
Jorge Z.
Director of China Operations at Filamento- Claim this Profile
Click to upgrade to our gold package
for the full feature experience.
Topline Score
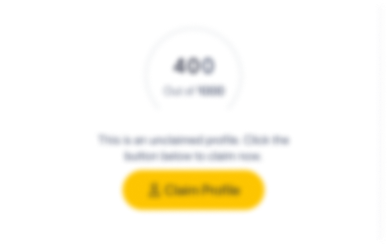
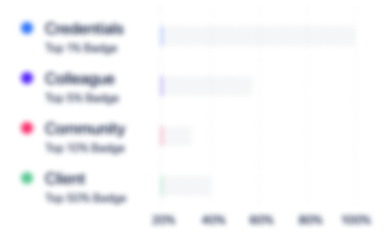
Bio


Experience
-
-
Director of China Operations
-
Aug 2020 - Present
Oversee all aspects of Operations and Supply Chain in Asia to ensure reliable, compliant, cost effective, and on-time supply of product and drive the continuous improvement on output, quality and cost etc.-.Manage the supply chain and quality and commercial aspects of Filamento Asia, but not limited to, quality, purchasing, logistics, warehousing, inventory management, material forecasting, capacity planning and sourcing, master scheduling.-.Serve as the lead in Asia for supply and… Oversee all aspects of Operations and Supply Chain in Asia to ensure reliable, compliant, cost effective, and on-time supply of product and drive the continuous improvement on output, quality and cost etc.-.Manage the supply chain and quality and commercial aspects of Filamento Asia, but not limited to, quality, purchasing, logistics, warehousing, inventory management, material forecasting, capacity planning and sourcing, master scheduling.-.Serve as the lead in Asia for supply and Operations and oversee the forecast planning, demand planning and inventory management of products in the pipeline.-.Oversee product purchasing and planning at contract manufacturers and logistic suppliers.-.Work with suppliers, to identify and qualify shipping routes for the product including establishment and oversight of rolling forecasts.-.Review and oversee Supplier Agreements and Contracts with vendors and partners. Coordinate the execution of purchase orders for finished products as approved and agreed.-.Partner and collaborate with other Senior Management to achieve and continually maintain maximum operational efficiency, interdepartmental coordination, and initiative / projects prioritization.-.Initiate and coordinate Quality Improvements, Operational Excellence techniques, Business Process optimization, Budget Analyses and Cost Reduction processes / programs sufficient to ensure that the most effective ‘best practices’ are in place.-.Demonstrated track record to run project on time and on budget.-.Oversee the R&D activities and transfer to manufacturing.-. Set up ERP/SOS and Quality Systems including all necessary documentation such as SOPs, IQC, Purchase Agreements.-.Prepare management reports, metrics, presentations, KPIs sufficient to communicate and measure functional area performance on regular basis. Show more Show less
-
-
-
-
Independent Consultant
-
Sep 2019 - Aug 2020
-. As a senior consultant, train and coach some start-up companies on Quality Management(ISO, Six Sigma)& Lean Manufacturing& Supply Chain management etc.-. As a tutor, give guidance to my boy on mathematics and English in Grade 6, ensuring smooth transition from primary school to middle school. Also, be as a volunteer in WFLS primary school.
-
-
-
-
Regional Quality Head, Asia
-
Mar 2012 - Aug 2019
As Regional Quality Head, strives to be the leader in overall quality management and ability to scale to support Smart Vacuum Cleaner’s engagement from NPI to MP. Major responsibilities include:• Work with US Engineering and Asia Operation team, to participate/facilitate Quality Earlier Involvement in NPI stage, i.e. product design overview, project scope review, DFMEA, SKU&BOM, new parts/suppliers, PPAP, PFMEA, product agency approval, reliability testing for new parts and products, SW/MFG… As Regional Quality Head, strives to be the leader in overall quality management and ability to scale to support Smart Vacuum Cleaner’s engagement from NPI to MP. Major responsibilities include:• Work with US Engineering and Asia Operation team, to participate/facilitate Quality Earlier Involvement in NPI stage, i.e. product design overview, project scope review, DFMEA, SKU&BOM, new parts/suppliers, PPAP, PFMEA, product agency approval, reliability testing for new parts and products, SW/MFG testing in-process, NPI issue list and actions follow-up, QCP and SIP creating, 4M1E readiness for coming PVT and MP etc.• Develop/Survey new CMs(contract manufacturers) for LDS/Robot Assembly and new suppliers for Mass Production of high quality parts. Manage suppliers in Mass Production to continuously produce high quality products/parts consistently, with yield improvement quarter to quarter. Qualify and bring-up of potential new suppliers and CMs to support increased capacity and new programs (addressing all aspects of supplier quality/ process readiness).