Julian Bergstein
Director Of Operations at Peerless Coffee & Tea- Claim this Profile
Click to upgrade to our gold package
for the full feature experience.
Topline Score
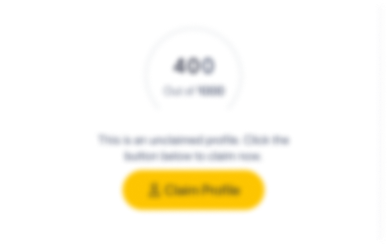
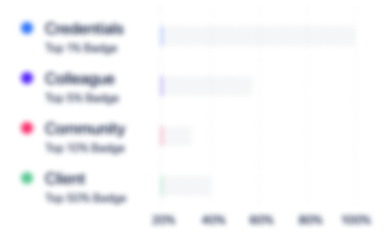
Bio


Experience
-
Peerless Coffee & Tea
-
United States
-
Food and Beverage Services
-
1 - 100 Employee
-
Director Of Operations
-
Jan 2021 - Present
-
-
-
Premier Nutrition: The Good Energy People
-
United States
-
Manufacturing
-
100 - 200 Employee
-
Senior Contract Manufacturing Manager
-
Nov 2019 - Jan 2021
Senior Co-Man Manager at Premier Nutrition owning contract negotiation and strategy, relationship management, cost savings initiatives, and overall performance and production at our external contract manufacturing facilities.-Conducting RFI and RFP processes to find new suppliers to commercialize innovation concepts (bars and beverages) at the lowest landed cost while delivering on stakeholder needs of the cross-functional team- Developing RFx templates to standardize work for strategic sourcing team for more consistent results.-Leading negotiation teams including strategy, research, defining team roles, and internal communication for multi-year contracts
-
-
Contract Manufacturing Manager
-
Aug 2017 - Nov 2019
Co-Man Manager supporting our corporate office and our co-man locations, driving Co-man KPIs, cost savings initiatives, and overall performance and production- Voted by peers as the 2018 “Good Energy Award” winner for outstanding display of our company valuesincluding being a “doer, dreamer, leader, innovator, and creative thinker who challenges the status quo"-Managing relationships at 5-10 contract manufacturers (Co-Mans) through product lifecycles (launch-to-disco) including process improvements, presenting results, and mediation of disputes-Conducting RFI and RFP processes to find new Co-Mans to optimize costs and gain category knowledge.
-
-
-
-
Co-Owner
-
May 2016 - May 2018
The Thirst Amendment is the producer of the Beer Advent Calendar and 12 Beers of Christmas products as seen on FoodandWine.com.-Designed foldable corrugate packaging to deliver structural needs while delighting consumers by hiding individual bottles (as an advent calendar)-Filed trademarks and provisional patents to defend intellectual property-Designed crowd funding campaign including video filming and editing, customer service, marketing (social/digital) The Thirst Amendment is the producer of the Beer Advent Calendar and 12 Beers of Christmas products as seen on FoodandWine.com.-Designed foldable corrugate packaging to deliver structural needs while delighting consumers by hiding individual bottles (as an advent calendar)-Filed trademarks and provisional patents to defend intellectual property-Designed crowd funding campaign including video filming and editing, customer service, marketing (social/digital)
-
-
-
Addivant
-
United States
-
Chemical Manufacturing
-
1 - 100 Employee
-
Plant Manager
-
May 2016 - May 2017
-Led an RC14001/ISO9001 certified manufacturing site including EHSS, logistics, capital projects,maintenance, HR, production, QA lab, engineering, water treatment, and acid recovery.- Designed and implemented a capital project to eliminate high risk transloading practice- Removed process bottlenecks to increase plant capacity by 20% and service additional customers- Implemented capital projects for loading accuracy and on-site scales resulting in $100K annual savings- Created operator development program including defining job level requirements, setting pay scales,and creating skills testing- Created annual financial plan including fixed cost and capital budget; led monthly reviews to reportlatest estimate and risks to financial plan- Implemented continuous improvement measures for reduction of exposure to process chemicals
-
-
-
Olin
-
United States
-
Chemical Manufacturing
-
700 & Above Employee
-
Membrane and Chlorine Area Production Supervisor
-
Aug 2015 - May 2016
-Budgeting and planning for the membrane cell room, membrane evaporator, and diaphragm and membrane chlorine drying and liquefaction-Managed membrane and chlorine area frontline operators (30 direct reports)Implemented headcount reduction in HPB area without impacting safety or production-Designed and implemented Standard 60 management plan in Hypo Area to eliminate Olin’s liability forshipping non-compliant bleach-Eliminated root cause of 2015 H2 deflagration incident with implementation of remote, continuousmonitoring system for membrane cell maintenance.
