Jose Edwardo Cobio
Manager of Plant Engineering at Burke Corporation- Claim this Profile
Click to upgrade to our gold package
for the full feature experience.
-
English -
Topline Score
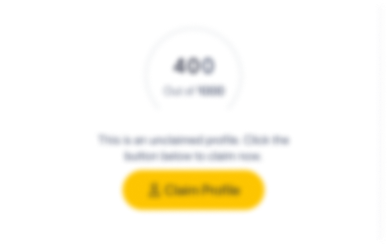
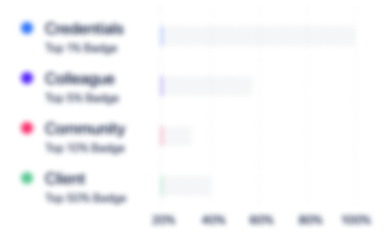
Bio


Credentials
-
Lead ISO Auditor Certification
BSIFeb, 2018- Nov, 2024 -
KepnerTrego - Problem Solving and Decision Making Practicioner
-
Experience
-
Burke Corporation
-
United States
-
Food and Beverage Manufacturing
-
1 - 100 Employee
-
Manager of Plant Engineering
-
Mar 2022 - Present
-
-
-
Coca-Cola Southwest Beverages
-
United States
-
Food and Beverage Services
-
700 & Above Employee
-
Maintenance Manager III & Reliability Engineering Leader
-
Apr 2018 - Mar 2022
▪ Responsible for the facility industrial equipment preventive and corrective maintenance program.▪ Develop and improve preventive maintenance program, with the intent of improving facility performance, increasing program robustness, whilst ensuring Food Safety, Safety, Environmental and Quality requirements are met.▪ Coordinate facility annual preventive maintenance routines including, but not limited to electrical substation PMs, external party equipment rebuilds, grounding and bonding and thermal imaging maintenance.▪ Participate and lead in corporate capital projects including equipment transfers and commissioning.▪ Strive to create a self-sustaining team which increases team morale, promotes engagement, and aids in team succession.▪ Promote the use of data to facilitate departmental report-out and easily identify process/program deficiencies▪ Developed and implemented weekly monitoring and metric review process and scorecard which improved team and plant performance▪ Participate and lead capital expenditure projects in various capacities ranging from capital appropriation business case development to commissioning of facility equipment▪ Mentor direct reports, indirect reports and peers on the skills that facilitate professional growth, including developing their soft skills▪ Develop and manage departmental budget, drive reduction of operational CPC (Cost per Case), whilst focusing on our customers, equipment health, and team needs▪ Drove improvements to weekly Maintenance / Production Coordination meeting agenda to increase transparency and collaboration between all departments within the manufacturing group▪ Implemented tools to improve our planning process and bring openness to our relationship with our internal customers, promote the fact that their needs are our priority▪ Certified Reliability Leader and designated Asset Management Leader, responsible for introducing the corporate asset management strategies Show less
-
-
Management Systems
-
Oct 2016 - Apr 2018
Managed Safety, Food Safety, Environmental, and Quality ISO System for the manufacturing facility.
-
-
-
Johnson Controls
-
Ireland
-
Industrial Machinery Manufacturing
-
700 & Above Employee
-
Launch and Engineering Manager
-
Nov 2015 - Oct 2016
New Product Introduction, Test Development and Product Engineering Mananger
-
-
Plant Engineering Leader
-
Oct 2010 - Nov 2015
• View employee safety as a top priority, address/escalate safety related issues and drive through to completion• Generated organizational procedures and implemented paperless electronic tracking system which enabled global visibility and collaborative product life management• Serve as mediator in conflict resolution between employees and peers, mentor employees on problem solving skills through coaching, constructive feedback, and by leading by example• Facility project manager for corporate and facility led cost saving initiatives• Led corporate cost savings initiative, transfer of manufacturing operation from an external supplier to our Reynosa facility, completed with zero impact to customers• Drove procedure changes to corporate business operation specifications which streamlined engineering change process, and standardized documentation across multiple facilities• Generated and implemented paperless engineering deviation process which enabled traceability of engineering requests executed by the engineering, enabled global visibility• Facility’s