Juan Carlos Martínez Rodríguez
Plant Manager at Majorpack- Claim this Profile
Click to upgrade to our gold package
for the full feature experience.
-
Ingles -
Topline Score
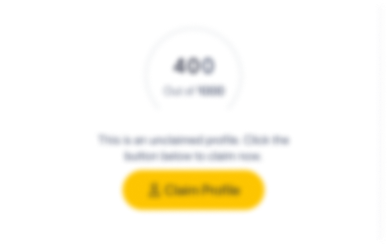
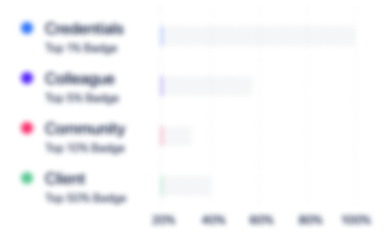
Bio

Haydeé Escamilla
Juan Carlos is a person focused to deliver results, understand and collaborate with customer through team leadership aligned with company strategy. He always shows respect, empathy and caring for his people.

Haydeé Escamilla
Juan Carlos is a person focused to deliver results, understand and collaborate with customer through team leadership aligned with company strategy. He always shows respect, empathy and caring for his people.

Haydeé Escamilla
Juan Carlos is a person focused to deliver results, understand and collaborate with customer through team leadership aligned with company strategy. He always shows respect, empathy and caring for his people.

Haydeé Escamilla
Juan Carlos is a person focused to deliver results, understand and collaborate with customer through team leadership aligned with company strategy. He always shows respect, empathy and caring for his people.

