Julie Granath
Aftersales Manager - Renault, Dacia & Alpine at RN Nordic- Claim this Profile
Click to upgrade to our gold package
for the full feature experience.
-
Swedish -
-
English -
-
German -
-
Arabic -
Topline Score
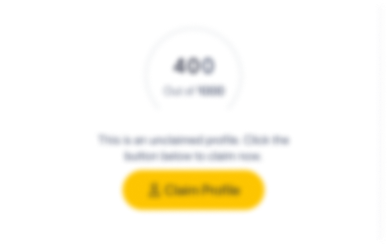
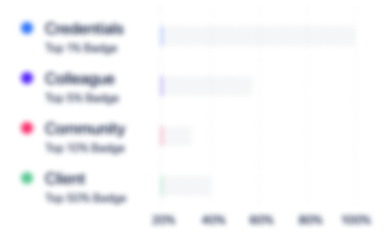
Bio


Credentials
-
NPM - New Performance Management - Employees digital path
CrossKnowledgeNov, 2021- Oct, 2024
Experience
-
RN Nordic
-
Sweden
-
Motor Vehicle Manufacturing
-
1 - 100 Employee
-
Aftersales Manager - Renault, Dacia & Alpine
-
Jul 2022 - Present
Marketing, Business and Supply Chain Marketing, Business and Supply Chain
-
-
-
Renault
-
Motor Vehicle Manufacturing
-
700 & Above Employee
-
Logistics and Warehouse Manager & Senior Project Manager
-
Dec 2018 - Aug 2022
Objectives:Responsible for Renaults' aftersales logistics including warehouse, transportation and spare part support for the dealer network in Sweden, Denmark, Norway and Finland.Which includes:Managing a team of purchaser, customer and technical support and quality technican. Budget and KPI responsibilities. Monitor, handel and manage the warehouse 3PL contract and performance. As a project manager I had the responsability of implementation a Retail Inventory Management system (RIM) in the dealer network.Other tasks is to cooperate internally with product managers, warrenty department and sales team in Nordics in order to solve customer or dealer issues. Close cooperation with central logistics teams in France and other warehouses in Europe. Reported crossfunctionally to both French and Nordic mangers.
-
-
Team Leader Parts Logistics Network Support & Logistics Project Manager
-
Feb 2017 - Dec 2018
Objective:To lead the customer and technical support team.Project lead and implement two new markets to supply spare parts from the warehouse in Borås.Increase the service rate and performance by the 3PL partner DSV.Achived result:Logsitics project - started up the two new markets (Norway and Finland) to supply from the distributing warehouse in Borås. The project includes system changes, new IT-connections, addaptation in the warehouse flows, new references in stock, new linehaulings to set up, new way of working, training etc. DSV delivery performance improved from >90% to 99,5% through many improvment projects, new contract conditions and new meeting structure with close monitoring of deviations and corrective action plans.
-
-
-
SensationLabs AB
-
Boras, Sweden
-
Business consultant - Quality Management, Internal Logistics, Lean philisophy, Six Sigma
-
Jun 2015 - Feb 2017
Behöver du hjälp med att utveckla organisationens processer - administrativa eller producerande? För att höja produktkvaliten, effektivisera de interna flödena, de kundstyrda projekten eller förbättra kommunikationen? Kanske söker ni rätt slags mätningar och uppföljningar som ger resultat? Kanske är det dags att implementera lean, six sigma verktyg eller till och med påbörja er lean resa? Då är du välkommen att höra av dig! Tidigare konsultuppdrag: Jabo Nordic - produktutvecklare Syfte: utveckla innevarande sortiment samt nya produkter, höja produktkvaliten och leverantörsrelationer. Tidigare konsultuppdrag: Volvo Bussar AB - logistikprojektledare Syfte: Ett omfattande logistikprojekt med syfte att effektivisera materialpresentationen för montören och effektivisera materialförsörjningen från lagret och ut. Önskat resultat: Ytredusering per produktionsyta, ombyggnation av lagerytor, systemförändringar, förändrat leveranssätt av material (kitt, serkvesering etc) samt eliminering av gaffletruckstrafik. Levererat resultat: En förstudie med tre alternativa förslag på lagerutformning, varav en rekommenderad, ett pilotområde inom produktion med 30% reduktion i yta och 20% reduktion i produktledtid.
-
-
-
Specma AB
-
Tranemo, Sweden
-
Quality and Environmental Manager
-
Apr 2013 - Jun 2015
Objective: Minimize scrap and customer complaints by creating corrective and preventive activities together with the employees. Implement lean-tools. Be part of the local management team and the management representative in quality and environmental issues. Responsible for the company's management system (ISO 9001, 14001 and developing further towards ISO/TS 16949) including internal and external audits. Be a part of new quality requirement projects together with customers such as new cleanliness requirements etc. Achieved results: Together with the co-workers, scrap was reduced by 30% and customer complaints with 20%. Implemented lean-tools as Andon and 5S within production, standardized weekly meetings following the Safety-Quality-Delivery-Cost standard with follow-up-meetings, root-cause analysis, action plans and corrective actions. Together with the production manager started up work with preventive maintenance and reduction of set-up-time according to “SMED”. Responsible of the acquisition of a cleanliness lab that supplied all the Specma units in Sweden in verification of the cleanliness levels. Personnel/staff: Two quality technicians and a quality engineer, quality lab and a cleanliness lab (later included two lab technicians).
