Jonathan Moreno
Quality Engineer at Suhner Abrasive USA- Claim this Profile
Click to upgrade to our gold package
for the full feature experience.
-
Spanish Native or bilingual proficiency
-
English -
Topline Score
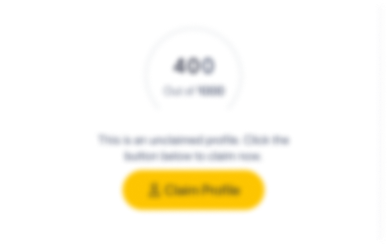
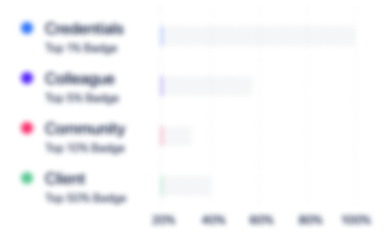
Bio


Experience
-
Suhner Abrasive USA
-
United States
-
Machinery Manufacturing
-
1 - 100 Employee
-
Quality Engineer
-
Mar 2022 - Present
-
-
-
Cooper Standard
-
United States
-
Motor Vehicle Manufacturing
-
700 & Above Employee
-
APQP Quality Engineer
-
Oct 2020 - Mar 2022
Responsibilities: • APQP documentation submission at customer portals (GM, Ford) • Manage deliverables at customer portals. • Root cause analysis and implementation of corrective actions for new processes & products. • Quality Leader for new launches. • Coordinate multidicilpinary team to comply with APQP deliverables. • Develop training to improve the Quality culture into the factory. Sr SQE (Six Months) • Manage MRB cages. • Supplier PPAP documentation review and approval. • Incoming area supervisor. • Supplier 8Ds monitoring and evaluation. • Supplier Engineering changes. • Recover supplier chargebacks from Defective material notifications • Provide supplier PPAP documentation for customer approval. • Supplier Quality Engineer for inter-companies (China, India) Achievements: As SQE the MRB cages were properly managed from a 451,269 USD in stock to 6,002 USD in two months, modifying the MRB Goal from 53K USD to 23K USD . Recovered chargesback of 20K USD in 2021 from suppliers. As APQP Quality Engineer all the program deliverables were submitted on time at the customer portals, 0 delays. 2 Engineering changes and one new program successfully implemented with GM and FORD. 3 Ideas Kaizen successfully implemented of 5 ideas submitted. Show less
-
-
-
Honeywell
-
United States
-
Appliances, Electrical, and Electronics Manufacturing
-
700 & Above Employee
-
Sr.Customer Quality Engineer
-
Aug 2016 - Oct 2020
Responsibilities: • Quality leader in charge of a customer focus Team initiative. • Supplier Quality Engineer for inter-companies (China, India) • Supplier issues, PPAP’s follow up • Root cause analysis and implementation of corrective actions for processes & products. • Assist Quality Leader implementing and maintaining the Proactive Quality Program. • Coordinate corrective and preventive actions to improve the Manufacturing process. • Develop training to improve the Quality culture into the factory. • Provide statistical data for electrical tests and Quality data. • Coordinate corrective actions to respond to customer complaints. • Continuos improvement by using six sigma tools. • Develop/upgrade inspection procedures for the quality department. • Support development of PFMEA and Control Plan documents. • Supervise QA Inspectors and work with In-process Quality Engineer • Assist the NPI and Manufacturing Engineering team. • Develop and maintain company, site and department metrics. Achievements: Succesfull engineering changes for critical components by leading suppliers, cordinating, communicating and executing all the activities to achieve the changes. Reducing RMA’s amount from 36 to 2 RMAs in three months, and improving the customer response from 26 to 3 days when the goal is 10 days. Improved the scorecard from 7.1 to 8.8 (Quality, delivery and service) from one of or most important medical customers by leading and working with the suppliers and internal team. Working with Japan team to implement Customer focus team initiative for most important Japan Customer (Horiba), by leading the meetings, working with Japan to align quality visual criteria, visiting and having good relationship with Honeywell Japan and customer.A improvement plan was implemented to improve the Quality and yield by using the DMAIC methodology: The overall cost avoidance was $1,624,610 USD (104,881 units) and the yield was improved 20.87%. Show less
