Juan José Morín Pérez
Jefe de aseguramiento de la calidad at Industrial Papelera San Luis- Claim this Profile
Click to upgrade to our gold package
for the full feature experience.
-
Español Native or bilingual proficiency
-
Ingles Full professional proficiency
Topline Score
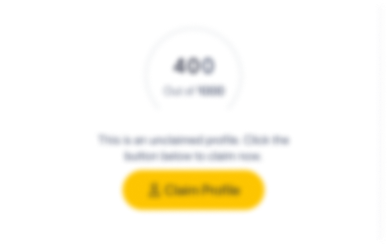
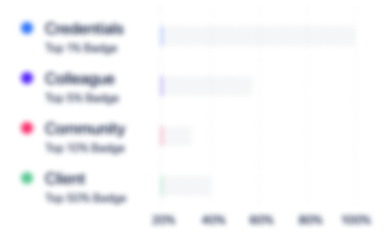
Bio


Credentials
-
Green Belt
Sigma-ProAug, 2018- Oct, 2024 -
ISO 9001:2015
Burea VeritasFeb, 2018- Oct, 2024 -
ISO / TS 16949 Quality Auditor
-Jun, 2006- Oct, 2024 -
Delegate Quality Representative Supplier (DQRS) for Pratt & Whitney USA, Rolls Royce, MTU, Airbus
Pratt & WhitneyJun, 2015- Oct, 2024
Experience
-
Industrial Papelera San Luis
-
Mexico
-
Paper and Forest Product Manufacturing
-
1 - 100 Employee
-
Jefe de aseguramiento de la calidad
-
Sep 2020 - Present
Jefe Laboratorio de pruebas Jefe Laboratorio de pruebas
-
-
-
Ramsa
-
Mexico
-
Mechanical Or Industrial Engineering
-
1 - 100 Employee
-
Customer Quality Coordinator
-
Sep 2016 - Mar 2020
I was in charge of the Quality Management for the Customer Service department and Final Inspection operations including Non Destructive Test. Reducing the % of the Customer Complaint in the first month from 25 to 10 NCR Currently in 2019 5 Customer Complaint per month. Layered Process Audits and Product Audits implementation. FAI (First Article Inspection / PPAP) reports following internal and external. Leader of the APQP for new products. 6 Sigma project as Green Belt reducing the scrap $150,000.00 USD in one year. Internal Quality Auditor ISO 9001:2015. Challenge: High customer complaints Actions: Processes (molding, pouring, heat treatment, final inspection and shipping) were mapped in order to figure out in what area there were producing the defects, there was used the pareto chart according data collect for 1 year. There were received 25 NCR´s and there were reduced to 3 in one day. Results: There were monitoring the customer satisfaction according survey sent to each customer monitoring OTD, Quality and New Projects developed. Before the mapping process the Customer Satisfaction was 45%; after corrective actions implemented in each processes the Customer Satisfaction increased to 90%. Show less
-
-
-
-
Quality Assurance Chief
-
Apr 2013 - Jun 2016
I was in charged to administrate the quality resources, Internal Quality System (AS9100), Over checking at suppliers F.A.I.R’s (tubes), Performance of F.A.I.R’s for tubes for Airbus, Rolls Royce, Honeywell, UTC, Pratt & Whitney USA-CANADA, MTU, Self-audits, Management of non-conformances product (internal and suppliers), Final Inspection of tubes, Performance of Quality rates, Customer rejections, Improvement teams; DQR representative for Honeywell, Rolls Royce-MTU Self Release, DQR Pratt & Whitney USA. KPI`s following and corrective actions for each one. Process control of Airbus line. Main Achievements: • Quality management of the quality areas (supplier, AS9100 audits, Customer, Quality process, NADCAP audits) • Customer Quality delegation to release material Rolls Royce, MTU, Airbus, Pratt & Whitney) • PPM´s reduction at 25% • Non-Quality Cost reduction at 30% • Multifunctional team developed according with the people skills • Piping Airbus line validation Challenge: Airbus line implementation. Airbus was a new customer with high quality level on the pipping products (gas, oil, air) the challenge was to produce 100% of Quality level. Actions: There was translated the Airbus quality specifications (English to Spanish) in order to deploy all Airbus requirements were understood to all people in the shop floor. There were implemented poka-yokes in all line. There was implemented the quality system. Results: The Airbus line was launched with zero defects since the beginning and we received several Quality Awards Show less
