K Adam Williams
Quality Manager at Schoen Insulation Services, Inc.- Claim this Profile
Click to upgrade to our gold package
for the full feature experience.
Topline Score
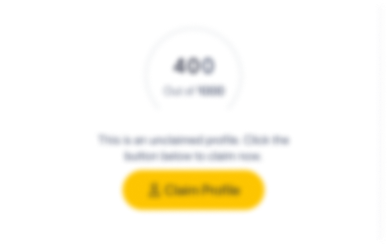
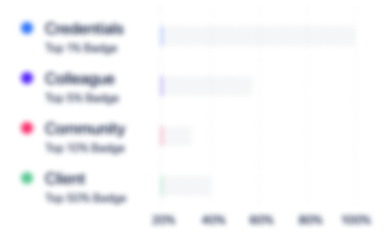
Bio


Experience
-
Schoen Insulation Services, Inc.
-
United States
-
Appliances, Electrical, and Electronics Manufacturing
-
1 - 100 Employee
-
Quality Manager
-
Jul 2021 - Present
I lead a team that ensures SIS quality is at its peak thus paving the way for us to be the leading low-cost supplier of non-metallic machined, cut, and turned parts to make our customer the HERO! We manufacture and supply the needs of every industry from medical, aerospace, oil and gas, power generation, just to name a few. Our skilled talent focuses on quality one piece at a time to make sure the parts our customers depend on are to their specifications and right the first time every time. I lead a team that ensures SIS quality is at its peak thus paving the way for us to be the leading low-cost supplier of non-metallic machined, cut, and turned parts to make our customer the HERO! We manufacture and supply the needs of every industry from medical, aerospace, oil and gas, power generation, just to name a few. Our skilled talent focuses on quality one piece at a time to make sure the parts our customers depend on are to their specifications and right the first time every time.
-
-
-
CMI Limited Co.
-
United States
-
Wholesale Building Materials
-
1 - 100 Employee
-
Production Manager
-
May 2019 - Jun 2021
Responsible for production operations, quality, and personnel for $18M to $24M in annual production. Manage and schedule operations for a twenty-four-hour, five-day-a-week production schedule. Create PDCA initiatives that foster teamwork and operational uptime by creating efficiencies through preventative tasks with communication boards and hand-off meetings. Coordinate the review of customer quality escalations with internal reviews and QC testing operations. Create a pay-for-performance system with tangible tracking and updates on a monthly, quarterly, and annual basis. Organize and structure SOP's within the filing system and update tracking functions for review and update. Manage a 92.5% production performance yield goal through daily shift meetings. Drive safety training for new hires and initiatives by awareness in shift meetings.
-
-
-
NCR Corporation
-
United States
-
IT Services and IT Consulting
-
700 & Above Employee
-
Production Manager, Material Recovery
-
Apr 2016 - May 2019
Ensuring the most cost-effective method of recovery is being utilized for reusable materials. By focusing on revenue and expenditures for the most economical results. I achieve this with an engaged team through coaching, building, upholding, and creating a responsible workforce that understands their time, effort, and vision are responsible for how they present the quality of the NCR business to the customer. This is achieved through in-house designed methods and processes, with input and buy-in from the workforce that drives their personal involvement and pride. We do this to recover materials in order to achieve multiple life cycles. Thus reducing NCR's environmental impact to our local landfill, with ultimately improving our bottom line. After all our logo is green.
-
-
Fulfillment Operations Supervisor
-
Jan 2015 - Mar 2016
As part of the Operations Team, I am in charge of operations personnel that have the soul responsibility for fulfilling the global customer needs for NCR's Advanced Exchange Depot Service model. Within this role I manage the process improvements needing to be made daily for optimal performance within my Fulfillment Team's operation. Taking on this role I have implemented a training platform for bringing in new personnel setting them up for success in every role that we need them to perform at their best. I enjoy being the best at what I do and building up my team to do the same for the win.
-
-
HSR- Field Service Engineer
-
Oct 2013 - Jan 2015
I am a part of an engineering team that uses our combinations of skills and experience to solve problems, create solutions along with redesigning operations to meet demand. Using the 5S systems, Kaizen ideology, with quality control concepts that improve work flow along with increasing the output with the same resources and assets. I am currently adding to the team with my wide range of work experience that consists of experiences in many large operations of contract government work, field service management for a petroleum company that covers the Atlanta metro area, and a customer service technician with an automotive service facility in Marietta. Along with a lifetime of mechanical, electrical, and manufacturing experiences that I have been a part of through my career.
-
-
-
-
Process improvement intern
-
May 2013 - Aug 2013
Worked with the Stormwater manager to outline and document the stormwater system within the city. in addition creating a database of the information captured from the field to make track all of the changes made to the system for mapping to be accurate in the GIS database. Created process documents within the public works department to document current operations so the city could better understand the needs of the operations. This allowed staffing, equipment, and time needs to be able to allocated appropriately.
-
-
Education
-
Southern Polytechnic State University
Bachelor of Science (BS), Industrial Engineering Technology -
Brewbaker Technology Magnet High School
Diploma, Architectural and Building Sciences/Technology
Community
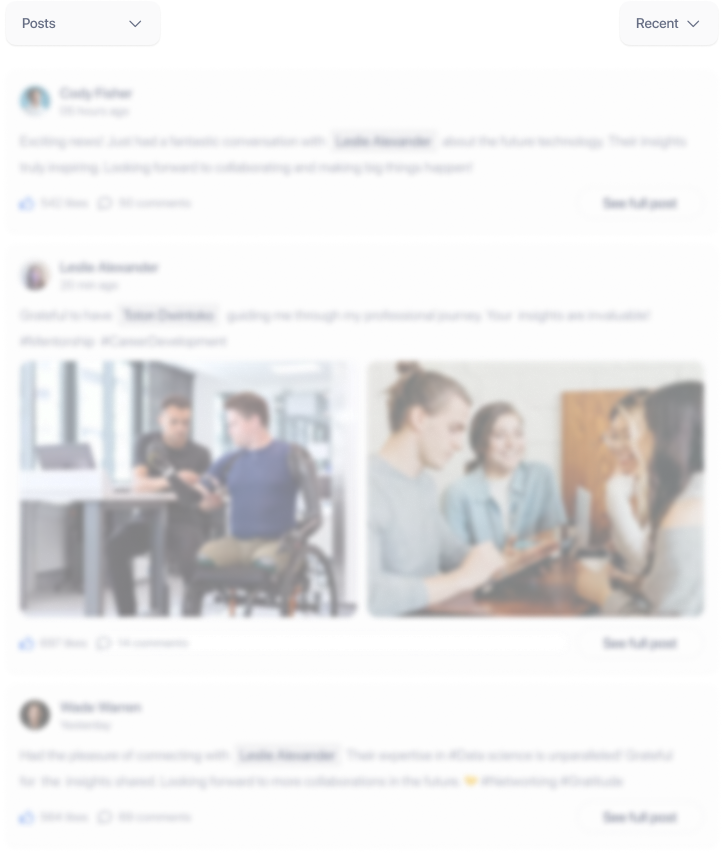