john stenning
Skilled bodymaker 5000 fitter at CarnaudMetalbox Engineering Limited- Claim this Profile
Click to upgrade to our gold package
for the full feature experience.
Topline Score
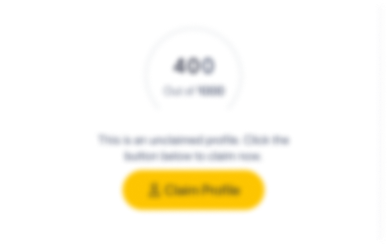
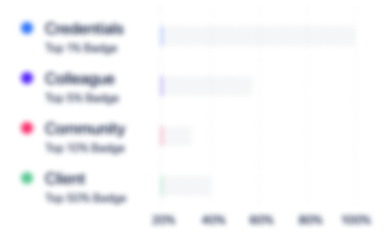
Bio

William Pearson
During John's time working for CMB he was a well respected member of his team. He was one to push himself and wanted to get stuck into any new challenge. I wish John the best of luck in his next job role.

David Beaver
John is a very skilled and knowledgeable engineer with years of experience yet isn't afraid to ask questions if unsure of the task in hand. He can be relied upon as an individual and also as part of a team. His knowledge is such that he was often tasked with mentoring apprentices. All in all a very likeable character with a pleasant disposition. I would have no qualms in recommending John to any future prospective employer.

William Pearson
During John's time working for CMB he was a well respected member of his team. He was one to push himself and wanted to get stuck into any new challenge. I wish John the best of luck in his next job role.

David Beaver
John is a very skilled and knowledgeable engineer with years of experience yet isn't afraid to ask questions if unsure of the task in hand. He can be relied upon as an individual and also as part of a team. His knowledge is such that he was often tasked with mentoring apprentices. All in all a very likeable character with a pleasant disposition. I would have no qualms in recommending John to any future prospective employer.

William Pearson
During John's time working for CMB he was a well respected member of his team. He was one to push himself and wanted to get stuck into any new challenge. I wish John the best of luck in his next job role.

David Beaver
John is a very skilled and knowledgeable engineer with years of experience yet isn't afraid to ask questions if unsure of the task in hand. He can be relied upon as an individual and also as part of a team. His knowledge is such that he was often tasked with mentoring apprentices. All in all a very likeable character with a pleasant disposition. I would have no qualms in recommending John to any future prospective employer.

William Pearson
During John's time working for CMB he was a well respected member of his team. He was one to push himself and wanted to get stuck into any new challenge. I wish John the best of luck in his next job role.

David Beaver
John is a very skilled and knowledgeable engineer with years of experience yet isn't afraid to ask questions if unsure of the task in hand. He can be relied upon as an individual and also as part of a team. His knowledge is such that he was often tasked with mentoring apprentices. All in all a very likeable character with a pleasant disposition. I would have no qualms in recommending John to any future prospective employer.

