Justin Woodall
Maintenance Controller at Pacific Coast Jet- Claim this Profile
Click to upgrade to our gold package
for the full feature experience.
-
English -
Topline Score
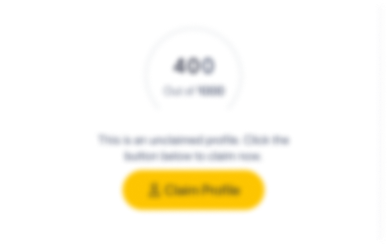
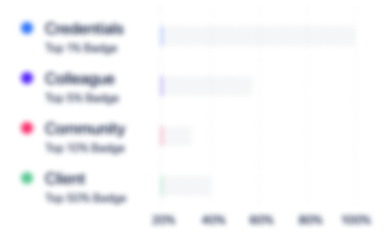
Bio


Credentials
-
Airframe & Powerplant License
Federal Aviation AdministrationMay, 2016- Nov, 2024 -
Professional Manager Certification
Community College Of The Air ForceMay, 2014- Nov, 2024
Experience
-
Pacific Coast Jet
-
United States
-
Airlines and Aviation
-
1 - 100 Employee
-
Maintenance Controller
-
Mar 2021 - Present
● Manage daily and scheduled maintenance requirements of fleet aircraft operating under 14 CFR Part 91 and 135 (CE 510, 525/A/B, 560XL/S, 680, 750; PC-12; CL604/605; Phenom 300, G-IV). ● Direct company maintenance personnel ensuring work is accomplished in a safe, timely and effective manner. ● Ensure all work accomplished adheres to 14 CFR Parts 43, 91, 119 & 135 and company standards. ● Create and maintain positive working relationships with maintenance vendors, manufacturers, outside companies, FAA, and organizations ensuring effective collaboration and resolution of department needs. ● Review all work accomplished by maintenance personnel and return aircraft to service per established guidelines. ● Proactively ensure all necessary parts, tooling, equipment, and technicians are available for both scheduled and AOG maintenance events, enabling both reduced downtime and lower event expenditures.
-
-
-
XOJET Aviation
-
United States
-
Airlines and Aviation
-
200 - 300 Employee
-
Maintenance Controller
-
Feb 2018 - Mar 2021
● Managed daily maintenance requirements of fleet aircraft (Citation X, Challenger 300/350, Global 5000/7500). ● Debriefed aircrews on maintenance issues, ensuring proper documentation of discrepancies and other concerns. ● Effectively applied and managed fleet MELs/NEFs/CDLs ensuring adherence to pertaining regulations. ● Responsible for building, scheduling, and releasing fleet MX and detailing work orders to the appropriate vendors. ● Ensured accurate and timely information is conveyed to operations for AOG and delayed aircraft. ● Provided oversight and management of fleet during MX events. ● Responsible for releasing aircraft for RTS in accordance w/ company and FAA guidelines, including Airworthiness Releases and Special Flight Permits. ● Monitored Fleet MX and ensure its completion in a timely manner, never to exceed governing time limitations.
-
-
-
DynCorp International
-
United States
-
Defense and Space Manufacturing
-
700 & Above Employee
-
Quality Control Inspector
-
Mar 2017 - Feb 2018
● Managed Quality/Safety program by evaluating aircraft maintenance repairs and personnel performing maintenance to ensure regulatory compliance and adherence to published technical manuals. ● Conducted Root Cause Analysis for discrepancies found during audits/inspections and applied proper corrective actions to programs and procedures to eliminate/reduce hazards/risks and ensure regulatory compliance. ● Developed Quality Control programs to ensure compliance with regulatory (OSHA and AF) and company policies. ● Assisted with parts research and compared specifications, ensuring compliance with regulatory requirements. ● Provided technical advice and assistance to maintenance personnel and the work force. ● Inspected organizational compliance to company policies and developed procedures to correct negative trends. ● Conducted Quality, Safety, Environmental and Hazardous Material assessments and audits/inspections, and shared findings thru inter-agency meetings to find and collaborate on best practices to resolve any issues found. ● Provided remedial training courses to the workforce ensuring standards were maintained.