-
-
-
Elliott Manufacturing
-
United States
-
Mechanical Or Industrial Engineering
-
1 - 100 Employee
-
Quality Leader
-
Oct 2013 - Aug 2016
Responsibilities: • Quality group leader. • 8D’s Leader (lead 8D's Meetings) • Supplier Quality (in charge of incoming area ) • Quality system coordinator • ISO TS 16949/9001 internal auditor • Conduct PFD, FMEA, Control plans • Manufacturing support at assembly area. • CPK, Capacity and Attributes studies. • Preparation and delivery of PPAP. • Layered audits develop. • Calibration System. Achievements: Leader at the ISO-9001 certification audit & successfully passed, validating the quality management system. Developing and implementing layered audits, we improve the 5S’s of the area, (from a 2.3 score to 5 the maximum 5S’s score). DPPM’s reduction from 2,955 DPPM’s (FY14) to 2,544 DPPM’s in the present. Warranty Expense reduction from 129,594 USD to 63,480 USD in FY14, FY15 with 49,3388 USD and in the present with 22,645 USD. Show less
-
-
-
Federal-Mogul Powertrain
-
United States
-
Motor Vehicle Manufacturing
-
700 & Above Employee
-
Process Engineer
-
Jan 2011 - Aug 2013
Responsibilities: • Develop and re-evaluate the wiper process routings. • Conduct PFD, PFMEA. • Design fixtures. • Work instructions, visual aids, packaging reaction plan. • Cost reduction projects at the packaging area. • PPAP preparation for new projects. • Process routings. • New projects • Lay out • Process connection . Achievements: lead a cost reduction project at the packaging area, increasing the productivity 3% monthly, reducing the ppm’s from 449 to 64. Coordinated and developed process flow diagrams (PFD), PFMEA’s, and control plans for the wipers and packaging process. Show less
-
-
-
Siemens
-
Germany
-
Automation Machinery Manufacturing
-
700 & Above Employee
-
Quality Engineer
-
May 2007 - Dec 2010
Responsibilities: • Molding Quality System transferense ( El Paso –Juarez) • Proof methods, visual aid, quality alerts. • Quality group leader. • Develop the website to improve the organization of documents • Conduct PFD, DFMEA, FMEA, Control plans • Manufacturing engineer support at assembly area. • CPK, Capacity and Attributes studies. • Leader of VSM QA Team • Design fixtures for destructive test. • Develop the measurement system analysis plan. • Preparation and delivery of PPAP. • Layered audits develop • DOE Conducting. Achievements: Successfully performed plant transfer in QA documentation & inspection methods, leadering a VSM QA team that reduced the time for first article process by 30 %. Coordinated and developed process flow diagrams (PFD), PFMEA’s, and control plans for the molding area Lead the RPN’s reduction program from 125 average to 50 average. With the website develop the production operators can get documents easily. Preparation and delivery of PPAP. Developing and implementing layered audits for the molding, fabrication and assembly areas, improving the discipline, minimizing operator’s mistakes, production variation and waste in a 35%. As a member of a DOE team, my responsibility was recollecting the different samples to make the destructive test and record the data for the analysis. Show less
-
-
Education
-
Universidad Autonoma de Chihuahua
Master's degree, Master Degree in Administration -
Universidad Autonoma de Cd. Juarez
Engineer's degree, Industrial Engineering
Community
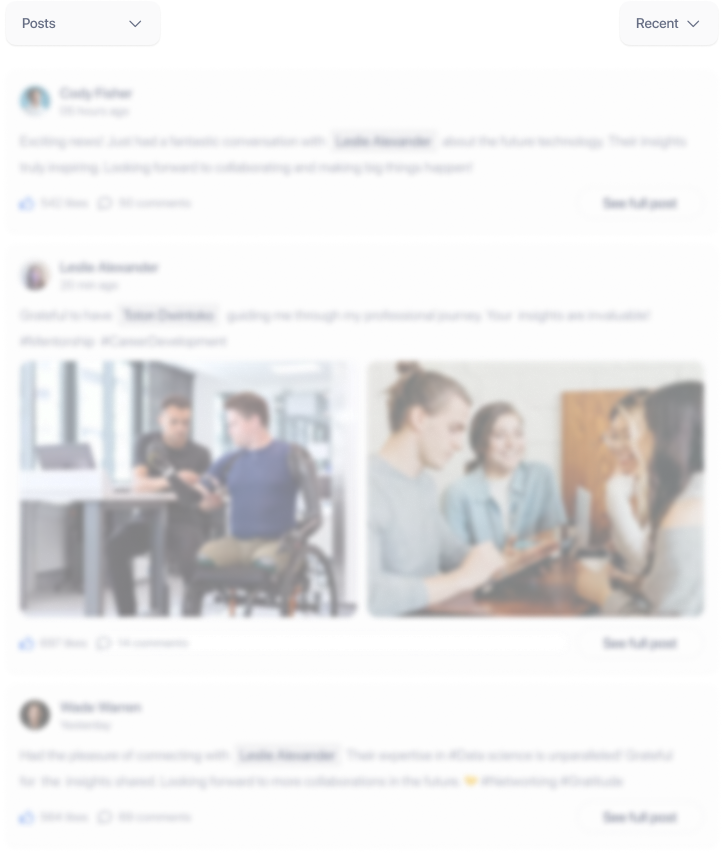