Experience
-
CarnaudMetalbox Engineering Limited
-
United Kingdom
-
Machinery Manufacturing
-
100 - 200 Employee
-
Skilled bodymaker 5000 fitter
-
Oct 2021 - Present
Skilled fitter building the bodymaker 5000 canning machine. Leveling entire machine using Engineer levels then progressing to adding primary & secondary bulkheads scraping flat where necessary & using DTI to clock up to precise tolerances. Fitting of all parts including, fly wheel, gear boxes, prop shaft, yoke, ram housing, slides, guarding, sump, dome door, cradle, tool pack, all fittings, coolant & oil pipes. Connection of all pneumatic pipes to fittings. On completion of machine then connection of oil hoses to the power pack to maintain correct oil temperature & filtration. Coolant filling of the sump & attachment of the cooler to maintain correct temperature & filtration. Running machine to complete 20 hr checks. All work throughout build from start to finish is checked & signed off by the inspection team all of which is logged. Machine is then ready to hand over to the setting team to can off. Show less
-
-
-
HARRISON SPINKS BEDS LTD
-
Furniture and Home Furnishings Manufacturing
-
1 - 100 Employee
-
Research And Development Engineer
-
Jan 2011 - Oct 2021
Research & Development innovation of mattress core units, supplied to leading suppliers. worked within a skilled team of Engineers building production machines. Fitted components that are required from pneumatics, motors, shafts to bearings. also machining parts as & when required. On completion of the machine, built within the required time frame, set up the spring making coilers, tested & ran machines to ensure product meet specifications required & ready to go into production. Research & Development innovation of mattress core units, supplied to leading suppliers. worked within a skilled team of Engineers building production machines. Fitted components that are required from pneumatics, motors, shafts to bearings. also machining parts as & when required. On completion of the machine, built within the required time frame, set up the spring making coilers, tested & ran machines to ensure product meet specifications required & ready to go into production.
-
-
-
ASHTON TOOLS LIMITED
-
United Kingdom
-
Industrial Machinery Manufacturing
-
1 - 100 Employee
-
Tool and Cutter Grinder
-
Apr 2007 - Jan 2011
Manufactured HSS and carbide cutters and specialist cutting equipment. Brazing of carbide blanks to various steel cutter bodies that I would machine using the conventional centre lathe & milling machines. Grinding of cutter body shafts using the conventional cylindrical grinding machine between centres. Operating the manual tool & cutter grinder to produce the finished product to the precise tolerances required from engineering drawings. Dipped in hot wax & boxed ready for customer. Manufactured HSS and carbide cutters and specialist cutting equipment. Brazing of carbide blanks to various steel cutter bodies that I would machine using the conventional centre lathe & milling machines. Grinding of cutter body shafts using the conventional cylindrical grinding machine between centres. Operating the manual tool & cutter grinder to produce the finished product to the precise tolerances required from engineering drawings. Dipped in hot wax & boxed ready for customer.
-
-
-
SANDERSON PRECISION ENGINEERING LIMITED
-
United Kingdom
-
Mechanical Or Industrial Engineering
-
Centre lathe turner
-
Jan 2007 - Apr 2007
Produced components using the centre lathe & conventional milling machine for a wide range of customers requirements. Fitting of various machined components to complete full assembly. Reading & interpret drawings & on occasions communicating with customers for their direct input with requirements. Working to tight tolerances & produced high quality work having a good eye for detail. Produced components using the centre lathe & conventional milling machine for a wide range of customers requirements. Fitting of various machined components to complete full assembly. Reading & interpret drawings & on occasions communicating with customers for their direct input with requirements. Working to tight tolerances & produced high quality work having a good eye for detail.
-
-
-
Jay-Be beds
-
Dewsbury, England, United Kingdom
-
Research And Development Engineer
-
Jul 2005 - Jan 2007
Worked within a skilled team involved with the design & manufacture of jigs & fixtures for bedroom furniture. Made prototype steel structured beds to customer requirements. Machined components on lathes & milling machines to produce welding fixtures for production of steel beds. Manufacturing punch head machines for square and tubular beds. Fitting of hydraulics to required machines for operations. Prepared resin prototypes to produce mould for producing castings for steel beds. Precise machining of produced castings ready for aluminium pouring withing the foundry. Following instruction & interpret drawings for products produced & on regular occasions designing & producing sketches to work from. Show less
-
-
-
Bray burners ltd
-
Leeds, England, United Kingdom
-
Tool & Die Specialist
-
Jun 1990 - Jun 2005
Bray Burners was the start of my Engineering career where I served my 4 year City & Guilds apprenticeship. I went on to learn in depth the whole process of Tool & Die making & specialising & utilising all of the conventional machines to produce the required parts to make up the press tool sets. Involved in the production of precise progession tool & Die sets, fixtures for the production of industrial & domestic gas burners. Working to very close tolerances, visualisation of product & determine materials required, machines to use & fitting of completed components. Liaised with colleagues, engineere & management. After becoming fully qualified I went on to training new apprentices within the Tool Room helping them develop there hand & machining skills, along with their current college training. Machines used within the production of the tool & Die sets included, Jig boring, jig grinding, cylindrical grinding, milling, turning, Sodik EDM machine for spark eroding for production of punch holders & stripper plates. Tool & cutter grinding, pedestal drilling, offhand grinder, lifting crane. Hardening of our own materials, hardness testing on the vickers hardness testing machine. Show less
-
-
Education
-
Leeds college of technology (kitson College)
4 year apprenticeship, Mechanical Engineering
Community
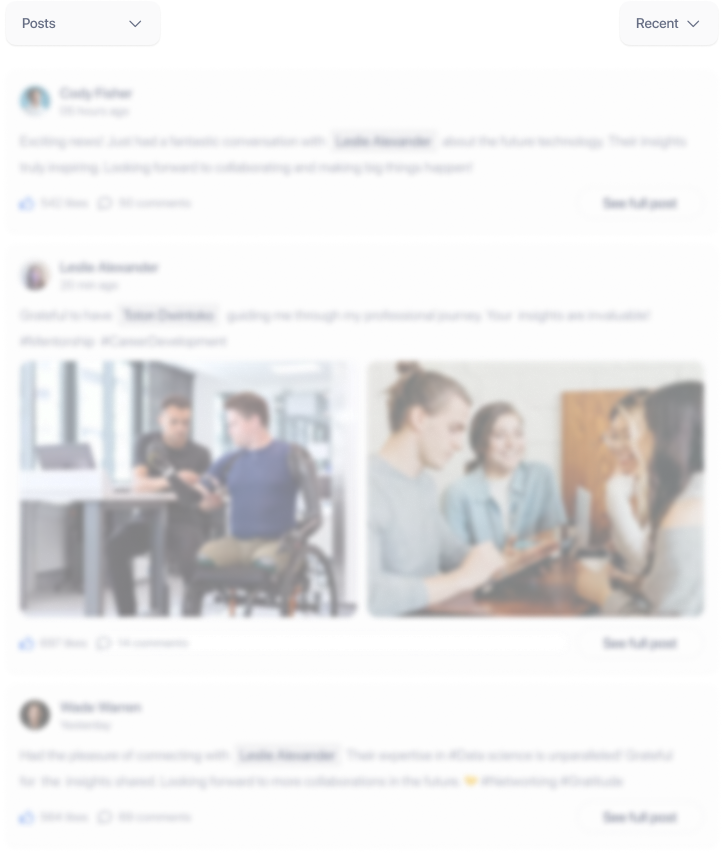