Karl Fawdry
Manufacturing Engineering Manager at Innolith- Claim this Profile
Click to upgrade to our gold package
for the full feature experience.
Topline Score
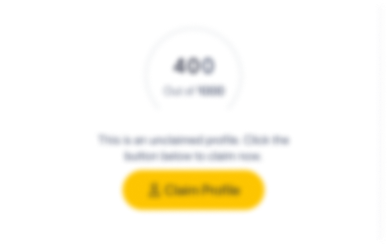
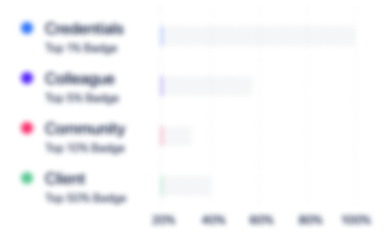
Bio


Credentials
-
Chartered Engineer
Institute of Engineering and Technology
Experience
-
Innolith
-
Switzerland
-
Appliances, Electrical, and Electronics Manufacturing
-
1 - 100 Employee
-
Manufacturing Engineering Manager
-
Jan 2023 - Present
-
-
-
hofer powertrain
-
Germany
-
Automotive
-
100 - 200 Employee
-
Engineering Quality Manager
-
Sep 2021 - Feb 2023
As an Engineering Quality Manager I am responsible for the liaison between the Engineering Design Department and the Manufacturing Facility. My duties include managing a small team in the delivery and execution of APQP, Supplier PPAP Maturity, Concessions, Process Change Requests and administration of the PSW (Part Submission Warrant). This is a customer facing role in which I am accountable for the coordination of non-conforming product and problem resolution. My duties include forming cross functional teams for the generation of 8D’s to demonstrate containment of stock, implementation of corrective actions and part/product validation. Show less
-
-
Senior Manufacturing Engineer
-
Oct 2016 - Sep 2021
As a Senior Manufacturing Engineer at hofer Powertrain, I was responsible for the project management and delivery of a low volume production line for a McLaren Hybrid Transmission. My role included the development of a manufacturing strategy that adhered to budget constraints, the writing of RFQ documentation / equipment specifications and the selection of suitable vendors for incoming inspection, assembly tooling and test equipment.Using a template that I developed, my initial responsibilities included the creation of an assembly process that incorporated takt time calculations, cycle time estimates, line balancing, direct labour costs, equipment lists and associated costs. During the delivery phase I was responsible for leading a small team in the approval of tooling drawings, the pre-acceptance of equipment at vendors and delivery to the production facility.I coordinated the installation and commissioning activities in order to achieve the customer's target date for SOP. In parallel with these activities, I was responsible for defining the final Assembly Process with Quality Care Points that linked to the PFMEA and Control Plan that I had also generated. Show less
-
-
-
Productiv
-
United Kingdom
-
Industrial Machinery Manufacturing
-
1 - 100 Employee
-
Advanced Manufacturing Engineer
-
Feb 2014 - Sep 2016
Past Responsibilities: - Creating and developing a Factory Strategy to ensure adherence to Lean Manufacturing principles. - Developing master Timing Plans in order to determine the critical path and drive the Simultaneous Engineering activities of cross-functional teams for the timely delivery of all resources. - Assessing new and existing vendors for the supply of manufacturing equipment that adheres to customer performance and reliability criteria, whilst building on supplier relationships. - Devising layouts that adopt Lean Manufacturing principles whilst working to space and services constraints. - Calculating equipment utilisation data based on forecasted production volumes, target cycle times and planned manpower. - Generating Enquiry documentation and Technical Specifications for the conformity of manufacturing equipment to functionality requirements. - Vetting vendor quotations based on ‘Fit for purpose’ criteria and generate purchase order requisitions with supporting justifications for expenditure. - Creating Process Sheets and Stage Drawings in order to define the process sequence of machining, assembly and gauging operations. - Creating schemes and approve detail design drawings of manufacturing equipment submitted by vendors. - Coordinating vendor commissioning activities including the generation of installation checklists, fault logging, capability testing, training, sign-off and release of funds in accordance with customer acceptance criteria. - Archiving documentation for future traceability and conformity to legislation e.g. design drawings, CE Marking and risk assessment, UKAS certification, R&R study results and instruction manuals. - Creating and implementing management processes to control the procurement of bespoke manufacturing equipment and review the content to ensure continuous improvement and conformity to ISO 9000. Show less
