
Jude Tongo, PMP, MNSE
Plant Operations Manager at Giant Beverages Limited- Claim this Profile
Click to upgrade to our gold package
for the full feature experience.
Topline Score
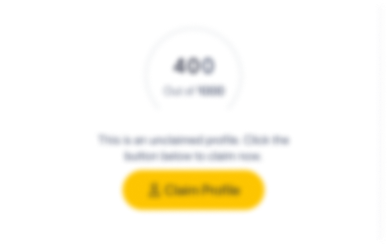
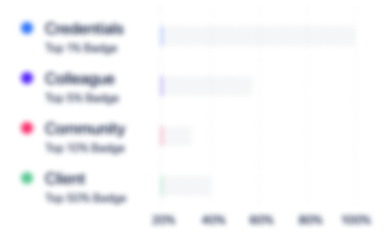
Bio


Credentials
-
Marketing Strategy Associate
VMEdu Inc.Oct, 2016- Nov, 2024 -
Scrum Fundamentals Certified
SCRUMstudy - Accreditation Body for Scrum and Agile;Download Free Scrum Body of Knowledge(340 pages)Sep, 2016- Nov, 2024 -
Six Sigma Yellow Belt Professional
VMEdu Inc.Aug, 2016- Nov, 2024 -
PMP®
SimplilearnMar, 2016- Nov, 2024 -
Project Management Professional (PMP)
Project Management InstituteApr, 2016- Nov, 2024
Experience
-
Giant Beverages Limited
-
Nigeria
-
Food and Beverage Services
-
1 - 100 Employee
-
Plant Operations Manager
-
Mar 2017 - Present
Successfully initiated Toyota Production System (TPS), via the 4P model to tackle the pending issues in the Plant.KEY RESULT AREAS•To develop processes to maximize productivity, quality and safety within the factory. •To ensure maximum up-time of all factory equipment. •Ensures that all Preventive Maintenance are carried out on the respective machines based on OEM equipment recommendations and Maintenance Schedules• Support Production schedules to meet internal goals and customers’ expectations. •Ensures policies and procedures are followed in line with business goals.•To provide clear expectations for individuals and teams and hold them accountable. Provide coaching and support.•To consistently proffer, visible, persuasive leadership to ensure effective individual and team motivation and productivity•Increase production, assets capacity and flexibility while minimising unnecessary costs and maintaining quality standards in line with the approved budget.•To be responsible for Production output quality and on time sourcing and shipping.•Directs team to identify, implement and continually improve processes and procedures in carrying out tasks.•To proactively monitor operations and trigger corrective actions if need be. •Be up to date with latest Total Quality Management practices and concepts.LATEST COURSES &TRAINING (2017)The Purpose of Finance-Finance for Non-Financial Managers, Organizational Change-Managing and Supporting Employees, Lean Six Sigma for Supply Chain, Practical Project Management for Creative Projects, Developing your Leadership Philosophy.
-
-
-
Nigerian Breweries Plc
-
Nigeria
-
Food and Beverage Services
-
700 & Above Employee
-
Engineering Manager
-
Oct 2012 - Jun 2015
Successfully eliminated the perennial bottle breakages experienced on the Bottle washer on the Packaging Line thereby reducing wastages (extract loss) by 5% and saving the company about 375000 USD that could have been spent at the end of 2014.KEY RESULT AREAS•Developed budgets, OPEX and CAPEX annually.•Supervised major projects to cover all aspects of cost, statutory regulations and required approvals.•Ensured proper adherence to company policies pertaining to energy utilization and improvement.•Made sure that all equipment failures across the factory are effectively managed and reported to the management on a timely basis.•To continuously introduce novel ideas towards attaining business objectives via benchmarking with best in class practices.•Developed a system for recording and updating all engineering related activities for planning purposes.•Ensured cost effective overhauls of all equipment and facilities in line with agreed schedules. •Consistently Improved the Packaging Line OEE viaTotal Productive maintenance methodology.•Introduced and sustained the Preventive Maintenance system of the Plant in line with the Computerized Maintenance Management System (CMMS).•Established and implemented policies, standards and procedures for all engineering and technical activities performed within the brewery.•Managed engineering KPIs in relation to Thermal Energy, Electrical Energy and Water Consumption in line with the Best-in-Class Breweries within the business.•Ensured that all projects were executed according to Safety requirements as well as to the local requirements and maintained a record of zero fatality.•Introduced 30 minutes of Cleaning Inspection Lubrication Tightening (CILT) into as part of daily operations.•Provided regular direction, mentorship, and coaching to team members by adopting the 1-2-1 system.•Introduced and enforced Lock Out and Tag Out (LOTO) system for all equipment interventions in the Plant.
