Joe Borrelli
Shift Manager at Lotito Foods- Claim this Profile
Click to upgrade to our gold package
for the full feature experience.
Topline Score
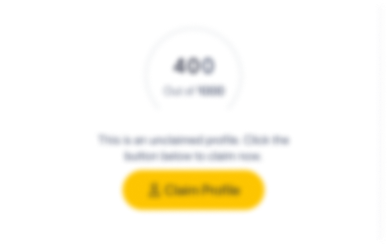
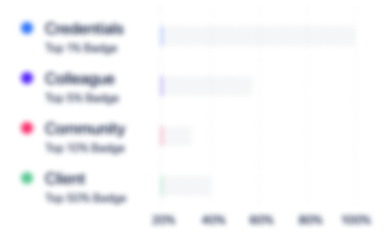
Bio


Experience
-
Lotito Foods
-
United States
-
Food Production
-
1 - 100 Employee
-
Shift Manager
-
Apr 2023 - Present
-
-
-
Accupac
-
United States
-
Manufacturing
-
100 - 200 Employee
-
Packaging Manager
-
May 2022 - Jan 2023
A third-party co-manufacturing plant making and packaging cosmetics, OTC medication, mouthwashes for companies such as L’Oréal, Johnson and Johnson, Church and Dwight, and MHC. As the first shift Packaging Manager-responsible for coordinating with the Supply Chain, Planning, Quality, Project Management and Manufacturing and Maintenance departments for scheduling daily production from between five to fifteen lines depending on customer and product. • Directly responsible for scheduling and staffing production lines based on the production schedule. • Coordinated daily personnel staffing with both Accupac employees and up to four temporary staffing agencies. • Responsible for Safety, Quality, Efficiency, and Cost-KPI’s. • Administered training, payroll and discipline as needed. • Member of Safety Committee. Conducted monthly audits. • Worked with Quality department on sanitation, packaging investigations, customer complaints, PPE and CAPA’s. • Member of CAPA team representing all Packaging shifts. • Created tracking sheet to track line efficiencies. Tracked line speed, headcount, actual versus target weights, and actual versus target production every two hours. Reviewed results with team leaders and supervisors daily. • Reduced staffing headcount by standardizing number of people per line and product across all three shifts. • Completed the annual inventory count in December 2022 Show less
-
-
-
KDCAG
-
Fairless Hills, Pennsylvania, United States
-
Production Manager
-
Jun 2021 - Feb 2022
A startup company that is converting supermarket waste food into chicken feed. This brand-new plant was under construction before I was hired and continues through February 2022. Partnered with HR to interview and hire our work force. We advanced from one shift in August to both a ten-hour day and night shift in October. We continued to interview and hire and train and went to a permanent four-shift 24/7 coverage at the end of January/beginning of February 2022. We continued to troubleshoot and work to get the process to standard work from receiving through the cooking process to shipping. • Created the safety committee and culture to ensure everyone is working safely and following all safety precautions. • Completed basic First Aid/CPR/AED and member of the first responder team. • Completed the Raymond Forklift “train the trainer” in order to certify all personnel on power industrial lifts. • Worked with the quality team ensuring everyone is following GMP and SQF processes. • Coach, mentor and teach all employees and trained, developed, and promoted operators into leads and supervisors. • Partnered with maintenance to develop processes and procedures. • Performed payroll functions and administered discipline as needed. Show less
-
-
-
Blue Apron
-
United States
-
Food and Beverage Services
-
700 & Above Employee
-
Operations Shift Manager
-
Aug 2020 - Jun 2021
A meal order preparation company based on creating and individualizing weekly meal plans for customers. Supervised eight production supervisors and five production leads and between 125-200 associates in the production of customer ordered boxes. Worked twelve hour shifts in a cold room environment. Scheduled staffing and lines based on weekly orders. • Joined the safety committee ensuring everyone worked in a safe manner and followed all safety precautions. • Worked with the quality team ensuring everyone followed GMP and SQF processes and procedures. • Coach and mentored, supervisors and line leads ensuring the associates are following all safety, quality, productivity, and cost KPI's. • Reported out safety, quality, boxes per hour and cost-hourly for the team and every morning for