Kamal T.
HSEQ Manager at Bolwell Corporation- Claim this Profile
Click to upgrade to our gold package
for the full feature experience.
-
English Full professional proficiency
-
Arabic Native or bilingual proficiency
Topline Score
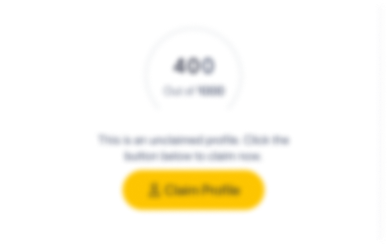
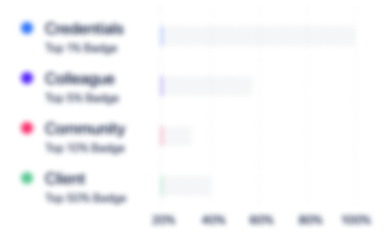
Bio

Robert D'Arcy
It isn't offend that you meet some one at was such a pleasure to work with as Kamal Taha was. Kamal is a talented, totally professional and passionate individual. I met Kamal during my time at Bowell and was impressed by his technical abilities and his enthusiasm for his work. His easy-going personality also made it a pleasure to work with him and help him to deal with difficult situation with easy . I am absolutely sure that Pascal would be an asset to any team.

LinkedIn User
I have had the pleasure to work closely with Kamal over the past few years and learned from his experience and expertise in manufacturing quality to drive efficiency. Kamal was a key member of our Australian facility and helped to establish the quality department, set and improve standards, and implement quality management systems. In addition, Kamal has organized and conducted training sessions to master problem solving primarily in analyzing and eliminating

Robert D'Arcy
It isn't offend that you meet some one at was such a pleasure to work with as Kamal Taha was. Kamal is a talented, totally professional and passionate individual. I met Kamal during my time at Bowell and was impressed by his technical abilities and his enthusiasm for his work. His easy-going personality also made it a pleasure to work with him and help him to deal with difficult situation with easy . I am absolutely sure that Pascal would be an asset to any team.

LinkedIn User
I have had the pleasure to work closely with Kamal over the past few years and learned from his experience and expertise in manufacturing quality to drive efficiency. Kamal was a key member of our Australian facility and helped to establish the quality department, set and improve standards, and implement quality management systems. In addition, Kamal has organized and conducted training sessions to master problem solving primarily in analyzing and eliminating

Robert D'Arcy
It isn't offend that you meet some one at was such a pleasure to work with as Kamal Taha was. Kamal is a talented, totally professional and passionate individual. I met Kamal during my time at Bowell and was impressed by his technical abilities and his enthusiasm for his work. His easy-going personality also made it a pleasure to work with him and help him to deal with difficult situation with easy . I am absolutely sure that Pascal would be an asset to any team.

LinkedIn User
I have had the pleasure to work closely with Kamal over the past few years and learned from his experience and expertise in manufacturing quality to drive efficiency. Kamal was a key member of our Australian facility and helped to establish the quality department, set and improve standards, and implement quality management systems. In addition, Kamal has organized and conducted training sessions to master problem solving primarily in analyzing and eliminating

Robert D'Arcy
It isn't offend that you meet some one at was such a pleasure to work with as Kamal Taha was. Kamal is a talented, totally professional and passionate individual. I met Kamal during my time at Bowell and was impressed by his technical abilities and his enthusiasm for his work. His easy-going personality also made it a pleasure to work with him and help him to deal with difficult situation with easy . I am absolutely sure that Pascal would be an asset to any team.

LinkedIn User
I have had the pleasure to work closely with Kamal over the past few years and learned from his experience and expertise in manufacturing quality to drive efficiency. Kamal was a key member of our Australian facility and helped to establish the quality department, set and improve standards, and implement quality management systems. In addition, Kamal has organized and conducted training sessions to master problem solving primarily in analyzing and eliminating