-
-
-
Mondi Group
-
Austria
-
Packaging and Containers Manufacturing
-
700 & Above Employee
-
Production Superintendent
-
Aug 2016 - Mar 2017
• Responsible for the day to day production operations on the manufacturing floor. • Conducted employee meetings to facilitate continuity with shift turnovers and successful continued operations. • Promoted a safe working environment that was producing above the established expectations. • Provided leadership and direction to the hourly union workforce within company policies and guidelines. • Ensured all employees followed safety rules and procedures. • Ensured all production records were recorded and approved for accuracy. • Monitored OEE (Overall Equipment Efficiency) for trending direction of production/set-up/down-time/waste and provided feedback and direction to hourly workforce. • Ensured housekeeping standards were enforced and maintained on a daily basis. • Provided employee assistance in areas of deficiencies that may require additional training, coaching or disciplinary action. Provided feedback and follow up with employees as necessary. • Completed company documentation in a timely manner with accuracy, i.e. shift reports, quality check off documentation, order sign off for approval and any company generated documentation.
-
-
-
United States Air Force
-
United States
-
Defense and Space Manufacturing
-
700 & Above Employee
-
Maintenance Operations Manager (Aircraft Section Chief)
-
Sep 2015 - Dec 2016
• Led/managed 250+ employees from 6 career fields in maintaining 12 C-130J aircraft valued at $660M.• Tracked and analyzed key performance indicators (KPIs) and metrics to detect positive and negative trends, recognize training needs, correct policy or procedure deficiencies and optimize operational efficiency.• Skillfully aligned aircraft generation with scheduled maintenance requirements. Completed 150+ detailed inspections generating 3K missions/7.1K flight hours annually enabling a 99% scheduling effectiveness rate with zero mishaps.• Managed Quality Assurance prgm. Scheduled 98 inspectors/5.3 K insp’s annually facilitating unit’s 97% pass rate.• Investigated safety incidents/damaged property. ID’d existing shortfalls and developed/implemented changes to programs and procedures to avert future loss.
-
-
Production Manager (Flightline Expediter)
-
Sep 2013 - Sep 2015
• Leads and supervises six Air Force maintenance specialties to produce aircrew training sorties. • Prioritized and scheduled over 8,000 maintenance tasks and effectively allocated 31K labor hours to achieve aircraft availability rates 1.9% above USAF standards and exceed production goals by up to 20%.• Coordinated aircraft availability with Ops flying schedule to provide safe, reliable aircraft for mission accomplishment.• Enforced mx directives, technical data, foreign object damage prevention and hazardous waste procedures.• Conducted training to remedy skills deficiencies. Ensured compliance with U.S., AFOSH and OSHA regulations.• Oversaw team for 3 month ops surge/109 sorties. Erased 30-day deficiency/reduced backlog 85%.• Energized maintenance effort promoting team cohesion. Drove unit to exceed 10/10 performance-based metrics.
-
-
Assistant Maintenance Operations Manager (Assistaint Section Chief)
-
Mar 2012 - Sep 2013
• Planed, implemented, and supervised upgrade/transition training for the aircraft maintenance unit. • Ensured qualified technicians were available to meet the production supervisor's needs eliminating shortages/over ages/stoppages on shifts. • Oversaw program management ensuring vital areas were covered to include safety, foreign object damage prevention, operational risk management and vehicles.• Point of contact for the unit's in-processing/out-processing troops. • Evaluated task qualification, training, and readiness of all assigned personnel. • Administered and tracked unit's enlisted performance reports. • Obtained additional information through discussion with supervisors and technicians on complex issues. • Maintained unit's monthly and yearly personnel awards program. • Explained personnel procedures to managers and employees and assisted in interpreting and applying guidance to answer general personnel-related questions. • Formulated all budget requirements, plans and inputs for the unit. • Responsible for managing and tracking all personnel actions and inputting them into the appropriate system. • Continually monitored the unit manpower document and creates the appropriate request for personnel actions.
-
-
Training Manager
-
Jan 2011 - Mar 2012
• Managed units training database; maintained 64 training records/4K upgrade tasks. Ensured on-time upgrades.• Led implementation of ancillary/training database user guides. Cut unit’s monthly training suspense's by 5 days.• Pushed squadron's annual qualification/ancillary training for personnel. Processed 1.5K tasks with zero defect.
