Julian Pelser
Warehouse Manager at Hylec Energy Solutions Pty Ltd- Claim this Profile
Click to upgrade to our gold package
for the full feature experience.
Topline Score
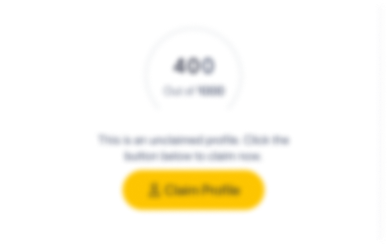
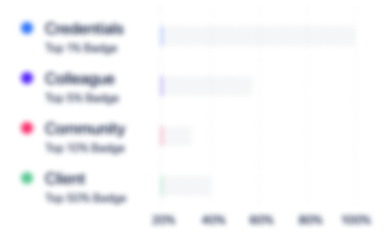
Bio


Experience
-
Hylec Energy Solutions Pty Ltd
-
Australia
-
Appliances, Electrical, and Electronics Manufacturing
-
1 - 100 Employee
-
Warehouse Manager
-
Sep 2020 - Present
• Overseeing daily warehouse and production operations with meticulous attention to detail • Establishing, implementing and overseeing effective warehouse systems, processes and controls • Supervising, coaching, training, motivating and mentoring personnel, setting clear goals and expectations, providing relevant feedback and discipline as required • Managing and conducting systematic cycle counts of inventory to ensure inventory record accuracy and assist in periodic stock takes. • Developing system improvements by analysing process work flow, manning and space requirements, and equipment layout • Customer service and liaison, building strong working relationships and effective communication channels with key stakeholders • Responsible for continuous improvement and development of warehouse design layout, product flow and product handling systems • Managing inventory records, sourcing goods from internal and external suppliers • Managing and assisting with inwards goods and dispatch. Accurate stock picking / packing as per Customer purchase orders. • Receive incoming goods, check for damage and for discrepancies between goods and invoices • Loading / unloading vehicles with listed goods, ensuring goods are loaded correctly and taking precautions with hazardous items. • Producing various reports, presentations, analyses, correspondence and quality documentation • Performing as a strong leader of a cohesive team with strict enforcement of health, safety and statutory regulations, quality standards, governance processes and compliance requirements
-
-
-
-
Warehouse Storeman
-
Feb 2020 - Aug 2020
• Accurate stock picking / packing as per Customer purchase orders • Package and dispatch outgoing goods • Over counter service to internal and external customers and recording of stock issues • Conduct systematic cycle counts of inventory to ensure inventory record accuracy and assist in periodic stock takes • Receive incoming goods, check for damage and for discrepancies between goods and invoices • Operate forklifts, high reach forklifts, pallet jacks to lift and transport items / products onto trucks, racking and around warehouse • Loading / unloading vehicles and shipping containers with listed goods, ensuring goods are loaded correctly and taking precautions with hazardous items. • General housekeeping / cleaning of stores areas and storage facilities including storage racks • Any other duties / responsibilities relative to the improvement of Product Services supply and Customer Relations as may be directed by the Warehouse Manager / Supervisor or his / her nominated representative
-
-
-
Downer New Zealand
-
New Zealand
-
Construction
-
700 & Above Employee
-
Outside Plant Senior Designer
-
Jul 2019 - Jan 2020
• Applying knowledge of telecommunications systems and practices to scope and design competitive solutions • Project management including managing costs and quality assurance systems • Producing and overseeing tenders and budgets • Supervising, coaching and motivating contractors and personnel, setting clear goals and expectations, providing relevant feedback and discipline as required • Customer service and liaison, building strong working relationships and effective communication channels with key stakeholders • Resolving onsite design enquiries • Performing as a strong member of a cohesive team with strict adherence to health, safety and statutory regulations, quality standards, governance processes and compliance requirements
-
-
-
Trelleborg Wheel Systems
-
Italy
-
Industrial Machinery Manufacturing
-
300 - 400 Employee
-
Warehouse Operations Manager
-
Jul 2017 - Jul 2019
• Overseeing daily warehouse and production operations with meticulous attention to detail • Proactively planning and coordinating production plans, requirements and priority lists • Managing cycle counting, ensuring a minimum of four completed cycles per year • Supervising, coaching, training, motivating and mentoring personnel, setting clear goals and expectations, providing relevant feedback and discipline as required • Establishing, implementing and overseeing effective warehouse systems, processes and controls • Developing system improvements by analysing process work flow, manning and space requirements, and equipment layout • Customer service and liaison, building strong working relationships and effective communication channels with key stakeholders • Responsible for continuous improvement and development of warehouse design layout, product flow and product handling systems • Managing inventory records, sourcing goods from internal and external suppliers • Managing and assisting with inwards goods and dispatch, booking in all branch containers and shipments • Overseeing plant equipment, tools and vehicle maintenance, evaluating and recommending new equipment • Producing various reports, presentations, analyses, correspondence and quality documentation • Performing as a strong leader of a cohesive team with strict enforcement of health, safety and statutory regulations, quality standards, governance processes and compliance requirements
