JOSE CUELLAR
Operations Manager at Jones Plastic and Engineering- Claim this Profile
Click to upgrade to our gold package
for the full feature experience.
Topline Score
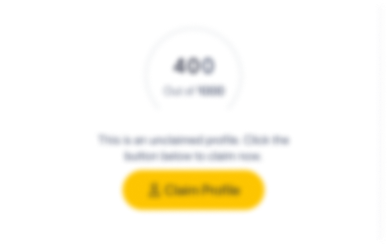
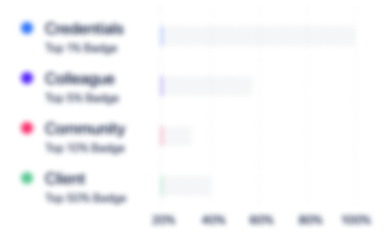
Bio


Experience
-
Jones Plastic and Engineering
-
United States
-
Plastics Manufacturing
-
200 - 300 Employee
-
Operations Manager
-
Jul 2022 - Present
Responsible of operations, production & process departments on Jones Plastic - Monterrey facility. Responsible of operations, production & process departments on Jones Plastic - Monterrey facility.
-
-
-
ISGO MANUFACTURING
-
Mexico
-
Plastics Manufacturing
-
1 - 100 Employee
-
Plant Manager
-
Oct 2019 - Jul 2022
Responsible for plant operations at Monterrey facility. Departments under my responsibility Quality, engineering, maintenance, production, tooling, materials. Responsible to establish and implement strategy to achieve company goals related to safety, quality, delivery and moral. Over +200 employees company. Main segments: Automotive industry, home accessories and refrigeration components (HVAC). Plastic products produced for main OEMs from America, Europe and Asia. Responsible for plant operations at Monterrey facility. Departments under my responsibility Quality, engineering, maintenance, production, tooling, materials. Responsible to establish and implement strategy to achieve company goals related to safety, quality, delivery and moral. Over +200 employees company. Main segments: Automotive industry, home accessories and refrigeration components (HVAC). Plastic products produced for main OEMs from America, Europe and Asia.
-
-
-
Methode Electronics
-
United States
-
Appliances, Electrical, and Electronics Manufacturing
-
700 & Above Employee
-
AMD - Plant Manager
-
May 2017 - Oct 2019
Plant Manager at AMD facility plastic industry, molding, painting and sub assembly processes reporting to Mexico Operations Director. Establish plant strategies to meet corporate goals & overall metrics focus to Safety/Quality/Delivery/Cost/MoralImplement a safety culture / 0 work accidents in plant.Create and define overall plant budget for resources, expenses and capital investment needs for Mexico operation director and corporate review and approval.Responsible to track and maintain plant within budget.Responsible to monitor and execute strategies established for annual year to report profit within target and overall positive P&L numbers.Over my direct responsibility plant staff managers for production (molding, painting and assembly), quality, materials, program management, maintenance, human resources.Responsible to create and maintain a "healthy and clean" work environment focus on team work.Ensure main KPIs are achieved in a daily, weekly and monthly base.Ensure plant ready and prepare for annual re-certifications IATF 16949:2016 and ISO 14001 auditsSupport and coordinate monthly meetings with ALL plant employees to provide an overview results on main plant metrics as well as coming events. Establish a 5s culture in all plant.Establish projects & core teams focus on continuous improvements with a weekly presentation to track progress and time lines.Ensure and prepare overall plant and team to launch new programs / products within budget and on time.Engage and support teams to all organization levels to work on continuous improvement. Always there is "A better way" to do things. Show less
-
-
Mexico Continuous Improvement Group Manager OPEX/VAVE & Mexico Product Line Manager
-
May 2015 - May 2017
