John Cournoyer
Senior Mechanical Engineer at Gener8- Claim this Profile
Click to upgrade to our gold package
for the full feature experience.
Topline Score
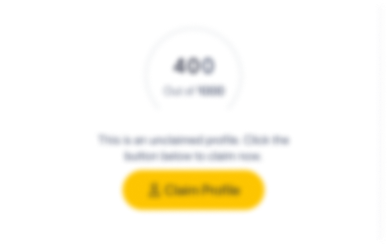
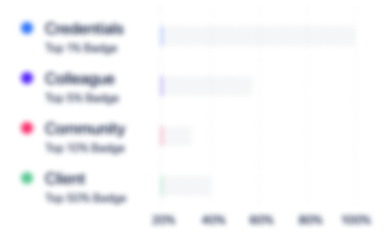
Bio
0
/5.0 / Based on 0 ratingsFilter reviews by:
Experience
-
Gener8
-
United Kingdom
-
Software Development
-
1 - 100 Employee
-
Senior Mechanical Engineer
-
Jul 2021 - Present
Gener8 Designing and Manufacturing of Instruments and Consumables Serving the BIOTECH, MEDICAL, and INDUSTRIAL Markets Gener8 Designing and Manufacturing of Instruments and Consumables Serving the BIOTECH, MEDICAL, and INDUSTRIAL Markets
-
-
-
Velico Medical, Inc.
-
United States
-
Medical Equipment Manufacturing
-
1 - 100 Employee
-
Principal Mechanical Engineer
-
Oct 2017 - Jul 2020
- Hired at a time the project’s Research and Design tasks were already 6 months behind. Worked 7 days a week for 6 weeks to deliver several, critically needed design iterations. - Used an Engineering Test Apparatus to simulate the systems main 3’ long disposable. - Worked closely with test technicians and Scientists to make many changes needed on the fly. - Created/modified designs in the machine shop myself or had machined parts out at local Vendors. - Controlled fixture parameters consisting of varying pressures, high temperatures, aerosolization parameters of plasma, filtration, and powder collection techniques. - Placed 15 ‘temperature indicating’ labels all throughout the disposable. Provided accurate thermal map of peak temperatures reached inside the disposable when heated air passed through it. - Once successful yields were achieved, commercialization of the system commenced. - Worked closely with the converter company that assembled the disposable, the two injection mold houses, and the design firm making the Instrument (pressure vessel). - Maintained role of design liaison for all activities related to the disposable - Other activities included creating and maintaining the BOM and creating Regulatory Document Packages in preparation of our Clinical Submission to the FDA.
-
-
-
Ximedica
-
United States
-
Medical Equipment Manufacturing
-
1 - 100 Employee
-
Sr. Mechanical Engineer
-
Apr 2014 - Oct 2017
Project A (118 weeks): - Led a diverse, cross-functional Team of, Mechanical, Manufacturing, Electrical, Software, & Engineers, and Industrial Designers to design and build 4 patient carts targeted for Urological Surgery. Robots were operated from a workstation outside the operative field. - Designed boom arms with electro-mechanical brakes, enclosures for computer, optics, brake systems for casters, Ingress protection (ISTA), EMI Isolation. - Worked closely with Industrial Designers to determine surfacing of “Looks like” model. Also worked with a off-shore Design group consisting of Electrical, Software, and Mechanical Engineers. - ANSI 60601, Human Factors Guideline HE75. Project B (15 weeks): - Developed a handheld electro-mechanical atomizer to deliver precise amount of drug to eye via micro-fluidics. - Worked closely with Clients to develop a works-like model of the system. - Activities included custom O-ring selection, shutter design and timing events of shutter and contact sensors. Project C (28 weeks): - Characterized wearable, neck collar that minimized concussions by applying a load to both carotid veins, which in turn, minimized the blood flowing back to the heart. Results in cushioning brain in a pool of blood. - Upgraded fatigue fixture to cycle collars through sinusoidal loading. Developed a spring constant force fixture to characterize collars performance before and after fatigue testing. Tested different collar sizes and determined that smaller collars were deflecting beyond its elastic limit Project D (8 weeks): - Heat Study to determine maximum temperature reached and heating/ cooling rates of a light curing cement used in dental applications. Used phase change material (pcm) heat sinks to prevent overheating and thermocouples to map out the heat profile.
