Joseph Koziczkowski
Sr. Director, Clinical Laboratory Operations at Pharmaron- Claim this Profile
Click to upgrade to our gold package
for the full feature experience.
Topline Score
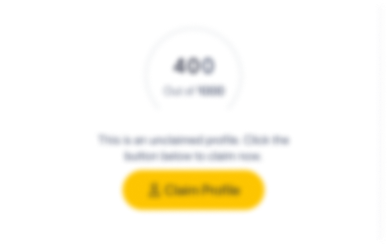
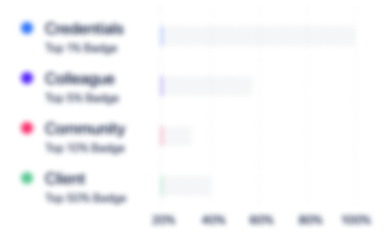
Bio

LinkedIn User
I wouldn’t have my Green Belt were it not for Joe’s encouragement! Though our time together was brief, he helped point me in a brighter direction professionally. Learning Six Sigma principles has been a huge help in how I approach professional and personal projects both big and small.

Julie Roberts
Amazing boss, team player, extremely knowledgeable, works with you and not against you, understandable.

LinkedIn User
I wouldn’t have my Green Belt were it not for Joe’s encouragement! Though our time together was brief, he helped point me in a brighter direction professionally. Learning Six Sigma principles has been a huge help in how I approach professional and personal projects both big and small.

Julie Roberts
Amazing boss, team player, extremely knowledgeable, works with you and not against you, understandable.

LinkedIn User
I wouldn’t have my Green Belt were it not for Joe’s encouragement! Though our time together was brief, he helped point me in a brighter direction professionally. Learning Six Sigma principles has been a huge help in how I approach professional and personal projects both big and small.

Julie Roberts
Amazing boss, team player, extremely knowledgeable, works with you and not against you, understandable.

LinkedIn User
I wouldn’t have my Green Belt were it not for Joe’s encouragement! Though our time together was brief, he helped point me in a brighter direction professionally. Learning Six Sigma principles has been a huge help in how I approach professional and personal projects both big and small.

Julie Roberts
Amazing boss, team player, extremely knowledgeable, works with you and not against you, understandable.