Experience
-
Bolwell Corporation
-
Australia
-
Truck Transportation
-
1 - 100 Employee
-
HSEQ Manager
-
Apr 2020 - Present
-
-
Production Supervisor
-
Feb 2020 - Apr 2020
-
-
-
CCL Secure
-
Australia
-
Printing Services
-
100 - 200 Employee
-
Inks, Pre-press and Cylinder Manufacturing Manager
-
Mar 2017 - Jan 2020
• Lead and manage the effectiveness and efficient operations of the value stream business unit• Manage two separate teams (Gravure Inks, Pre-press and Cylinder Manufacturing)• Manage and control labour, finances and budgets• Provide leadership and a safe environment for both teams• Manage production schedules and deliveries locally and internationally• Apply lean concepts to reduce lead times and first time through capability• Educate team members in problem resolution, lean, time management, statistical analysis and in the use of other business tools to ensure improved quality, efficiency and customer satisfaction• Provide leadership at various management gatherings and meetings• Budget planing and submissions• Take the lead in managing and resolving people, machine and environmental aspectsAccomplishments• Reduction in lead time leading to higher capacity and greater efficiency, from 6 weeks to 2.5 weeks.• Improved analysis and reporting and visualisation of demand vs expectations • Improved internal and external customer satisfaction• Improved team Members Satisfaction and Engagement participation• Right first time capability improvement (Inks, Pre-press and Cylinders) resulting in less down time on the press• Worked in collaboration with project management on the future cylinder manufacturing facility $4M proj.• First time right ink colour mismatch from twice weekly to once every three months saving on downtime / spoilage $400,000 pa.• Reduced overall operating costs saving +$280,000 pa• Workplace behaviour / culture alignment with company values
-
-
Quality Assurance Engineer
-
Feb 2015 - Mar 2017
• Create / maintain catalogue of defects for all new and existing products• Lead root cause analysis of problems and the execution of the Corrective Action activities, including the 8D Program / A3 DIAMAC problem solving process• Specification review prior to production run• Provide leadership and support to Laboratory members• Internal Waste / Scrap Analysis daily reporting• Statistical Process Control (SPC)• Participate in new product introduction• Identification of CTQs and maintenance of PFMEAs / CP• Training production / quality personnel with CTQ identification and assessment• Procedures / work instruction development and implementation• Direct production personnel with regards to rework / AQL and disposition implementation• Waste reduction projects – Black Belt Six Sigma DMAIC• Work with and assist a team of eleven (11) quality lab techniciansAccomplishments• Direct involvement in the reduction of internal spoilage / waste by 35% (+4M) 2015 Vs 2016 • Established and reviewed existing acceptance standards to minimise waste in conjunction with customers, saving +$2M in unnecessary waste / rejections• Introduction of a new scrap analysis reporting system• Introduction of a new SPC pack to provide real time quality performance• Assist the organisation in moral / team building / culture change
-
-
-
Vistaprint
-
Australia
-
Executive Offices
-
Senior Quality Engineer
-
Jul 2010 - Dec 2014
Accomplishments • Part of the team to achieve the Shingo Award 2014 (Medallion for Operational Excellence) • Customer complaint rate reduction by >25% 2010-2014 • Plant (Deer Park) with the highest customer satisfaction rate, the best of three plants with regards to quality / delivery • Directly involvement with the introduction of the Global Root Cause Analysis System and its deployment • Reduced complexity between the Customer Service Team (call centre) and the manufacturing plant reducing waste and improvement in defect categorisation by greater than 80%. • Reduced internal scrap / waste rate by >20% 2010 -2014 • Alignment between quality personnel and production teams regarding CTQ guidelines / acceptance stds reducing errors and spoilage costs • Directly involved in the environmental climate control system and ongoing daily monitoring in order to reduce print waste, improve first time through capability (efficiency) and minimise costs, +$1M in waste / downtime savings
