
José Henrique Freire Júnior
Quality Analyst at Tokai Rika Brasil - TRBR- Claim this Profile
Click to upgrade to our gold package
for the full feature experience.
-
Inglês Full professional proficiency
-
Português Native or bilingual proficiency
Topline Score
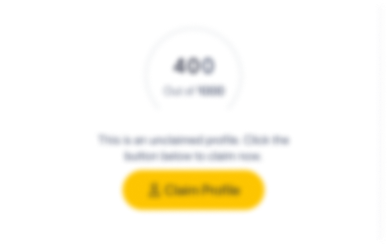
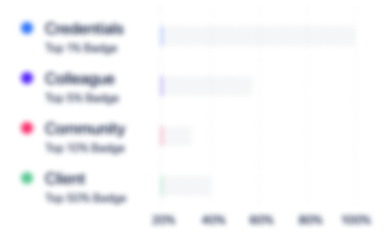
Bio

Renan Carlos
Tive o prazer de trabalhar com o José na Hwashin, profissional altamente qualificado, alto conhecimento na área onde trabalha, eu recomendo fortemente este profissional e recomendo tambem pelo seu carater, pessoa honesta e de familia!

Renan Carlos
Tive o prazer de trabalhar com o José na Hwashin, profissional altamente qualificado, alto conhecimento na área onde trabalha, eu recomendo fortemente este profissional e recomendo tambem pelo seu carater, pessoa honesta e de familia!

Renan Carlos
Tive o prazer de trabalhar com o José na Hwashin, profissional altamente qualificado, alto conhecimento na área onde trabalha, eu recomendo fortemente este profissional e recomendo tambem pelo seu carater, pessoa honesta e de familia!

Renan Carlos
Tive o prazer de trabalhar com o José na Hwashin, profissional altamente qualificado, alto conhecimento na área onde trabalha, eu recomendo fortemente este profissional e recomendo tambem pelo seu carater, pessoa honesta e de familia!