-
-
Aircraft Maintenance Technician
-
Jan 2006 - Jan 2011
• Supported the generation of 26 assigned C-130E/H aircraft flying over 9,500 flt hours and 4,000 sorties annually.• Primarily performed aircraft launch, recovery, inspection, towing, jacking, and servicing on assigned aircraft. Performed maintenance on all systems as needed. Engine run qualified. • Ensured timeliness and quality of aircraft forms, automated maintenance system, parts tags, and Air Force forms.• Led a 12-member team responsible for the successful completion of over 20 Home Station Check (Phased) Inspections. Coordinated with numerous agencies to obtain the required parts/manpower, minimizing down-time and ensuring a 100% on-time completion rate.• Performed maintenance as required when aircraft were off-station, flying with the aircraft and ensuring minimal downtime if required.
-
-
Human Resources Recruiter
-
Dec 2001 - Dec 2005
• Supervised, led, and motivated personnel in the Delayed Entry Program (DEP) and directed all Air Force recruiting activities in a highly populated area of 439,000 people. • Interviewed, tested, and evaluated quality applicants to meet diversified and critical Air Force needs.• Completed enlistment documents that become part of the applicant's personnel file. • Conducted and maintained comprehensive market and productions analysis to determine goal allocation. • Hosted Center of Influence functions with community leaders and potential recruits to increase Air Force awareness. • Conducted advertising and promotion programs essential for Air Force visibility in local academic institutions. • Managed recruiter generated mail program and conducts telemarketing tasks and follow-up. • This was a selectively manned position.
-
-
Aircraft Maintenance Technician
-
Mar 1996 - Dec 2001
• Responsible for maintenance activities on assigned C-5 aircraft valued over $150M each. • Ensured timeliness and quality of aircraft forms, automated maintenance systems, parts tags and Air Force forms. • Enforced the use of maintenance directives, technical data, supply, safety, and hazardous waste procedures.
-
-
Education
-
Embry-Riddle Aeronautical University
Bachelor of Science (BS), Aeronautics (Double Minor in Aviation Safety & Management) -
Community College of the Air Force
Associate of Science (A.S.), Human Resources Management/Personnel Administration, General -
Community College of the Air Force
Associate of Science (A.S.), Aviation Maintenance Technology
Community
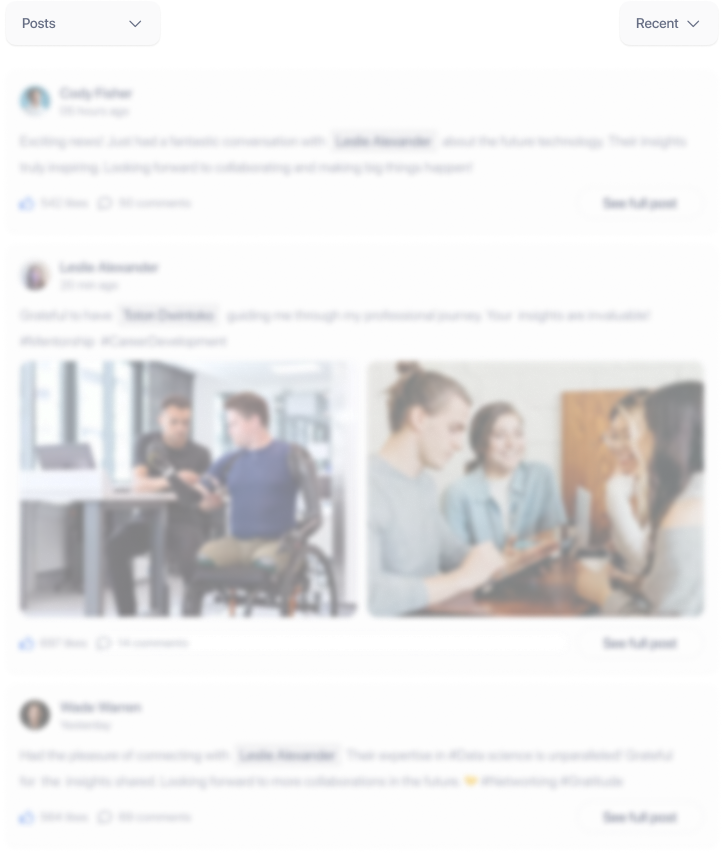