Jonathan Colosimo
Product Development Manager at Dagostino Electronic Services, Inc.- Claim this Profile
Click to upgrade to our gold package
for the full feature experience.
Topline Score
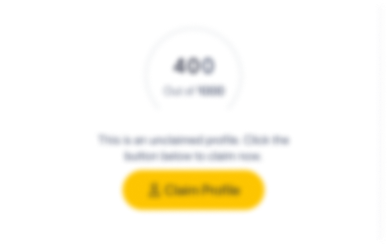
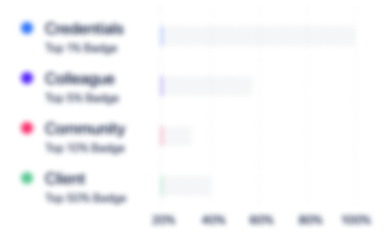
Bio


Credentials
-
Construction Estimating: Specifications and CSI MasterFormat
LinkedInNov, 2021- Oct, 2024
Experience
-
Dagostino Electronic Services, Inc.
-
United States
-
Telecommunications
-
1 - 100 Employee
-
Product Development Manager
-
Jan 2020 - Present
My work with DES is truly the perfect blend of entrepreneurship and innovation to bring Master Systems Integrator solutions to life for clients, aiming to eliminate friction in critical workflows. Along with my primary responsibility of New Products Development, I also manage DES's AI Department, Pittsburgh AI Works. As the New Product Development Manager for DES, my main duty is to drive innovative efforts to fruition across the organization and clients, with specialty focus in AI, IoT/IoE, Industry 4.0, and Continuous Improvement and Quality. This responsibility not only pertains to extending the value of existing partner solutions to our clients, but includes growing our portfolio of product offerings as the technology market continuously evolves. In March of 2019, I co-led the initiative to build and now currently manage the Innovation division, Pittsburgh AI Works, alongside highly accomplished AI and ML professionals to create a consulting and delivery services program to solve complex business problems using the latest AI technologies. Utilizing Design Think Methodology, I coordinate project discovery, testing, and implementation between the PAIW team and the clients to craft end user-oriented solutions to ensure meaningful return on investment. Website: https://www.pghaiworks.com/ Internally at DES, I strategize and manage Digital Transformation efforts aimed to modernizing/migrating core business technologies, infusing automation to reduce mundane and repetitive tasks, and ultimately bridging people, processes, and technology in the enterprise. Along with my responsibilities, I assist Project Managers and Sales Engineers in the design of Structure Cabling, Security, Multimedia, and Networking solutions via AutoCAD. Show less
-
-
-
Tern Water, Inc.
-
United States
-
Utilities
-
Director Of Engineering
-
Apr 2016 - Sep 2019
Tern Water is a current start up company and alumnus of Drexel University's Baiada Institute. Based, Tern has developed itself to become a very well know up and coming company in the Philadelphia Area as well as multiple points along the East Coast. My role in the company revolved around the research and development of the products and technology to integrate into the Internet-of-Things, as part of the services offered by Tern. Being a start up company developing new consumer goods and services, I worked within the means of various patented projects and intellectual properties alongside multiple team members. As the Engineering Director, I oversaw and worked alongside multiple full time and contract based engineers, designers, and developers to create one of a kind products from the ground up, carrying out numerous counts of product testing and customer interviews, as well as design iteration and design for manufacturing with supply chain management in consideration. Along with all of the engineering experience associated with Tern, I have been exposed to a plethora of Entrepreneurship learning experiences, working along side multiple advisers and professionals from both Drexel and outside sources. Through my years with Tern Water, the company has achieved numerous start up awards, grants, and investments in which helped kicked our internal development into high gear, as well as attend and table at multiple expos such as CES 2018 and 2019. In the winter of 2019, we accomplished a successful pre-order campaign for the Smart Faucet. Links: http://www.ternwater.com/ Show less
-
-
-
Henkels & McCoy, Inc.
