Jonathan Lim
Manager of Procurement at Peerless Coffee & Tea- Claim this Profile
Click to upgrade to our gold package
for the full feature experience.
-
English Native or bilingual proficiency
-
Cantonese Elementary proficiency
-
Mandarin Elementary proficiency
Topline Score
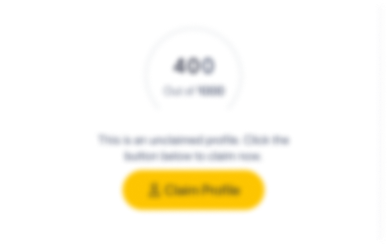
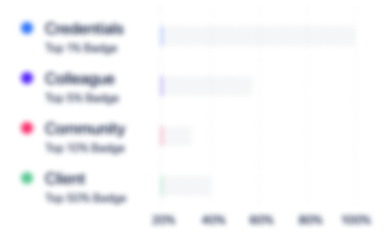
Bio

Jonathan is a determined, dedicated employee. He is no stranger to staying late and working weekends to make sure his work gets done. A real team player. He has passion for whatever he is working on and genuinely cares about his team and the quality of his work. Jonathan is a great addition to any collaborative team.

Jonathan is a very sharp guy. During the couple months that Jonathan interned at Pebble, I found Jonathan a fast learner and could finished any assigned task with ease. Jonathan was a shortstop for the team, in which he had covered planning, program management, quality and even logistics for the team. I feel great and honor to be able to work with him.

Jonathan is a determined, dedicated employee. He is no stranger to staying late and working weekends to make sure his work gets done. A real team player. He has passion for whatever he is working on and genuinely cares about his team and the quality of his work. Jonathan is a great addition to any collaborative team.

Jonathan is a very sharp guy. During the couple months that Jonathan interned at Pebble, I found Jonathan a fast learner and could finished any assigned task with ease. Jonathan was a shortstop for the team, in which he had covered planning, program management, quality and even logistics for the team. I feel great and honor to be able to work with him.

Jonathan is a determined, dedicated employee. He is no stranger to staying late and working weekends to make sure his work gets done. A real team player. He has passion for whatever he is working on and genuinely cares about his team and the quality of his work. Jonathan is a great addition to any collaborative team.

Jonathan is a very sharp guy. During the couple months that Jonathan interned at Pebble, I found Jonathan a fast learner and could finished any assigned task with ease. Jonathan was a shortstop for the team, in which he had covered planning, program management, quality and even logistics for the team. I feel great and honor to be able to work with him.

Jonathan is a determined, dedicated employee. He is no stranger to staying late and working weekends to make sure his work gets done. A real team player. He has passion for whatever he is working on and genuinely cares about his team and the quality of his work. Jonathan is a great addition to any collaborative team.

Jonathan is a very sharp guy. During the couple months that Jonathan interned at Pebble, I found Jonathan a fast learner and could finished any assigned task with ease. Jonathan was a shortstop for the team, in which he had covered planning, program management, quality and even logistics for the team. I feel great and honor to be able to work with him.

