
Justin Edward Dickamore, IMBA
Senior Principal Subcontract Manager at Raytheon- Claim this Profile
Click to upgrade to our gold package
for the full feature experience.
-
Portuguese Professional working proficiency
Topline Score
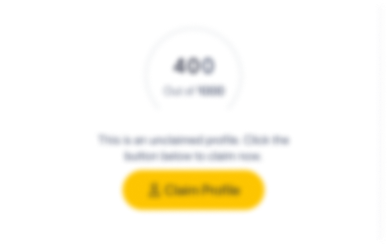
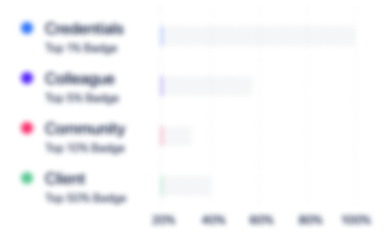
Bio

Brian Tuthill, C.P.M.
Justin is a self starter; he is always well prepared and excels in challenging / changing environments. Justin worked for me on a high profile nuclear fabrication project. He always kept his cool despite constant changes, and was a trusted and well respected member of the team. He is driven to succeed, tackles the ordinary with the same enthusiasm as the extraordinary, and always delivers exceptional results. Justin has my highest recommendation!

Matthew Mazur
In any business, especially one of the largest construction projects in the world at the time which is where I met and worked with Justin, having the right material at the right time at the right price is critical. The sourcing requirements to build a nuclear new build power plant are absolutely immense. Justin was not only successful with the core skill requirements of handling sourcing on such a large scale but also, even though officially part of a different team, also large contributor to my own success in my role. He was always available to answer questions with both a broad and technical understanding of the plant, the process of building it, and the materials that were needed. Beyond his willingness take my regular phone calls with constant questions he was always a positive contributor to the environment. He was always positive and solution oriented and eager and excited to share his knowledge and help others learn more. I would be excited to work with Justin again and if I ever come across an opening I think he'd be interested in I'd be the first to recommend him to any manager!

Brian Tuthill, C.P.M.
Justin is a self starter; he is always well prepared and excels in challenging / changing environments. Justin worked for me on a high profile nuclear fabrication project. He always kept his cool despite constant changes, and was a trusted and well respected member of the team. He is driven to succeed, tackles the ordinary with the same enthusiasm as the extraordinary, and always delivers exceptional results. Justin has my highest recommendation!

Matthew Mazur
In any business, especially one of the largest construction projects in the world at the time which is where I met and worked with Justin, having the right material at the right time at the right price is critical. The sourcing requirements to build a nuclear new build power plant are absolutely immense. Justin was not only successful with the core skill requirements of handling sourcing on such a large scale but also, even though officially part of a different team, also large contributor to my own success in my role. He was always available to answer questions with both a broad and technical understanding of the plant, the process of building it, and the materials that were needed. Beyond his willingness take my regular phone calls with constant questions he was always a positive contributor to the environment. He was always positive and solution oriented and eager and excited to share his knowledge and help others learn more. I would be excited to work with Justin again and if I ever come across an opening I think he'd be interested in I'd be the first to recommend him to any manager!

Brian Tuthill, C.P.M.
Justin is a self starter; he is always well prepared and excels in challenging / changing environments. Justin worked for me on a high profile nuclear fabrication project. He always kept his cool despite constant changes, and was a trusted and well respected member of the team. He is driven to succeed, tackles the ordinary with the same enthusiasm as the extraordinary, and always delivers exceptional results. Justin has my highest recommendation!

Matthew Mazur
In any business, especially one of the largest construction projects in the world at the time which is where I met and worked with Justin, having the right material at the right time at the right price is critical. The sourcing requirements to build a nuclear new build power plant are absolutely immense. Justin was not only successful with the core skill requirements of handling sourcing on such a large scale but also, even though officially part of a different team, also large contributor to my own success in my role. He was always available to answer questions with both a broad and technical understanding of the plant, the process of building it, and the materials that were needed. Beyond his willingness take my regular phone calls with constant questions he was always a positive contributor to the environment. He was always positive and solution oriented and eager and excited to share his knowledge and help others learn more. I would be excited to work with Justin again and if I ever come across an opening I think he'd be interested in I'd be the first to recommend him to any manager!