Engineering POC for Product Management, Quality, Design Engineering and customer requests• Collaborated with functional teams and team leaders on identifying administrative process deficiencies, product design and quality issues, worked with peers on root cause analysis and corrective actions• Generate weekly facility performance reports for corporate engineering directors on engineering change implementation and cost saving project execution• Utilized expertise to establish BBPs (Best Business Practices) to drive improvements in operations efficiency, administrative functions, and quality practices• Endorsed positive morale by keeping a consistent positive and professional attitude when facing high stress situations Show less
-
-
-
Siemens
-
Germany
-
Automation Machinery Manufacturing
-
700 & Above Employee
-
FSE
-
Jun 2010 - Oct 2010
-
-
-
U.S. Cotton, LLC
-
Manufacturing
-
1 - 100 Employee
-
Supervisor
-
Sep 2007 - Mar 2010
• Managed daily operations between two manufacturing facilities and multiple departments • Conducted daily/weekly meetings with management staff and personnel, presented operations information and communicated changes to policies and procedures • Supported equipment upgrades with feedback from an operational/cost perspective and assisted with equipment installation • Drove process changes to operational specifications which resulted in reduced cycle time and reduced production costs • Initiated evaluation of workgroup health, drove efforts to improve team efficiency and cross functional workgroup relationship • Identified quality issues and worked with peers to identify root cause and corrective actions • Provided Equipment Technicians with assistance on planned maintenance and non-routine error recovery • Audited work performed by Equipment Technicians and ensured all repairs were performed safely, and documented accurately • Actively sought opportunities to support multiple workgroups and improve company efficiency and performance • Generated daily reports on equipment downtime, quality defects and production constraints • Worked closely with peers to identify and resolve conflicts between teams, strived for a “168 hour” workgroup mentality • Liaison between Engineering, Quality, and Manufacturing group • Educated peers on manipulating automated applications to retrieve information needed to perform tasks effectively Show less
-
-
-
Intel Corporation
-
United States
-
Semiconductor Manufacturing
-
700 & Above Employee
-
Operations Coordinator
-
Sep 2000 - Sep 2007
• Consistently demonstrated excellent communication and organizational skills as the head of the Manufacturing Safety Chairman • Educated NPI (New Process Introduction) Technicians on software utilized in tracking and forecasting steps in processing line and record vital information which hindered throughput time • Trained Technicians on advanced automation tools utilized to measure, maximize, and record area performance • Collaborated with Production Managers and Engineering groups to identify and eliminate process line constraints to maximize output efficiency • Implemented operational indicators which increased workgroup awareness of group’s metrics and area performance • Utilized strong operations knowledge across multiple functional areas to effectively manage area resources which increased efficiency and output • Established daily production schedule goals and priorities; allocated resources as need to ensure goal and schedule attainment • Mentored peers across multiples shifts to support the plant’s vision, values and priorities • Identified and drove resolution to equipment safety and ergonomics issues • Built and maintained effective business unit relationship and role modeled cross-functional mentality in an effort to promote employee engagement Show less
-
-
Education
-
Colorado Technical University
Master of Business Administration (MBA), Project Management -
ITT Technical Institute-Knoxville
Electrical and Electronics Engineering -
National American University-Albuquerque
Bachelor of Applied Science (BASc), Management Information Systems, General
Community
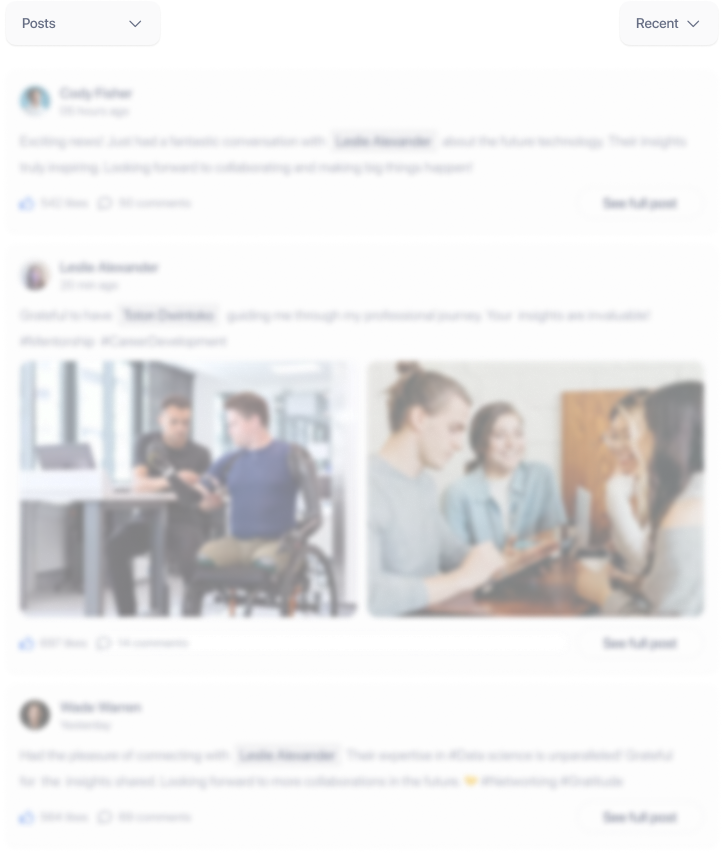