Jonathan Bain, P. Eng
Manager, Customer Success at Qube Technologies- Claim this Profile
Click to upgrade to our gold package
for the full feature experience.
-
French -
Topline Score
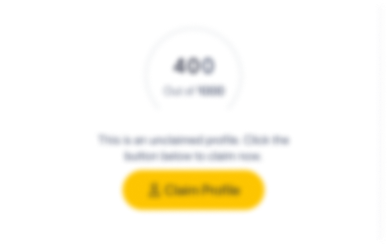
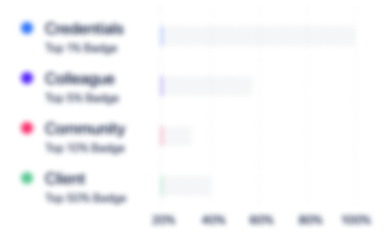
Bio
0
/5.0 / Based on 0 ratingsFilter reviews by:
Experience
-
Qube Technologies
-
India
-
Information Technology & Services
-
1 - 100 Employee
-
Manager, Customer Success
-
May 2023 - Present
-
-
-
Metro Vancouver
-
Canada
-
Government Administration
-
700 & Above Employee
-
Senior Project Engineer - Maintenance and Business Support
-
Mar 2022 - May 2023
Support day to day operations and maintenance with technical support. Manage incident investigations for equipment failure and utilize 5-why and causal tree analysis to identify root causes. Manage minor capital projects program and budget. Leverage continuous improvement and lean management principles to identify and implement solutions for inefficient business processes within the organization. Support day to day operations and maintenance with technical support. Manage incident investigations for equipment failure and utilize 5-why and causal tree analysis to identify root causes. Manage minor capital projects program and budget. Leverage continuous improvement and lean management principles to identify and implement solutions for inefficient business processes within the organization.
-
-
-
Parkland Refining Ltd.
-
Canada
-
Chemical Manufacturing
-
1 - 100 Employee
-
Operations Area Lead - Polymerization, Alkylation and Sulfur Recovery
-
Oct 2020 - Mar 2022
Responsible for managing a multi-disciplinary team to maintain day to day operation for 3 units in the refinery. Responsibilities included setting daily unit priorities for the team, supporting unit troubleshooting, determining yearly unit objectives, managing unit budgets, providing direction and feedback to team members and ensuring work is executed in a safe and timely manner. Project 1 - Management of Severe Fouling of Sour Water Stripping SystemThe refinery sour water treatment system experienced a sudden and severe increase in fouling that required the unit to be shut down every 4 months for cleaning (previous run length was 5 years). Created and managed a support team to brainstorm, develop and prioritize key projects and investigations to resolve the issue and determine root cause.Successfully installed spare critical equipment and completed a novel on-the-run chemical cleaning of the unit which increased unit availability by 10% and reduced the length of cleaning outages by 60%. Project 2 - Redesign of Management of Change Workflow ProcessWorked on a team of four to support redesigning of the management of change (MOC) process for the refinery to eliminate low value work and overloading of resources.Worked with key stakeholders of the MOC process to develop an “ideal” work flow and completed a gap analysis by comparing to the actual work flow to develop areas of focus and project roadmap. Implemented a separate, simplified MOC process to streamline execution of small, low-risk changes and developed a new review and prioritization process to rank complex changes and limit the total number of active projects to prevent resource overload. Show less
-
-
Process Engineer: Fluidized Catalytic Cracker and Crude Unit
-
Feb 2019 - Oct 2020
Provided day to day technical recommendations to ensure the refinery met the short, medium and long term business plan for assigned units. Typical deliverables included writing technical reports, evaluating 3rd party engineering plans, reviewing/managing internal and external project deliverables, owning the management of change process and planning and executing turnarounds.Project 1 - Fluidized Catalytic Cracker Turnaround Unit Process LeadServed as lead process engineer for the 2020 FCC major unit turnaround.Work entailed planning and ordering hardware for planned repairs, updating start-up and shutdown procedures, inspecting