-
-
-
-
Project Supervisor
-
Oct 2016 - Jul 2017
• Managing the delivery of critical projects, ensuring projects and programs are executed using agreed standards and processes• Costing, estimating, planning and supporting projects, tracking daily activities against detailed project plans, providing monthly financial and technical updates to senior managers• Identifying, costing and processing any contract variations• Building strong working relationships and effective communication channels with key stakeholders, liaising closely with other managers to promote overall company effectiveness• Communicating effectively with clients and suppliers• Managing personnel and subcontractors, ensuring timesheets are accurately completed• Maintaining and completing project key performance indicators (KPI)• Implementing and overseeing effective quality assurance systems• Organising and overseeing toolbox meetings• Preparing project initiation documentation, including generating work packages and instructions• Producing detailed and summarised project progress reports• Reviewing and approving all project documentation, updating project plans to include changes• Monitoring expenditure figures against project budgets• Performing as a strong leader of a cohesive team with strict enforcement of health, safety and statutory regulations, quality standards, governance processes and compliance requirements
-
-
OSP and NGA Telecommunications Designer 2
-
May 2013 - Oct 2016
• Applying knowledge of telecommunications systems and practices to scope and design competitive solutions• Project management including managing costs and quality assurance systems• Producing and overseeing tenders and budgets• Supervising, coaching and motivating contractors and personnel, setting clear goals and expectations, providing relevant feedback and discipline as required• Customer service and liaison, building strong working relationships and effective communication channels with key stakeholders• Performing as a strong member of a cohesive team with strict adherence to health, safety and statutory regulations, quality standards, governance processes and compliance requirements
-
-
-
FLSmidth
-
Denmark
-
Industrial Machinery Manufacturing
-
700 & Above Employee
-
Sales Engineer / Technical Engineering Manager
-
Jun 2010 - May 2013
• Delivering professional and technical consulting, support and trouble-shooting services to customers and colleagues in multiple branches • Managing projects from design to manufacturing stages • Overseeing drawing office and serving as board member • Designing screening panels, dies, tooling, woven wire screens, deck frames and sieve bends • Tracking production problems, conducting fault isolation and failure analysis • Performing as a strong leader of a cohesive team with strict enforcement of health, safety and statutory regulations, ISO quality standards, governance processes and compliance requirements • Managing continuous improvement initiatives and providing recommendations to quality team • Liaising with customers, managing relationships between multiple stakeholders • Writing and reviewing technical specifications, schedules, reports, manuals and operating procedures • Running a technical data system to capture company IP in drawings, manuals and other documents
-
-
-
-
Design Engineer
-
Mar 2008 - May 2010
• Providing full pack of drawings to international standards including complete sets of bills of material • Preparing and reviewing technical documentation such as manuals and operating procedures • Designing screening panels, dies and tooling, wire frames, complete screening deck frames, sieve bends and complete vibrating machines for the mining industries • Managing projects from design stage through to manufacturing, installation and commissioning phase • Liaising with OEMs • Providing full pack of drawings to international standards including complete sets of bills of material • Preparing and reviewing technical documentation such as manuals and operating procedures • Designing screening panels, dies and tooling, wire frames, complete screening deck frames, sieve bends and complete vibrating machines for the mining industries • Managing projects from design stage through to manufacturing, installation and commissioning phase • Liaising with OEMs
-
-
-
-
Design Engineer
-
Jul 2006 - Feb 2008
• Providing full pack of drawings to international standards including complete sets of bills of material • Preparing and reviewing technical documentation such as manuals and operating procedures • Designing jigs and fixtures for the automotive, glass and tooling manufacturing industries • Managing projects from design stage through to manufacturing, installation and commissioning phase • Liaising with OEMs • Providing full pack of drawings to international standards including complete sets of bills of material • Preparing and reviewing technical documentation such as manuals and operating procedures • Designing jigs and fixtures for the automotive, glass and tooling manufacturing industries • Managing projects from design stage through to manufacturing, installation and commissioning phase • Liaising with OEMs
-
-
Education
-
Nelson Mandela Metropolitan University
National Diploma, Mechanical Engineering (S1-S4)
Community
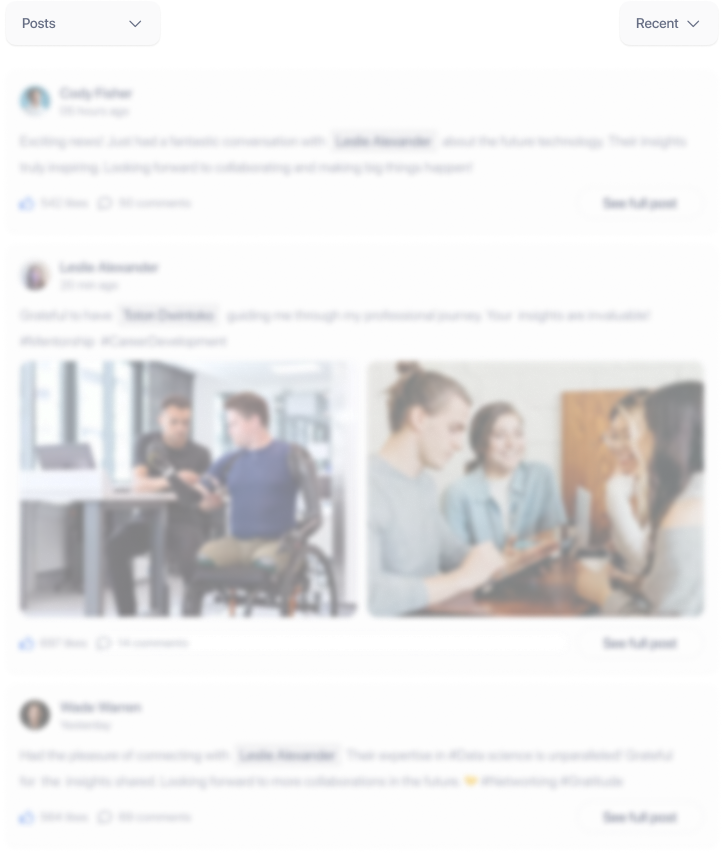