Continuous Improvement Manager Responsibilities:Responsible to lead Mexico plants to achieve Annual Savings target (> 2.5 M USD)Responsible to coordinate and lead OPEX /VAVE teams from Mexico plants to work on savings projects to ensure achieve annual saving goal for North America Region.Follow and implement standardization procedures / process in Mexico plants base to corporate guidelines.Establish and meet in Mexico plants annual calendar for LEAN activities. Engage teams from Mexico plants to participate on Kaizen, workshops and VSMs to identify continuous improvement projects representing savings to company.Responsible to coach and lead OPEX engineers from Mexico plants.Meet on time LEAN activities in Mexico plants. Coordinate LEAN events.Product Line Manager Responsibilities:Main responsible for automotive product line and customer main contact.Responsible to implement on time automotive engineer changes and new model year change. Main contact to provide status and update to OEMs.Follow up with customer providing proposals on possible changes to product that represents on optimization and savings projects.(VAVE).Maintain production programs within budget and running "smoothly" Show less
-
-
Mexico Group Leader for Launch Managers
-
Jun 2013 - May 2017
Coaching / Coordinate Mexico launch managers group, engineering coordinators, PPAP’s coordinators.Responsible for all new program introductions on Mexico facilities.Responsible to establish strategy for Mexico facilities on new program introduction.During 2015, 2016 & 2017 responsible to coordinate and support launch manager group in Mexico over 3 different programs in Mexico facilities with sales over the 250M USD, over 150 tools and main programs for North America Region. Responsible to improve and standardize new program introduction procedures into Mexico facilities.Responsible to follow up and report new program status to corporate team.Over 150 molding tools were involved during last 2 years, involve with SMT, painting, assembly, laser etch process.Responsible to evaluate plant capacity for new programs introduction.Responsible to identify capital investment require for new program introduction such as assembly lines, tools, molding machines, new technologies, etc.Responsible to manage and run new programs base to budget established.Responsible to create risk assessment on new programs and establish correct action plan to minimize program risks.Direct communication between Mexico plants, customer management Show less
-
-
Engineering Manager
-
Mar 2013 - Jul 2013
Responsible for plant launch managers at AMD facility, product engineers and change engineer coordinator.Follow APQP on new programs to launch in time and smooth.Responsible for new technologies / equipment in the plant for new programs introduction.Establish strategy and procedures to follow as engineering department responsible.Responsible to coordinate and lead teams for the VA/VE projects from engineering side, reporting saving projects over 500K USD per year as annual savings. Projects such as to optimize usage of material, improve cycle times, optimize laser etch programs; improve packaging reducing cost, etc.Responsible to lead time launch manager team to launch one of the most critical & important program to the company with main automotive customers.Over 100 molding tools were involved on this program, + painting + laser etch and assembly process.Responsible to evaluate plant capacity for new programs introduction.Responsible to identify capital investment require for new program introduction such as assembly lines, tools, molding machines, new technologies, etc.Responsible to manage and run new programs base to budget established. Show less
-
-
Sr. Program Manager
-
Jul 2011 - Mar 2013
Automotive industry. Launching KEY programs in the company at AMD facility following APQP.Focus on results and APQP metrics.Main contact between facility and customer to launch new programs.Continuous participation with corporate team to launch new programs.Main leader at facility with multidisciplinary team formed with members from quality, molding process engineer, painting, assembly, tooling, materials, etc).Provide updates and results to facility staff and corporate stake holders regarding new launch programs status.Tier 1 suppliers for OEM’s Responsible for all validation process on new programs to make sure achieve goals such as timing, cost, quality, customer requirements, budget, follow company