Credentials
-
Lab Management University Advanced
American Society for Clinical Pathology (ASCP)Sep, 2018- Nov, 2024 -
OSHA 30 hour
OSHAcademy Safety and Health TrainingNov, 2011- Nov, 2024 -
Medical Laboratory Scientist
American Medical TechnologistsDec, 2010- Nov, 2024 -
American College of Healthcare Executives
American College of Healthcare ExecutivesNov, 2010- Nov, 2024 -
Lean Six Sigma Green Belt
US NavyFeb, 2009- Nov, 2024
Experience
-
Pharmaron
-
China
-
Pharmaceutical Manufacturing
-
700 & Above Employee
-
Sr. Director, Clinical Laboratory Operations
-
May 2022 - Present
-
-
-
Lifescan Health
-
United States
-
Hospitals and Health Care
-
1 - 100 Employee
-
Regional Director Of Operations
-
Oct 2021 - May 2022
Oversee and responsible for operational strategies, elements, and execution through managers and supervisors of mobile phlebotomy, courier and dispatch, specimen processing, core lab, microbiology, molecular lab, call center and resolution team, Covid team, supply and shipping, HR, and compliance. Ensure adherence with regulatory and licensure standards through implementing KPI's, quality metrics and reporting, standards, enhanced training and competency, and accountability standards. Established goals for operational departments, evaluate leaders and employee performance (through department leadership, accountability, and expectations), and maintains medical laboratory productivity by monitoring workload of functional areas; identifying peak and slack periods; making operational or staffing adjustment, hire, coach, develop, and mentor teams to achieve goals and strategic objectives. Evaluate cost savings initiatives through the analysis and review of the operational, financial, billing, coding functions, as well as the evaluation of instrumentation, supply costs, service agreements, and technology. Implemented internal process improvements to specimen processing and molecular departments that extended specimen stability, improved sample integrity and quality, along with increased client satisfaction while generating over $600,000.00 additional revenue annually and saving over $150,000.00 in supply waste. Network with clients and assist with new client discovery. Negotiated 3rd party contracts and vendor agreements saving over $105,000 in overpayments and contracted services. Continuous improvement champion. Implementing a quality system and building a team enhancing productivity and installing processes for stability and sustainable results. Enhanced leadership IQ and held leaders accountable to standards, productivity goals, and team execution. Show less
-
-
-
Northwest Community Healthcare
-
United States
-
Hospitals and Health Care
-
700 & Above Employee
-
Laboratory Operations Manager II
-
Jan 2018 - Oct 2021
Oversee technical functions of clinical laboratory including operations and general oversight of Blood Bank, Microbiology, Hematology, Chemistry, Immunology, Molecular, Histology, and Cytology. Implemented new system installs in Microbiology, Chemistry, Histology, Hematology, and Coagulation including a new automation line, being one of the first in the Chicago-land area. Lead a team of over 85 focused professionals to provide exceptional healthcare and top quality diagnostic testing for patients and clients processing over 2 million tests per year and growing. Implemented process changes in Anatomic Pathology where noticeable impact to quality and timeliness provided the gateway for improved turnaround and quicker diagnosis through pathology. Enhanced programs and processes to resolve gaps and deficiencies with sample management, processing, resulting, and improved documentation standards for regulatory attributes. Instilled a collaborative working environment with leaders, physicians, and team to allow anyone to have a voice and improve quality and productivity, enhanced engagement scores, and instilled a culture of communication, teamwork, and collaboration. Strategic and budget planning for operating costs of over 50 million and revenue over of 400 million dollars. Mentored and provided guidance to team and subordinate supervisors. Show less
-
-
-
Pharmaron
-
China
-
Pharmaceutical Manufacturing
-
700 & Above Employee
-
Director of Clinical Laboratory Operations
-
Sep 2016 - Dec 2017
