John Naughton
Chief Operating Officer at Energy Federation- Claim this Profile
Click to upgrade to our gold package
for the full feature experience.
Topline Score
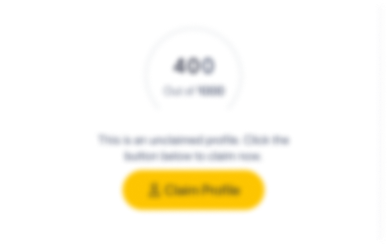
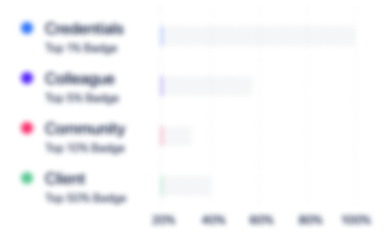
Bio

Kent Kise
I had the privilege of working for John at Keurig Green Mountain. John is one of those rare individuals who not only can create a rock-solid organizational vision but provides the key strategic direction to deliver outstanding results within a complex, global footprint. His management style is open, participative, and energetic as he routinely leads by example. He is a visionary leader in the quality management arena and routinely provides concise, beneficial guidance to his staff and peers. John's key strengths are his ability to build a team, gain alignment, and provide guidance towards defined strategic goals for the organization. His wide knowledge of enterprise management significantly raised the bar of excellence at Keurig and through his persistence, the Keurig quality structure grew into a robust scalable system. John is an individual you want on your team when major enterprise-wide improvements in the quality system are mission critical. He has my unreserved recommendation.

Bob Whipple MBA CPTD
I worked with John for a couple years, and I found him to be a great asset at strategic thinking and supply chain management. John is personable and highly capable of managing teams. His leadership instincts are rock solid, and he is able to work well with people at all levels. Any organization would benefit greatly from having John on their management team.

Kent Kise
I had the privilege of working for John at Keurig Green Mountain. John is one of those rare individuals who not only can create a rock-solid organizational vision but provides the key strategic direction to deliver outstanding results within a complex, global footprint. His management style is open, participative, and energetic as he routinely leads by example. He is a visionary leader in the quality management arena and routinely provides concise, beneficial guidance to his staff and peers. John's key strengths are his ability to build a team, gain alignment, and provide guidance towards defined strategic goals for the organization. His wide knowledge of enterprise management significantly raised the bar of excellence at Keurig and through his persistence, the Keurig quality structure grew into a robust scalable system. John is an individual you want on your team when major enterprise-wide improvements in the quality system are mission critical. He has my unreserved recommendation.

Bob Whipple MBA CPTD
I worked with John for a couple years, and I found him to be a great asset at strategic thinking and supply chain management. John is personable and highly capable of managing teams. His leadership instincts are rock solid, and he is able to work well with people at all levels. Any organization would benefit greatly from having John on their management team.

Kent Kise
I had the privilege of working for John at Keurig Green Mountain. John is one of those rare individuals who not only can create a rock-solid organizational vision but provides the key strategic direction to deliver outstanding results within a complex, global footprint. His management style is open, participative, and energetic as he routinely leads by example. He is a visionary leader in the quality management arena and routinely provides concise, beneficial guidance to his staff and peers. John's key strengths are his ability to build a team, gain alignment, and provide guidance towards defined strategic goals for the organization. His wide knowledge of enterprise management significantly raised the bar of excellence at Keurig and through his persistence, the Keurig quality structure grew into a robust scalable system. John is an individual you want on your team when major enterprise-wide improvements in the quality system are mission critical. He has my unreserved recommendation.

Bob Whipple MBA CPTD
I worked with John for a couple years, and I found him to be a great asset at strategic thinking and supply chain management. John is personable and highly capable of managing teams. His leadership instincts are rock solid, and he is able to work well with people at all levels. Any organization would benefit greatly from having John on their management team.