Experience
-
Majorpack
-
Italy
-
Industrial Machinery Manufacturing
-
1 - 100 Employee
-
Plant Manager
-
Mar 2023 - Present
-
-
-
Autónomo
-
Monterrey, Nuevo León, Mexico
-
Coach and Business Consultant
-
May 2022 - Mar 2023
Improve company's metrics based on professional consulting. Improve company's metrics based on professional consulting.
-
-
-
Carrier
-
United States
-
Wholesale Building Materials
-
700 & Above Employee
-
Plant Operations Manager
-
Jul 2020 - May 2022
Responsible for production team, industrial engineering and facilities. KPIS follow up. (Safety, Quality, Productivity and cost). Key player on Carrier Excellence implementation. Achievements: Production Record 157,588 units March 2020. Weekly management 5S Gemba Walk implementation. 5S cross-audit system implementation. Zone mapping according to supports and coordinators LSW. Design and implementation of Leader Standard Work for supports and coordinators. Responsible for production team, industrial engineering and facilities. KPIS follow up. (Safety, Quality, Productivity and cost). Key player on Carrier Excellence implementation. Achievements: Production Record 157,588 units March 2020. Weekly management 5S Gemba Walk implementation. 5S cross-audit system implementation. Zone mapping according to supports and coordinators LSW. Design and implementation of Leader Standard Work for supports and coordinators.
-
-
-
Weir Minerals
-
United States
-
Mining
-
700 & Above Employee
-
Plant Operations Manager
-
Sep 2016 - Jul 2020
Achievements: ISO45001:2018 certification, 0 LTI for 2 years, FPY at 96% yearly average, 17% OEE improvement on bottle neck process, 15% cost reduction on consumables expenses, 12 monthly averages on Mini Kaizen implementation, 98% OTD yearly average. Production, Production Control, Manufacturing Engieniering & Maintenance Teams responsible. VCE (LEAN) implementation, KPIS follow up. (Safety, Quality, Productivity and cost), long term production and service planning, investment project plan and execution, Service Center management, Cananea, Sonora Mex, Mining service responsibility, Kaizen Projects execution plan. Responsible for 100 operators head count in Monterrey Facility, 15 operators head count in Service Center. One Production Chief, 5 Supervisors, 1 Process Engineer, 1 Maintenance Supervisor, 1 Project Engineer and 1 Service Center Manager. Show less
-
-
-
Masonite®
-
United States
-
Wholesale Building Materials
-
700 & Above Employee
-
Production Manager
-
Nov 2015 - Sep 2016
Achievements: 0 LTI for 1 years, FPY at 90% yearly average, 23% OEE improvement on bottle neck process, 23% cost reduction on consumables expenses, 99% OTD yearly average. Responsible for production team. Leader of implementation on internal continues improvement program based on LEAN philosophy. Safety, Quality, Productivity and Cost KPI follow up and improvements programs implementation. Team Leader, 4 Supervisor, 6 Crew Leaders and 212 operators. Achievements: 0 LTI for 1 years, FPY at 90% yearly average, 23% OEE improvement on bottle neck process, 23% cost reduction on consumables expenses, 99% OTD yearly average. Responsible for production team. Leader of implementation on internal continues improvement program based on LEAN philosophy. Safety, Quality, Productivity and Cost KPI follow up and improvements programs implementation. Team Leader, 4 Supervisor, 6 Crew Leaders and 212 operators.
-
-
-
Seoyon E-hwa Automotive Mexico
-
Monterrey y alrededores, México
-
Production Manager
-
Jun 2015 - Nov 2015
Achievements: 0 LTI for 1 year, 94% start up plan accomplishment, 100% hiring plan on time accomplishment. • Responsible for production team on company's start operations. • In charge to recruit teammates, manage and coordinate all startup activities. Operator's behavior policy definition. Production management system implementation including KPI for Safety, Quality, Productivity and Cost. • Team Leader for 3 Production Engineers, 1 Supervisor, 2 Crew Leaders and 24 operators for project phase 1. Show less
-
-
-
FRISA
-
Mexico
-
Primary Metal Manufacturing
-
700 & Above Employee
-
Operation & Production Lab and NonDestructive Testing
-
Sep 2013 - Aug 2014
Achievements: 0 LTI for 1 years, FPY at 99% yearly average, 43% OEE improvement on bottle neck process, 94% OTD yearly average.• Management and coordination to laboratory and non-destructive testing.• Production planning considering increasing productivity, reducing non-operating times, line balancing work and product on time delivering scheduled.• Team Leader for technical testing: 2 supervisors and 9 operators.• Key indicators implementation and monitoring process for safety, quality, OTD, cost reduction and 5S audits.• Responsible for test results and material logistics, non-conformance material handling.• Coordinate action plans for non-conforming product.• Sample shipping logistics and coordination of delivery material and receiving results to external laboratories, 3 in USA and 1 in Monterrey.• Responsible for manage payments, costs, negotiations with external laboratories. Show less
