Josh Stottmann
Operations Manager, Paulsboro Refinery at PBF Energy- Claim this Profile
Click to upgrade to our gold package
for the full feature experience.
Topline Score
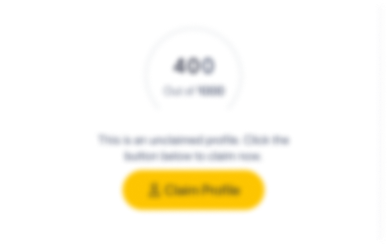
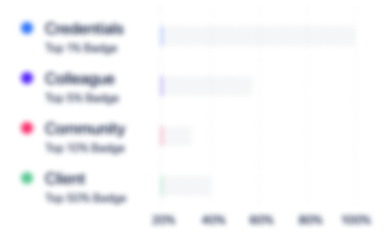
Bio


Experience
-
PBF Energy
-
United States
-
Oil and Gas
-
700 & Above Employee
-
Operations Manager, Paulsboro Refinery
-
Jan 2021 - Present
Responsible for daily operation, safety & environmental compliance, and strategic planning of the reconfigured Paulsboro Refinery. Process units include Crude Distillation, Furfural Extraction, Propane De-asphalting, Asphalt Blending, Benzene Recovery, Mobil Lube Dewaxing, Hydrogen Reformer, Jet Hydrotreater, Naphtha Hydrotreater, Sulfur Recovery, Amine Treating, Flare Gas Recovery, Oil Movements, Wastewater Treatment, Utility Plant.Safely manage a 100 person Operations staff
-
-
Operations Manager, Crude/Coker Complex
-
Jul 2019 - Dec 2020
Responsible for daily operation, safety & environmental compliance, and strategic planning of the Crude/Coker Complex at the Paulsboro Refinery. Process units include Crude Distillation, Delayed Coker, Amine Treating, Flare Gas Recovery.Safely manage a 50 person Operations staff
-
-
Manager West Coast Crude & Feedstocks
-
Apr 2017 - Jul 2019
Trade waterborne crude and intermediates including VGO, LCO, CSO, & Asphalt for PBF Torrance Refinery.Manager of Commercial and Refinery Optimization for the West Coast. Collaborate with refinery Planning & Economics group to streamline commercial decisions and refinery operations to maximize margins and efficiency.
-
-
Planning & Economics Engineer II
-
Jan 2016 - Mar 2017
Utilized Linear Program to run weekly plant economics and made operational decisions based on economic margins. Developed 90 day Refinery Operating Plans. Evaluated feedstock economics and feasibility for purchase. Developed 2017 Paulsboro Refinery Business Plan. Used Linear Program to project monthly rates and gross margin.
-
-
Process Engineer II - Lubes Complex
-
Jan 2012 - Dec 2015
Responsible for daily performance monitoring, troubleshooting, and providing technical support to operations for the following process units: Furfural Extraction, Propane De-asphalting, Asphalt Blending, Benzene Recovery, Mobil Lube Dewaxing, Hydrogen Reformer, Jet HydrotreaterReformulated Jet Hydrotreater catalyst, eliminating a product mercaptan level constraint, which increased unit throughput and annual margin by $4MM.Developed a continuous system of tracking lube basestock quality characteristics to implement unit process changes to minimize product giveaway and off-spec product quality incidents.
-
-
Process Engineer I - Crude & Coker Complex
-
Feb 2010 - Dec 2011
Responsible for daily performance monitoring, troubleshooting, and providing technical support to operations for the following process units: Crude Distillation, Delayed Coker, Amine Treating, Flare Gas Recovery.Introduced chemical program to improve coke fines recovery, reducing coke fines flow to wastewater treatment plant by 75% and increasing recovered coke sales by $100M/year.
-
-
-
Valero
-
United States
-
Oil and Gas
-
700 & Above Employee
-
Process Engineer I - Gasifier & Utilities Complex
-
Jun 2008 - Jan 2010
Responsible for daily performance monitoring, troubleshooting, and providing technical support to operations for the following process units: Petroleum Coke Gasifier, Air Separation Unit , Amine Treating, Combustion Turbines, Heat Recovery Steam Generators, Power Boilers, Steam Turbo-Generators, Water Treatment Plant.Implemented changes in three Power Plant Boilers to increase total steam output with minimal fuel gas usage, while decreasing environmental emissions. Key improvements include renovated air distribution, external and internal cleaning of boiler tubes, adjustments in firing pattern, and procedural changes.
