John Pasley
Facility Assessor at ISES Corporation- Claim this Profile
Click to upgrade to our gold package
for the full feature experience.
Topline Score
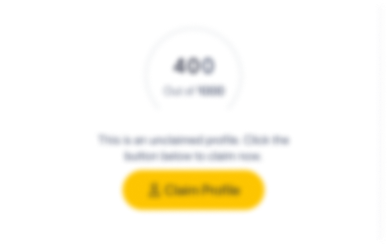
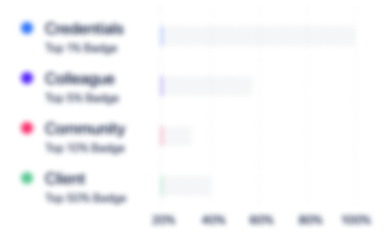
Bio


Experience
-
ISES Corporation
-
United States
-
Facilities Services
-
1 - 100 Employee
-
Facility Assessor
-
Sep 2019 - Present
-
-
-
Owens Corning
-
United States
-
Wholesale Building Materials
-
700 & Above Employee
-
Maintenance Planner
-
Dec 2017 - Aug 2019
• Work with Maintenance Team to ensure production and facility equipment maintained to high standard of reliability.• Encouraged and supported all maintenance technicians and production machine operators to assist in accomplishing their goals and company objectives.• Created work orders for planned work. That included parts and work instructions, verified the kitting process.• Worked with the Scheduler to organize department schedules and work assignments.• Created and track purchase request for materials and services within the Maintenance Department. • Support all phases of the preventive maintenance plan using SAP for production equipment, maintenance plans, and task list.• Collected and recorded equipment information, including BOMs, OEM materials, and historical data. • Provided daily, weekly, monthly, and quarterly schedule reports to RWP Team.• Oversaw daily operation of PM Program, generating all planned and unplanned work orders, notifications, and part request.• Organize Facility Department’s annual end-of-year shutdown schedule. Aligned all department work plans and coordinated the multiple groups of outside contractors.• Modify and create work instructions and SOPs for preventative and corrective maintenance process, work order management, spare parts inventory control.• Create layout and design drawings using AutoCAD.
-
-
-
JLL
-
United States
-
Real Estate
-
700 & Above Employee
-
Operations Manager
-
May 2013 - Nov 2017
• In this management role, I oversee GMP maintenance to assure quality work performance and documentation compliance with FDA regulations, while leading a 16-member technical team in achieving completion at or about 100% monthly.• I ensure quality of work meets or exceeds company guidelines and timely completion of projects and duties in collaboration with contractors and service providers.• I also serve as site administrator for the Facility 360 and Apipro CMMS.• Next, I prepare FDA-required control documents to outline and clarify process and requirements for maintenance team. • In addition, I modify and create work instructions and SOPs for preventative and corrective maintenance process by working with the Alcon Quality Control Department, participate as member of Alcon site PSM quality team, and identify all potential safety and hazardous operations with equipment and in working environment.• Other essential tasks include: developing and implementing comprehensive preventive maintenance plan in compliance with all federal, state, and local codes, managing all Facility Department drawings, modifying existing drawing to update essential data, and organize Facility Department’s annual end-of-year shutdown schedule. • Finally, I improve service-level to client by working with Facility Manager, and JLL team.A key accomplishment includes:• Supporting audit-ready, everyday approach for areas by achieving 100% accuracy in work, including documentation, data entry, and other areas, as assigned.
-
-
Facility Planner Scheduler, CMMS Administrator
-
Mar 2013 - Feb 2016
-
-
-
Schwan's Company
-
United States
-
Food and Beverage Manufacturing
-
700 & Above Employee
-
Planner Scheduler
-
Aug 2011 - Jan 2013
• In this role, I led a team of 40 to 45 service technicians in ensuring production and facility equipment maintained to high standard of reliability.• Next, I encouraged and supported all production service technicians and production machine operators to assist in accomplishing their goals and company objectives.• I also created and tracked all purchase orders for Technical Services Department and spearheaded preventive maintenance plan using SAP for 625 pieces of production equipment, 1,4K maintenance plans, and 1.2K task list.• Additionally, I collected and recorded equipment information, including BOMs, OEM materials, and historical data, provided weekly, monthly, and quarterly schedule reports to Plant Manager, and oversaw daily operation of PM Program, generating an average of 400 planned and 290 unplanned work orders, notifications, and part request.A key achievement as Maintenance Planner/Scheduler included:• Serving as member of Extended Management Team, Vendor Selection Team, 5S Improvement Team Safety Committee, First Responders Group, and Equipment Support Team.
