Jose Gonzalez
Engineering at ISGO MANUFACTURING- Claim this Profile
Click to upgrade to our gold package
for the full feature experience.
Topline Score
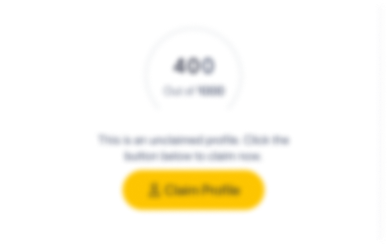
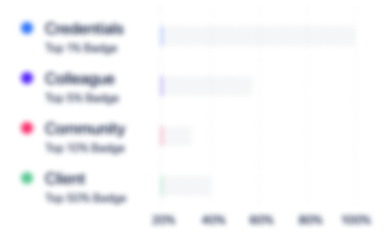
Bio


Experience
-
ISGO MANUFACTURING
-
Mexico
-
Plastics Manufacturing
-
1 - 100 Employee
-
Engineering
-
Dec 2021 - Present
-
-
-
Organización Reynera
-
Mexico
-
Wholesale
-
100 - 200 Employee
-
Engineering Manager
-
Feb 2021 - Jun 2021
Responsible of Design, Tooling (Injection Molds, Extrusion), New Projects Launch, Industrial Engineering, Packaging, Injection molding machines, equipment selection and production support. Leading a team of 9 collaborators. Technical support to supply chain team Projects feasibility analysis. Responsible to evaluate and approve process or materials deviations. Established engineering procedures and proper documentation for New Projects, APQP, Engineering Change Control, Injection Tooling Fabrication. Show less
-
-
-
-
Engineering Department Manager
-
Oct 2013 - Feb 2021
Resources planning to ensure plant and department KPI´s accomplishment. Technical support to sales/commercial and supply chain team. Create and execute work plans to meet customer requirements. Continuous Improvement responsible, operation and cost reduction. Plant capacity and direct labor requirement analysis. Responsible of projects feasibility and risk analysis. Coordinate engineering team, 3 Program Managers, to fulfill quality system procedures and core tools (apqp, ppap, fmea, msa, spc). Responsible to evaluate and approve Manufacturing deviations. Engineering changes control and administration. Show less
-
-
-
Tepso Plastics
-
Plastics Manufacturing
-
1 - 100 Employee
-
Manager Program Management
-
Mar 2012 - Oct 2013
Responsible of project planning, development, and launch. Tooling sourcing and tooling supplier administration, following customer and plant procedures for tool and part approval before tool ship. Project team coordination and documentation following core tools (apqp, ppap, fmea, msa, spc) and quality system procedures to ensure project accomplishment. Technical reviews with customer and OEM´s to define critical characteristics. Process Layout and PFMEA elaboration. Dimensional full layout revision and approval. Show less
-
-
-
-
Plant Operations Manager
-
Mar 2010 - Feb 2012
Responsible of production area (Corrugated, Flexo print and rotary die cutting), Maintenance, Quality and Warehouse. Established negotiations with customers to adjust forecast requirement to improve production planning. Responsible of production area (Corrugated, Flexo print and rotary die cutting), Maintenance, Quality and Warehouse. Established negotiations with customers to adjust forecast requirement to improve production planning.
-
-
-
EVCO Plastics
-
United States
-
Plastics Manufacturing
-
300 - 400 Employee
-
Engineering Department Manager
-
Feb 2007 - Oct 2008
Projects development and planning establishing milestones. Project quote approvals, machine and equipment invest analysis. Responsible of project feasibility and risk analysis. Coordinate engineering team, 5 Engineers, to fulfill quality system procedures to ensure deliverables on time. Projects development and planning establishing milestones. Project quote approvals, machine and equipment invest analysis. Responsible of project feasibility and risk analysis. Coordinate engineering team, 5 Engineers, to fulfill quality system procedures to ensure deliverables on time.
-
-
-
Montoi SA de CV
-
Consumer Goods
-
1 - 100 Employee
-
Senior Product Engineer
-
Feb 1997 - Jan 2007
10 Years career, escalating positions from Costing Engineer, Manufacturing Engineer, Industrial Engineer and Senior Product Develop Engineer. Product development from the 3D concept to production, working with a multidisciplinary team of designers, mechanical and electrical engineers to review design and tooling required. BOM maintenance, secondary operations development (in-mold labeling, ultrasonic welding, vibration welding, hot stamp, tampo print, painting and assembly fixtures). Production lines balance, assembly line and molding area layouts, packaging specifications, fixtures design. Tooling, purchasing and BOM costing. Definition of parts and product standard cost. Show less
-
-
Education
-
Universidad Autónoma de Nuevo León
Ingeniero Mecánico Administrador
Community
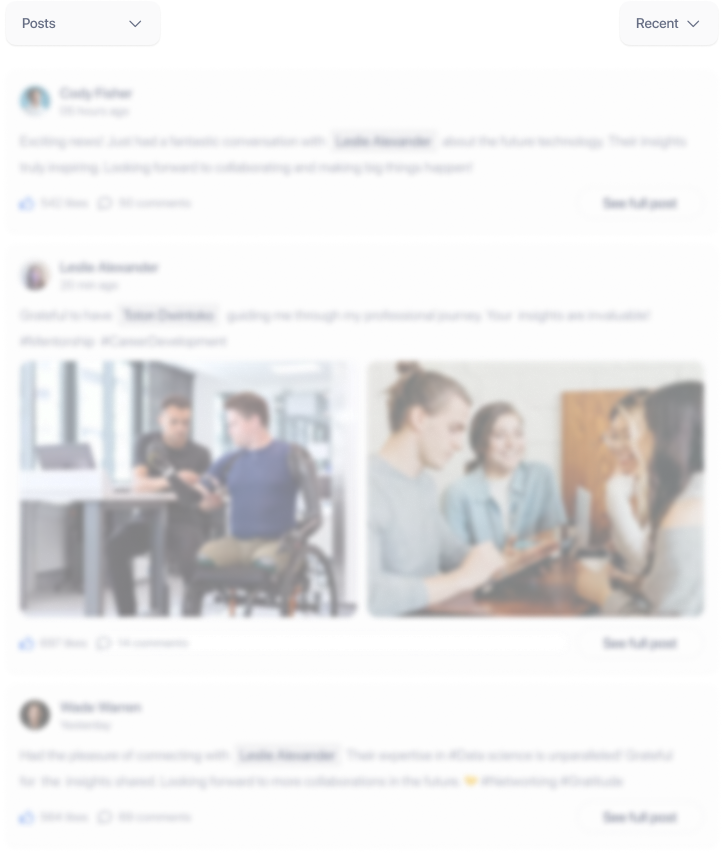