José Luis Elizondo
Plant Manager at Lecoq Cuisine Corporation- Claim this Profile
Click to upgrade to our gold package
for the full feature experience.
-
Español -
-
Ingles -
Topline Score
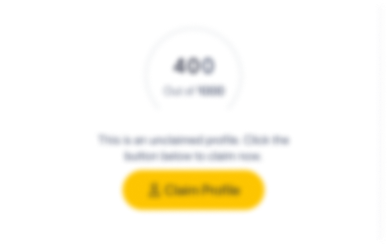
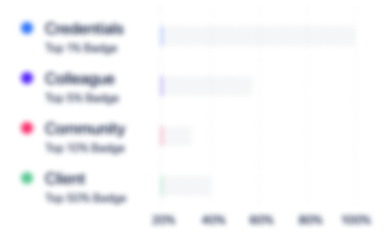
Bio


Credentials
-
Lean Manufacturing
Corporate Resources ManagementJan, 2009- Nov, 2024 -
Business Administration
Tecnológico de MonterreyJan, 2004- Nov, 2024 -
Lean Six Sigma Black Belt (ICBB)
Tecnológico de MonterreyJan, 2004- Nov, 2024
Experience
-
Lecoq Cuisine Corporation
-
United States
-
Food Production
-
1 - 100 Employee
-
Plant Manager
-
Dec 2020 - Present
• Leading Manufacturing, Warehouse and Maintenance teams to achieve key Budget, Quality, Production, On-time delivery and Preventative and corrective maintenance goals. • Working with various corporate business partners to drive plant and company initiatives. • Responsible for the Plant Capital Expense Plan. • Coordinate resources to investigate and resolve technical issues related to the manufacturing processes. • Developing a pilot program to enhance leadership and operational performance to keep morale high and employee Engagement during times of change. • Designing organization structure to accomplish company´s strategic road map. Show less
-
-
-
Eastman
-
United States
-
Chemical Manufacturing
-
700 & Above Employee
-
Operational Excellence Specialist
-
Sep 2018 - Nov 2020
• Identified and implemented innovative manufacturing processes, including automation, to improve performance measured by safety, quality, cost, and output.• Supported world-wide operations to establish reliability and best practices initiatives that reduce equipment down time by 1.88% and quality defects by 1.15%.• Led the implementation of an automated control loop for critical temperature variables that reduce the presence of contaminants in the product.• Developed and deployed Operational Excellence policies, procedures, tools, and systems.• Managed and monitor operational improvement initiatives to analyse sustainable benefits.• Defined, monitored, and improved key process indicators across global operations and sites. Show less
-
-
PLANT MANAGER
-
Oct 2012 - Sep 2018
• Led Research & Development, Manufacturing, Supply Chain, Quality and Health, Safety, Environmental, and Security teams.• Drafted and implemented project budgets and plans to develop medical device products of capital scales up to $1,300,000.• Translated executive team programs into operational schedules to achieve to grow sales by 3% and meet organization goals.• Led a wage progression and shift rotation model to bolster workforce flexibility and support new business initiatives.• Prepared initiatives geared towards operational excellence, safety, quality, and cost improvement to support all departments. Show less
-
-
Plant Manager
-
Oct 2011 - Sep 2012
• Led the operational launch of a company product with an estimated impact of $1,500,000.• Led R&D, manufacturing, supply chain, quality, and health, safety, & environmental teams.• Planned and managed the installation, testing, operation, maintenance, and repair of facilities and equipment.• Developed and implemented global corporate policies, standards, and procedures to increase operational efficiency.• Prepared detailed plans to accomplish goals and directed the integration of technical activities.• Created and managed key result metrics for all sites to identify opportunities and implement solutions toward company goals Show less
-
-
-
Solutia
-
Business Consulting and Services
-
1 - 100 Employee
-
Business Unit Lead
-
2008 - Jan 2011
• Increased production line gross yields by 9% as the on-site representative of the World-Wide Asset Effectiveness Management Team.• Led teams to improve key process indicators such as an annual rework reduction of $900,000 by fostering a teamwork culture and implementing training programs.• Managed the processes, budgets, and workforce of the operations area.• Identified and solved process bottlenecks to reduce cycle-times and equipment change-overs.• Tracked and analysed costs of 6-Sigma continuous improvement projects and assisted R&D in new product transfers. Show less
-
-
Manufacturing Team Lead
-
May 1998 - Jun 2008
• Led new product manufacturing trials and analysed outcomes to improve line efficiency and rework levels.• Developed manufacturing concepts for new products that reduced capital investment requirements by $875,000 annually.• Recorded and organized manufacturing metrics to lead problem-solving investigations.• Oversaw production line modification projects that expanded mass production volume capacities by 20%.• Planned and recommended strategies to ensure all products met their specifications.• Managed the day-to-day operations of manufacturing teams.• Led teams through ISO accreditation audits and ensured safety guidelines were followed. Show less
-
-
Process Engineer
-
Mar 1996 - Apr 1998
• Drove a 4% reduction in batch cycle times by optimizing equipment and processes.• Identified and implemented efficiency, safety, quality, and cost improvements on equipment and processes.• Analysed data to ensure product consistency and coordinate root cause failure investigations.• Implemented corrective and preventive actions in conjunction with supporting areas.• Implemented start-up plans for manufacturing line expansions in collaboration with international engineering teams. Show less
-
-
-
CONSORCIO INDUSTRIAL
-
Mexico
-
Oil and Gas
-
1 - 100 Employee
-
Operations Manager
-
1991 - 1995
• Led an initiative to revise products’ bill of materials with alternative raw materials that reduced cost by 15%. • Implemented and managed key process indicators to reduced downtime by identifying and solving equipment issues. • Reduced operator downtime by redesigning workstations, eliminating wasteful activities, and implementing error prevention methods to avoid defects. • Supervised daily operations and trials for new products. • Led an initiative to revise products’ bill of materials with alternative raw materials that reduced cost by 15%. • Implemented and managed key process indicators to reduced downtime by identifying and solving equipment issues. • Reduced operator downtime by redesigning workstations, eliminating wasteful activities, and implementing error prevention methods to avoid defects. • Supervised daily operations and trials for new products.
