John Maynard
Program Coordinator / Mentor at Guilford Technical Community College- Claim this Profile
Click to upgrade to our gold package
for the full feature experience.
-
English -
-
Very little Spanish -
Topline Score
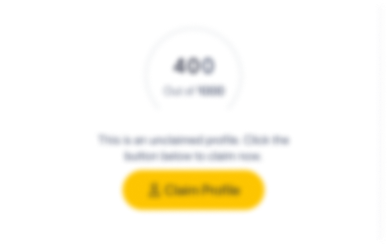
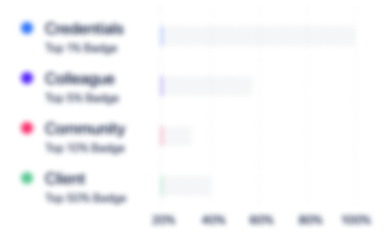
Bio


Credentials
-
Claims Adjuster
PearsonJul, 2020- Oct, 2024 -
Certified Life Agent
North CarolinaApr, 2014- Oct, 2024
Experience
-
Guilford Technical Community College
-
United States
-
Higher Education
-
700 & Above Employee
-
Program Coordinator / Mentor
-
Sep 2015 - Present
• Design and implement programs for student retention• Perform system to system reconciliation of student information• Student Mentoring• Organize Student Activities • Coordinate Student volunteering (Community Service Initiative)• Career planning and assistance• Co-coordinator of Minority Male Mentoring Program (R.I.T.E) • Design and implement programs for student retention• Perform system to system reconciliation of student information• Student Mentoring• Organize Student Activities • Coordinate Student volunteering (Community Service Initiative)• Career planning and assistance• Co-coordinator of Minority Male Mentoring Program (R.I.T.E)
-
-
-
Electrical Equipment Company (EECO)
-
United States
-
Wholesale
-
700 & Above Employee
-
Vendor Management
-
Dec 2015 - Aug 2020
Supply chain management I was responsible for inventory control and budgeting for over 60 manufacturing companies within the North Carolina, South Carolina, and southern Virginia areas.I was also tasked with the ordering and recognizing the need for special equipment and or temporary inventories. Daily task consists of visiting locations, maintaining site store rooms, reorders, communications with maintenance personnel and accounts payable. Supply chain management I was responsible for inventory control and budgeting for over 60 manufacturing companies within the North Carolina, South Carolina, and southern Virginia areas.I was also tasked with the ordering and recognizing the need for special equipment and or temporary inventories. Daily task consists of visiting locations, maintaining site store rooms, reorders, communications with maintenance personnel and accounts payable.
-
-
-
-
Assistant Director
-
Aug 2013 - May 2014
Employee evaluation• Hiring and termination of employees• Account Management • Billing Employee evaluation• Hiring and termination of employees• Account Management • Billing
-
-
-
-
SAP Logistics Coordinator
-
Feb 2007 - Aug 2013
• Managed crew of 9 employees• Organized the delivery of materials and supplies • Facilitated support to manufacturing line with tools and materials essential to production• Maintained an inventory Database that recorded product and tool locations throughout campus (S.A.P)• Communicated concerns from product line to Logistic Management• Maintained detailed log of wafer process and inspected wafers to ensure quality• Performed periodic tool maintenance • Managed crew of 9 employees• Organized the delivery of materials and supplies • Facilitated support to manufacturing line with tools and materials essential to production• Maintained an inventory Database that recorded product and tool locations throughout campus (S.A.P)• Communicated concerns from product line to Logistic Management• Maintained detailed log of wafer process and inspected wafers to ensure quality• Performed periodic tool maintenance
-
-
-
RF MICRO DEVICES UK LIMITED
-
United Kingdom
-
Defense and Space Manufacturing
-
Production Operator
-
Jan 2006 - Feb 2007
• Worked with silicon wafers through the Photolithography process• Maintained detailed log of wafer process• Worked with Process Technicians to refine certain Processes• Preformed periodic tool maintenance • Reprocessed error wafers to salvage good die• Inspected wafers for quality• Managed inventory flow through “whip graph” usage • Worked with silicon wafers through the Photolithography process• Maintained detailed log of wafer process• Worked with Process Technicians to refine certain Processes• Preformed periodic tool maintenance • Reprocessed error wafers to salvage good die• Inspected wafers for quality• Managed inventory flow through “whip graph” usage
-
-
-
AT&T Mobile Tel
-
United States
-
Wireless Services
-
700 & Above Employee
-
Customer Service Representative
-
Jun 2003 - Feb 2006
• Provided aide and relief to various team members• Coordinated training for quality improvement• Assist customers via phone with account / Mobile phone issues• Coached and mentored co-workers with adverse call ins• Effectively resolved issues while handling high call volumes and multiple computer programs• Offer troubleshooting and technical aid to mobile customers via phone • Provided aide and relief to various team members• Coordinated training for quality improvement• Assist customers via phone with account / Mobile phone issues• Coached and mentored co-workers with adverse call ins• Effectively resolved issues while handling high call volumes and multiple computer programs• Offer troubleshooting and technical aid to mobile customers via phone
-
-
Education
-
Guilford College
Bachelor of Applied Science (BASc), Business Administration and Management, General -
Guilford College
Bachelor of Science (BSc), Business Administration, Management and Operations
Community
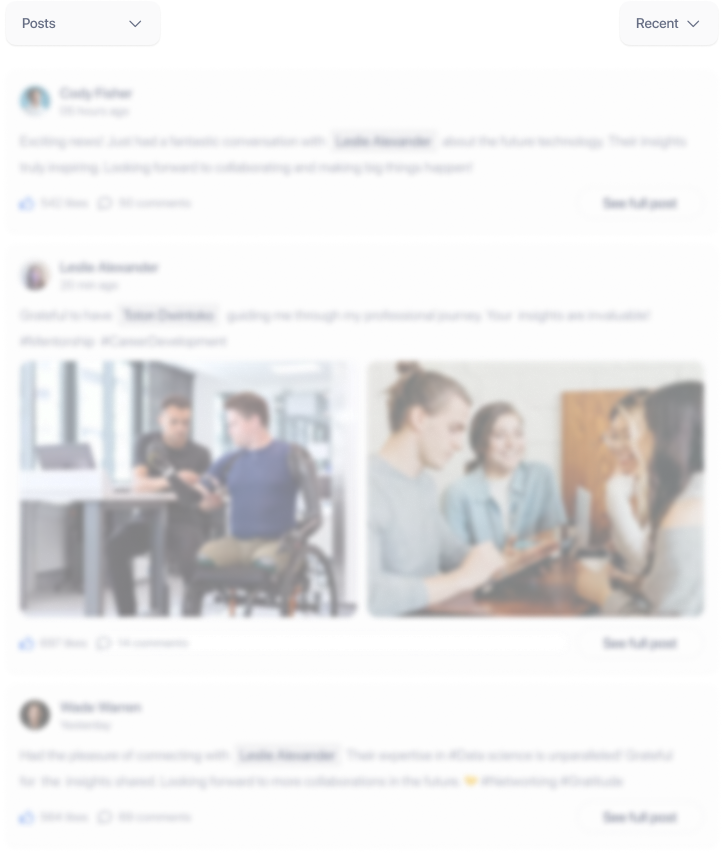