upper management. walk through meeting and at the afternoon manager meeting reporting on issues and corrective actions. • Responsible for safety, quality, and production reports. Attended Bi-weekly management meetings. • Administer payroll and discipline. Coach and mentor supervisors, leads and associates. • Develop and implement continuous improvement projects with team using visual factory management. • Wrote job descriptions and wrist scanning QR tag procedures. • With HR-developed associates into leads, leads into supervisors and supervisors into managers. • Completed leadership development November 2020. Show less
-
-
-
Mauser Packaging Solutions
-
United States
-
Packaging and Containers Manufacturing
-
700 & Above Employee
-
Production Manager
-
Jul 2017 - Apr 2020
Supervised three supervisors and sixty-five union personnel. Responsible for payroll, administration, training, staffing, overtime, and discipline. Scheduled Production using IPC. Member of Safety and Quality teams and introducing Shoplogix to machine operators to track and record downtime. Manufacture between 5,000-8,000 fifty-five-gallon steel drums daily. • Managed two production lines, Press and Parts lines and Cutting line, Silk-screening, Receiving and Shipping. • First Aid/CPR/AED qualified and member of safety committee. • Successfully managed out an accident-prone employee who had collected $250,000 in workmen’s compensation. • Assisted Quality Manager with customer complaints and investigations • Increased plant efficiencies utilizing continuous improvement and employee participation. • Created and trained a second shift to meet increased demand. • Coordinated production with several new maintenance projects to replace older equipment. • Completed annual inventories in 2017, 2018 and 2019. • Inputted information into monthly Profit and Loss statement. Show less
-
-
-
Nestlé
-
Switzerland
-
Food and Beverage Services
-
700 & Above Employee
-
Production Supervisor
-
Jun 2015 - Jul 2017
Front line leader in Jar department. Jar department was built and staffed only months before joining Nestle. Supervised and rotated on all three shifts and weekends. Line ran 24/7. Supervised twenty-seven union personnel for payroll, administration, training, staffing, and discipline. Opened and closed Production orders in SAP. Transferred to tea department early 2017. • Member of Safety Committee. • Partnered with Quality to respond to any quality issues or customer complaints. • Received many recognition awards from co-workers through Real Thanks program. • Completed Disc Training (team building 05/16). Member of Operational Review sub-team. • Completed FLL-1 training 06/16 in Glendale, California. • Completed and able to supervise permit required Confined Space and Mode 4 lockout/tagout. • Successfully completed summer shut-down/deep cleaning and training for 2015 and 2016. Show less
-
-
-
Sunny Delight Beverages Co.
-
Food and Beverage Services
-
200 - 300 Employee
-
Aseptic Department Manager
-
Mar 2013 - May 2015
Managed one Business Leader, three Team Leaders and twenty-four technicians. Expanded from one shift to two shifts to three shifts. Co-packed for three outside businesses. • Member of Safety committee. • Completed EMRT first responder training. • Collaborated with Quality department investigating quality issues and customer complaints. • New customer collaborations with Mojo and Very Fine. • Completed Very Fine validation. Bottle and CIP/Sterilization passed. • Improved OEE from @18% to 35%. • Went from a negative $3.6 million in 2013 to a positive $632,000 in 2014 in revenue. • Completed one week of Lean Training 4/16/15. • Completed one week of Autonomous Maintenance training (AM). • Participated in 3 Earth Day’s by cleaning up the property and surrounding area. • Participated in 3 Boy Scout popcorn and 3 Girl Scout cookie drives-storing and dispensing from our warehouse. Skills: Kaizen, Autonomous Maintenance, PM's, CIP's, Team Work. Show less
-
-
-
Ocean Spray Cranberries
-
United States
-
Food and Beverage Services
-
700 & Above Employee
-
Tetra Department Supervisor
-
Dec 2010 - Feb 2013
