Quentin Morse
Vice President of Operations at Nuvara- Claim this Profile
Click to upgrade to our gold package
for the full feature experience.
Topline Score
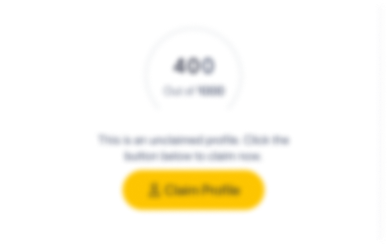
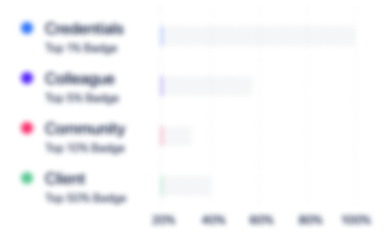
Bio


Experience
-
Nuvara
-
United States
-
Medical Equipment Manufacturing
-
1 - 100 Employee
-
Vice President of Operations
-
Jan 2021 - Present
-
-
-
Talon
-
United States
-
Medical Device
-
1 - 100 Employee
-
Vice President of Manufacturing
-
Mar 2019 - Jan 2021
-
-
-
Roper Technologies, Inc.
-
United States
-
Software Development
-
100 - 200 Employee
-
Director of Manufacturing Operations & Site Leader
-
Nov 2016 - Mar 2019
• Lead annual strategic plan and day-to-day direction toward hitting company goals including Cash Return on Investment (CRI) and Net Promotor Score (NPS) for PAC, a leading manufacturer of advanced analytical instruments for laboratories and online process applications such as gas chromatography, elemental analysis, physical properties, fuels composition, and laboratory automation, while adhering to ASTM, EN, DIN, IP, ISO, ATEX, and DEF STAN standards• Manage all plant manufacturing and supply chain activity, as well as compliance with Environmental, Health, and Safety standards• Responsible for all aspects of profit and loss and balance sheet, including driving lean and continuous improvement• Accomplishment include: o Development and implementation of a facility-wide Kanban material control system o Creation of a 48-hour spare parts and consumables shipping program that improved turn rates, while optimizing inventory levels and minimizing costs o Consistent year-over-year improvements in CRI, NPS score, inventory turns, COGS, and gross margin Show less
-
-
Value Stream Manager/Manufacturing Engineer
-
Jul 2015 - Oct 2016
• Advocated for and trained employees on all aspects of strategic deployment, lean manufacturing, Six Sigma, and Kaizen methodologies, as well as facility health and safety• Increased on-time delivery and minimized inventory costs by implementing line-side material system for key production areas• Owned planning, development, and prototype buildout of all new products, as well as shop floor implementation and integration
-
-
Manufacturing Engineer - PAC
-
Dec 2013 - Jun 2015
• Responsible for daily product output, and the determination/implementation of production efficiencies which incorporated the frequent use of DOE, FMEA, value stream mapping, and other lean/six sigma tools to investigate, improve, or repair manufacturing and testing procedures• Advocated continuous improvement and lean manufacturing principles through daily implementation of Gemba walks, kaizen events, design of experiments, and employee coaching/training• Managed maintenance and service of all equipment in plant producing $60M annually Show less
-
-
-
Toshiba International Corporation
-
United States
-
Appliances, Electrical, and Electronics Manufacturing
-
500 - 600 Employee
-
Andvanced Manufacturing Engineering - Launch Specialist
-
Feb 2013 - Dec 2013
• Managed the launch of all R&D motor plant projects by overseeing personnel, ensuring manufacturing capability, tooling design and fabrication, product quality, and adhering to budget and release dates• Specified, installed, and launched induction brazing system that decreased cycle time by 800% and improved safety by removing the need for open flames and torches• Successfully launched eight different large horse power product lines yielding more than $1.8M revenue increase• Developed and implemented plant-wide Advanced Process Quality Planning System Show less