Kent Kise
I had the privilege of working for John at Keurig Green Mountain. John is one of those rare individuals who not only can create a rock-solid organizational vision but provides the key strategic direction to deliver outstanding results within a complex, global footprint. His management style is open, participative, and energetic as he routinely leads by example. He is a visionary leader in the quality management arena and routinely provides concise, beneficial guidance to his staff and peers. John's key strengths are his ability to build a team, gain alignment, and provide guidance towards defined strategic goals for the organization. His wide knowledge of enterprise management significantly raised the bar of excellence at Keurig and through his persistence, the Keurig quality structure grew into a robust scalable system. John is an individual you want on your team when major enterprise-wide improvements in the quality system are mission critical. He has my unreserved recommendation.

Bob Whipple MBA CPTD
I worked with John for a couple years, and I found him to be a great asset at strategic thinking and supply chain management. John is personable and highly capable of managing teams. His leadership instincts are rock solid, and he is able to work well with people at all levels. Any organization would benefit greatly from having John on their management team.

Credentials
-
Six Sigma Blackbelt
EK Company
Experience
-
Energy Federation
-
United States
-
Renewable Energy Semiconductor Manufacturing
-
1 - 100 Employee
-
Chief Operating Officer
-
Jan 2019 - Present
• Drove process improvements for incentive management business, conducted value-stream mapping, waste elimination, and training yielding $1M cost reduction while improving customer experience. • Interim CIO (90 days) managed developers plus contractors with overall $6.7M budget, deploying advanced Agile practices, structured QA and release management, insourced work driving business savings and cost avoidance. • Expanded C-Suite as COO to drive strategy, performance, and communication. Responsible for Supply Chain, Procurement, Logistics, Customer Experience, and Sales Operations. Created Procurement Transformation achieving $4.9M annualized savings.
-
-
-
Keurig Dr Pepper Inc.
-
United States
-
Food and Beverage Services
-
700 & Above Employee
-
Senior Vice President - Quality Engineering & Appliance Manufacturing
-
Sep 2013 - Sep 2018
Provided strategic leadership of Quality Engineering & Appliance Manufacturing organization, driving enterprise quality transformation to deliver product, customer, and operational improvement. Define and execute on strategies for meeting operational demands while simultaneously improving customer satisfaction and retention. Scope encompassed Lean Six Sigma, Beverage QA/ Food Safety, Appliance QA/Test, Manufacturing Engineering, Asia Operations, and Supplier Quality. • Recruited executive-level talent to scale-up the organization and support the rapid expansion of workflow; engaged 3 contract manufacturers to better develop, build, test, and delivery of 8.5M units/year. • Co-created a formal Stage Gate Development Process and Agile methodology designed to drive improvements to speed, quality, and efficiency. With focus on early stage verification process, and lean development, delivered a 200% improvement in appliance consumer return rate and achieved industry benchmark for reliability.