-
-
-
Ericsson
-
Sweden
-
Telecommunications
-
700 & Above Employee
-
Lean Six Sigma Driver
-
Jan 2012 - Apr 2013
Objective: Responsible of the improvement work at two production-lines with purpose of eliminating waste. Responsible for the lean-tools 5S, Visual management, continuous improvement and kaizen work shop. Achieved results: Implemented a one-piece-flow at the “Radio flow” which triggered a need of sequenced material and rebuilding of the warehouse (three warehouses became one picking stock). Part of an area efficiency project. Created a visual control structure for the daily planning, start-up and follow-up meetings from production to the management team, easing and clarifying prioritizing of activities. Developed lean methods by creating standards and an audit structure for 5S. Created training materials and trained the co-workers in 5S. Started a SixSigma-certification
-
-
-
Parker Hannifin
-
United States
-
Industrial Machinery Manufacturing
-
700 & Above Employee
-
Quality Coordinator & Lean Champion
-
Nov 2007 - Dec 2011
Objective: Responsible for the quality management system, internal and external audits, improvement suggestions and internal deviations. Implement lean methodology within the sales company (administrative and production flows). Running job with lean tools 5S + safety, Visual control, standardized work, and more. Train new employees in quality and lean. Achieved results: Developed expertise in lean through several lean boot camps arranged by Parker. Lead multiple lean events /value stream analyses. Created a cell/one-piece-flow at the hose-assembly and at the Order office, which reduced lead times and handling time, simplified production planning, and demanded kiting of the material. New certificate at environmental system ISO 14001.
-
-
-
Volvo Cars
-
Sweden
-
Motor Vehicle Manufacturing
-
700 & Above Employee
-
Logistics Coordinator
-
Jun 2006 - Oct 2007
Objective: Internal material handling, projects and ongoing logistics support Achieved results: Participated in projects such as the construction of new warehouses, automatic warehouse for gearboxes, construction of a production line, introduction of a new material handling system (MHS). Responsible for the new material management system resulting in continuous improvements, training and support. Continuous preparation of miscellaneous materials for logistics with close cooperation with the production.
-
-
-
-
Trainee
-
2004 - 2004
-
-
Education
-
Högskolan i Borås
Master, Quality Management/Engineering -
Högskolan i Borås / University of Borås
Bachelor's degree, Mechanical Engineering -
Bäckänggymnasiet
Naturvetenskapligt gymnasium, Naturvetenskap
Community
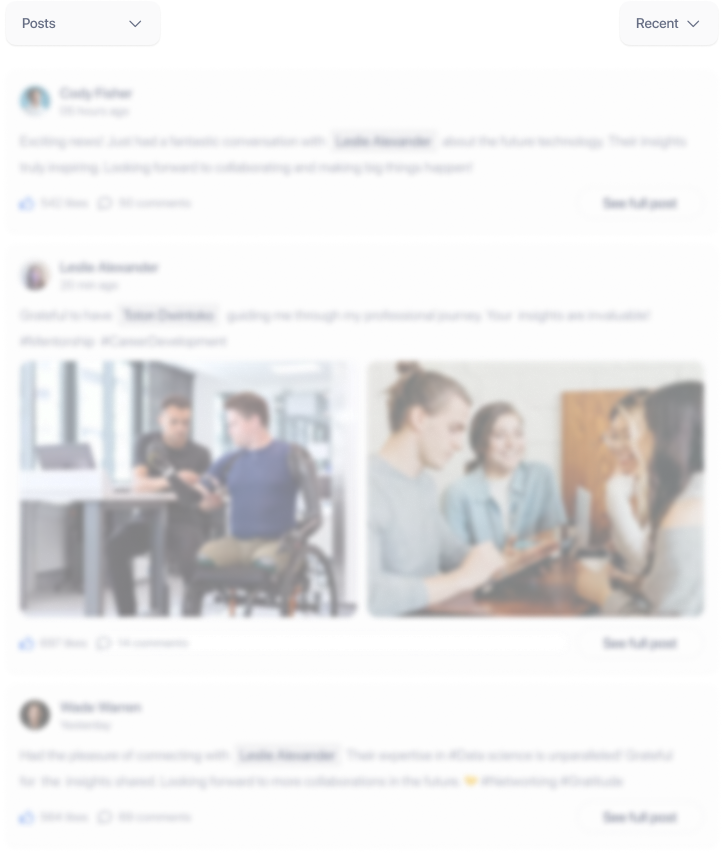