Joshua Nelson
Operations Manager at Verta, Inc- Claim this Profile
Click to upgrade to our gold package
for the full feature experience.
Topline Score
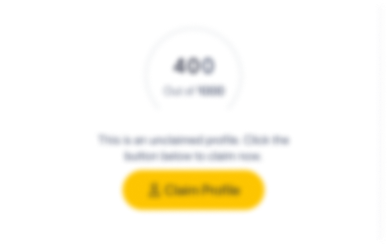
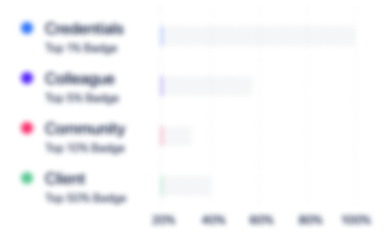
Bio


Experience
-
Verta, Inc
-
United States
-
Construction
-
1 - 100 Employee
-
Operations Manager
-
Aug 2021 - Present
-
-
-
U.S. Navy Reserve
-
United States
-
Armed Forces
-
700 & Above Employee
-
Gunners Mate First Class
-
Mar 2012 - Present
Currently holding a position of leadership in the Naval Reserve Unit. As Leading Petty Officer of Administration I am responsible for maintaining service records for all 30 members of the unit. Direct supervisor of 7 personnel. Coordinate with Air Force Security Forces to augment with Naval Security Forces to complete watch standing qualifications and reinforce security and law enforcement training. Currently holding a position of leadership in the Naval Reserve Unit. As Leading Petty Officer of Administration I am responsible for maintaining service records for all 30 members of the unit. Direct supervisor of 7 personnel. Coordinate with Air Force Security Forces to augment with Naval Security Forces to complete watch standing qualifications and reinforce security and law enforcement training.
-
-
-
rms Surgical
-
United States
-
Medical Equipment Manufacturing
-
1 - 100 Employee
-
Manufacturing Supervisor
-
May 2019 - Aug 2021
Works to ensure the production schedule is accurate, issues are resolved and target dates are met. Maintains work flow by monitoring steps of the process; setting processing variables; observing control points and equipment; monitoring personnel and resources; studying methods; implementing cost reductions; developing reporting procedures and systems; facilitating corrections to malfunctions within process control points; initiating and fostering a spirit of cooperation within and between departments. Maintains quality and safety by establishing and enforcing standards. Drives continuous improvement by implementing and coordinating lean initiatives Kaizan/5S/A3. Leads project management activities. Communicates and delivers employee communication tools for job performance to include annual performance goals, employee recognition, training and development, coaching and counseling. Leads staff through visual metrics and tiered accountability meetings. Monitors staffing levels and works with Human Resources on talent management initiatives. Communicates, adheres and enforces company policies. Maintain office standards by following policies and procedures. Responsible for continual process improvements in quality, delivery, inventory, and safety procedures. Enter production information into the ERP system on a timely basis. Accurately records and reports hours worked. Maintain an organized work area (5S) to include workstations, equipment, walkways, and locker rooms. Participate in the Operational Excellence Program. Understand and complies with the Cretex professional competencies, company policies, and employee manual. Support and complies with the company's Quality System, ISO, and medical device requirements.
-
-
-
Protolabs
-
United States
-
Industrial Machinery Manufacturing
-
700 & Above Employee
-
CNC Team Lead
-
Nov 2017 - Apr 2019
Lead a team of 37 people operating 250+ HAAS CNC Machines. Create a culture of Safety and accountability on the Team as well as individual work assignments. Enforce safety procedures and guidelines, and housekeeping practices. Organize, plan and prioritize daily workload, training and activities in the functional areas. Communicate with supervisors and other leads to coordinate operations and activities within or between shifts and other functional areas. Communicate updates in daily, weekly and other meetings. Establish production sequences and assignments to meet production goals. Identify, recommend and implement measures to improve production methods, equipment performance, product quality and efficiency. Provide guidance and expert advice on technical, systems, or process- related topics. Encourage and build mutual trust, respect, and cooperation among team members. Identify training needs, and conducts training in equipment operations or work and safety procedures. Observe technical performance of the area staff and provide on the spot guidance. Motivate team members to meet deadlines and productivity goals. Provide input to the supervisor for employee performance reviews. Participated in an A3 event to better expedite and process “Same Days” more accurately and on time in an effort to save Protolabs $500,000/yr in missed goals.