• Review Neato’s specification/requirements with approved CMs, key suppliers, sub-suppliers according to company quality standards, qualifies assembly lines and fixtures, and manages the limit samples. • Establish inspection procedures and processes(SIP), and perform some limited inspection of incoming parts, return product and shippable product. Develop/monitor the standard processes and procedures with effective implementation.• Ensure supplier quality assurance to meet Neato’s requirements: reviews IQC rejects and MRBs; involves with CMs and supplier quality issues & drives for quality improvement; monitors FATP fallout; drives supplier FACA and 8D reporting. • Manage the agency approval of new products and design change i.e. CCC, TUV, UL, NRTL, PSE, FDA, SRRC etc. Show more Show less
-
-
-
-
Deputy General Manager, Quality&Environment
-
Aug 2009 - Jan 2012
Supplier Quality / Production Quality / Customer Quality / Cost of Qualtiy / QMS&EMS&RoHS compliance / Continuous Improvement Process1. Oversee the overall quality function and ensure quality product supply to meet customer requirement, including Supplier Quality, Production Quality, Customer Quality, Design Quality, Calibration, QMS & EMS & RoHS, CIP steering group.2. Appointed as the Management Representative of Shenzhen site to liaise directly with external third party system auditor… Supplier Quality / Production Quality / Customer Quality / Cost of Qualtiy / QMS&EMS&RoHS compliance / Continuous Improvement Process1. Oversee the overall quality function and ensure quality product supply to meet customer requirement, including Supplier Quality, Production Quality, Customer Quality, Design Quality, Calibration, QMS & EMS & RoHS, CIP steering group.2. Appointed as the Management Representative of Shenzhen site to liaise directly with external third party system auditor on ISO9001&ISO14001 certification program, and product safety audits plus certification program.3. Continuously review and improve Shenzhen site QMS&EMS by defining necessary quality objectives and targets (Customer complaints and Resolution time, RTY, DPPM, LRR, CoQ, WASTE etc.) through management review meeting regularly.4. Lead Supplier Quality Engineering (SQE) & IQA function to drive Earlier Supplier Quality Involvement in new product development phase and ensure continuous improvement of suppliers’ quality performance by the phases of supplier selection, supplier quality development, supplier on-site assessment, supplier qualification and supplier quality monitoring.5. Lead Production Quality Engineering (PQE) team to establish the process control & sampling plan product/process criteria, outgoing sampling plan, reliability test plan upon the product mature & customer requirement. 6. Lead Customer Quality Engineering (CQE) team to liaise with internal and external customers in critical quality issues and facilitate customer audits. Organize regular meeting and actions driven for potential & formal customer concerns to facilitate the achievement of zero defect supplying. 7. Lead internal Quality & Environmental Management System audit / process audit on planned regular basis and report to top management on the continuous compliance level of QMS&EMS in relation to ISO9001&ISO14001 international standard. Show more Show less
-
-
-
-
Global Supplier Quality Manager
-
Jan 2003 - Jun 2009
Global Supplier Quality Management,Early Supplier Qualtiy Development, Supplier Audits(QSA/RSC/CSR/QPA), New Supplier and Component Approval Process, Supplier CNP Management, SCAR, MRB, SSS-Performance Management, Supplier Training and Coaching, Material Quality KPI Reporting, Component CIP.1. Lead the Global Supplier Quality Engineering function on establishing, educating, and driving internal quality requirement and expectations with the suppliers among the global sites of China, Brazil… Global Supplier Quality Management,Early Supplier Qualtiy Development, Supplier Audits(QSA/RSC/CSR/QPA), New Supplier and Component Approval Process, Supplier CNP Management, SCAR, MRB, SSS-Performance Management, Supplier Training and Coaching, Material Quality KPI Reporting, Component CIP.1. Lead the Global Supplier Quality Engineering function on establishing, educating, and driving internal quality requirement and expectations with the suppliers among the global sites of China, Brazil and India. 2. Supports and/or drives global sourcing development and qualification projects necessary to improve total costs, quality and supply risk working with Quality and Procurement Organizations, Sourcing engineers, Operations and Engineering functions. 