAS ● Evaluated RFQ/drawings/specifications and studied India/BCC sourcing. ● Technical interaction with vendors and competency assessment. RFQ, supplier quote, Priced components and tools. QMS & CSR-compliant supplier audit. ● Utilizing NPI, prepared Tool/Mold/Die budget. Obtained tool and process development plans and tracked progress. Sample inspection/testing with QA and client submission. ● Procedure audit and pilot lot shipments. First-time sample pass improved. ● Developed using APQP and PPAP. Support product/part validation. ● Establish essential CP, CPK. ● Decreased lead time by coordinating suppliers, R&D, quality, and PE. Developed with engineering adjustments. ● Established local aftermarket contract manufacturing. ● Mechanical/body parts for captive passenger car service. ● Serial production release schedules/shipment monitoring/logistics. ● Implemented TS16949, IMS, and NCRs. ● Implemented Tri-party agreement with commodity suppliers. Price index, trend analysis, supplier negotiations. Revised all current parts' costs for commodity and process price escalations.
-
-
Education
-
Birla Institute of Technology and Science, Pilani
Master of Science - MS, Manufacturing Management -
Indian Institution of Industrial Engineering
Graduate, Industrial Engineering
Community
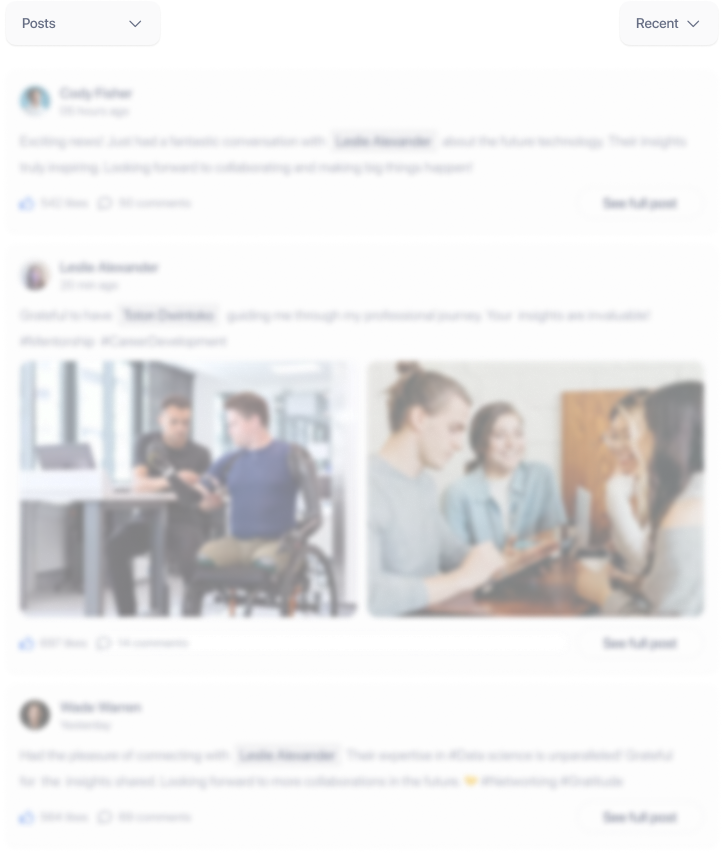