-
-
-
M&G Polímeros México, S.A. De C.V.
-
Mexico
-
Chemical Manufacturing
-
1 - 100 Employee
-
Manufacturing Team Lead
-
1990 - 1991
• Drove a 4% increase in equipment throughput by analysing equipment designs for capacity and reporting solutions. • Developed and maintained operating work procedures to standardize operator activities. • Tracked and recorded manufacturing summaries, line efficiencies, and rework levels. • Arranged problem-solving investigations. • Coordinated operator workloads. • Drove a 4% increase in equipment throughput by analysing equipment designs for capacity and reporting solutions. • Developed and maintained operating work procedures to standardize operator activities. • Tracked and recorded manufacturing summaries, line efficiencies, and rework levels. • Arranged problem-solving investigations. • Coordinated operator workloads.
-
-
-
Rassini
-
Mexico
-
Automotive
-
500 - 600 Employee
-
Quality Control Analyst
-
1987 - 1989
• Performed and reported tests to certify that all incoming and finished goods met quality standards. • Increased availability of measuring devices by analysing usage data and developing a streamlined scheduling system. • Developed a program for lab area training and task-based certification. • Performed and reported tests to certify that all incoming and finished goods met quality standards. • Increased availability of measuring devices by analysing usage data and developing a streamlined scheduling system. • Developed a program for lab area training and task-based certification.
-
-
Education
-
Benemérita Universidad Autónoma de Puebla
LICENCIATURA EN INGENIERIA QUIMICA, Chemical Engineering -
Tecnológico de Monterrey
Community
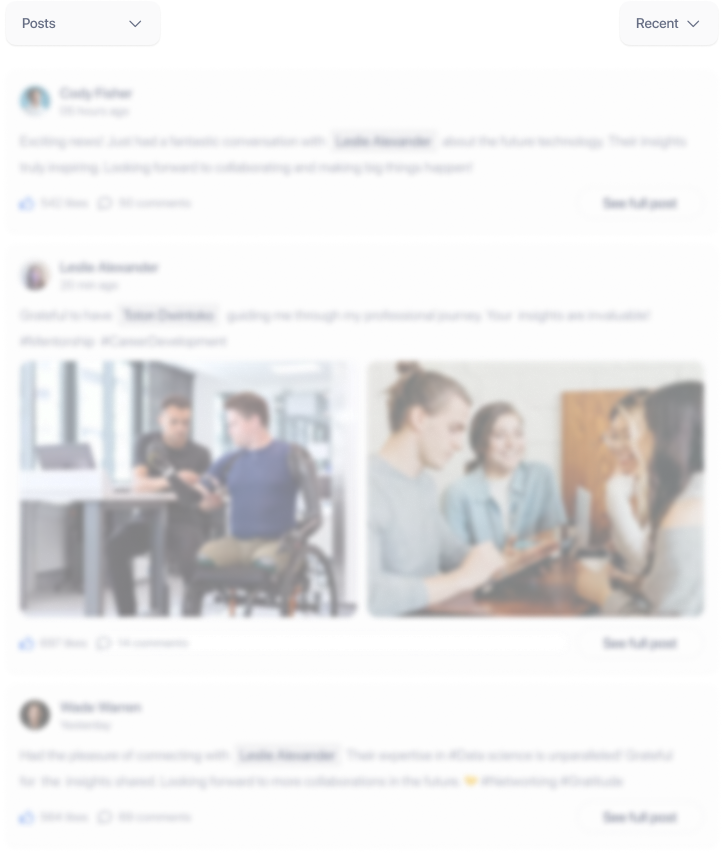