the internals of all major equipment in event, managing and inspecting the execution of all process related work and repairs and developing a final report with all findings and work completed in event.Project 2 - Process Engineering Team Time Allocation Review and OptimizationIdentified the need for a time allocation review as the team was overloaded with base load work and was unable to focus on high value work.Worked with a senior process engineer to develop a time tracker for the team to use over multiple months to gather sufficient data to analyze time allocation across various work categories.Data analysis found base load activities accounted for 90-100% of weekly hours and key activities such as process optimization (high value) received little to no allocation (<5%). The team was able to eliminate several low value recurring meetings and monthly reports which freed up approximately 10% of time for the team to focus on on high value work. Show less
-
-
-
Solaris MCI
-
Canada
-
Professional Services
-
100 - 200 Employee
-
Process Engineer
-
Jan 2018 - Jan 2019
Worked closely in multi-discipline engineering teams and provided process engineering expertise to prepare conceptual designs, reports and proposals for clients on large capital projects. Served as both intermediate and lead process engineer depending on project scope and requirements. Project 1 - Three Well Tie-in and Dehydration Expansion Served as joint-lead process engineer for front end assessment and detailed engineering design for a three well tie-in and a 100 MMSCFD dehydration facility expansion. Identified multiple pieces of existing equipment in the field that could be used in place of purchasing new equipment to save on capital. Worked with one other process engineer and limited resources to complete full design. Final design utilized both existing equipment and new equipment which maximized production and minimized capital expenditure for the client. Show less
-
-
-
Shell
-
Oil and Gas
-
1 - 100 Employee
-
Operations Engineer
-
Jan 2013 - Jun 2017
Provided day to day, multi-discipline technical support to operations and identified and managed improvement projects across multiple gas plants. During final two years, acted as technical mentor for junior engineers and final design reviewer and engineering stamp for management of change design packages (MOCs). Project 1 - Montney Gas Plant Pressure Safety Valve and Flare System Upgrades Managed a budget of $2M and multi-disciplinary support teams to assess and upgrade flare systems across 3 gas plants. Identified undersized equipment and replaced 50 pressure safety valves, multiple discharge headers and a full flare stack. Worked within a short timeline of 6 months in order to execute during scheduled plant turnaround. All upgrades were installed on schedule and with minimal deferment. Project 2 - Montney Gas Plant Engineering Turnaround Lead Managed an engineering projects turnaround budget of $4M that included 20 multi-disciplinary projects (MOCs) and 3 operations engineers across 3 gas plants. Team worked together to stay on schedule and deliver all projects on budget and during the turnaround. Worked within a short timeline of 6 months and with minimal technical support to meet turnaround dates. Completion of projects made all 3 plants code compliant for process safety and increased yearly revenues by $1M. Project 3 - Saturn Gas Plant Debottlenecking Study Identified opportunity and conducted simulations and calculations for a plantwide debottlenecking study of a 200 MMSCFD gas plant. Increased nameplate capacity from 200 to 216 MMSCFD with future improvements planned. Managed a thorough field sampling plan with operations to ensure accurate data was obtained. Yearly revenues were increased by $5-10M and additional debottlenecking studies for other plants were requested. Show less
-
-
Education
-
University of Waterloo
Applied Science, Chemical Engineering
Community
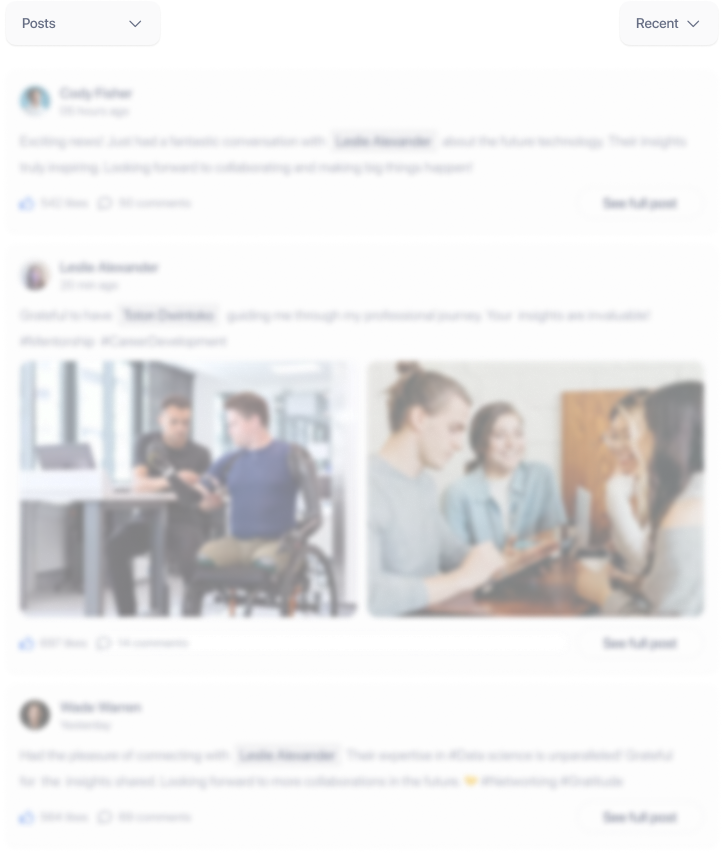