-
-
-
-
Maintenance Coordinator
-
Jan 2005 - Oct 2010
• As coordinator, I managed, supported, motivated, and led team of 18 production service technicians and 20 production machine operators in accomplishing goals as part of Maintenance Team, while leading daily operation of maintenance program, generating all planned and unplanned work orders, notifications and parts request. • I also provided weekly, monthly, and quarterly schedule reports to Production Manager. My key accomplishments included:• Creating database identifying inventory of $1.4M in spare parts to support production operations. • Developing infrastructure for production preventive maintenance plan, including 326 pieces of production equipment, 900 maintenance plans, 2.5K Task List, and 32K spare parts in collaboration with Integration team. • Preparing more than 400 work instructions and 260 service training Instructions to define and ensure all maintenance and process events following company SOPs.• Acting as member of Extended Management Team, Vendor Selection Team, 5S Improvement Team, Safety Committee, First Responders Group, and Equipment Support Team.
-
-
-
Capital Container
-
Brazil
-
Utilities
-
Maintenance Lead Technician
-
2001 - 2005
• With this company, I completed all phases of maintenance on automated corrugated presses, including multi-color die cutters flexographic folder gluers, and multi-stage conveyor systems.• In addition, I installed, calibrated, and troubleshot multiple process controllers, programmers, and data recorders used to control and document temperature, pressure, vacuum, and compressed air. • I also installed and maintained three phase power distribution and low voltage control power circuits while maintaining and controlling daily activities of preventive maintenance program for all manufacturing and facility support equipment. • Last, I documented all daily, weekly, monthly, and annual preventive maintenance work orders.
-
-
-
GKN Aerospace
-
United Kingdom
-
Aviation and Aerospace Component Manufacturing
-
700 & Above Employee
-
Lead Maintenance Technician
-
1990 - 2001
• With GKN, I utilized CMMS (MP/2) to produce and implement company's first preventive maintenance program for manufacturing and facility support equipment in three production facilities. • Next, I geometrically aligned 3-6 axis milling machines and routers, CNC machine controls. • I also worked with thermal compression molding presses (5-750 ton), process ovens, automated storage and retrieval systems, autoclave bonding equipment, and water jet cutting. • Finally, I coordinated facilities layout and design using AutoCAD. • Serving as member of ISO 9000, Kaizen, and Safety teams.
-
-
Education
-
Central Alabama Community College
Business Courses
Community
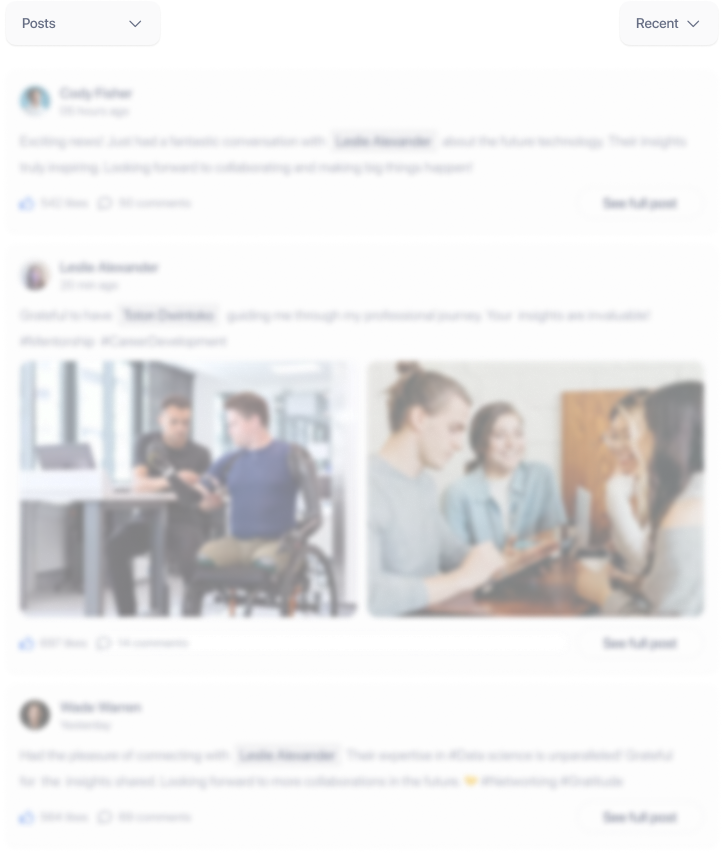