John Nelson
Sr. Technical Manager at Carlisle Fluid Technologies- Claim this Profile
Click to upgrade to our gold package
for the full feature experience.
Topline Score
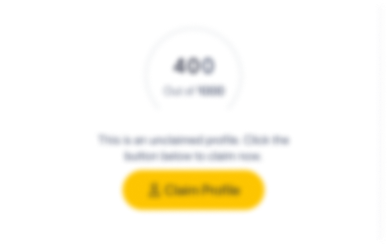
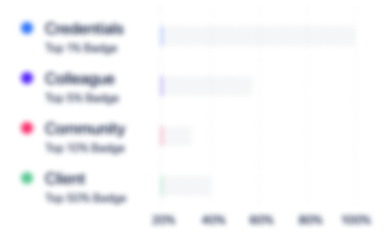
Bio


Experience
-
Carlisle Fluid Technologies
-
United States
-
Machinery Manufacturing
-
200 - 300 Employee
-
Sr. Technical Manager
-
Sep 2016 - Present
-
-
Sr. Technical Manager
-
Sep 2016 - Present
• Delivered process application improvements and new technology for rotary bells and fluid delivery in collaboration with R&D, providing mechanical design insight for product development.• Championed a 15% cost reduction for a major Tier One process line through improvements made to the trigger efficiencies for paint application robotics.• Supported Binks installation for a major O.E.M, resulting in a Defect Per Unit (DPU) decrease of 20% while completing the project on time and under budget.• Conducted root cause analysis for international clients, identifying issues and defects and advising clients on possible solutions for both established operations and newly launched facilities. Show less
-
-
-
Magna International
-
Canada
-
Motor Vehicle Manufacturing
-
700 & Above Employee
-
Staff Engineer, Paint
-
Sep 2013 - Sep 2016
• Maintained production readiness of all rotary and gun electrostatic atomizers, atomizer process controls, fluid delivery controls, paint circulation system, and all paint kitchen mix systems for both waterborne and solvent based paint formulations. • Managed production support on a daily basis, overseeing the paint application line and paint mix room while maintaining a 99.9% uptime for paint mix operations during tenure. • Spearheaded a variety of system improvements that drove a net increase in FTC greater than 8%, including the installation of new paint mix pumps across 65 systems. • Secured cost savings in excess of $1M annually through multiple initiatives, including increasing waterborne prime, base coat, and clearcoat application efficiency. Show less
-
-
-
-
Area Manager
-
Dec 2012 - Sep 2013
• Oversaw team of 40 in maintaining two Fanuc robot lines, two supporting paint mix rooms with 37 active systems, six fascia styles, two on-line inspection zones, and four repair zones. • Drove significant improvements in First Time Capability (FTC) through the reduction of scrap and repaints, meeting or exceeding department KPIs (SEQPDM). • Supported improved staff engagement and buy-in, fostering collaboration on internal improvement projects and leading training sessions. • Oversaw team of 40 in maintaining two Fanuc robot lines, two supporting paint mix rooms with 37 active systems, six fascia styles, two on-line inspection zones, and four repair zones. • Drove significant improvements in First Time Capability (FTC) through the reduction of scrap and repaints, meeting or exceeding department KPIs (SEQPDM). • Supported improved staff engagement and buy-in, fostering collaboration on internal improvement projects and leading training sessions.
-
-
-
-
Hyundai Mobis
-
Jan 2011 - Dec 2012
PAINT DEPARTMENT SUPERVISOR • Directed a 48-member staff on the paint production line, coordinating schedules and monitoring safety, quality, cost, and productivity on a daily basis, reporting data to management as needed. • Communicated any quality or equipment issues and maintained environmental compliance for the paint department, ensuring the safety of all team members in accordance with established regulations. • Developed and implemented process improvements that drove an FTC Quality Rating increase from 85% to 92% average per shift and an FTC Quality Ratio increase from 88% to a 93% average. Show less
-
-
-
Honda of America Mfg., Inc.
-
Automotive
-
700 & Above Employee
-
ATS, Paint Process Engineer
-
2006 - 2008
Served as Engineer / Team Leader for Paint Mix Operations with accountability for the operation of all paint mix circulation systems in Body Assembly and Bumper Plastics. Created and implemented procedures for New Model/Style within the Paint Department. Supported process equipment group, maintenance, and modification for consistency in New Model introductions. • Recognized as department expert in rotary bell applicators for solvent and waterborne applications. • Led Paint Material Team to improved system productivity and reduced cost for equipment maintenance in robotic and mix room systems by $500K. • Accountable for annual solvent loss reduction and decreased Volatile Organic Compound emissions by 20%. Show less
-
-
-
ABB
-
Switzerland
-
Automation Machinery Manufacturing
-
700 & Above Employee
-
Sr. Proces Engineer (Paint)
-
Jan 1990 - Jan 2006
Managed Paint Process Team in paint process solutions for both waterborne and solvent borne technologies. Applied process and procedures for color match to standard, paint pattern development, and increased transfer efficiency. Consulted with atomizer engineering group and provided technical expertise for design enhancements to the paint atomizer product line that included rotary bells and robotic guns. • Led Launch Team at the first electrostatic, indirect charge, waterborne automotive assembly paint system in North America. • Demonstrated expertise in process, programming, and troubleshooting of paint robots. Show less
-
-
Education
-
U.S. Marine Corps., 29 Palms, CA.
E.E.T., Electronics and Tactical Communication
Community
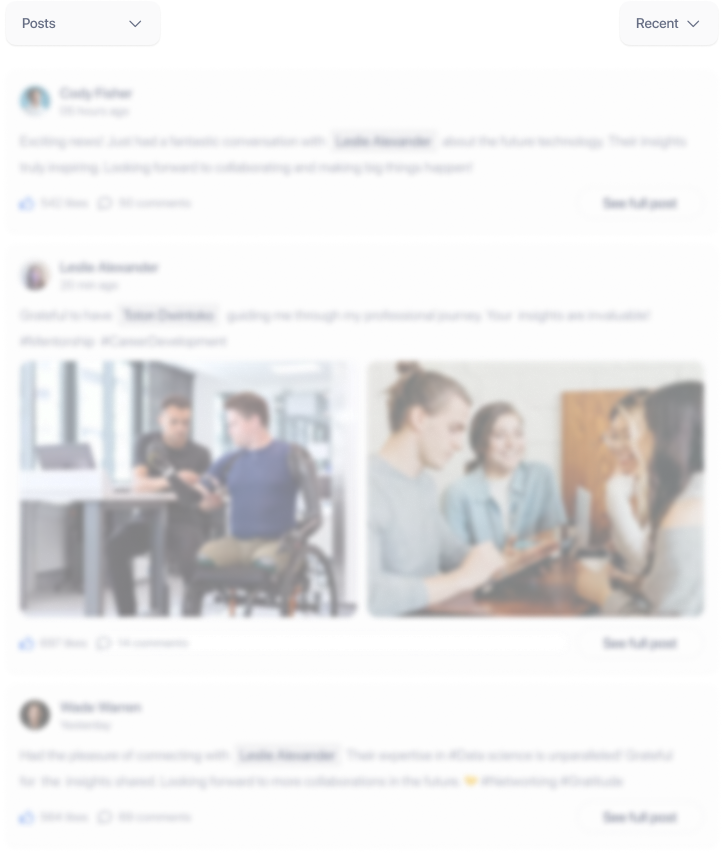