Supervised four crews of seven personnel in Tetra department in a 24/7 operation. Includes Blending, Production and Maintenance personnel. Responsible for safety, quality, and line efficiencies. Duties include production reporting, payroll, evaluations, discipline, and training. I replaced four supervisors and used four production leads-one per shift.• Safety: 2,032,227 hours and 1,276 days without a lost time accident. 867 days in Tetra. • Safety celebration-shut down plant for 36 hours and went to outside venue.• 500,000 hours without a recordable on 2/27/12.• Vice President Safety Committee.• First Responder Certified.• Forklift & Aerial Platform “Train the Trainer” certified, • 2 million Hours Celebration. 11/2010 • Vice chair, ACTS (Behavior based safety training) “Train the Trainer.” • Quality-Passed SQF, GMA and Nestle Audits. • Certified SQF Practioner and HACCP Certified- Passed SQF Audit with 90% and received Level 3 certification.• Successfully completed Rapids commissioning which rolled out Fruitables. (Nestle Juice boxes)• Efficiencies: YTD line 5-88.69%, Line 6-87.79%, Combined PY10-88.24%. Goal was 87.5%. World Class!Skills: Change Management, Safety Management, SQF, Cost Reduction, Team building Show less
-
-
Supply Chain Supervisor
-
May 2008 - Nov 2010
Supervised between 20-25 personnel including two non-exempts and twenty-three hourly employees including Shipping/Receiving drivers and Depalletizer/Palletizer operators. Responsible for safety, quality, and line efficiencies. Duties included but not limited to WMS, SAP, RTP, driver efficiencies, payroll, and Chep pallet counts, evaluations, discipline, quality, safety, and training. • Vice president Safety Committee, First Responder Certified, Forklift & Aerial “Train the Trainer” Certified. Anhydrous Ammonia 8-hour Refresher Course. • STOP (Safety behavioral based) trained. Inputted STOP cards. Ran reports for safety committee review.• Passed several quality audits including GMA, Nestle, FDA, and corporate including BevNet high of 86.5%. • Lead Continuous Improvement Projects with Green Belt Training as a member of the Line 2 Palletizer unplanned downtime reduction team, and as a Project Leader for the Line 3 Palletizer unplanned downtime reduction team. • Took responsibility for forklifts, batteries, and chargers removing obsolete equipment and bringing fleet up to date including Speed Shield implementation. Replaced plant maintenance personnel with Eastern Forklift moved onsite.Skills: Change Management, Safety Management, SQF, Cost Reduction, Team building, Supply Chain Management Show less
-
-
Tetra Operations Shift Supervisor
-
May 2006 - Apr 2008
Supervised ten to fifteen personnel in the Tetra production department. Includes blending, production, maintenance, and warehouse personnel. Responsible for safety, quality, and line efficiencies and cost. Duties included but not limited to production reporting, payroll, employee evaluations, and discipline. • Plant achieved recent milestones of 600,000+ man-hours with no lost time. Barbeque Safety Celebration.• Safety Committee, First Responder Certified, Anhydrous Ammonia 8-hour Refresher Course.• Had several quality audits and received a score 90% with Nestle.• Tetra department was newer. Lines had just been installed and started up approximately one year before I was hired. Increased line efficiencies from 60% to 75% Change Management, Safety Management, SQF, Cost Reduction, Team building Show less
-
-
-
COMFLEACTDET Yokohama, Japan-OIC
-
Yokohama, Kanagawa, Japan
-
US Navy
-
May 1987 - May 1989
Officer in Charge Yokohama Detachment Officer in Charge Yokohama Detachment
-
-
-
COMFLEACT Yokosuka Japan
-
Yokosuka, Japan
-
US Navy
-
Mar 1987 - May 1987
Hospital Liaison Sanitation Officer CDO qualified Hospital Liaison Sanitation Officer CDO qualified
-
-
-
USS Reeves CG-24
-
Yokosuka, Japan
-
US Navy
-
Jan 1985 - Mar 1987
Communications Officer Electrical Officer Site TV Officer Communications Officer Electrical Officer Site TV Officer
-
-
Education
-
University of Illinois at Urbana-Champaign
Bachelor of Arts (BA), History
Community
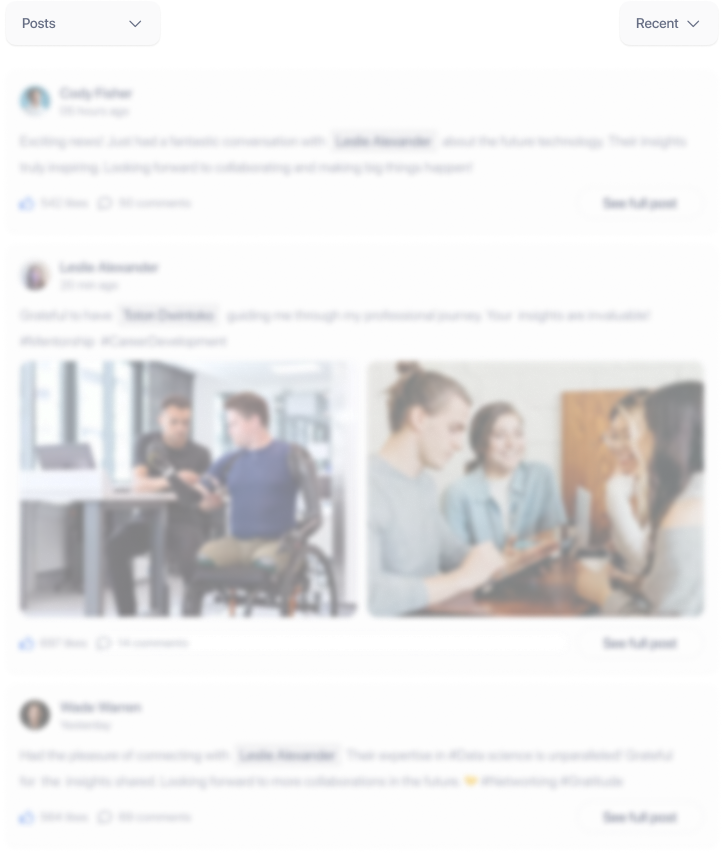