guidelines, etc. Lead facility multidisciplinary team to make sure goals are achieve on different departments to successfully launch new programs.Direct communication with final customersEstablish corrective actions with responsible names and due dates during launching process. Follow up open actions until all of them are completely closed.Training and support other program managers in the company to follow up company procedures during for New program introduction phase. Playing as “superintendent” role inside engineering department.Coordinate meetings with toolmakers and tooling engineer team to follow up and make sure tool design is robust and correct. “A good tool design avoids a lot of headache”. Show less
-
-
-
Nypro, A Jabil Company
-
United States
-
Medical Device
-
700 & Above Employee
-
Corporate / Regional Program Manager
-
Jan 2010 - Jun 2011
Main contact with customer regarding technical / launching new programs for the company.Review quote / contracts with customer to bring “new” business.Provide all initial information to Mexico facilities to launch new programs.Active participation during new business negotiation. Provide and follow up on general timeline to launch a new program. Follow up with plants manager to launch on time.Coordinate meetings for follow up activities between customer and manufacturing facility to launch new programs.Provide technical information during quoting process such as machine tonnage requirements, tooling information, cycle times, part weight, packaging requirements, quality information such as PPAP, APQP, 2D & 3D’s, validation process, resins to consider, etc.Review if second operations apply such as automatic painting process, assembly, pad printing, and other decoration technologies.Review initial investments to consider in budget. Such as tools, machines, barrels, EOAT, robots, measuring fixtures, etc.Provide updates and monthly indicators results to stakeholders (China & USA).“Sale” the customer our own technology, experience, support and advantages vs. competitors to have us as suppliers. Show less
-
-
Program Manager
-
Jan 2004 - Dec 2009
Main responsible at the plant during launch of new programs.Main contact at the plant with customer during new program introduction phase until ramp up phase.Manage / lead multidisciplinary team formed at the plant by different departments to work during entire new product introduction phase at the plant. Continuous involvement since design phase with customer and company ESI team providing necessary support required from the plant. Participation during ESI phase including design reviews, product specifications, technology to use, toolmaker validation results.Responsible for program management activities with customer such as timeline, program budget, open issue list, matrix contact list (inside company & customer), create and update weekly reports Responsible to coordinate the Mty team involved in the program to follow up with open actions, including due date and responsible person.Follow ProM guidelines.Responsible to create quote for NRE’s, such as tooling cost, validation process.Responsible to evaluate program risk during new program introduction. Main contact and support from the plant to the Global program managerResponsible to provide updates internally and customer regarding program status. Weekly reports.Responsible to request validation trails at the plant, make sure they are on time, meet customer requirements and get the customer final approval for mass production.Responsible to evaluate program capacity, meet customer peak demand, machine available, meet customer demand requirements such as pcs/day, week, month.Responsible in the plant to follow up with any engineering change required in the tool, product, assy line, process.Responsible to provide customer quotes regarding engineering change cost, lead time, validation process plan.Responsible to perform cost audit after 3 months in mass production to confirm new program within budget and main metrics achieve. Show less