Credentials
-
Project Management Foundations: Schedules
LinkedInJul, 2020- Nov, 2024
Experience
-
Peerless Coffee & Tea
-
United States
-
Food and Beverage Services
-
1 - 100 Employee
-
Manager of Procurement
-
Oct 2020 - Present
-
-
-
Beyond Meat
-
United States
-
Food and Beverage Services
-
400 - 500 Employee
-
Supply Chain Planner
-
May 2019 - Jun 2020
- Manage and maintain the MPS (Master Production Schedule) for the Americas and International customers. Managed the production volume increase of over 800% over a period of 10 months. - Materials management and production scheduling across five contract manufacturers representing 70% of the total production capacity. Provide direction to the supply chain team on how to position future supply to ensure proper inventory management. - Expert user of NetSuite ERP system by Oracle. Develop NetSuite logic and process flows with IT team to run the business. Create work orders on NetSuite to drive factory builds to fulfill demand- Work with IT, Finance, Procurement, Logistics, and Engineers to implement a cloud based planning system, Demand Caster, to replace a manual Excel based planning process.- Create analysis reports for material usage, weeks of supply, and material transitions. Present weekly updates to operations team members and management. - Work closely with R&D, Engineers, Procurement, and Project Managers to plan materials for new products- Analyze production schedules and issue Purchase Orders based on materials lead time. Managed material spend from $1.8M/month to $11.5M/month to support production volumes.
-
-
-
Premier Nutrition: The Good Energy People
-
United States
-
Manufacturing
-
100 - 200 Employee
-
Supply Planner
-
Nov 2018 - Apr 2019
- Manage component materials and finished goods supply used in the manufacturing of five products- Maintain open purchase order report and production forecast with suppliers to ensure products meet commit date- Initiate workorders for production builds and create purchase orders in Oracle NetSuite- Fulfill/receive in transfer orders for finished goods- Reconcile monthly inventory reports with suppliers
-
-
-
Amazon Lab126
-
United States
-
Computers and Electronics Manufacturing
-
700 & Above Employee
-
Supply Chain Planning Manager
-
Jul 2017 - Jun 2018
- Managed worldwide buffer inventory for power adapters used across Echo, Fire TV, and Fire Tablet devices- Collaborated with Device Planning Managers to determine buffer based on Production Forecasts and Allocation Plan- Analyzed device production forecasts and buffer reports from factories to ensure lead time can support inventory requirements - Managed NPI programs relating to power adapters and cables accessories.- Collaborate with fulfillment center inventory managers to determine worldwide supply for power adapters- Collaborate with the factories and Materials Managers to determine excess cost for power adapters due to buffer set up and sudden decrease in consumer demand.
-
-
-
Cisco
-
United States
-
Software Development
-
700 & Above Employee
-
Global Supplier Management Intern (Mechanicals and Thermals)
-
May 2016 - Aug 2016
- Validated quarterly pricing of select contract manufactures to ensure compliance with Cisco negotiated costs- Rationalized supply base with commodity managers to identify suppliers for consolidation by summarizing part numbers, demand, and total spend - Utilized Agile (Oracle) and Business Objects (SAP) to compare BOMs of low spend suppliers with preferred suppliers - Analyzed data with commodity managers using advanced Excel features
-
-
-
Cisco
-
United States
-
Software Development
-
700 & Above Employee
-
Global Supplier Management Intern (Semiconductors)
-
May 2015 - Aug 2015
- Recovered over $700,000 in supplier rebates for commodities such as processors and hard drives resulting from price masking activities - Worked with Finance, IT, and Commodity Managers to claim rebates through data mining- Mapped multiple rebate recovery processes to identify areas for improvement
-
-
-
Ingersoll Rand
-
United States
-
Industrial Machinery Manufacturing
-
700 & Above Employee
-
Materials Planning Intern
-
Jan 2015 - Apr 2015
- Materials management for inbound supply to EMEA Distribution Center- Worked with key stakeholders to address supplier delivery issues and expedite materials- Validated Oracle item master supplier details for specific parts and report invalid source information
-
-
-
Pebble Tech
-
United States
-
Computers and Electronics Manufacturing
-
1 - 100 Employee
-
Manufacturing Operations Intern
-
Jun 2014 - Aug 2014
- Managed a project to modify retail packaging to address retail theft. Interact with Engineering, Sales, and Marketing to define project tasks and key milestones- Updated inventory logs from factories to enable better supply demand matching
-
-
Education
-
Arizona State University - W. P. Carey School of Business
Bachelor's degree, Logistics, Materials, and Supply Chain Management
Community
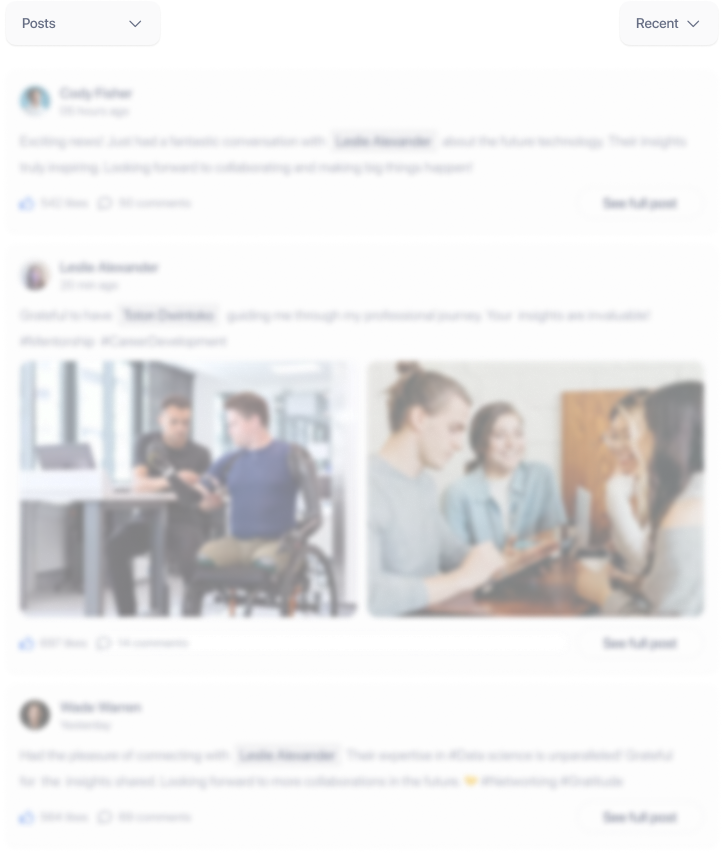