Justin Gauthier
Operations Manager at KGH Equipment- Claim this Profile
Click to upgrade to our gold package
for the full feature experience.
Topline Score
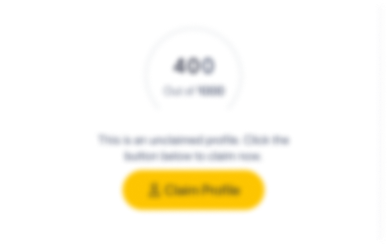
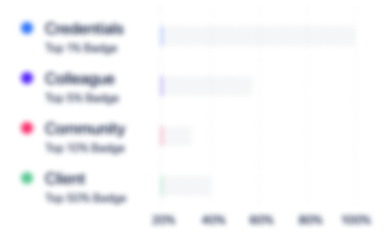
Bio


Credentials
-
Inspection Facility Operator
Ministy of TransportationDec, 2022- Oct, 2024
Experience
-
KGH Equipment
-
Canada
-
Construction
-
1 - 100 Employee
-
Operations Manager
-
Mar 2023 - Present
-
-
-
Arrow Transportation Systems Inc.
-
Canada
-
Truck Transportation
-
100 - 200 Employee
-
Division Manager
-
Jul 2022 - Mar 2023
• Responsible for annual Divisional strategic planning and budgeting. Focus must be on maximizing productivity and striving for least total cost operating position. • Ensure the division is financially successful but never at the expense of safety, regulatory and legal compliance. • Manages local operation towards high quality of customer service at least possible cost. • Ensures that Divisional assets are utilized to maximum productivity. • Oversees Division maintenance to ensure that company, industry and government regulations and standards are met. Plans to minimize equipment total maintenance cost over the life of the assets. • Responsible for divisional human resource planning and utilization. • Ensures the divisional processes are conducted as per the Operations Excellence, company and divisional S.O.P’s. • Builds a team of motivated, efficient and productive employees and coordinates their efforts through strong leadership, coaching and direction. • Provides employee-sensitive, considerate, courteous leadership through consistently fair treatment of people so that a relationship of mutual trust and support is maintained. Creates an honest and open communications environment which involves participative problem solving. Shares information with all employees so that a mutual understanding and appreciation of the company business is ensured. • Oversees the company’s safety policies and programs, ensures full compliance and leads by example in this area. • Cultivates and maintains a productive relationship with Arrow’s customers, and the local community.
-
-
-
Cam Tran Co. Ltd.
-
Canada
-
Appliances, Electrical, and Electronics Manufacturing
-
1 - 100 Employee
-
Lean Leader
-
Sep 2019 - Jul 2022
• Orchestrate lean structure throughout the company at 5 facilities through collaboration with other leaders.• Conceive and deploy key performance indicators, visual management tools, and in-house lean certification programs to establish robust processes and results. • Partner with HR department to create and execute leadership structure and performance management that is adopted companywide, from the shop floor to plant managers.• Verify employees’ roles contribute to customer value, measured by production time, waste, and quality. • Coach and mentor employees to drive the lean vision. • Execute lean initiatives and events in critical areas throughout the business. • Optimize and share best practices, and act as a conduit to accelerate cross business programs.
-
-
Process Improvement Leader
-
May 2015 - Sep 2019
• Facilitated the design and implementation of new/improved process models and organizational structures. • Performed project management, analytics, and measure to ensure milestones are met and deliverables are achieved.• Collaborated with teams in-person and remotely in various facilities to complete specific projects with measurable targets.• Developed process analysis and re-engineering to improve efficiency, lower costs, and improve product quality. • Coordinated with various teams to scrutinize projects results and performance, and identified and monitored resources with goal of delivering effective solutions. • Oversaw teams to ensure adherence to approved company operating methods and procedures.
-
-
Operations Team Lead
-
Nov 2011 - May 2015
• Deployed and allocated manpower and daily resources to achieve client requirements.• Directed operators on daily procedures to ensure efficiency and accuracy.• Offered training to employees to foster a culture of continuous improvement, encouraging teamwork, cooperation, and productivity.• Boosted company’s day-to-day efficiency, communicating effectively with interdepartmental staff and helping company achieve its goals. • Innovated tangible contributions to the advancement of organizational goals and practices by developing work schedule and ensuring employee adherence to it for successful implementation.
-
-
Quality Assurance Technician
-
May 2008 - Nov 2011
• Reinforced company and quality standards by conducting quality tests, performing inspection checks, calibrating equipment, and communicating test results. • Exceeded customer expectations through ensuring day-to-day operations met high quality standards. • Drove corrective actions from the production teams by creating Nonconformance reports. • Optimized profits by reducing waste and identifying more efficient methods of conducting business. • Validated quality processes by establishing product specifications and quality attributes, measuring production, documenting evidence, determining operational and performance qualification, and writing and updating quality assurance procedures.
-
-
Production Worker
-
Oct 2006 - May 2008
-
-
-
-
Lead Hand
-
Mar 2003 - Oct 2006
-
-
Education
-
University of Fredericton
Executive MBA, Innovation Leadership
Community
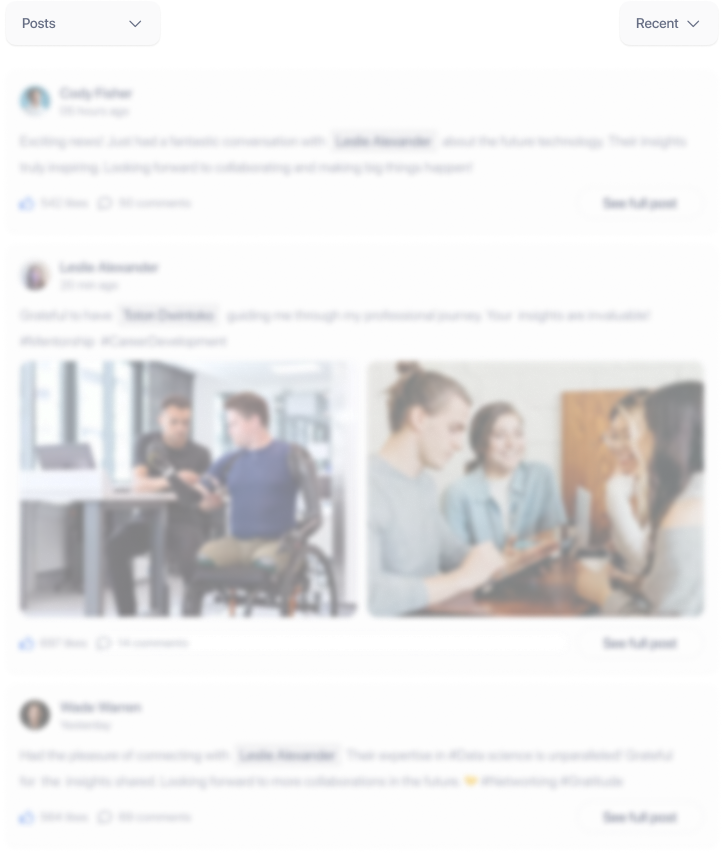