Kasra Zamani
Quality Manager at Altec Integrated Solutions Ltd.- Claim this Profile
Click to upgrade to our gold package
for the full feature experience.
Topline Score
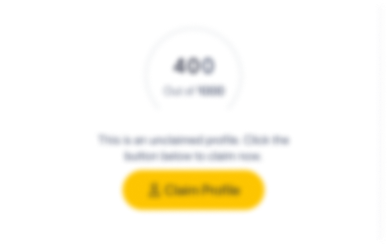
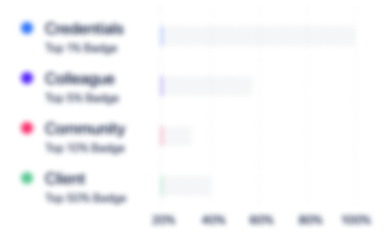
Bio


Experience
-
Altec Integrated Solutions Ltd.
-
Canada
-
Automation Machinery Manufacturing
-
1 - 100 Employee
-
Quality Manager
-
Oct 2021 - Present
Altec designs and manufactures precision machinery and advanced controls equipment. We create innovative solutions to solve the toughest application demands in the amusement park industry and the veneer and plywood manufacturing industry. With our facilities in Coquitlam, BC and Diboll, Texas, we continue to expand our products and services, setting new benchmarks for innovation and integration. Altec designs and manufactures precision machinery and advanced controls equipment. We create innovative solutions to solve the toughest application demands in the amusement park industry and the veneer and plywood manufacturing industry. With our facilities in Coquitlam, BC and Diboll, Texas, we continue to expand our products and services, setting new benchmarks for innovation and integration.
-
-
-
Beachcomber Hot Tubs
-
Canada
-
Manufacturing
-
1 - 100 Employee
-
Quality Assurance Leader
-
May 2018 - Oct 2021
• Implemented and maintained Good Manufacturing Practice (GMP); • Provided training to all employees to ensure the highest standard of quality to comply with internal and external requirements • Defined and implemented continuous Improvement protocols • Lead Quality Team responsible for implementing quality improvement projects. • Reviewed individual customer complaints and trends implemented systems to prevent a recurrence. • Managed the quality performance of critical parts of suppliers. • Prepared quality analysis and reports for Senior Management and other Managers/Supervisors. • Developed and implemented quality control/test methodologies and standards. • Developed and implemented statistical process control methods. • Investigated nonconforming products, failures and causes • Led production and quality staff in the integration of quality management into daily operations. • Prepared quality presentations and presented to the Dealers/Development Personnel at special functions as required. Show less
-
-
-
Poly-Chlor Plastic Industries Ltd
-
Coquitlam, BC
-
Quality Assurance Manager
-
Aug 2014 - Jan 2018
- Directed and coordinated the company’s quality program, including the implementation of ISO9001 systems and procedures. - Compiled quality control reports, created statistical process control metrics, manage nonconformity material discrepancy reports, recommended continuous improvement activities. - Prepared monthly summaries of quality issues for the senior management team. - Implement quality training programs for key quality & manufacturing personnel. - Ensured proper calibration of quality equipment. - Worked with Production Management to apply pertinent Six Sigma Green/Black Belt attributes and other quality procedures appropriate to the business objectives. - Issued and managed supplier Corrective Action Reports. - Worked with Design on new component introduction, alternative raw materials, tooling requirements, test plans, and product qualification requirements. - Communicated and shared the company quality philosophy to key personnel in the company. - Investigated and record customer complaints regarding product performance, specifications, and reliability. Show less
-
-
-
Hevvy/Toyo Pumps North America Corporation
-
Canada
-
Mechanical Or Industrial Engineering
-
1 - 100 Employee
-
Quality Assurance Manager
-
Dec 2012 - Aug 2014
Directed and coordinated the company’s quality program, including the implementation of ISO9001 Systems and procedures.Quality Standards. Quality Project Management. Business Process Documentation Document Control. Quality Communications. People Management. Quality Auditing. Problem Solving. Team Player. Quality “Go To” Guy. Directed and coordinated the company’s quality program, including the implementation of ISO9001 Systems and procedures.Quality Standards. Quality Project Management. Business Process Documentation Document Control. Quality Communications. People Management. Quality Auditing. Problem Solving. Team Player. Quality “Go To” Guy.
-
-
-
Wesgar Inc.
-
Canada
-
Fabricated Metal Products
-
1 - 100 Employee
-
Quality Assurance Supervisor
-
Jan 2009 - Dec 2012
- Drafted quality assurance policies and procedures - Interpreted and implemented quality assurance standards - Evaluate the adequacy of quality assurance standards. - Reviewed the implementation and efficiency of quality and inspection systems - Planned, conduct and monitor testing and inspection of materials and products to ensure finished product quality - Documented internal audits and other quality assurance activities - Investigated customer complaints and non-conformance issues - Collected and compiled statistical quality data - Analyzed data to identify areas for improvement in the quality system - Developed, recommended and monitor corrective and preventive actions - Prepared reports to communicate outcomes of quality activities - Identified training needs and organized training interventions to meet quality standards - Coordinated and supported on-site audits conducted by external providers - Evaluated audit findings and implemented appropriate corrective actions - Assured ongoing compliance with quality and industry regulatory requirements Show less
-
-
Community
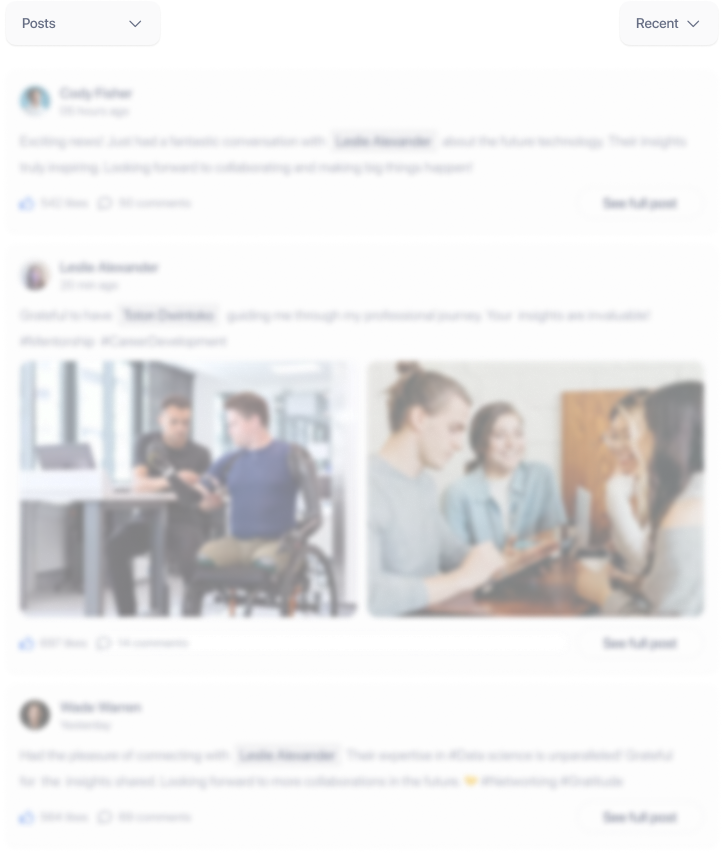