-
-
-
-
Mechanical Adjuster
-
Nov 2015 - Oct 2017
Maintain and perform maintenance on manufacturing equipment. Responsible for the safe handling of explosives and quality control. Consistently met and exceeded production goals set by management. Maintain and perform maintenance on manufacturing equipment. Responsible for the safe handling of explosives and quality control. Consistently met and exceeded production goals set by management.
-
-
-
The Home Depot
-
United States
-
Retail
-
700 & Above Employee
-
Department Head
-
Mar 2010 - Oct 2015
Responsible for training and professional growth of personnel, meet sales expectations and management of seven personnel. Forklift operator and designated forklift trainer. Responsible for training and professional growth of personnel, meet sales expectations and management of seven personnel. Forklift operator and designated forklift trainer.
-
-
-
US Navy
-
United States
-
Armed Forces
-
700 & Above Employee
-
Gunners Mate Second Class
-
Sep 2014 - Sep 2015
Conducted the monthly inspections of 54 Ammo, Arms and Explosive storage spaces. Point of contact for the 15-25 tenant commands that operated these AA&E Storage spaces ensuring they are adhering to the Navy’s regulations for safe AA&E Storage as well as Navy Physical Security Requirements on Camp Lemonnier Djibouti, Africa. Firing Range Safety Officer responsible for the planning and safety of all personnel qualifying with small arms training. Department supervisor managing five personnel and 600 weapons. Maintain a maintenance schedule for all weapons and reports of completion.
-
-
-
US Navy
-
United States
-
Armed Forces
-
700 & Above Employee
-
Aviation Support Equipment Technician 3rd Class
-
Jun 2006 - Jun 2010
Performed maintenance on a variety of support equipment, such as, diesel engines, hydraulics, mobile power generators and turbines. Received the Army Commendation Medal for my duties as a guard force member maintaining records and safe keeping of 430 detainees. Being known as the resident expert with the Detainee Management System served as a direct adviser to the chief of the guard. Performed maintenance on a variety of support equipment, such as, diesel engines, hydraulics, mobile power generators and turbines. Received the Army Commendation Medal for my duties as a guard force member maintaining records and safe keeping of 430 detainees. Being known as the resident expert with the Detainee Management System served as a direct adviser to the chief of the guard.
-
-
Education
-
Brainerd Senior High School
Graduated, High School/Secondary Diplomas and Certificates
Community
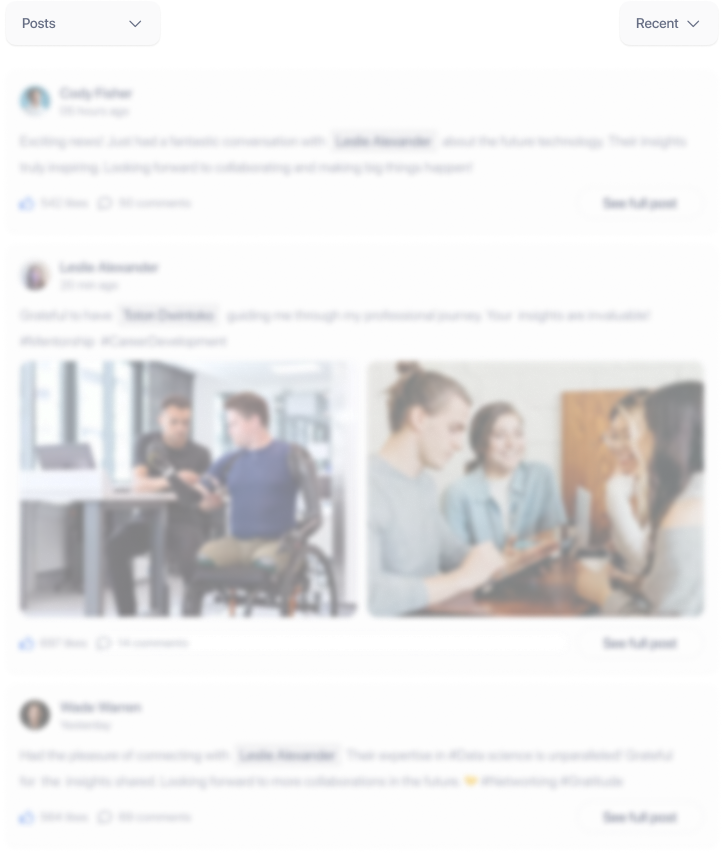