-
-
-
Meritor Manufacturing
-
Motor Vehicle Manufacturing
-
Senior Quality Engineer
-
May 2008 - Apr 2013
I was in charged to manage the inspection stations to assure its correct implementation and operation its standardized work. I developed and implemented all ISO/TS 16949 quality system work instructions, procedures, and standard work of the Gearing, Blanking Turning and Ring Rolling lines. Assure to follow the inspection requirements according of systems and policies of the organization guaranteeing the total fulfillment of the quality objectives. Reduce the percentage of scrap of the setup pieces in the C50’s machines after implementation of the master summary reset in the gearing line. I developed all the PPAP part numbers that have been produced at Meritor. I attended the quality and customer audits. Main Achievements: • I developed all the PPAP part numbers that have been produced at Meritor. (More than 200 Part Numbers; Forging, machining and Gearing sets) • It was released to production more than 60 machines on the entire gearing supply chain processes (forging, blanking and gearing) Challenge: High % of rework and scrap (% of the products) on the quench press machine after carburizing process. Actions: It was developed a DOE (Minitab technique) at the gearing area reducing the % scrap at 75%. There were defined the quenching parameters according size of the ring gears. Results: After parameters defined the % of the scrap there were reduced to 75% we received several Quality Awards for the Head Quarters for the % scrap reduction. Show less
-
-
-
TREMEC
-
Motor Vehicle Manufacturing
-
500 - 600 Employee
-
Quality Engineer
-
Sep 1999 - Apr 2008
I participated on the APQP team for new projects. I elaborated the PPAP documentation and sent it to customer approval, participating on the APQP project as part of the team. I attended the customer complaints and making continuous improvement in the gearing line. I reduced the customer complaints in Ford Australia using the 6-sigma methodology. I reduced the noise level in the Orion transmission manufacturing a gear with a different angle of pressure on the gear teeth. I received the core tools methodology. I attended the quality and customer audits, answer the non-conformities. Main Achievements: • 100% warranties reduction with General Motors transmission (199 and TR-4050), it was developed a Six sigma methodology. • 100% warranties reduction with Ford Australia transmission (T56), it was developed a Six sigma methodology. • 75% of scrap reduction at the shaft areas (parameters of the induction machine) Show less
-
-
Education
-
Universidad TecMilenio
Maestría en Administración de Negocios Área Calidad y Productividad, Six Sigma (Green Belt) -
Instituto Tecnológico de Monterrey Campus Queretaro
DIPLOMADO HABILIDADES GERENCIALES, Desarrollo de Habilidades Gerenciales -
Instituto Tecnologico de San Luis Potosi
Ingeniero Mecanico, Diseño mecanico
Community
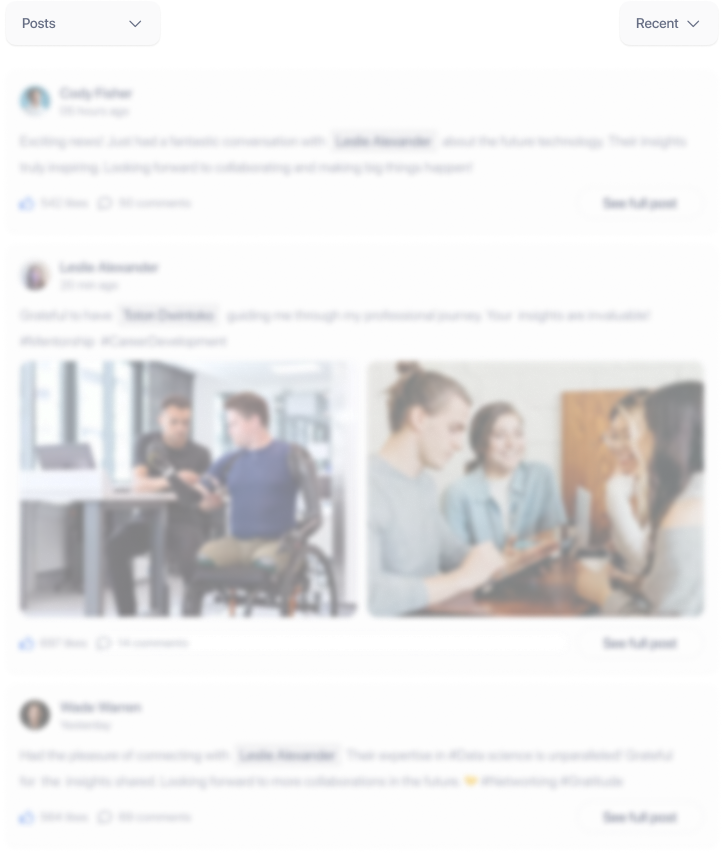