-
-
-
The Shotton Group
-
Australia
-
Industrial Machinery Manufacturing
-
1 - 100 Employee
-
Quality Assurance Manager / Process Improvement Engineer
-
Oct 2007 - Jul 2010
Accomplishments • Improved customer service and response rating by greater than 50% from 47% to > 85%, as preferred supplier • Acquired new business orders and contracts as a results of improved customer relations • Complete re-certification to ISO9001 with no major / minor non compliance • Improved first time through capability, a reduction of non conformity by greater than 50% • Implemented a 5S program and a lean culture • Monitored individual and plant performance for OEE, able to provide individual feedback for improvement • Workplace behaviour / culture change
-
-
-
-
Quality Assurance Manager
-
Apr 2005 - Oct 2007
Accomplishments • Reduced customer complaints defective parts per million (DPPM) rate from 32,000 to 700 • Improved customer relations by more than 50% to a rate above 87% with Kenworth and Iveco Trucks making Bolwell preferred supplier listing • Reduced internal scrap & waste rate by greater >30% • Positively impacted relations between production, quality and the customer quality and supply chain teams • Improved overall efficiency (OEE, quality, internal waste) • Assisted procurement in the development of suppliers • Instrumental in the development and implementation of acclimatised gel coat / glass spray control booth, positively impacting the customer complaint rate / internal rework and scrap cost and down time by greater than 50% saving the business +$300,000 pa in repairs / rework.
-
-
-
MTM Pty.Ltd.
-
Australia
-
Automotive
-
1 - 100 Employee
-
Quality Assurance Supervisor
-
Feb 2002 - Apr 2005
Accomplishments• Improved customer quality rating (Ford / Toyota / Holden / Mitsubishi)• Excellent roper with all customers • Reduced DPPM rate to target levels, GM Holden < 25ppm, Ford <500ppm, Mitsubishi and Toyota <50 ppm• Reduced cost of warranty by 50%, saving ~$200,000 yearly as result of proper RCA and internal changes to address key issues• Introduced real time SPC, charts / capability assess. on display and trained all personnel through the use of SPC and the importance of customer satisfaction• Member of the TPS team, working closely with the Toyota Lean Team that resulted in the savings of 35 head count directly as a result of implementing TPS (Toyota Production System)• Culture change advocate
-
-
Senior Quality Assurance Engineer
-
Mar 1999 - Feb 2002
Accomplishments• Improved customer quality rating (Ford / Toyota / Holden / Mitsubishi)• Excellent roper with all customers • Reduced DPPM rate to target levels, GM Holden < 25ppm, Ford <500ppm, Mitsubishi and Toyota <50 ppm• Reduced cost of warranty by 50%, saving ~$200,000 yearly as result of proper RCA and internal changes to address key issues• Introduced real time SPC, charts / capability assess. on display and trained all personnel through the use of SPC and the importance of customer satisfaction• Member of the TPS team, working closely with the Toyota Lean Team that resulted in the savings of 35 head count directly as a result of implementing TPS (Toyota Production System)• Culture change advocate
-
-
Education
-
Complete Lean Solutions
Certificate VI of Competitive Manufacturing -
Western Metropolitan Institute of TAFE
Associate Diploma Of Engineering (National), Manufacturing Engineering -
Computer Power Training Institute
Diploma of Computer Operations
Community
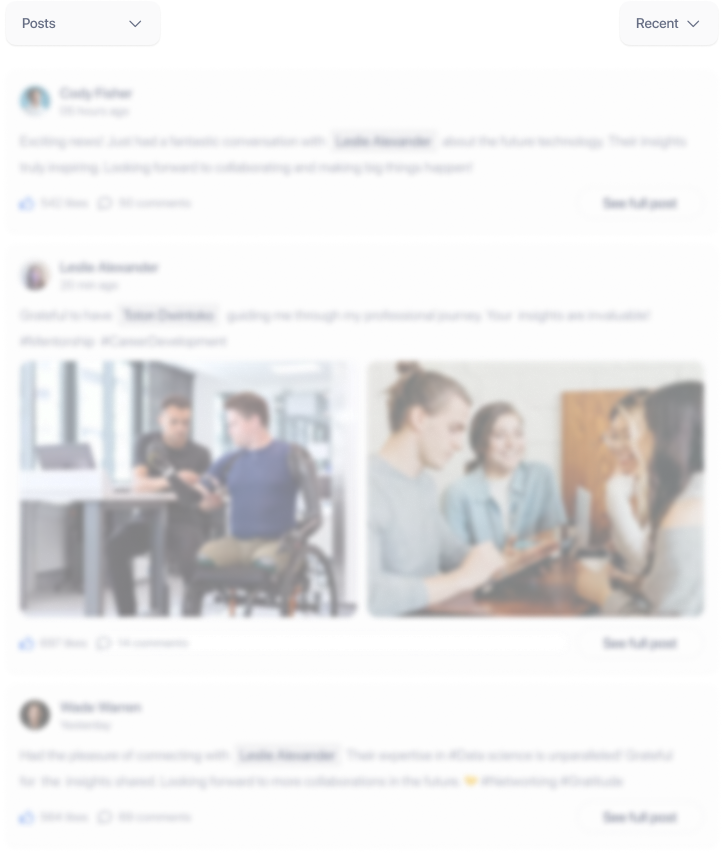