Engage and lead a team of Laboratory Professionals in clinical lab and pharmaceutical research. Executed change in method, process, and philosophy of operating while ensuring accurate and timely results which resulted in reductions in costs by over $100K, reduced error rates by 52%, and improved efficiency two fold. Measured improvements in all areas of laboratory functions within five months by driving excellence with process standardization, structured training, and competency programs. Organization strategy development to ensure laboratory services provide exceptional quality and performance, which includes pre-analytic, analytic, post-analytic phases of testing along with technology and training. Established compliant clinical laboratory under CLIA, CAP, COLA, and FDA, along with maintaining continued compliance with OSHA, MD State, and any other regulatory agency as applicable. Developed, streamlined, and implemented strategies that have increased quality related to patient safety and verification procedures used to verify accuracy and precision of test methods and methodologies. Technology platform research for LIMS, contract negotiation, project development, system development and implementation, IQ,OQ, PQ protocol development and execution, and system roll out. Developed and implemented competency testing program and enhanced proficiency testing program improving staff technical knowledge while reducing errors. Improved quality control and quality assessment programs including implementing new systems and services that evaluate and investigate failures, track and trend stats, and analyze gaps. Created and evaluated over 50 processes and procedures, reducing redundancies and ensuring consolidation where necessary which has improved efficiency by 38%, error rates by 21%, turnaround times by 45%, and rework/retesting by 40%. Provide leadership, coaching and technical development to direct reports in order to improve the productivity of all staff levels. Show less
-
-
-
Sysmex America, Inc.
-
United States
-
Medical Equipment Manufacturing
-
700 & Above Employee
-
Reagent Supervisor
-
Aug 2014 - Oct 2016
Supervise team of technicians in a medical device, reagent manufacturing environment, enforcing cGMP, cGDP, and cGLP principles. Manufacture and manipulate chemical compounds used for hematology and urinalysis reagent production. Monitor chemical preparations through laboratory testing and performance resulting. Manage cross functional processes with internal and external entities improving turn around times, scrap counts, and inventory control methods and measures. Developed training and competency programs, identifying gaps in staffing and enhancing team readiness by 45%. Championed 5S program and implemented Lean systems for manufacturing and testing routines. Develop and champion change control processes Develop, modify, and mature standard operation procedures (SOP), work instructions, validation protocols, and technical documents. Developed and implemented comprehensive quality systems and control procedures for testing and manufacturing improving production times, product yields, and material usage. Update and manage KPIs and conduct process improvement studies with statistical and scientific charting and reporting. Manage quality systems, including investigations, deviations, NCMR, and CAPA. Develop and execute protocols for device characterization, installation, and operation, (IQ, OQ, PQ) Executed change control processes, validation protocols, FAT/SAT testing, work stream analysis, and process improvement studies for workforce and supply. Developed operating procedures (SOP and work instruction) for filling machines. Technical expert and trainer for operators in clean room operations. Staff coaching, and professional development. Initiated and implemented staff development program, establishing goals and milestones that have improved moral, quality of work, and retention. On boarding, performance reviews, and disciplinary evaluations. Show less
-
-
-
Immucor, Inc.
-
United States
-
Medical Device
-
700 & Above Employee
-
Red Cells Manager
-
Aug 2013 - Aug 2014
Supervise and manage complex manufacturing department responsible for bulk manufacturing and processing of blood and blood components used in diagnostic applications using cGDP, cGLP,and cGMP principles. Prepare and maintain production and bulk manufacturing schedules with cross functional coordination and supply chain timeline emphasis. Technical and scientific review of processes. Implement change control, and document revisions for process improvement and device history records. Raw material reconciliation, MRP and Lean methods, improving material usage and reducing scrap and expiring lots by 82%. Comprehensive culture change to enforce FDA and OSHA standards and to align with cGMP and cGDP practices. Lead a comprehensive quality system culture change reducing deviations, Non-Conformances, and CAPA's by over 40% in 12 months. Develop, organize and maintain QA/QC programs for equipment, materials, and products, to include trending, process improvement, and regulatory compliance. Implemented departmental improvements leading to a successful FDA audit and removal of Notice of Intent to Revoke (NOIR). Conducted product investigations to determine stability, performance, and precision. Part of team that investigated and identified critical process deficiencies to improve product availability and customer satisfaction, as well as increasing profits. Staff on boarding with comprehensive training and competency program development to improve technician training and readiness from 35% to 95% in eight months. Motivate, coach, and mentor strong technical team in a fast paced clean room manufacturing environment. Show less