-
-
Advanced Manufacturing Manager
-
Jan 2012 - Feb 2013
• Responsible for implementing lean, process control, and statistical process control principles, as well as launching new equipment plant wide• Managed lean kaizen and blitz, SMED, and other continuous improvement events across the plant to improve safety, throughput, and overall 5S; All cells showed a 5S score improvement between 30%–80%• Launched all new product developments by creating and leading cross-functional teams of executives, engineers, and operators, and ensuring team member goals were measureable and achievable Show less
-
-
Manufacturing Manager
-
Feb 2011 - Jan 2012
• Managed activities of 6 manufacturing engineers and maintenance department consisting of supervisor and 16 maintenance technicians• Responsible for all plant environmental compliance and waste handling, and investigating/solving safety issues• Developed maintenance key process indicators for downtime, response time, and other critical maintenance metrics, as well as PM and TPM procedures and documentation• Expanded Motor Plant’s manufacturing capabilities from 4000 to 5000 horsepower • Implemented $2.5M automation system to increase throughput by 50% in highly bottlenecked plant department Show less
-
-
-
Baker Hughes
-
United States
-
Oil and Gas
-
700 & Above Employee
-
Quality Control Engineer
-
Mar 2010 - Feb 2011
• Developed and implemented expansive SPC system across several critical processes in utilizing remote measurement acquisition and analysis • Developed robust Gage R&R system used in all applications throughout plant • Utilized Six Sigma statistical methods and other continuous improvement methodologies to monitor/improve processes • Participated in and prepared for various API and ISO audits • Developed and implemented expansive SPC system across several critical processes in utilizing remote measurement acquisition and analysis • Developed robust Gage R&R system used in all applications throughout plant • Utilized Six Sigma statistical methods and other continuous improvement methodologies to monitor/improve processes • Participated in and prepared for various API and ISO audits
-
-
-
Toshiba International Corporation
-
United States
-
Appliances, Electrical, and Electronics Manufacturing
-
500 - 600 Employee
-
Manufacturing Engineer
-
Aug 2006 - Mar 2010
• Led international team of Japanese/American technicians and engineers to develop, implement, and automate notching cell that increased productivity by 400% • Led cost-down team to improve manufacturing methods of outsourced parts resulting in reoccurring savings of over $65,000 annually • Managed retrofitting outdated equipment to convert all high-speed stamping machines from gear-driven to servo-controlled in order to decrease machine setup times by 70% and improve part quality • Developed engineered safety controls to improve high-speed stamping production capacity by 40% • Developed layout and production flow for shaft sawing process resulting in 65% reduction in material handling resources Show less
-
-
Education
-
Texas A&M University
Bachelor of Science (BS), Industrial Engineering
Community
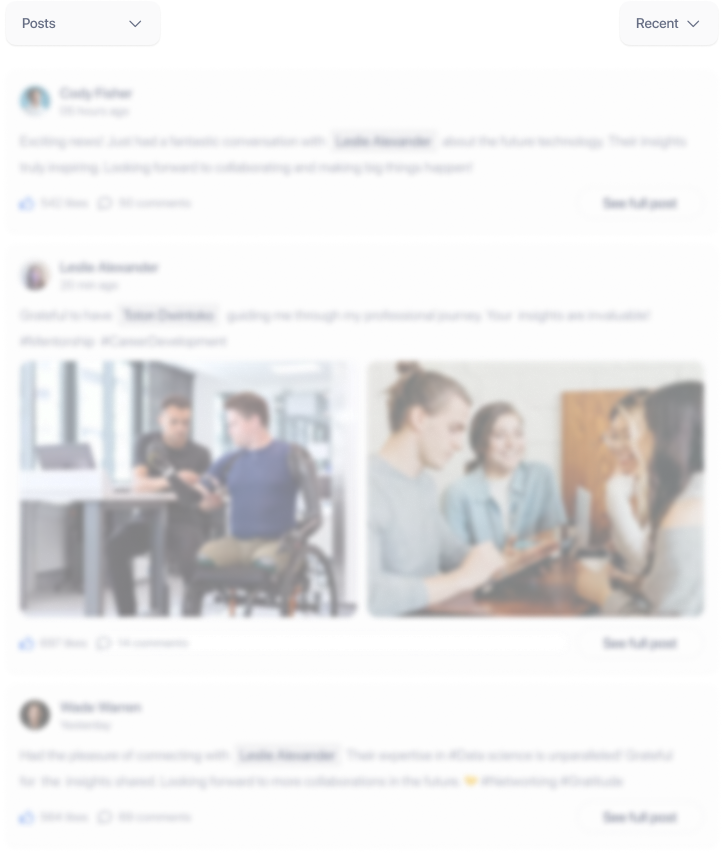