-
-
-
JLR
-
United Kingdom
-
Motor Vehicle Manufacturing
-
700 & Above Employee
-
Principal Engineer
-
Sep 2011 - Jan 2014
Past Responsibilities: - Maintaining cost control documents to ensure adherence to a £12M budget and negotiate discounts in order to achieve cost saving targets. - Developing master Timing Plans in order to determine the critical path and drive the Simultaneous Engineering activities of cross-functional teams for the timely delivery of all resources. - Assessing new and existing vendors for the supply of manufacturing equipment that adheres to customer performance and reliability criteria, whilst building on supplier relationships. - Devising layouts that adopt Lean Manufacturing principles whilst working to space and services constraints. - Calculating machine utilisation data based on forecasted production volumes, target cycle times and planned manpower. - Generating Enquiry documentation and Technical Specifications for the conformity of manufacturing equipment to functionality requirements. - Vetting vendor quotations based on ‘Fit for purpose’ criteria and generate purchase order requisitions with supporting justifications for expenditure. - Creating Process Sheets and Stage Drawings in order to define the process sequence of machining, assembly and gauging operations. - Creating schemes and approving detail design drawings of manufacturing equipment submitted by vendors. - Coordinating vendor commissioning activities including the generation of installation checklists, fault logging, capability testing, training, sign-off and release of funds in accordance with customer acceptance criteria. - Archiving documentation for future traceability and conformity to legislation i.e. design drawings, CE Marking and risk assessment, UKAS certification, R&R study results and instruction manuals. - Creating and implementing management processes to control the procurement of bespoke manufacturing equipment and reviewing the content to ensure continuous improvement and conformity to ISO 9000. Show less
-
-
-
BMW Hams Hall Motoren GmbH
-
Hams Hall, Coleshill
-
Manufacturing Equipment Design Engineer
-
Sep 1999 - Aug 2011
Past Responsibilities: - Assessing new and existing vendors for the supply of design drawings and manufacturing equipment to quality, lead-time and cost targets. - Generating Enquiry documents and Technical Specifications for the conformity of manufacturing equipment to functionality requirements. - Vetting vendor quotations based on ‘Fit for purpose’ criteria and generating purchase order requisitions with supporting justifications for expenditure. - Creating equipment design drawings in CAD and approving schemes and designs submitted by vendors. - Managing SE meetings and liaising with vendors at each stage of the equipment procurement process to ensure project timings are achieved. - Managing vendors commissioning activities including the generation of installation checklists, fault logging, capability testing, sign-off and release of funds in accordance with BMW acceptance criteria. - Archiving documentation for future traceability and conformity to Health & Safety legislation i.e. design drawings, CE marking & risk assessment, UKAS certification, R+R Study results, instruction manuals and training. - Creating and implementing management processes to control the procurement of bespoke manufacturing equipment and reviewing their content to ensure continuous improvement and conformity to ISO 9000. Show less
-
-
Education
-
University of Central England
Management of Manufacturing Systems, Manufacturing Engineering -
East Birmingham College
ONC & HNC in Manufacturing & Engineering, Manufacturing Engineering
Community
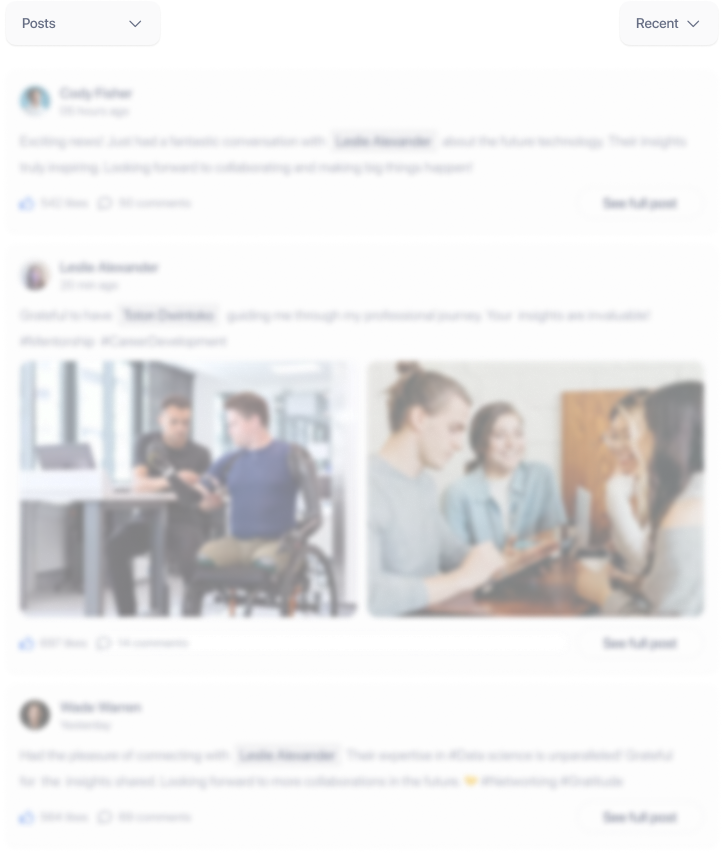