-
-
-
Valero
-
United States
-
Oil and Gas
-
700 & Above Employee
-
Process Engineering Intern
-
Jun 2007 - Feb 2008
Provided guidance for improved yield and increased catalyst life on the Catalytic Polymerization Unit. Implemented changes in catalyst loading, quench distribution, and start-up/shutdown procedures. Changes resulted in increased catalyst conversion and catalyst life.Proposed improvements to prevent the recurrence of heat exchanger corrosion that led to an external fire. Changes included metallurgy upgrade, water injection rate, filtering methods, and procedural changes. Provided guidance for improved yield and increased catalyst life on the Catalytic Polymerization Unit. Implemented changes in catalyst loading, quench distribution, and start-up/shutdown procedures. Changes resulted in increased catalyst conversion and catalyst life.Proposed improvements to prevent the recurrence of heat exchanger corrosion that led to an external fire. Changes included metallurgy upgrade, water injection rate, filtering methods, and procedural changes.
-
-
-
University of Delaware
-
United States
-
Higher Education
-
700 & Above Employee
-
HHMI Undergraduate Research Scholar
-
Jun 2006 - Feb 2007
Utilized a two-level factorial design of equation approach to systematically evaluate factors which are crucial to the high-level recovery of fluorescently-labeled A2A receptor. Developed an optimal process for lysing yeast cells for the enhanced recovery of membrane proteins. Utilized a two-level factorial design of equation approach to systematically evaluate factors which are crucial to the high-level recovery of fluorescently-labeled A2A receptor. Developed an optimal process for lysing yeast cells for the enhanced recovery of membrane proteins.
-
-
Education
-
University of Delaware
Bachelor of Science - BS, Chemical Engineering
Community
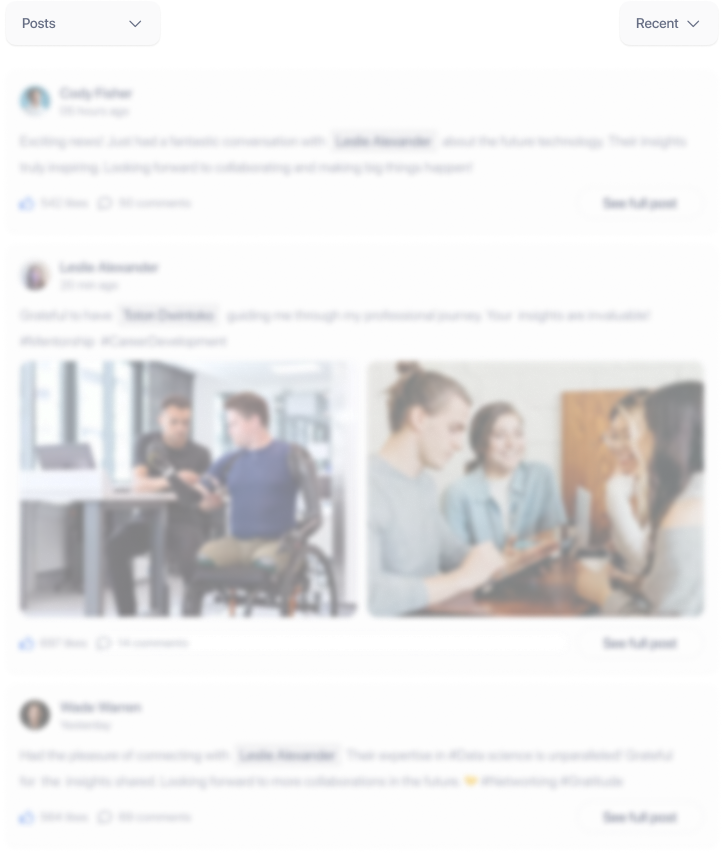