
Jonathan Tindall
Product Manager PC-21 at Pilatus Aircraft Ltd- Claim this Profile
Click to upgrade to our gold package
for the full feature experience.
Topline Score
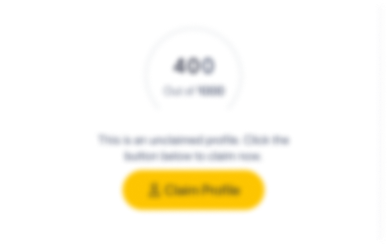
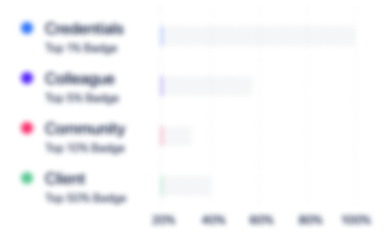
Bio


Experience
-
Pilatus Aircraft Ltd
-
Switzerland
-
Aviation and Aerospace Component Manufacturing
-
700 & Above Employee
-
Product Manager PC-21
-
Sep 2021 - Present
-
-
PC-12/PC-24 Principle Engineer Avionics (Automatic Flight Control Systems)
-
Oct 2017 - Present
PC-24: Automatic Yaw Trim development, Overspeed Protections/Tactile Feedback, Autothrottle enhancementsFly-By-Wire Feasibility Study.PC-12: Development, Integration and certification of Tactile Feedback System, Autothrottle, Emergency Descent functions. Autopilot/Yaw Damper enhancements/Bug fixes/Improvements.PC:24: Autopilot/Yaw Damper/ hold items/enhancements/Bug fixes/Improvements.
-
-
PC-24 Lead Avionics Engineer
-
Nov 2010 - Oct 2017
Avionics Lead Engineer from initial concept of the PC-24 until Certification.Responsible for developing Avionics related marketing requirements, defining PC-24 Avionics Requirements, SOW, developing initial programme plan and selection of supplier. Co-ordinating activities and work share amongst other engineers working on the program.Design and Development of Safety Critical Stall Warning and Protection and Probe Heating Systems.Overall engineering lead to take PC-24 Avionics project through concept to certification, integrating functionality such as; Utility Management System, TCAS 2, ADSB Out Transponders, MMDR (VUHF, VOR/ILS), ADF, IRS, AHRS (DG Mode), Air Data System Integration, Synoptic Pages for display and control of Systems, CAS (Inc Inhibits and Suppression), Display Management/Window Navigation, FADEC Integration, Landing gear display, CPCS Integration, EGPWS, FMS, GNSSU (WAAS), Radalt, WX Radar, XM Weather, Electronic checklists, Synthetic Vision, RAAS, 2D Maps, Datalink, Global Weather, Weather RadarSystem Modelling produced in Simulink/Matlab and Labview. Responsible for managing test plan of all functionality up to first flight, developing rig and aircraft test procedures. Responsible for developing and managing the Avionics Problem Reporting System. Responsible for system configuration, support to physical integration of all equipment, driving architecture to meet a Sys1/2 functional and physical split. Support to Flight Test, Safety, Reliability and Maintainability, AeroDynamics, Design, Technical Publications, Mechanical Systems, Human Factors, Pilots, Aircraft Fault Finding, EMC
-
-
Lead Avionics Engineer - PC-21 Air to Ground Radar
-
Nov 2008 - Nov 2010
Overall engineering lead for the integration of a simulated Air-Ground Function into the PC-21 Mission System. Responsible for System Level Functional requirements, allocating requirements to Radar Simulator and Mission System suppliers.Managed Team of Sub Suppliers, HW, and SW Components, Test and Flight Test Activities to complete the project from concept until Certification and Customer Verification activities.
-
-
-
Pilatus Aircraft Ltd
-
Switzerland
-
Aviation and Aerospace Component Manufacturing
-
700 & Above Employee
-
Avionics Engineer - Navigation Systems PC-21
-
Nov 2004 - Feb 2008
Responsible for the overall Navigation System including Mission System Tactical Navigation, FMS, GNSSU, IRS, Radalt, TACAN VOR/ILS, DME and Primary and Secondary Flight Displays on the PC-21 Aircraft.Definition of Subsystem Requirements, Equipment specifications, use of DOORSSystem Design and Integration of Flight Management System and Sensors, Definition of Navigation System Ground Test Procedures, Support to development of Flight Test Procedures, Production of Production Test Instructions, conducting test procedures, writing test reports and qualification documentation, producing a FAR 23requirement compliance matrix, training certification authority pilots in use of aircraft equipment for evaluation flights, to aid IFR certification of the PC-21 Aircraft. Supplier Management, Support in Rig Development, support to technical publications, support to training systems.Equipment Engineering, familiarity with RTCA/DO-160, System Design, Architectural Definition, System Integration of TACAN, Radalt, HMI design changes to cockpit displays and controls.
