Karl Johann Tilly
Research Associate at IBF der RWTH Aachen University- Claim this Profile
Click to upgrade to our gold package
for the full feature experience.
Topline Score
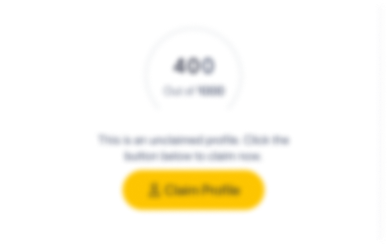
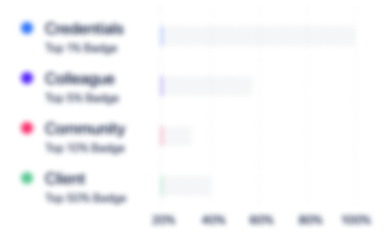
Bio


Credentials
-
Six Sigma Yellow Belt
RWTH Aachen UniversityJan, 2020- Sep, 2024
Experience
-
IBF der RWTH Aachen University
-
Germany
-
Research Services
-
1 - 100 Employee
-
Research Associate
-
Feb 2021 - Present
Research Area: Aluminium Sheet Testing and Forming in High Temperature ApplicationsResearch Group: Materials Testing Current Project: Development of a gas-based high-temperature test method for material data determination for modern aluminum hot forming processes
-
-
Research Assistant
-
Oct 2020 - Jan 2021
Tribology and lubricant research for Hot Metal Gas Forming: Development of a Hot Strip Drawing Test
-
-
Master Thesis Project
-
Feb 2020 - Sep 2020
"Development of an optimized process chain for gas-basedsheet metal forming of a heattreatable aluminium alloy"
-
-
-
Werkzeugmaschinenlabor, WZL der RWTH Aachen
-
Germany
-
Research
-
400 - 500 Employee
-
Student Research Assistant
-
Apr 2018 - May 2019
Deepdrawing: numerical simulation with ABAQUS, material characterization via Nakajima tests and laboratory experiments During my time at Laboratory for Machine Tools and Production Engineering (WZL) of RWTH Aachen University I was working within the project "Damage-controlled forming processes, influence on damage development during deep drawing". In my role as a Student Research Assistant I was tasked with working on fundamental experiments like Nakajima Test to examine the influence of defined stress states on the damage development of DP800 dual-phase steel. Furthermore, I was working on the development of a finite-element model of deep-drawing in ABAQUS.
-
-
-
-
Bachelor Thesis
-
Sep 2017 - Jan 2018
"Incremental Sheet Forming - Investigations into Springback Compensation for Metal Parts by Overcrowing" "Incremental Sheet Forming - Investigations into Springback Compensation for Metal Parts by Overcrowing"
-
-
-
KAMAX
-
Poland
-
Renewable Energy Semiconductor Manufacturing
-
1 - 100 Employee
-
Student Intern
-
May 2017 - Aug 2017
Departement Heat Treatment – process optimization of heat treatment furnaces In terms of technology, KAMAX is the world's leading manufacturer of high-strength fasteners for the automotive industry. With locations in the three leading automobile regions of Europe, America and Asia, KAMAX is a key supplier for all major manufacturers and suppliers of the passenger car and commercial vehicles industry. During my work as an intern in the department of Heat Treatment at KAMAX I was tasked with the reduction of scrap- and reworking parts during the annealing process. Due to my review and intensive analysis of the processing data I was able to reduce the quota of reworking parts up to 66%.
-
-
-
-
Student Research Assistant
-
Sep 2016 - Apr 2017
Stretch Drawing, Incremental Sheet Forming: laboratory experiments and tooling During my time at Institute of Metal Forming of RWTH Aachen University I was able to gain insights in different variants of metal sheet forming, most significantly Incremental Sheet Forming as well as Stretch Drawing and the process development of said technologies. My tasks included preperation and excecution of laboratory experiments as well as optical forming and deformation analysis with GOM ATOS, ARGUS and ARAMIS. Materials, I worked with include different grades of aluminum alloys, deep drawing/ mild steels and stainless steels.
-
-
Education
-
RWTH Aachen University
Master of Science - MS, Business Administration and Engineering Materials and Process Engineering -
Aalto University
Master's degree, Industrial Engineering -
RWTH Aachen University
Bachelor of Science - BS, Business Administration and Engineering Materials and Process Engineering
Community
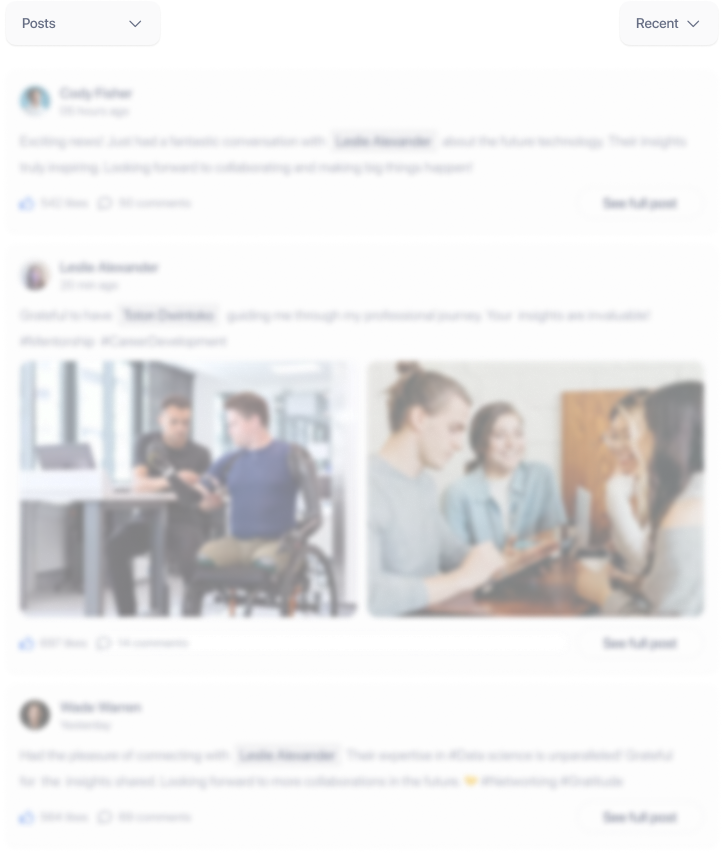