Joshua Hardin
Territory Manager at Association Reserves- Claim this Profile
Click to upgrade to our gold package
for the full feature experience.
Topline Score
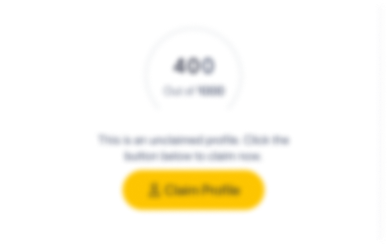
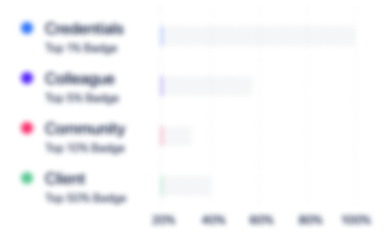
Bio


Experience
-
Association Reserves
-
United States
-
Financial Services
-
1 - 100 Employee
-
Territory Manager
-
Jan 2022 - Present
Miami-Fort Lauderdale Area
-
-
Project Manager
-
Mar 2019 - Dec 2021
Miami/Fort Lauderdale Area
-
-
-
Sonoco
-
United States
-
Packaging and Containers Manufacturing
-
700 & Above Employee
-
Plant Quality Manager
-
Dec 2017 - Jun 2018
Hayward, CA I served as the Plant Quality Manager at a manufacturing facility specializing in temperature assured packaging. Responsibilities included working with customers, investigating customer complaints, developing internal specifications, and auditing processes.
-
-
Shift Supervisor, Safety Coordinator
-
Jan 2017 - Dec 2017
Dallas/Fort Worth Area At the Irving, Texas facility, I helped oversee the consolidation of two divisions under one roof. Responsible for managing the Protective Solutions portion of the plant, I made immediate corrective actions to improve margin, EBIT, customer response times, and DOH - metrics that the plant had historically struggled with. I led efforts to outsource several of our labor-intensive items, which allowed the plant to make much-needed headcount reductions without sacrificing productivity.
-
-
Management Trainee
-
Jun 2016 - Jan 2017
Greater Nashville Area, TN As a management trainee, I served as the shipping supervisor for our Protective Solutions Nashville plant. I oversaw the scheduling and delivery of freight as well as the management of hourly employees. While in charge of the shipping department, I led cost reduction efforts resulting in $70,000 a year through improved scheduling and management of labor. Challenged with historically poor inventory accuracy, I also implemented a system which improved accuracy by 80% while cutting in half the… Show more As a management trainee, I served as the shipping supervisor for our Protective Solutions Nashville plant. I oversaw the scheduling and delivery of freight as well as the management of hourly employees. While in charge of the shipping department, I led cost reduction efforts resulting in $70,000 a year through improved scheduling and management of labor. Challenged with historically poor inventory accuracy, I also implemented a system which improved accuracy by 80% while cutting in half the time taken to do cycle counts.
-
-
-
DISH Network
-
United States
-
Telecommunications
-
700 & Above Employee
-
Operational Excellence Intern
-
May 2015 - Aug 2015
Greenville, South Carolina Area I was able to serve as an Operational Excellence intern with a focus on Lean Manufacturing principles, all under the guidance of a Master Black Belt. While at Dish, I aided in 5S implementations and led a wide variety of rapid improvement events. In addition to work at our facility, I was able to travel to different manufacturing facilities to preform gap analysis participate in several Kaizen Events. My main project for the summer was to implement single operator flow in our Recovery area. I… Show more I was able to serve as an Operational Excellence intern with a focus on Lean Manufacturing principles, all under the guidance of a Master Black Belt. While at Dish, I aided in 5S implementations and led a wide variety of rapid improvement events. In addition to work at our facility, I was able to travel to different manufacturing facilities to preform gap analysis participate in several Kaizen Events. My main project for the summer was to implement single operator flow in our Recovery area. I was able to propose a solution that saves the company $150,000 annually while simultaneously improving the operators' quality of life and enjoyment of the job. Show less
-
-
-
Walmart
-
United States
-
Retail
-
700 & Above Employee
-
Real Estate/Store Planning
-
Jun 2013 - Aug 2013
I worked on a remodel team that renovated store #1146 over the course of two months. Daily tasks comprised of helping to oversee the incoming shipments and managing inventory of all equipment in storage. I served as the head forklift operator and was routinely given supervisional duties among other employees.
-
-
-
-
Waiter/Middle Person
-
May 2012 - Aug 2012
I served as a waiter in the restaurant, assisting customers and taking care of tables; however, I was also required to do some small food preparation and perform janitorial duties after hours.
-
-
-
True Value Company
-
United States
-
Wholesale
-
700 & Above Employee
-
Sales Associate
-
Feb 2011 - May 2012
I served as a sales associate for the Lawn and Garden department, assisting customers with both questions and products while performing irrigation management and daily tasks.
-
-
Education
-
Clemson University
Bachelor of Science (B.S.), Industrial Engineering -
St. John's Christian Academy
High School Diploma, 5.2 GPA
Community
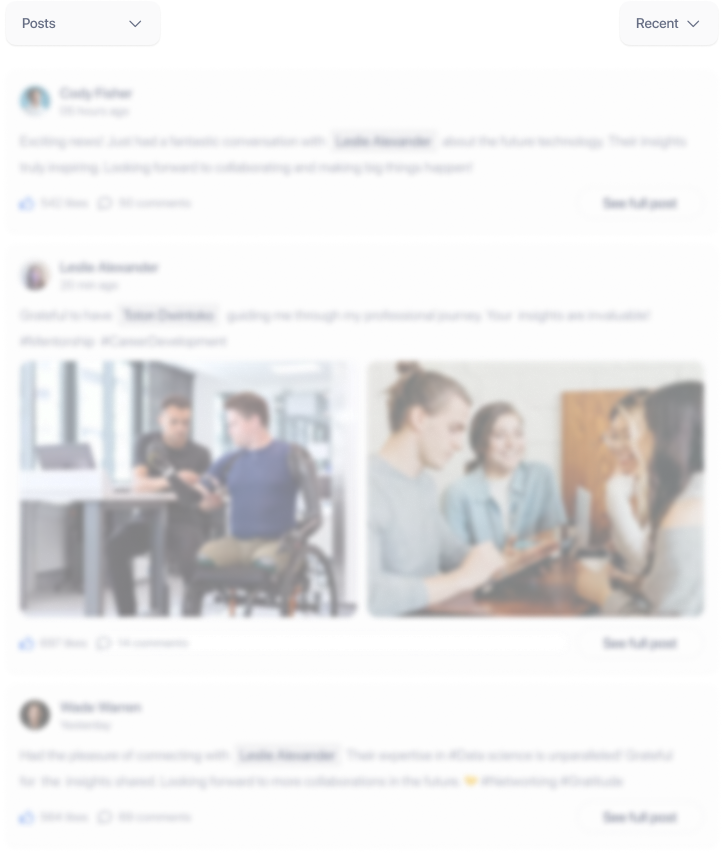