-
United States
-
Construction
-
700 & Above Employee
-
CIQ Intern
-
Mar 2016 - Sep 2016
Returning for final Co-op cycle at Henkels & McCoy as a Corporate Intern in the Continuous Improvement and Quality department. Main tasks include providing support to multiple regions in several lines of businesses, such as Gas Distribution, Power Transmission, and Pipeline Construction. During the summer, I was relocated to the Central Region in Batavia, IL to provide Quality support to Gas Distribution as well as implement the ToolWatch program into the region to monitor and track tools for calibration purposes. This Continuous Improvement Project derived from the Region's A3 Business Plan, beginning with the Quality Department developing the ToolWatch system to monitor and track calibrated equipment used across the region. With future plans having ToolWatch fall under the Procurement department, I would then spend time with other departments to develop Procedures and Standards of Work to create a sustainable system for the Region to use. Compared to my previous Co-Op with this company, the was more of an administrative role within Continuous Improvement in the company, while being exposed to A3 Business Planning and Execution as well as following Lean Construction mentality. Show less
-
-
-
-
CIQ Intern (QA/QC) - Pipeline Division
-
Apr 2015 - Sep 2015
This was my second Co-op at Drexel University. I worked as a Continuous Improvement and Quality (QA/QC) Intern in the Pipeline Division. Spent three months in New Jersey performing the Quality Management tasks of pipeline construction for Williams, and three months performing Quality Management for 1 project in Harrisburg for Spectra, 1 project in Butler County, PA for Columbia, 1 project in Washington County, PA for Columbia, and 2 projects in Waynesburg, PA for Spectra and Columbia. Tasks include but are not limited to conducting tests, inspections, and audits of the work being done by H&M personnel, tracking welder performance along with go back costs, responding to nonconforming issues, and working with the gas company's inspectors and engineers to ensure the work being done meets expectations as well as mitigating risk. Along with what is listed above, I look for ways to improve how Quality Management is applied to H&Ms production. Use of IPads is now utilized in the field so on site reports can be made and submitted. Improving the process so it can be applied to all projects and is easy to learn is the end goal for me at my time at Henkels and McCoy. Show less
-
-
-
Dietz and Watson
-
United States
-
Food and Beverage Manufacturing
-
300 - 400 Employee
-
Project Engineer
-
Mar 2014 - Oct 2014
Assisted Plant Engineers in project engineering with energy cost reduction projects and improving plant equipment. Worked on site plans to set up for an expansion plan along with the research and development of a suitable cogeneration system to power the plant. Experienced working with other environmentally friendly projects pertaining to the future of the plant as well. Gathered and processed data from plant production and worked with maintenance department on preventative maintenance plans to upkeep production rates. Used Excel, SolidWorks, AutoCAD, and 3D printing for projects. Show less
-
-
-
-
Management
-
2008 - Jan 2013
Beginning with my Grandfather George Key in 1965, our family Sunoco franchise has been one of the top performing franchises in the Pittsburgh area, as well as recently achieving awards for in store sales and performance, which is recognized by the corporate office. George entered the business along with my father in 1970 working in service stations where they would own several locations over the past 45 years. As George began to take a step back from the business, my mother, Gigi, would step up with my father and would continue to grow their Sunoco franchise as well as expand to now owning a Sunoco and and Exxon On the Go Market in Dormont, each located within a quarter mile of each other. These businesses have led to a lot of success as well as developing interpersonal relationships in the town of Dormont, right outside of the city of Pittsburgh, making both locations very depended on by the loyal customers in the area. My experience here began with me growing up in a doorway bouncer as a baby in the store while my parents worked hard every day to grow their business to what it is today. As I got older, I found myself more and more involved, whether it was self maintenance carried out through my father or even meeting and working with representatives, just to provide assistance when needed and grow my experience portfolio. As I entered my high school career, I began full-time employment, starting as a cashier where they would develop me to a manager role by the time of my Junior and Senior year, exposing me to all the backend management revolving around the development of the business. To this day, I stay involved in the stores as much as possible granted my college studies are in Philadelphia. Between attending trade shows, meetings, and special topic seminars, I look to provide consulting services to my parents where I can assist them in the trends of merchandising to the consumer market as it is today. Show less
-
-
Education
-
Drexel University
Bachelor of Science (BS), Mechanical Engineering -
Peters Township High School
Community
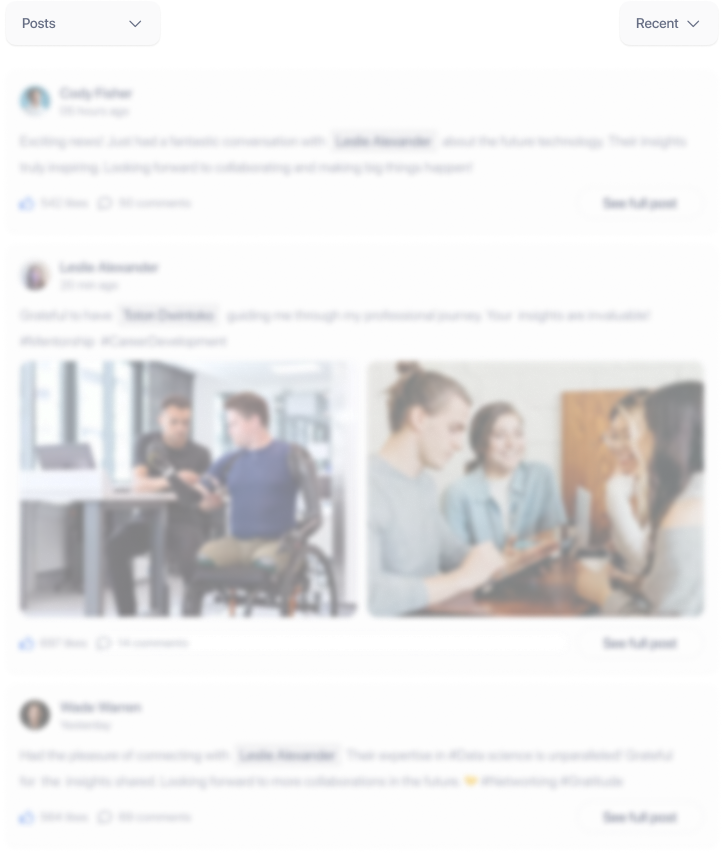