Brian Tuthill, C.P.M.
Justin is a self starter; he is always well prepared and excels in challenging / changing environments. Justin worked for me on a high profile nuclear fabrication project. He always kept his cool despite constant changes, and was a trusted and well respected member of the team. He is driven to succeed, tackles the ordinary with the same enthusiasm as the extraordinary, and always delivers exceptional results. Justin has my highest recommendation!

Matthew Mazur
In any business, especially one of the largest construction projects in the world at the time which is where I met and worked with Justin, having the right material at the right time at the right price is critical. The sourcing requirements to build a nuclear new build power plant are absolutely immense. Justin was not only successful with the core skill requirements of handling sourcing on such a large scale but also, even though officially part of a different team, also large contributor to my own success in my role. He was always available to answer questions with both a broad and technical understanding of the plant, the process of building it, and the materials that were needed. Beyond his willingness take my regular phone calls with constant questions he was always a positive contributor to the environment. He was always positive and solution oriented and eager and excited to share his knowledge and help others learn more. I would be excited to work with Justin again and if I ever come across an opening I think he'd be interested in I'd be the first to recommend him to any manager!

Credentials
-
The Complete SQL Bootcamp
UdemyOct, 2016- Oct, 2024 -
Strategic Management and Leadership - Level 7
Chartered Management InstituteJul, 2016- Oct, 2024
Experience
-
Raytheon
-
United States
-
Defense and Space Manufacturing
-
700 & Above Employee
-
Senior Principal Subcontract Manager
-
Dec 2019 - Present
-
-
Principal Subcontract Manager
-
Dec 2017 - Dec 2019
-
-
-
Westinghouse Electric Company
-
Nuclear Electric Power Generation
-
700 & Above Employee
-
Onsite Procurement Manager
-
Dec 2016 - Dec 2017
-
-
Nuclear Sourcing Analyst III
-
Dec 2015 - Dec 2016
Westinghouse Electric Company is a world supplier of nuclear technology. Providing dependable nuclear power plants, nuclear fuel, plant automation and operating plant products and services. 12,000 employees working on innovation, safety, and sustainability. WECTEC LLC (subsidiary of Westinghouse Electric Company) is the EPC portion of Westinghouse Electric Company. WECTEC provides engineering, procurement, and construction efforts for new nuclear power plants including the first being built in the United States in the last several decades.- Procure nuclear grade items (NQA-1 & ASME) based on MRP and engineering needs- Provide procurement management for 20 purchase orders approximately $50,000,000 at 4 nuclear sites- Work with inventory management to ensure delivery of products and services to sites- Utilize ERP system (Smart Plant) to enter and maintain purchase orders- Evaluate RFQ with commercial analysis to find best delivery and most economical supplier- Negotiate contract terms, pricing, and delivery with suppliers for purchase orders- Resolve shipping discrepancies with construction sites’ material management group and supplier representatives- Expedite material according to construction need dates to minimize damages and delays for sites- Plan and coordinate supplier meetings collaborating with expediting, engineering, and documentation to inform suppliers of policies and procedures- Conduct status meetings with suppliers in conjunction with engineering and expediting to ensure construction and delivery schedule is being maintained