-
-
Bleach Area Supervisor
-
Jan 2015 - May 2016
Supervisor of HyPure(R) Bleach and Hypo area
-
-
Production engineer
-
Jun 2012 - Jan 2015
I was in charge of engineering support for the Powell Bleach, caustic loading, and HyPure(R) Bleach processes. Daily roles include process troubleshooting, continuous improvement of processes, debottlenecking, and implementation and commissioning of new projects.Other experience:-Commissioning and start-up of 2 new HyPure(R) Bleach plants-Start up, troubleshooting, and process improvement of water chiller systems retrofit (screw compressors from R22 to R507)-Process hazard analysis leadership-Process safety management implementationTraining:-Process hazard analysis-Statistical methods in experimentation-York Industrial Refrigeration training
-
-
-
Dow
-
United States
-
Chemical Manufacturing
-
700 & Above Employee
-
Co-Op
-
Aug 2010 - Dec 2010
Production engineering co-op for wastewater treatment process. Process experimentation for organic compound removal. Pipe code standardization project. Production engineering co-op for wastewater treatment process. Process experimentation for organic compound removal. Pipe code standardization project.
-
-
-
Dow
-
United States
-
Chemical Manufacturing
-
700 & Above Employee
-
Co-Op
-
Jan 2010 - May 2010
Production engineering co-op at acrolein and acrylic acid plant. Projects included de-bottlenecking of nitrogen system to increase system pressure, creating a process hazards and safety manual for the acrolein and acrylic acid process. Production engineering co-op at acrolein and acrylic acid plant. Projects included de-bottlenecking of nitrogen system to increase system pressure, creating a process hazards and safety manual for the acrolein and acrylic acid process.
-
-
-
Dow
-
United States
-
Chemical Manufacturing
-
700 & Above Employee
-
Co-Op
-
Jun 2009 - Aug 2009
Process modeling of acid gas removal from oil an natural gas using Procomp 8 software Process modeling of acid gas removal from oil an natural gas using Procomp 8 software
-
-
Education
-
West Virginia University
Bachelor of Science (BS), Chemical Engineering
Community
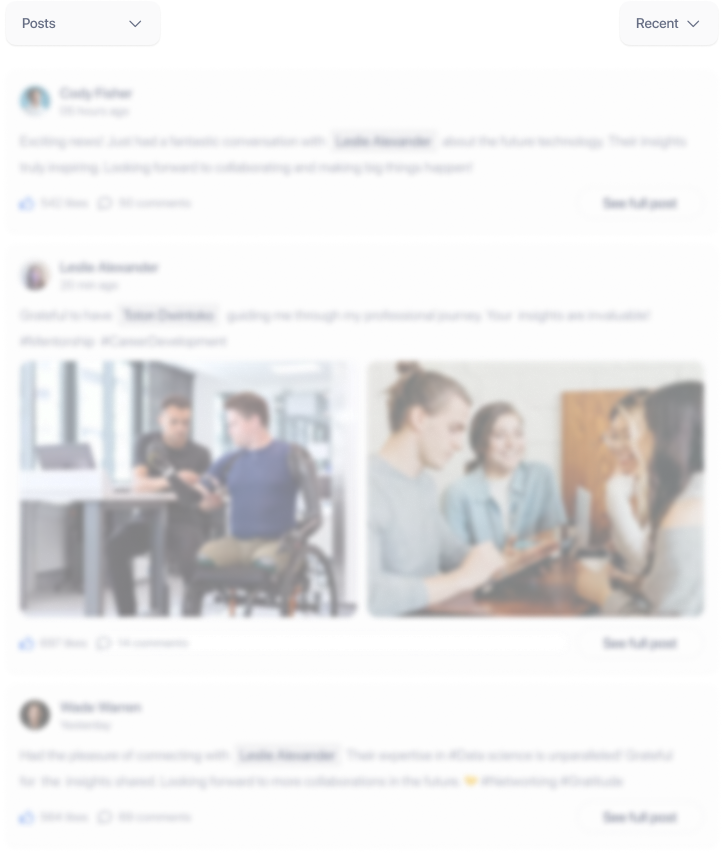