3. Manage the Supplier Audits to evaluate supplier capabilities, quality & environmental system in the process of supplier qualification and certification, executes supplier quality objectives consistent with product requirement and company criteria.4. Facilitate the Earlier Supplier Quality Involvement and Advanced Quality Planning of new products as required by Project Management(such as, Critical Characteristic Review, New component/ Tooling approval, Supplier Quality Risk Review, Quality Process Audit for safety critical components, New Product Ramp-up Report etc.)5. Organize the training and coaching to ensure specification and technical requirements can be achieved using quantitative measures and process control methods among the global sites of China, Brazil and India. 6. Manage the process of Supplier Change Notification& implementation status tracking on ECR/ECO documentation on the change of those key suppliers of specified/customized components.7. Supplier performance follow up with proactive actions to protect company from supplier issues and works on objectives, goals, monitors and analyze the supplier trends in quality KPI in order to control the efficiency of improvement actions, Show more Show less
-
-
-
-
Senior Quality Engineer
-
Mar 2002 - Jan 2003
1. To assist QA manager to setup quality KPI e.g. Material Quality, RTY, Product Return Counts, Customer Complaints, Cost of Quality etc.; Formulate, maintain and coordinate quality objectives in cooperation with cross-functional departments.2. To initiate standards/methods for inspection, testing, and evaluation, utilizing knowledge in engineering fields such as electronics or mechanical; Devise sampling procedures of IQA/IPQA/FQA/OQA; Develop instructions and forms for recording… 1. To assist QA manager to setup quality KPI e.g. Material Quality, RTY, Product Return Counts, Customer Complaints, Cost of Quality etc.; Formulate, maintain and coordinate quality objectives in cooperation with cross-functional departments.2. To initiate standards/methods for inspection, testing, and evaluation, utilizing knowledge in engineering fields such as electronics or mechanical; Devise sampling procedures of IQA/IPQA/FQA/OQA; Develop instructions and forms for recording, evaluating, reporting quality and reliability data. 3. To develop and implement the procedures for disposition of discrepant/ non-conformance material and devise methods to assess quality cost and responsibility.4. To establish program to evaluate MSA of production equipment and testing, measurement and analytical instruments.5. To investigate and handle key customer quality complaints with 8D and liaise with customers and suppliers where necessary. Responsible for customer satisfaction development& organizing regular meeting to provide sufficiently detailed information to initiate productions quality improvement; Actions driven for potential & formal customer concerns to facilitate the achievement of zero defect supplying. 6. To plan and organize internal training activities related to product quality and reliability; Compile and write training material and conduct training sessions on quality control activities and problem solving toolkits. Show more Show less
-
-
-
-
Quality Engineer/ Project Engineer
-
Sep 1996 - Mar 2002
Product/Customer Quality Engineering Project Engineering at TDK Kofu city, Yamanashi-ken, Japan1. Contact with oversea customers on product specification and quality standard, quality plan and guideline.2. Perform QMS internal audit, production line audit; Participate the local supplier audits with Purchasing Department.3. Confirm the result of First Article Evaluation for piece parts. Follow up the Initial Production Control report for new project.4. Review production 4M1E… Product/Customer Quality Engineering Project Engineering at TDK Kofu city, Yamanashi-ken, Japan1. Contact with oversea customers on product specification and quality standard, quality plan and guideline.2. Perform QMS internal audit, production line audit; Participate the local supplier audits with Purchasing Department.3. Confirm the result of First Article Evaluation for piece parts. Follow up the Initial Production Control report for new project.4. Review production 4M1E readiness and optimize process parameters and improve process capability. 5. Handle non-conforming products, and do failure analysis and ensuring effective corrective actions taken.6. To investigate and handle customer complaints and field returns.7. 6 months working experience at Kofu of Japan to transfer new projects of Thermal Printer Head. Show more Show less
-
-
Education
-
Huazhong University of Science and Technology
-
ASQ-美国质量协会
-
SBTI & NOKIA
Community
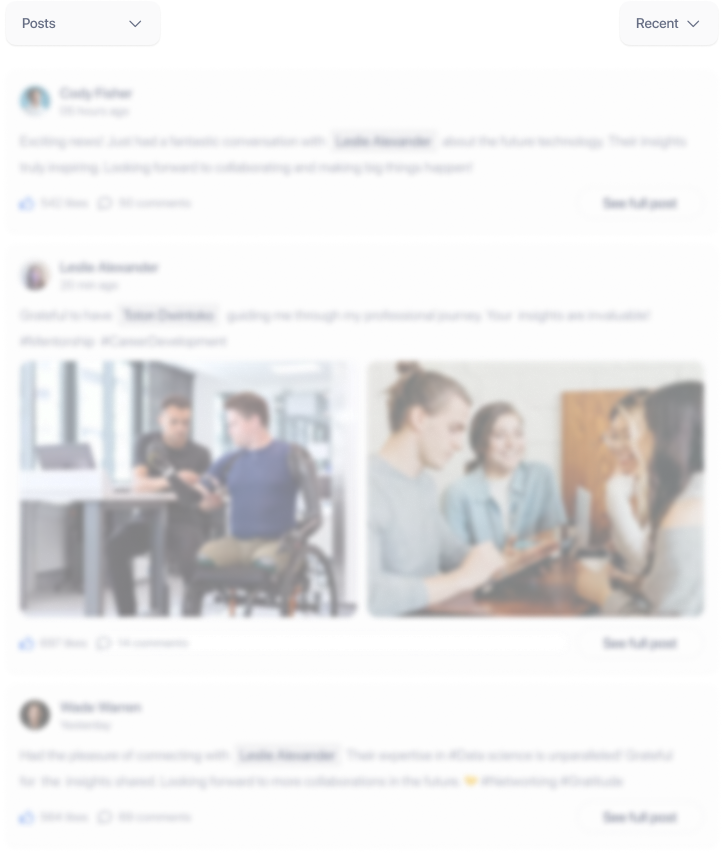