Experience
-
Tokai Rika Brasil - TRBR
-
Brazil
-
Motor Vehicle Manufacturing
-
1 - 100 Employee
-
Quality Analyst
-
Mar 2018 - Present
• Primary contact to Toyota, Honda and Mitsubishi to solve quality issues;• Prepared customer Production Part Approval Process (PPAP) from new developments;• Managed warranty claims throught failure analysis and provided feedback to head quarter in Japan; • Trained production team on quality and lean concepts to avoid quality issues and unnecessary process steps;• Tracked customer satisfaction by compiling key performance indicators such as PPM, non-quality costs, customer intimacy, and warranty claims;• Conducted internal process / product audit and open issues to the areas and analyse corretive actions;
-
-
-
Hwashin - Peças Automotivas Brasil
-
Brazil
-
Automotive
-
100 - 200 Employee
-
Quality Analyst
-
Jul 2016 - Mar 2018
• Primary contact to Hyundai and Kia to solve quality issues;• Performed Statistical Process Control (SPC) on manufactured parts and registered the values in a quality report;• Managed a team of 3 quality inspector on regular basis;• Conducted internal process / product audit and open issues;• Provided quality support in customer ISO TS16949 audit and answered corretive actions;• Performed all quality documentation review during Enginnering Change Product (ECP). • Primary contact to Hyundai and Kia to solve quality issues;• Performed Statistical Process Control (SPC) on manufactured parts and registered the values in a quality report;• Managed a team of 3 quality inspector on regular basis;• Conducted internal process / product audit and open issues;• Provided quality support in customer ISO TS16949 audit and answered corretive actions;• Performed all quality documentation review during Enginnering Change Product (ECP).
-
-
-
Industrias Machina Zaccaria
-
Brazil
-
Machinery Manufacturing
-
1 - 100 Employee
-
Quality Control
-
Jul 2014 - Jul 2016
• Performed troubleshooting (8D) conducted root cause analysis and develop action plans;• Led improvement projects using PDCA methodology and quality tools;• Provided quality support to regular suppliers with training on quality tools and problem solution methodologies;• Managed a team of 2 quality inspector on regular basis;• Tracked customer satisfaction by compiling key performance indicators such as non-quality costs, customer claim. • Performed troubleshooting (8D) conducted root cause analysis and develop action plans;• Led improvement projects using PDCA methodology and quality tools;• Provided quality support to regular suppliers with training on quality tools and problem solution methodologies;• Managed a team of 2 quality inspector on regular basis;• Tracked customer satisfaction by compiling key performance indicators such as non-quality costs, customer claim.
-
-
-
Maxion Wheels
-
Germany
-
Motor Vehicle Manufacturing
-
700 & Above Employee
-
Process Engineer (Co-op)
-
Jul 2012 - Jun 2014
• Performed control plan, process flow chart and work standard of wheels that was being developed;• Provided engineering support to stamping try outs with focus on material preparation and summarization of issues from each development step;• Led a six-sigma project that decrease 15% of costs with laser cut stamping material and this project was classified among 10 best on 2013;• Provided engineering support during Process Failure Mode and Effects Analysis (PFMEA) meeting. • Performed control plan, process flow chart and work standard of wheels that was being developed;• Provided engineering support to stamping try outs with focus on material preparation and summarization of issues from each development step;• Led a six-sigma project that decrease 15% of costs with laser cut stamping material and this project was classified among 10 best on 2013;• Provided engineering support during Process Failure Mode and Effects Analysis (PFMEA) meeting.
-
-
-
Pro-Metal
-
Mechanical Or Industrial Engineering
-
100 - 200 Employee
-
Quality Technician
-
Nov 2009 - Jul 2012
• Primary contact to Volvo, Faurecia, Tenneco, Continental, Whirlpool to solve quality issues;• Submitted quality documents to validate the product and process through PPAP methodology;• Conducted process audit using the Standard VDA 6.3 as parameter;• Performed mensurement at Coordinate Measuring Machine and performed Lay Out Inspection reports;• Managed regular suppliers to validate their products through PPAP analysis. • Primary contact to Volvo, Faurecia, Tenneco, Continental, Whirlpool to solve quality issues;• Submitted quality documents to validate the product and process through PPAP methodology;• Conducted process audit using the Standard VDA 6.3 as parameter;• Performed mensurement at Coordinate Measuring Machine and performed Lay Out Inspection reports;• Managed regular suppliers to validate their products through PPAP analysis.
-
-
Education
-
Einstein Faculdade e Colégio
Bachelor degree in Production Engineering, Engenharias -
Universidade Estadual de Campinas
Quality Management (3 years technical course), Qualidade -
SENAI SP
Mechanical Technician (2 years technical course), Área de Usinagem
Community
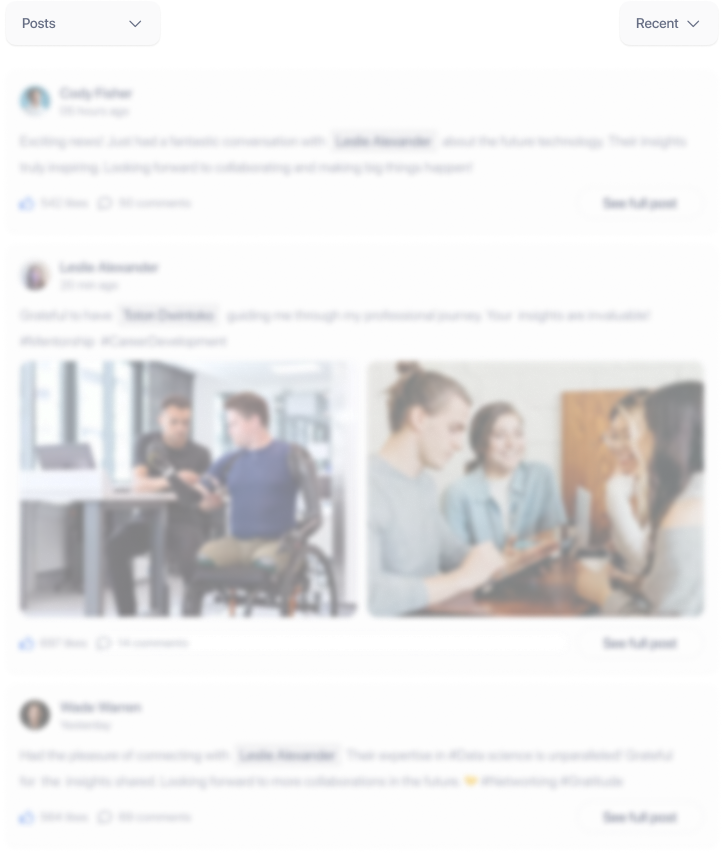