Joy Jenkins
Quality Assurance Manager at SERES ENGINEERING & SERVICES LLC- Claim this Profile
Click to upgrade to our gold package
for the full feature experience.
Topline Score
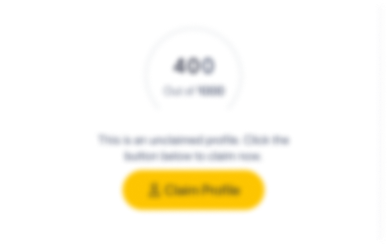
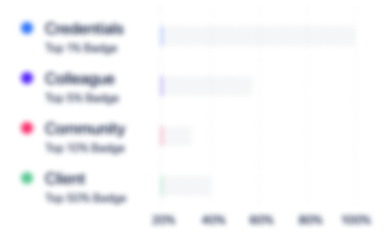
Bio


Experience
-
SERES ENGINEERING & SERVICES LLC
-
United States
-
Environmental Services
-
1 - 100 Employee
-
Quality Assurance Manager
-
Dec 2020 - Present
• Monitor, evaluate and verify performance standards • Develop and monitor appropriate metrics to track quality and process improvement. • Ensures internal processes and metrics are aligned to create a high level of product quality and consistency, in accordance with all internal and external regulations. • Responsible for review and approval of Non-Conformance Reports (NCR), Corrective and Preventive Action (CAPA) plans, Project Records for changes/updates to Standard Operating Procedures (SOP) within the company • Responsible for oversight and general management of Quality Assurance Systems and associated personnel, specifically the Quality Investigations team and designated Quality Specialists. • Perform root cause analysis to prevent recurrence. • Responsible for ensuring adequate Corrective and Preventive Actions result from nonconformance's or deviations, when necessary. • Maintain and update Quality documentation, processes, and procedures. • Responsible for review/approval of quarterly trend reports pertaining to any quality system. • Ensure compliance with SOPs and that SOP revisions are implemented correctly • Collaborate with and support other departments including Base Operations & Maintenance, Real Property Management and Environmental Program to ensure that quality standards and GMP compliance are met and maintained.
-
-
-
ImmunoTek Bio Centers, LLC
-
United States
-
Biotechnology Research
-
200 - 300 Employee
-
Quality Assurance Manager
-
Feb 2018 - Oct 2020
• Ensure all product shipments comply with all federal, state customer and company requirements (FDA, CLIA, COLA). • Ensure sample shipments are appropriately released, accurately labeled and shipped to testing laboratory • Ensure donor center records are complete and accurate • Ensure supplies and materials meet requirements • Ensure compliance with SOPs and that SOP revisions are implemented correctly • Ensure compliance cGMP • Oversee and manage the center’s Deviation Management System to ensure adequate investigations are completed, accurate root cause(s) identified, and CAPA process is identified and managed • Develop Corrective Actions and Preventive Actions for inspection findings and ensure CAPAs are implemented and effective • Track and trend the center’s quality and operational metrics with respect to applicable SOPs. • Work effectively and partner with the Field Quality, Operations support, Center Director and Corporate staff to ensure daily operations are in full compliance • Assist the Manager of Quality Assurance with compliance of all state and federal regulations, FDA-approved Standard Operating Procedure Manual, Clinical Laboratory Improvement Amendments (CLIA), Current Good Manufacturing Practice (cGMP), Occupational Safety and Health Administration (OSHA), and internal company procedures • Ensure equipment is qualified, maintained and calibrated properly • Verify employee training is complete and documented properly • Perform periodic self-assessments of the center’s quality and compliance • Responsible for all quality personnel functions including hiring, assignment and direction of work, development and training, disciplinary actions and termination, and the maintenance of all quality personnel records • Supervise Quality Assurance Unit and donor center quality assurance activities • Train other designated staff in performing the functions of the QAU position