-
-
Continues Improvement Engineer
-
Nov 2011 - Sep 2013
Achievements: Increase 23% FPY yearly average base on operative teams implementation, 89% OTD DMAIC projects implementation plan on time. Waste reduction kaizens implementation 5 monthly average.• Responsible for maintain all continues improvement initiatives in Santa Catarina Plant.• Project consultant of Operating Participative Teams activities, Kaizen events and DMAIC projects in production, maintenance, logistics and quality areas.• Responsible to train initiatives for Santa Catarina plant.• Aligning Plant objectives with all active projects, plan strategies and new projects considering the company development plans (Safety, Quality, Productivity and Cost Reduction).• Department expenses management.• Coordinate FORUMS to assign the best annual projects (surveys, playoffs, preparation of candidates, coach all participants. Show less
-
-
-
Bridgestone Americas
-
United States
-
Motor Vehicle Manufacturing
-
700 & Above Employee
-
Production Manager
-
Jan 2009 - Nov 2011
• Production management for assembly area and cured department (70% of total plant operations)• Team Leader to 135 union operators, 4 supervisors, 2 workshop coordinators, 1 kaizen leader, 1 production coordinator 1 BA and 2 students).• Responsible for production output and the monitoring of projects to improve opportunity areas in processes, reducing variation in the lines and countermeasures of poor quality.• Responsible for KPI monitoring, implementation and continuous improvement (Safety, Quality, Cost reduction, 3S)• Responsible for coordination of preventive maintenance of equipment and tooling. • Manage department expenses. Show less
-
-
Production Leader (Kaizen Leader)
-
Jun 2008 - Jan 2009
• Responsible to implement projects and improving tools to production area.• Safety, safety indicator's system implementation, incident report, safety performance chart by operator, security monitoring committee minutes.• Coordinate events of incidents for root cause analysis.• Quality management system implementation for precision equipment, implementation plan and 3S monitoring, manage rules for leftover materials, Kaizen countermeasures, material management systems to avoid overproduction.• Responsible for analyzing results of nonconforming product and perform countermeasures for recurring problems.• Production, productivity management system implementation, contingency plan for operator who has poor performance against target, system to track non-operative time control, tooling inventory control points, machine capacity control system.• Responsible to find variation in processes based on the 5M, coordinate activities to improve them.• Costs, implementation of leftover material monitoring system, analysis and improvement. Chart design to monitor department expenses. Management, inventory control, tooling damage investigation.• Non-conforming tires monitoring system implementation.• Development of suppliers of consumable tooling.• Responsible to train operation changes and process improvement projects. Show less
-
-
Industrial Engineer
-
Feb 2006 - Jun 2008
• Start-up plant activities.• Develop training plan for operators, coordinating training and progress of the plan against the process.• Supporting HR interview process for new operators.• Development budget for purchase of tooling and consumables according to production RAMP UP process. Cost analysis, purchase orders and delivery logistics.• Develop recruitment plan for union workers according to headcount calculated plan.• Time and motion study for non-productive processes according to standards, monitoring plan development of these processes to improve the current situation.• Bottlenecks peripheral processes analysis.• Implementation 3 improvement projects related to bottlenecks in the assembly process and curing tire process. Show less
-
-
Education
-
Universidad Autónoma de Nuevo León
Industrial Engineering and Administration, Ingeniería industrial -
Universidad Tecmilenio
Master of Business Administration (MBA), Finance, General -
Universidad Autónoma de Nuevo León
Ingeniería Industrial y Administración, Ingeniería industrial, procesos, producción, manufactura, calidad, mejora continua. -
International Coach Federation
Coach certificado
Community
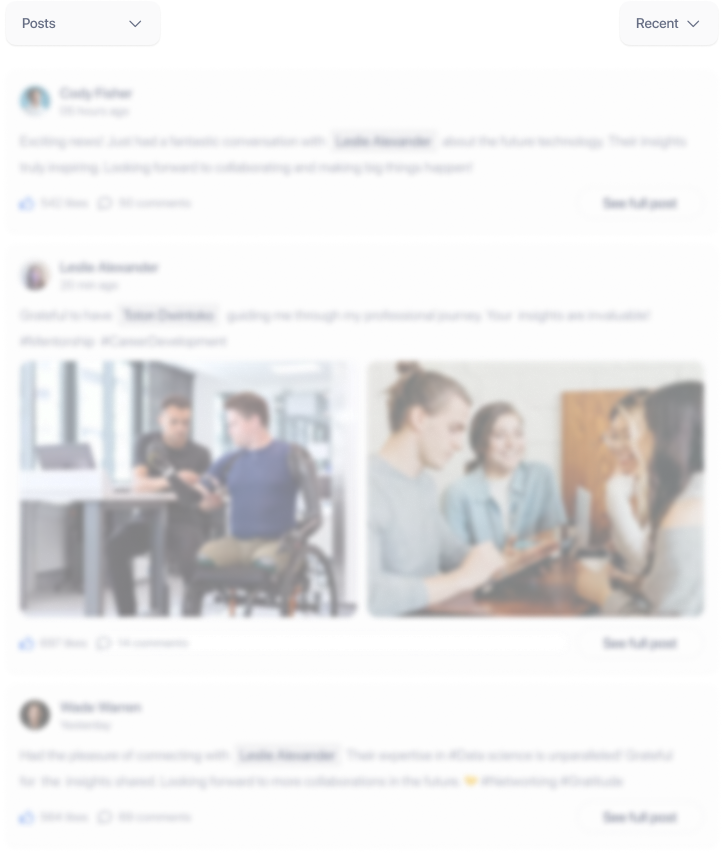