-
-
-
BAE Systems
-
United Kingdom
-
Defense and Space Manufacturing
-
700 & Above Employee
-
Safety Engineer Hawk Aircraft
-
2002 - 2004
Use a safety process based on MIL_STD 882 and using parts of DEFSTAN 00_56.Functional Failure Analysis on aircraft Mission Planning and Ground system as part of hazard identification.Radar Emulator: Hazard Checklist as part of the hazard identification process. Hazard mitigation through hardware interlocking, safety devices, SIL allocation and training/procedures. Influencing the design and writing safety requirements. Producing fault trees using fault tree +, reviewing vendors FMEAs and obtaining failure rates from reliability department. Hazards closed after presenting slides to the customer at the project safety committee. Wrote a safety procedure for writing/deriving safety requirements during the safety process.Navigation subsystem: Produced Mitigation strategies, Fault trees, reviewing vendor FMEAS, safety plans, preliminary hazard lists, improving safety by design improving aircraft wiring. Training fellow team members in producing mitigation strategies for attack and communications subsystems, and autopilot.Moving Map and TCAS: Hazard identification through functional failure analysis.
-
-
Avionics Systems Engineer - Hawk Aircraft
-
2000 - 2002
Navigation subsystem: Functional modelling using data flow diagrams and yourdon methodology. Allocation of functions to physical equipments within the avionics architecture using CRADLE.Equipment Engineer: Health & Usage Monitoring system (including crash recorder). Writing specifications including functional, and performance requirements, environmental requirements, reliability requirements, maintainability requirements, interface requirements and physical requirements. Production of an ICS.Worked with Test and Evaluation writing and reviewing Functional and Performance Test Procedures and Reports.Supporting Production during the aircraft production by writing installation test procedure to ensure system is correctly integrated within the aircraft and resolving issues such as failures and aircraft wiring problems via fault finding.
-
-
Education
-
Cranfield University
Master's Degree, Systems Engineering for Defence -
Newcastle University
Bachelor's Degree, Electrical, Electronic and Communications Engineering Technology/Technician
Community
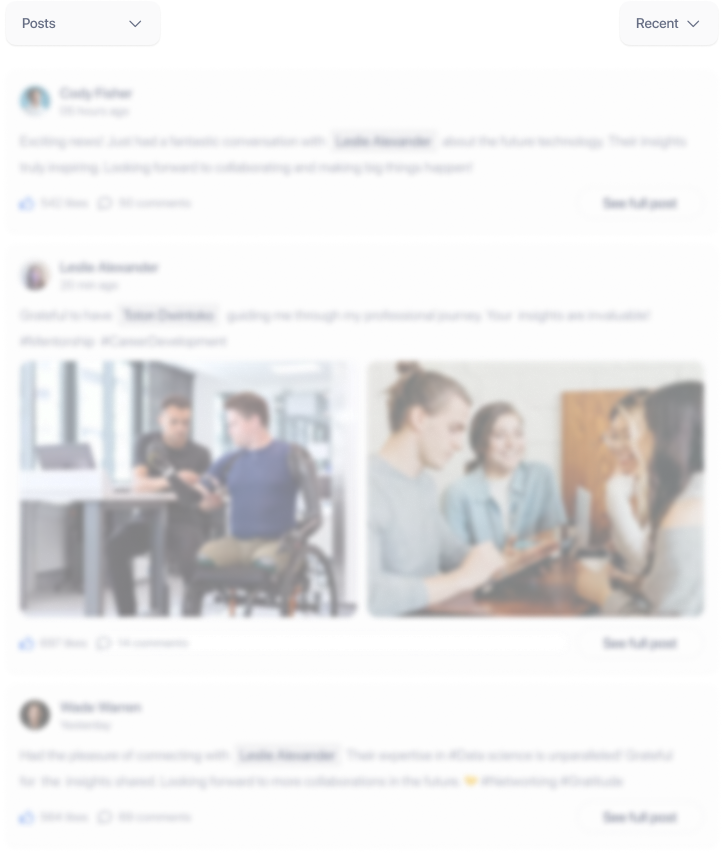