John Yang
Global CQE manager at SUNTAK TECHNOLOGY LIMITED- Claim this Profile
Click to upgrade to our gold package
for the full feature experience.
Topline Score
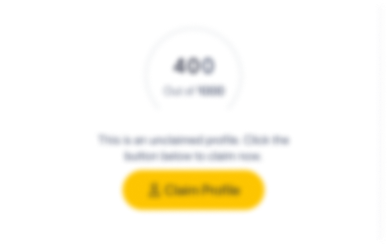
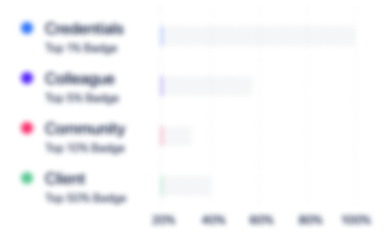
Bio


Experience
-
SUNTAK TECHNOLOGY LIMITED
-
China
-
Appliances, Electrical, and Electronics Manufacturing
-
1 - 100 Employee
-
Global CQE manager
-
Aug 2019 - Present
-
-
-
Compeq Manufacturing
-
Appliances, Electrical, and Electronics Manufacturing
-
1 - 100 Employee
-
Project Manager
-
Sep 2016 - Jul 2019
Lead the NPI team to handle new FPCA programs, from engineering build, ramp-up to MP:1. Coordinate the quotation from raw material cost, panel utilization, tooling design, estimated product yield, etc. to lower the cost to the minimum;2. Review customer design, combining with process capability, come up with the optimal design proposals from the aspects of better quality/yield and lower cost;3. Coordinate the raw material procurement, make sure the MIH date can fully meet the product delivery schedule;4. Work with the process engineer and customer DFM DRI to set up the process with the optimal process parameters; 5. Manufacturing process follow up and delivery schedule feedback to customer;6. Visit customer PD/PE, get to know customer technology roadmap, improve product design and process capability to prepare for the incoming new programs in advance. Show less
-
-
Quality Manager
-
Jan 2015 - Aug 2016
Manage the quality department of the FPC/SMT factory, supervise the daily quality activities:1. IQC/SQA: Assessment and qualification of suppliers or assembly subcontractors; Set up IQC quality criteria for material incoming quality control; Drive suppliers for continuous improvement; Trouble shooting and supervise suppliers to solve quality issues in a timely manner; Supplier scorecard management.2. IPQC: Tooling/fixture buy-off to make sure tooling/fixture are well designed and processed; First article inspection to make sure product meets required quality standard; In-line audit/sampling check to make sure processes are operating within control; Process/product excursion handling, lower the affected quantity, drive for improvements; Daily yield review and drive yield for continuous improvement.3. OQC: Follow the quality standards (SIP/SOP) to do the outgoing quality control; Set up inspection frequency based on AQL sampling plan; Perform OBA before shipment.4. CQE: Align the quality criteria with customers, set up SIP/SOP; Set up the working channel between customers and factory, drive factory to solve customer complains timely; Lead the Complains Reduction Program: drive factory for continuous improvement; Coordinate customer Audit/Visit/Qualification; Lead the FA and 8D activities unfolding and 8D report reply for the returned failure samples; Lead the correlation activities between customer and factory; Assist customer in the resolution of customer caused issues; Share key lesson learns with factory and apply them from the aspects of design, process and quality; Work closely with customer, gather the key information and translate for better FPCA design and quality; Own the scorecards of the assigned customers; 5. Laboratory: Align with customer documents and IPC standard, create and define test SOP for each test item; Oversee daily laboratory test activities, provide accurate data in a timely manner. Show less
-
-
-
Foxconn
-
Appliances, Electrical, and Electronics Manufacturing
-
700 & Above Employee
-
Quality Engineer
-
Aug 2009 - Dec 2014
Manage the customer quality activities on the Apple iPhone/iPad/Mac FPCA (Sensor, Dock, Button, Upper antenna, Lower antenna, GPS antenna, Wifi antenna, etc.): 1. Align the quality criteria with customers (Apple, CM Foxconn/Pegatron/QSMC), set up SIP/SOP for the quality activities in the factory; 2. Set up the working channels between customers and factory, drive factory to solve customer complains timely, make the cost to the minimum; 3. Lead the Complains Reduction Program: drive factory for continuous improvement, establish and maintain close quality interface relationships with customers, to reduce customer complains and save cost; 4. Coordinate customer Audit/Visit/qualification; 5. Failure analysis with the customer returned samples, lead the 8D activities unfolding and 8D report reply; 6. Lead the correlation activities between customer and factory in terms of dimension measurement, functional test, etc; 7. Assist the customer in the resolution of customer caused issues (e.g. ESD/EOS protection, assembly procedures, etc), joint effort of customer production line assessment; 8. Share key lesson learns with factory and apply them from the aspects of design, process and quality; 9. Work closely with customer PE/PD, gather the key information about customer product/process applications to translate for better FPCA design and quality; 10. Own the scorecards of the assigned customers, ensure proper actions follow up to improve the metrics and improve the customer perception. Show less
-
-
Education
-
Henan University of Science and Technology
Bachelor's degree, English
Community
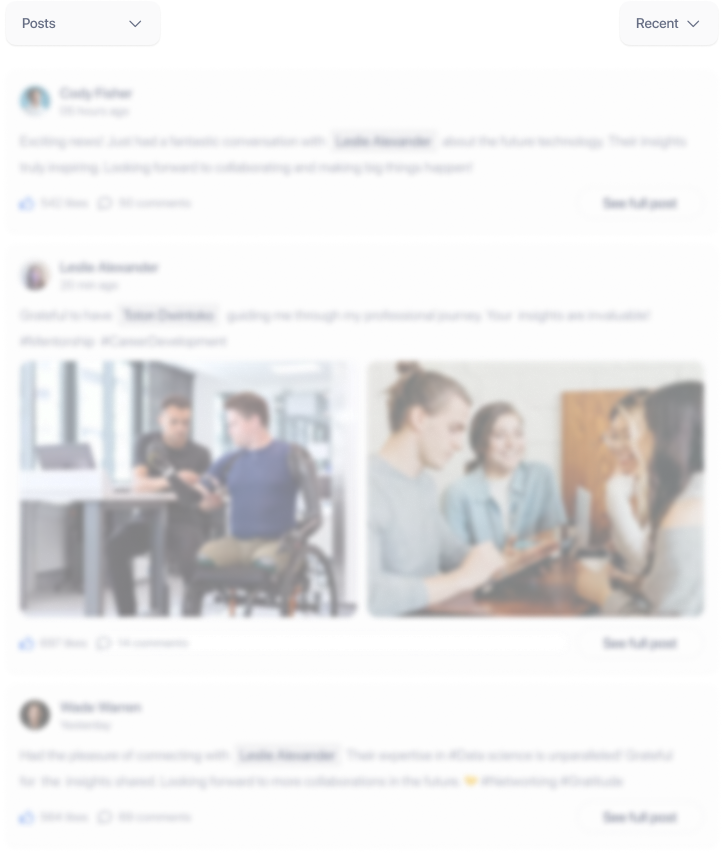