-
-
-
FLSmidth
-
Denmark
-
Industrial Machinery Manufacturing
-
700 & Above Employee
-
QA/QC Lab Technician
-
Apr 2013 - Feb 2018
• Check quality assurance of fabrics in accordance to customers specifications • Approves incoming materials by confirming specifications; conducting visual and measurement tests; rejecting and returning unacceptable materials • Approves in-process production by confirming specifications; conducting visual and measurement tests; communicating required adjustments to production Leads and Supervisor’s. • Approves finished products by confirming specifications; conducting visual and measurement tests; returning products for re-work; confirming re-work. • Inspects components, subassemblies and assemblies • Maintains lab equipment and supplies • Performs sample characterization and testing safely following basic procedures • Collects and prepares samples • Performs basic equipment and instrumentation maintenance • Check the quality of fabric filter bags • Test bags for permeability, mullen burst, tensile strength, flex strength, and microscopic analysis according to ASTM standards • Documents inspection results by completing reports and logs; summarizing re-work and waste; inputting data into quality database • Write and provide lab reports for maintenance and preventative measures • Promotes a culture of personal and team safety, including others who may be affected by the company’s operational
-
-
-
Augusta State University
-
Higher Education
-
200 - 300 Employee
-
Undergraduate Research Student
-
May 2009 - Dec 2012
RESEARCH Synthesis of 2-Aminofluorene Derivatives as an Organic Chemistry Laboratory Project Adviser Dr. Chad Stephens, Department of Chemistry & Project• Prepared solutions for daily lab experiments• Use of instrumentation: FTIR, NMR, AAS, GC, GC/MS, UV-Vis, pH, TLC• developed a multistep synthesis project for future organic chemistry students at Augusta State University
-
-
Laboratory Assistant
-
Aug 2009 - Dec 2009
• Assisted lab teacher • Supervised students in professor’s absence (20-24 students)• Prepared solutions for daily lab experiments• Use of instrumentation: FTIR, NMR, AAS, GC, GC/MS, UV-Vis
-
-
-
Body Central
-
United States
-
Apparel & Fashion
-
200 - 300 Employee
-
Assistant Manager
-
Feb 2004 - Dec 2006
• Assisted customers with purchase • Maintained inventory • Accountable for team performance through teaching, coaching and providing meaningful feedback to build capabilities • Provide front line supervision to an operational, service or administrative team • Support strategies and processes using a customer centric mindset to deliver results, drive store sales, and maximize efficiencies and productivity • Inspected and approved return merchandise • Coordinate and supervise loss prevention and operational programs. • Adapt team priorities to respond to customer and business partner needs • Manage the daily activity of the sales floor, backroom, front end and cash office. • Issued disciplinary action
-
-
Education
-
Augusta State University
Bachelor of Science (B.S.), Chemistry -
Keller Graduate School of Management of DeVry University
Master of Business Administration - MBA, Project Management
Community
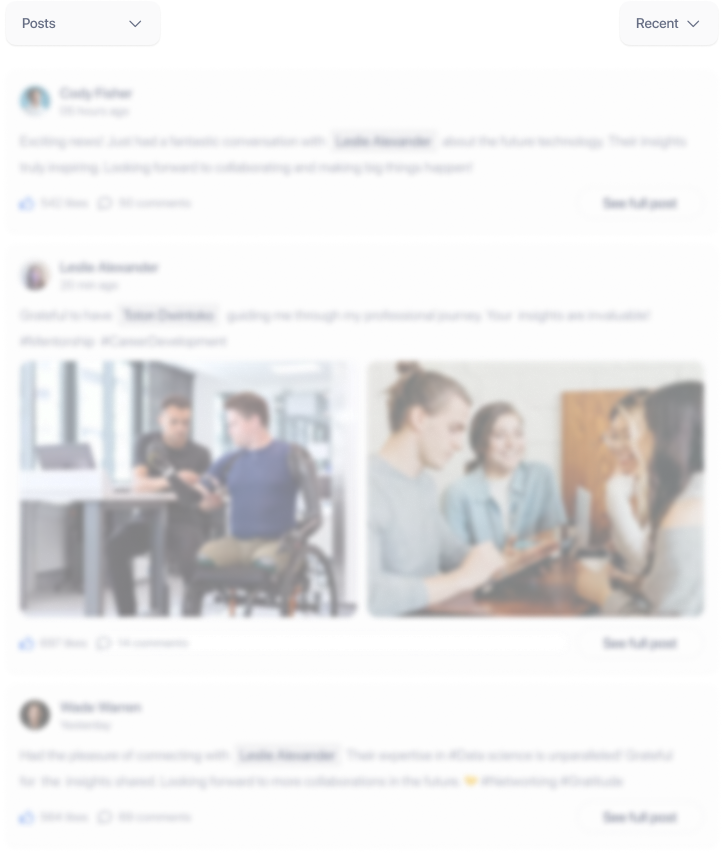