-
-
-
Unilever
-
United Kingdom
-
Manufacturing
-
700 & Above Employee
-
Production Manager, Shift ( Home and Personal Care)
-
Mar 2008 - Sep 2012
KEY RESULT AREAS•Produced record-breaking volumes in the powders plant and consistently met production targets.•Reduced the plant downtime by making sure that large breakdowns are prevented and promptly attended to when they are unavoidable. •Set and Met Production Goals.•Corrected problems on Production Lines.•Always maximized the Production Process to reduce costs.•Implemented and continuously monitored quality control programs•Ensured that all staff was always aligned with the Safety, Health and Environmental (SHE) rules of Company, achieved zero fatality.•Effectively warranted operational detergent & soap plants with good overall equipment efficiency (OEE).•Had always supported the QA teams to passing the periodic plant audits•Implemented continuous improvement via Production Excellence Tools and support cost savings initiatives of the Packaging Lines.•Identified poor cleaning of equipment in both packaging and process plant and systematically introduced Cleaning Inspection Lubrication Tightening (CILT) into the daily routine.•Judiciously delivered the weekly Safety, Health and Environmental talk to all departmental staff. TECHNICAL COURSES & TRAININGIntroduction to TPM (Autonomous Maintenance), Powders Technology Course, Manufacturing Management Techniques 1 & 2, Integrated Supply Chain Management, Six Sigma- Green Belt, Just in time (JIT) versus Lean Production, Sustainability awareness & development, Business Finance & overview, Project Management Awareness, Boato Pack Equipment Training, Quality, Waste & Continuous Improvement, Project Management Fundamentals, Implementation of Strategic Management Plan, Soaps Technology Course.
-
-
Plant MTCE Engr
-
Feb 2005 - Feb 2008
KEY RESULT AREAS•Implemented SHE Standards across the site company achieved zero fatality.•Reduced the plant downtime by making sure that large breakdowns were prevented and promptly attended to.•Executed preventive maintenance on packaging & process equipment.•Eliminated breakdowns in the Process plant from 40% to 5% under a span of 18 months, via the implementation of effective Condition Monitoring and Preventive Maintenance systems within the plant.•Ensured effective maintenance standards across the factory site. Organized training, counseling and other relevant courses for the engineering team as may be required for optimal performance.•Oversaw defining and resolving of critical technical and program issues and ensured engineering support to the manufacturing team•Provision of Planned and Breakdown Maintenance (Major overhauls) of all Process & Packaging Equipment.•Drove labour cost uncertainty and irregularity down from 25% to 8%.TECHNICAL COURSES & TRAININGMaintenance Training (Mechanical Drives I & II), Autonomous Maintenance, Powder Processing TechnologyISO 9001/14000 Quality & Environmental Management System Standards, Electrical Fire Safety & First Aid
-
-
-
Mantrac Nigeria Ltd
-
Nigeria
-
Machinery Manufacturing
-
500 - 600 Employee
-
Service Engineer
-
May 2002 - Jan 2005
KEY RESULT AREAS•.Stripped, Inspected and Overhauled Caterpillar 3306, 3412, 3508, 3508, 3512, 3516 Diesel and Gas generators.•Diagnosed fault with or without the Digital Diagnostic Tools (D. D. T)/Electronic Technician (E.T).•Judiciously ensured that the Time, Corrective, Condition and Improvement based Maintenance of customers were duly and adequately met• Effectively executed Pre-delivery on Generators Sets Prior to Delivery •Carried out back – back stand by Operations. TECHNICAL & SECURITY COURSESBasic Hydraulics/Engines, Basic Electricity, power Train I & II, Electric Power Generation (E.P.G), Olympian Generators, Precision/Maintenance Practices & Procedures.Introductory HSE, Level 3 –HSE Supervision: HEMP/HSE, MS/HSE CASE/ISO 14001, Safety Seminar: Tool/Equipment Handling, Hazardous Materials etc., Unsafe Act Audit (UAA): Accident Causes/Chart, Iceberg Concept, HACCP/SOP, Risk Control/Avoidance & Retention, Fire Safety Management
-
-
Education
-
Kingston University
Master's degree, Engineering Projects and Systems Management -
University of Benin
Bachelor's degree, Mechanical Engineering
Community
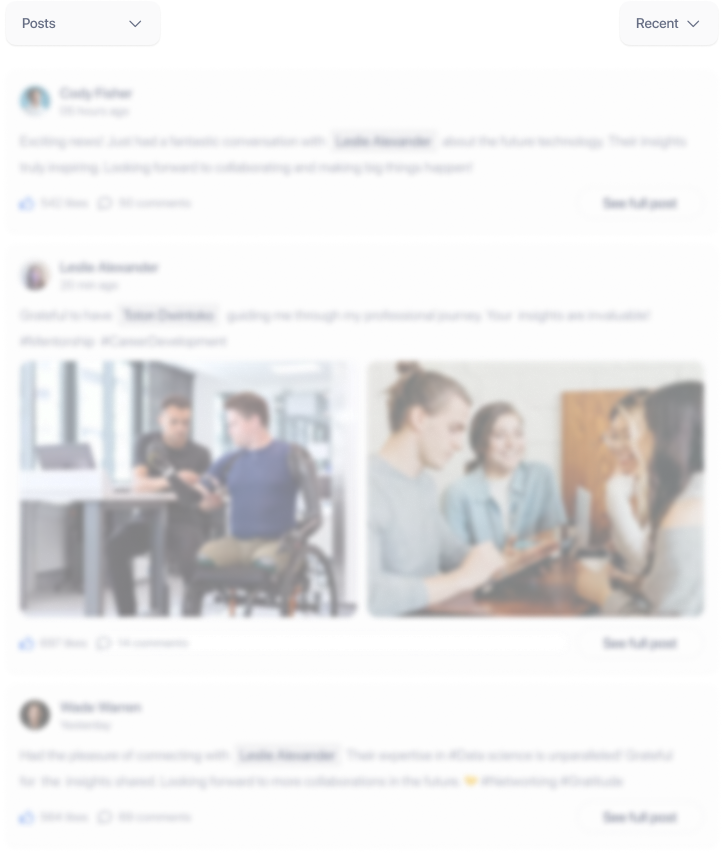