-
-
-
The Institute for Transfusion Medicine
-
Hospitals and Health Care
-
100 - 200 Employee
-
Quality Control Laboratory /Blood Product Labeling Manager
-
Oct 2010 - Aug 2013
Ensure all industry standards are met with regulatory bodies such as Food and Drug Administration (FDA), American Association of Blood Banks (AABB), and College of American Pathologists (CAP) through the use of industry published standards by AABB and Code of Federal Regulations (CFR). Insure good manufacturing practices (cGMP) are met and followed. Maintain procedures, equipment, and processes involved with; Quantification of residual white blood cells by using flow cytometry and hematological methods of qualifying leukocyte-reduced apheresis platelets and red blood cells. Bacterial detection using Blood Culture System with the capability of accurately detecting minute numbers of aerobic and anaerobic organisms in platelet products. Contaminant organisms are specifically identified using traditional methods. Platelet, white, and red blood cell counts. Manage the Quality Control program by extrapulating data, derive and report trends, variances, failures, adverse events, and regulatory infractions. Performed and investigated failures related to products and product testing. Prepared FDA reportable transcripts related to recalls, and positive test results. Evaluate staff for compentancy, provide training and development concepts for improved effeciency. Developed and implemented competency program for technicians specific for CLIA, CAP, and FDA regulations and guidelines Prepare and present trending data and training to customers, employees, superiors, and physician groups. Manage Human Leukocyte Antigen (HLA) platelet matching program. Completed patient specific ABO and HLA antigen matched blood products, and collaborated with physicians in platelet transfusion needs. Manage a team and responsible for the final QA and labeling of all blood products. Review and research product recalls/ look-backs. Investigate prohibiting factors, reconcile, and authorize override release for blood products. Wrote and performed site and equipment validations. Show less
-
-
-
US Navy
-
United States
-
Armed Forces
-
700 & Above Employee
-
Laboratory Manager
-
Aug 2008 - Dec 2010
Responsible for the collecting, processing, resulting, and documenting of all new recruits entering the Navy. Supervise nine military techs and three civilians in daily laboratory operations. Responsible for over 1.8 million dollars of equipment, supplies, and reagents. Conduct variance reporting and QA/QC charting. Manage tuberculosis resulting and reporting program to Occupational Health for reporting to state health department. Verify all entered lab results in LIS from previous day, recommend additional testing when required.Conduct personnel evaluations and counseling.Performed duties as generalist, accessioned and processed patient samples for clinical laboratory including Hematology, Chemistry, Special Chemistry, Urinalysis, coagulation, microbiology, and blood banking.Managed analyzer QC and maintenance, observed for trends, and identify questionable results.Performed complex titrations and dilutions.Reviewed and reported manual differentials, retic counts, semen analysis, body fluid counts, and crystal evaluations.Managed Lab Information Systems, developed test plans, and prepared and tested test menu builds.Trained Hospital Corpsman in phlebotomy and basic laboratory principles.Mentored, trained, and supervised new and cross training techs.Managed, reviewed, and completed competency assignments and proficiency/ CAP testing.Reviewed and reported critical results and call backs.Managed and participated POC testing program for hospital bedside glucose and ICU/ER iStat stat analyzers. Show less
-
-
Career Counselor
-
Nov 2008 - Oct 2010