• Created Lean Six Sigma platform with internal curriculum and certification, qualifying 128 practitioners to support $100M+ in productivity and $12M warranty reserve savings. • Established supplier quality engineering function to standardize process capability and control plans across critical sub-systems/components; eliminated sub-tier excursions and delivered 67% DPPM improvement over recent 12-month span. • Improved internal audit process, intervention training, and engineering best practices across 7 plant locations, delivering a 300% improvement in consumer complaints and established the industry benchmark for complaints per billion units sold. • Supported our Supply Chain Transformation Vision and implementation plan including automation, SCADA, Vision Systems, WIP management, and robotics, which will result in dramatic improvement in Unit Cost, Safety, and Quality.
-
-
-
Impactiva
-
China
-
Retail Apparel and Fashion
-
200 - 300 Employee
-
Advisory Board
-
2013 - 2016
-
-
-
Nokia
-
Finland
-
Telecommunications
-
700 & Above Employee
-
Vice President - Smart Devices Quality
-
2011 - 2013
Directed Global Windows Phone Quality organization, leading the development, management, and improvement of all related operations, including product development testing, validation of hardware, applications & system software, and technology modules. Built partnership with Microsoft as the OS provider and to lead the adoption of testing methods, including ship-room error management, SQ integration and transit, MTBF lab set-up, Agile test-led development. • Led cultural change, focused on quality improvements; restructured the development cycle to optimize the testing process to support lean development, SQ maturity at launch, and supply chain efficiency. • Achieved No. 1 consumer quality ranking and improved warranties 50% by creating quality improvement program.• Improved claim rate by supporting launch of 4 global products, attacking early issues with rapid field capture and stabilizing field customer quality.
-
-
-
Dell Technologies
-
United States
-
IT Services and IT Consulting
-
700 & Above Employee
-
Vice President - Consumer Product Group Quality
-
2008 - 2011
Promoted multiple times throughout tenure, taking over leadership roles focused on quality engineering, supply chain management operations, and product development. In this role, charged with leading global quality improvement program and product performance driving Net Promoter Score (NPS) results. Introduced new processes and standards for supporting quality product development.• Converted focus from classic lagging indicators (returns/warranty) to real-time, leading performance measures (MTBF, CAPA backlog, ORT) helping galvanize the development and operations teams to deliver more reliable products.• Improving DFx, design rigor, and sub-tier suppliers by integrating customer feedback loop into business planning process and conducting Lean development Kaizen process.• Helped shift product development and fulfillment to ODM partners, improving time to quality, and enhancing ownership in the sustaining phase, improving CAPA cycle-time by 50%. • Improved quality assurance and reliability by assigning dedicated staff in four international development centers to address risks presented from outsourcing and expanding into retail channel sales. • Maximized customer loyalty by refining quality measures with balance of warranty cost and customer voice. • Avoided $25 million in warranty costs and achieved industry-leading 4.5-star user rating.
-
-
Vice President - Global Operations & Technology
-
2007 - 2008
Selected to co-lead the development of Dell's Global Supply Chain hub in Singapore.
-
-
Vice President - Supplier Engineering/Quality
-
2003 - 2007
-
-
Director - EMEA Quality/Engineering
-
2000 - 2003
-
-
Education
-
Clarkson University
BS, Mechanical Engineering -
Northwestern University - Kellogg School of Management
EDP, Business
Community
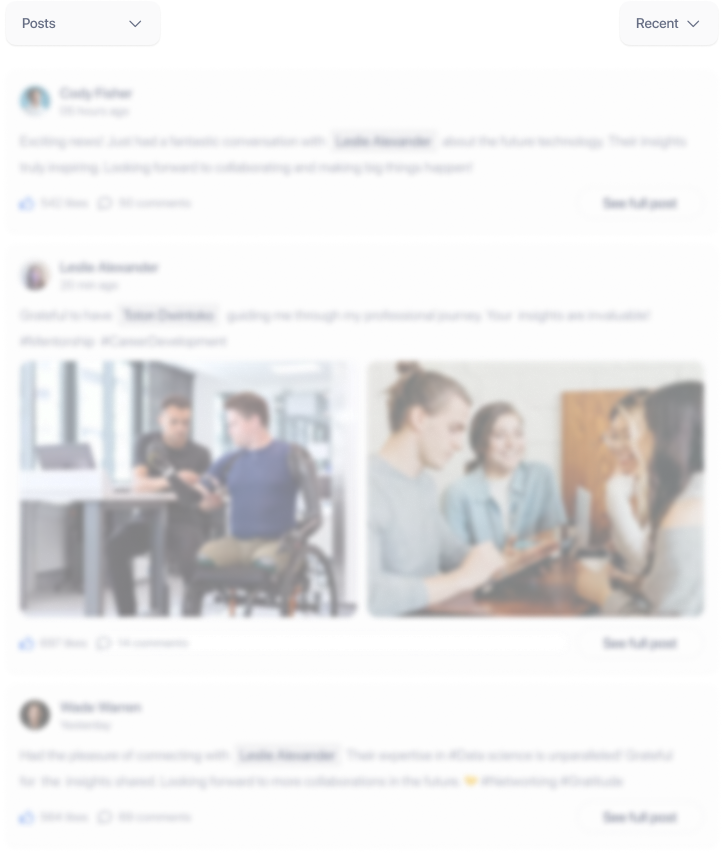