-
-
-
CB&I
-
United States
-
Oil and Gas
-
700 & Above Employee
-
Material Manager
-
Sep 2008 - Aug 2014
CB&I is a leading provider of technology and infrastructure for the energy industry. With over 125 years of experience and the expertise of more than 40,000 employees, CB&I provides reliable solutions to our customers around the world while maintaining a relentless focus on safety and an uncompromising standard of quality.Fabrication and Manufacturing is one of the business units within CB&I. It accounts for roughly 15 to 20 percentage of total revenue. Engineering- Revise shop drawing according to isometrics- Review isometrics in conjunction with shop drawings for accuracy- Review shop drawing for correct BOM (bill of materials)Planning- Enter customers work orders into ERP (JD Edwards) for fabrication- Collaborate with engineering on discrepant drawings- Perform material take-offs of customer isometrics to forecast demands- Input forecasted demands into MRP system- Run MRP to assess material need for procurement- Optimize inventory planning utilizing surplus material Materials/Inventory- Maintain inventory levels of 2,000 SKUs for shop production- Conduct inventory maintenance through cycle counting and physical inventory- Utilize in stock SKUs for active project to reduce project costs and stock material levels- Reconcile logical inventory distribution- Document and resolve NCRs (non-conformance) on incoming material and customer orders- Conduct trainings to decrease non-conformance occurrencesProcurement- Forecast demand for production and evaluate for requisitions- Perform commercial bid evaluations to choose the best supplier- Procure raw materials according to MRP demand needs totaling $300,000 monthly- Enter and maintain purchase orders within ERP (JDE)Training- Train 5 to 10 employees on policies and procedures to improve processes- Present new procedures and processes to increase efficiencies- Train 3 employees on MRP- Train 10 employees on corporate policies and procedures on inventory and storage
-
-
-
The Shaw Group
-
United States
-
Oil and Gas
-
200 - 300 Employee
-
Recieving Clerk (promoted to Material Manager)
-
Feb 2008 - Sep 2008
The Shaw Group was founded in 1986 specializing as a fabrication shop. The Shaw Group expanded into a major EPC. Shaw provided engineering, construction, maintenance, technology, fabrication, remediation and support services for clients in the energy, chemicals, environmental, infrastructure and emergency response industries.Naptech Fabrication Facility located in Clearfield, UT was a part of the Fabrication and Manufacturing (F&M) division. Building piping spools for nuclear, oil, and gas industries.- Managed receipt of raw material (pipe, fittings, flanges, and valves)- Received according to purchase order, packing list, and MTRs (material test reports)- Verified material and reported non-conformance material per non-conformance procedure- Stored raw material per company and customer procedures and instructions- Distributed raw materials into fabrication shop according to customer work orders- Prepared material (piping, fittings, flanges, and valves) for physical inventory- Reconciled discrepant material from work orders
-
-
Education
-
Utah State University
Master of Science (MS) - Food and AgriBusiness, Food and Agribusiness -
Royal Agricultural University
International Master of Business Administration (IMBA), Food and Agribusiness -
Weber State University
Bachelor of Arts, Business Administration -
Weber State University
Assoicates, General Studies
Community
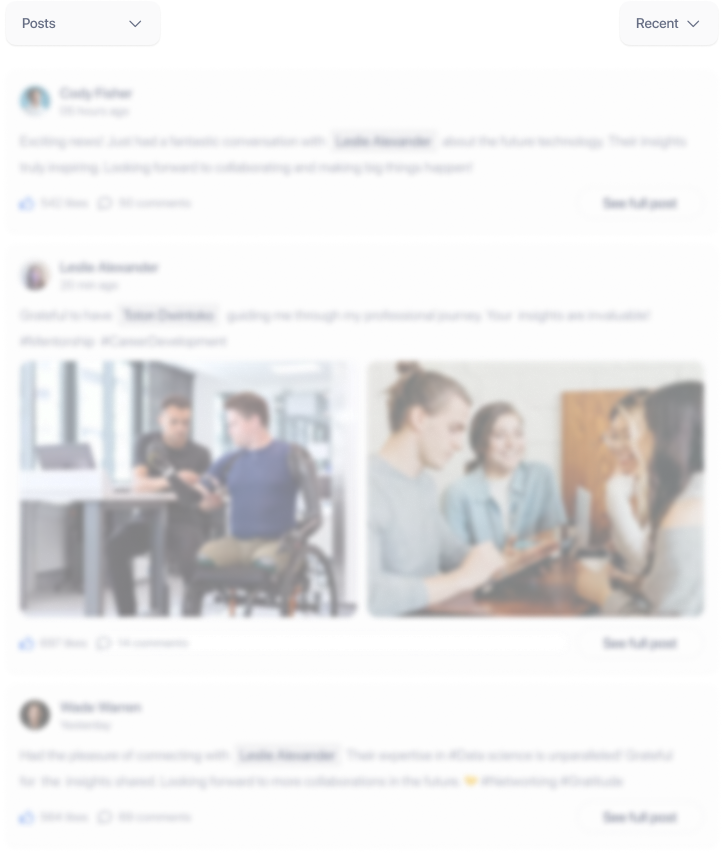