Managed career paths of over 565 staff members, to include specific training paths, special pay, advancement, education, and assignments. Provided counseling and advice on plans, goals, and priorities.Provided mentorship and leadership to junior members and peers, allowing for increased promotion rates, education advances, and personal awards.Created and coordinated training sessions along with providing guidance and supervision to subordinate instructions.Lead command leadership training and advancement training which directly resulted in an 54% increase in promotions and increasingly prepared staff. Show less
-
-
Laboratory Manager, Ancillary Manager, Public Affairs
-
Jul 2005 - Aug 2008
Laboratory Manager responsible for $3.5 million in laboratory functions and equipment, including managing 34 personnel, liaison with medical, IT, supply, and surgical directors to incorporate new procedures, testing, or technology.Supervise and perform advanced laboratory procedures such as autoanalyzers, spectrophotometers, blood gas analyzers, flame photometers (emission / absorption), osmometers, gas chromatographs, electrophoreses apparatus, sequential multiple analyzers and other procedures.Perform and oversee all phases of blood donor processing, blood banking procedures, clinical bacteriology, mycology, serology, immunohematology, hematology, parasitology, general and clinical chemistry, toxicology, and urinalysis in clinical laboratory with daily workload of up to 2000 samples.Prepared forecasts and perform strategic planning and budget for consumables, blood products, health care supplies and equipment, and administrative supplies for a multi-national health and humanitarian mission which allowed for increased testing regiment and reduced and estimated $250,000.00 in spending Develop standard operating procedures (SOP) and the Labeling Conversion Policy for the Department of Defense (DOD) and the Armed Forces Blood Program from a Codabar to ISBT 128 standard, while conforming to FDA, AABB, CAP, and DoD policies.Managed workforce and workflow capabilities with multi cultured and diverse staff, used team building techniques, and skill sets, along with mentorship to increase daily operations of the Ancillary department, while maintaining excellent patient care standards and quality. Managed quality control (QC) and quality assurance (QA) programs, including planning, determining and implementing internal processes and improvements for laboratory and blood bank procedures along with variance tracking, reporting, and corrections. Show less
-
-
Healthcare Professional
-
Jan 1991 - Jul 2008
Provided diverse services as Supervisor, EMT / Paramedic, Health-care Provider, Medical Technician. Supervised hundreds of personnel in the performance of clinical or ward duties and in areas such as sick call, preventive medicine, health care inspections and environmental inspections.Managed LIS network and user accounts for 18 personnel, ensuring LAN connectivity and security.Maintained medical records, conducted preventive medicine, water, food, safety and sanitation inspections.Identified critical flaws and prevented deployment of latest Defense Blood Banking System (DBSS) version 5.0; resulted in saving Armed Services over $500,000.Updated critical processes on SOPs resulting in increased quality performance standards, decrease in over 200 man hours monthly and 72% reduction in clerical errors.Created a data tracking system and enhanced LIS functions satisfying Food & Drug Administration (FDA), College of American Pathologists (CAP), and American Association of Blood Banks (AABB) accreditation inspector's checklists.Developed and instructed hands-on training in Frozen Blood Program for tri-service student laboratory officers enrolled in Specialist in Blood Banking (SBB) Program.Conducted process improvement inspection and Lean analysis for processing HIV samples, implemented plans which resulted in decrease of 3 man hours daily and saved over $2000.00 quarterly in supplies.Proficient in Microsoft Office, to include Word, Excel, PowerPoint, and OutlookEffective written and oral communicator, preparing and presenting various reports, presentations and training sessions to senior leadership, peers, students, and visitors. Show less
-
-
Education
-
Liberty University
Doctor of Philosophy - PhD, Business Administration, Management and Operations -
Keller Graduate School of Management of DeVry University
Master of Business Administration (MBA), Health Services Administration and Project Management -
Columbia Southern University
Graduate Certificate, Occupational Safety and Health -
Trident University International
Master of Science, Health Science - Public Health -
Touro College
Bachelor of Science, Health Sciences Laboratory Science -
Southern Illinois University, Carbondale
Bachelor of Science - BS, Healthcare Administration -
Naval School of Health Science
Diploma, Advanced Medical Laboratory Technology -
Naval Leadership Schools
Community
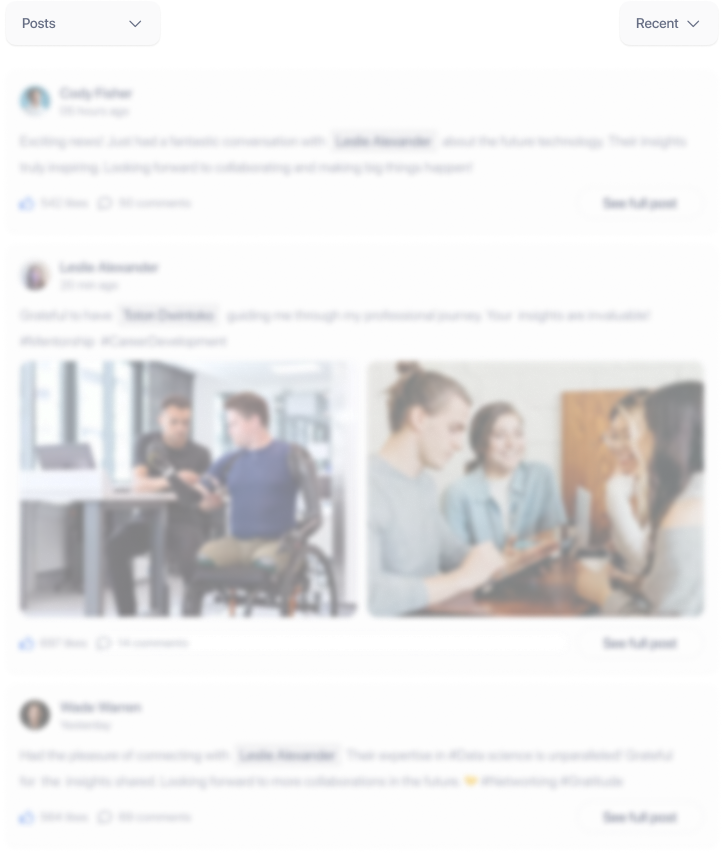