
Juan Javier Valdez
Planning, Process & Continuous Improvement Manager at Kores Europe s.r.o.- Claim this Profile
Click to upgrade to our gold package
for the full feature experience.
Topline Score
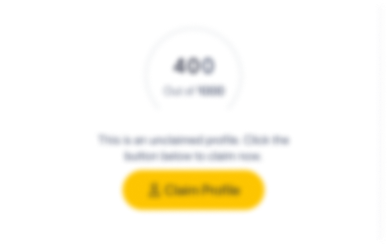
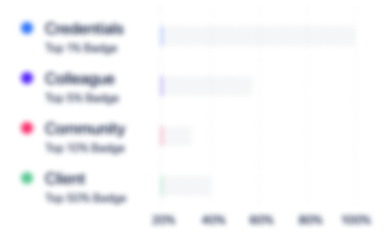
Bio


Experience
-
Kores Europe s.r.o.
-
Czechia
-
Manufacturing
-
1 - 100 Employee
-
Planning, Process & Continuous Improvement Manager
-
Dec 2021 - Present
People leader responsible for Planning, Master Data, Process & Continuous Improvement projects People leader responsible for Planning, Master Data, Process & Continuous Improvement projects
-
-
-
Mars
-
United States
-
Manufacturing
-
700 & Above Employee
-
Process and Continuous Improvement National Manager
-
2019 - 2021
Responsible to successfully launch the innovation pipeline across the 3 production segments -Gum & Confections Spicy Candy, Chocolate and Premium Chocolate- of the region. Moreover, to lead the execution of cost saving projects, standardization, continuous improvement, and problem solving at shop floor. Design for Vertical Start Up deployment leader for the region, coordinating marketing, product development, project feasibility and execution on shop floor. In charge of standardization of processes across the globe.• Succesfully led in less than a year the standardization of process sheets which opimized the production criteria to be replecated in 27 sites across the globe• Solved process chronic issue for tempering and packaging area using Six Sigma Methodology, increasing efficiency by 35% and avoiding investment in new machinery
-
-
-
Wrigley
-
United States
-
Manufacturing
-
700 & Above Employee
-
Value Stream Manager
-
2015 - 2019
Responsible for Safety KPI´s such as TRCF, LTA, Near Miss-, Quality -NQC, SCRAP, RFT-, Service -PSL, ATS, TRS, OEE-, Cost -MCC, PCC- and Moral -Engagement- for gum and confections operations unit. TPM Leader for AM and FI pillar.• Increased 50% efficiency of Orbit Gum lines using “Influence Model” to positively impact the behavior of production employees and also applying Problem Solving Tools for standardization criteria.• Improved 1.2% Right First Time for gum operations, implying $7 mill MXP and reduction of 2% of Non Quality Cost using the “Influence Model” to improve environmental and machinery conditions.
-
-
-
Hussmann
-
United States
-
Retail Groceries
-
700 & Above Employee
-
Process Engineer
-
2014 - 2015
Responsible for vertical startup of a new foaming / assembly line. In charge to develop new production standards as FMEA, Control Plan, Flow Diagrams, Standard Work Sheets, 5S´s, and others. As well as being in charge of new designs release process and cost reduction projects. • Reduced 18% cost of fabrication area by implementing a standard sheet to review design of fabrication parts.• Created the process and modification of the production line for new corner products before 6 months.
-
-
-
Siemens
-
Germany
-
Automation Machinery Manufacturing
-
700 & Above Employee
-
Manufacturing and Maintenance Engineer
-
2010 - 2014
Responsible to transfer assembly lines from Cd. Juarez, to Monterrey as well as vertical startup. In charge of Kaizen projects, maintenance budget, standardization and new products development.
-
-
Operations Leadership Development Program
-
2008 - 2010
Customer service: responsible to improve customer satisfaction by increasing fill rate from 97 to 98.5%.Warehouse: in charge to reduce in 50% the warehouse area and HC by reducing supply times 30%.Planning: responsible to buy material and plan the production of an assembly line.Plant transfer: Responsible to transfer a molding factory from Tx, USA to Cd. Juarez, Mx before plan. Manufacturing: Responsible to improve efficiency of assembly lines by working on standardization and kaizen projects.Maintenance: Responsible for facilities and lines maintenance Production: In charge of 9 welding lines and Kaizen event to improve efficiency.
-
-
Education
-
TECNOL��GICO DE MONTERREY
Industrial Engineer, Engineering
Community
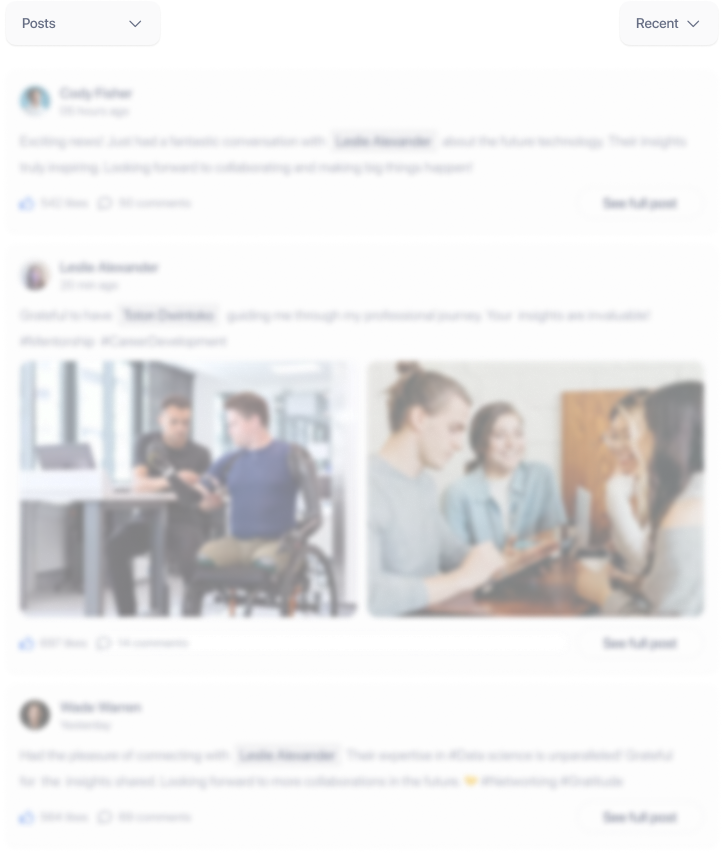