-
-
Quality Engineer
-
Aug 2002 - Jan 2004
Main responsible at the plant regarding all quality topics on programs been handled by myself (includes new programs and mass production programs).Negotiate with customer product specs, 2D’s, and quality requirements.Product 2D’s review with customer, identify critical characteristics, spc dimensions, etc.Responsible to coordinate meetings with the team in order to review quality issues using toolings such as 8D’s, root cause analysis, fish bone diagram, pareto gantt chart to identify defects 80/20, establish preventive, corrective actions , Responsible to evaluate and analyze trial validation process data, such as CPK results, product dimensions, cosmetic results (variable and attributes)Responsible to coordinate and create documents such as AMEF, control plan, flow chart, quality inspections, PPAP documentation.Follow ISO and TS guidelines.Manage and supplier development regarding quality topics.Responsible for all quality process involvement on mass production product, since incoming inspection for raw material and components to dock audit. process for finish good product.During new program introduction responsible to provide training to all the plant (including, production team, supervisors, quality auditors, etc) regarding quality criteria, specs, dimensional data, critical area of the part, identify class a,b,c areas in the partMain responsible for final decision regarding quality issues if a part should be rejected, can be limited accepted base on customer negotiation, if it is acceptable, etc. Show less
-
-
-
-
Quality Engineer
-
Jan 2000 - Aug 2002
Main responsible at the plant regarding all quality topics on programs been handled by myself (includes new programs and mass production programs).Negotiate with customer product specs, 2D’s, and quality requirements.Product 2D’s review with customer, identify critical characteristics, spc dimensions, etc.Responsible to coordinate meetings with the team in order to review quality issues using toolings such as 8D’s, root cause analysis, fish bone diagram, pareto gantt chart to identify defects 80/20, establish preventive, corrective actions , Responsible to evaluate and analyze trial validation process data, such as CPK results, product dimensions, cosmetic results (variable and attributes)Responsible to coordinate and create documents such as AMEF, control plan, flow chart, quality inspections, PPAP documentation.Follow ISO and TS guidelines.Manage and supplier development regarding quality topics.Responsible for all quality process involvement on mass production product, since incoming inspection for raw material and components to dock audit. process for finish good product.During new program introduction responsible to provide training to all the plant (including, production team, supervisors, quality auditors, etc) regarding quality criteria, specs, dimensional data, critical area of the part, identify class a,b,c areas in the partMain responsible for final decision regarding quality issues if a part should be rejected, can be limited accepted base on customer negotiation, if it is acceptable, etc. Show less
-
-
Manufacturing Engineer
-
May 1999 - Jan 2000
Responsible for facility assembly area. Coordinate and responsible for assembly supervisors.Assembly line balance responsible.Responsible to achieve internal assembly metrics (production/hr, output, yields, cycle times).Responsible to optimize assembly process/area.Responsible for assembly layout, cycle times processes.Responsible for 3 shift 7 days / week. Responsible for assembly operatorsDetermine assembly flow line, optimize it and perform value stream mapping identifying value and no value added activities.Responsible for assembly operators & supervisors trainingIdentify opportunities areas at assembly and perform an action plan to improve lay outs, out put, process.Responsible to achieve assembly daily production commitments Show less
-
-
Community
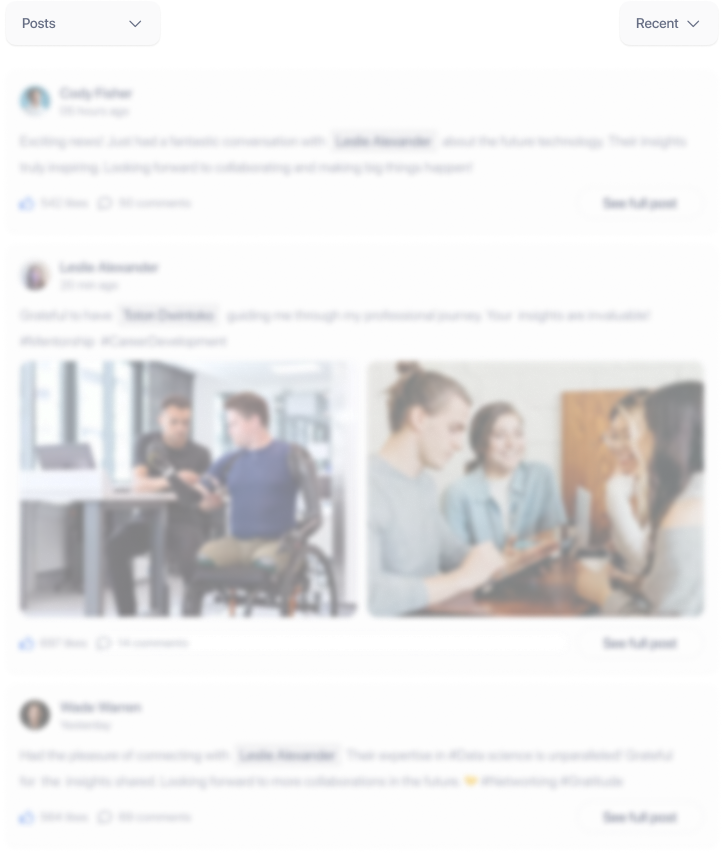