-
-
-
-
Principal Engineer
-
Nov 2010 - Mar 2014
Concept Development Group - Conceptual design of Labrum, Rotator Cuff and ACL Reconstruction Projects. - Concepts ranged from Anchors, Sutures, related instruments, mostly disposables. - Conducted several brainstorming sessions. - Utilized different forms of media such as foam boards, paper, sheet metal, clay, instant moldable plastic, plastic and metal SLA’s to create several iterations of prototype assemblies. - Used prototypes for bench top and cadaveric evaluations, testing, and voice of customer. - Presented successful concepts to patent review board. - Improved upon time it takes to make prototypes from weeks to hours. - Working from clearly defined User Needs, created problem statements based around these needs and verified with Surgeon Team. - Utilized Systematic Design Methodologies to bring new concepts across several pathologies. Resulted in winning 2 Design contests vs. 25 other Engineers. - Created a comprehensive Mindjet Mindmap of 500+ factors involved in rotator cuff repair. Initially, collected feedback from colleagues and verified content with Surgeons. Great platform for VOC.
-
-
-
-
Principal Engineer
-
Jan 2005 - Jun 2010
• Further design refinement activities on Head-to-Head Cross Connector, Ring Nut Implant, and related Instruments from below. • From 2006 to 2010, Independent Reviewer for 7 Projects. Performed auditing of all DHF activities related to Stage Gate review. • Participated in Lean Process Mapping activity to revamp DePuy Spine’s Product Development Process. Staff Engineer, 2005 – 2009 NX Unigraphics CAD • Led design activities in further expanding the Expedium 4.5 and 5.5 family by designing Head to Head Cross Connector, Ring Nut, and related Instruments. Successfully manufactured prototypes in time for a surgeon team meeting and received feedback to finalize designs. • Led a Project Team on Company’s largest Expedium Pediatric Deformity System (1500 codes). Included solutions for idiopathic, congenital, neuromuscular and syndromic disease states for children from 18 months to 13 years of age. Incorporated feedback from 7 Designing Surgeons for all implants and instruments. Considered most comprehensive pediatric system in the world at the time. Designs included polyaxial, monoaxial screws, & uni-planer screws, hooks, cablewire screws, bolts & offset connectors, dual diameter rods and connectors, SFX cross connector, extendable connector for growing spine, and instruments. Conducted Ansys FEA simulation on test fixture for growing spine connector.
-
-
-
-
Staff Engineer
-
Jan 1998 - Jan 2002
Senior Product Development Engineer, 2002 – 2005 NX Unigraphics CAD • Worked primarily on the strategy, logistics, test plan, and determined FDA route for the Expedium 510(k) submission. Provided Technical support to Engineers and Designers. Products include Single and Dual Inner screws, hooks, mono screws, sacral extenders, and instruments. • Project Manager of the Single Innie Project, whose importance was recognized at the corporate level. Main design tasks were to convert the double fastener design to a single fastener system. Developed a method to machine the threads that resulted in significantly less head splay compared to competitor screws. Product eventually became the Expedium Product Family, whose revenue to date grossed over 3.2 Billion in revenue. Utilized Ansys FEA to minimize head splay. • Submitted Patent on a driver that simultaneously applies 2 fasteners to a screw head in a timed manner. PRODUCT DEVELOPMENT ENGINEER, 2000 – 2002 NX Unigraphics CAD • Team leader for the Moss Max spinal instrument set. Successfully employed a new design interactions methodology for the Design Engineers to follow. Resulted in having a full instrument set within 5 weeks. • Project Manager of the large-scale, MOSS Miami Advantage Project Team challenged with the tasks of design of the Pin Nut, Kangaroo Cartridge, high thoracic and extended length screws, and Instruments. • Joined the Moss Miami Magnum team and provided engineering support on the ergonomic, modular instrumentation with the ¼” Spinal Rod System. Incorporated feedback from key surgeons. • Worked with outside design firm to develop an instrument for inserting 2 fasteners, simultaneously.
-
-
-
-
Research Engineer
-
Jan 1998 - Jan 1999
RESEARCH ENGINEER, 1998 – 2000 NX Unigraphics CAD • Joined Testing Group during the time that Depuy AcroMed was relocating from Cleveland to Raynham, MA. Successfully designed the layout of the lab full with test frames & servo-hydraulic pumps. Coordinated all electrical, plumbing, and servo hydraulics service efforts on time. • Provided static and dynamic testing for all Pathology groups in Spine R&D. Projects included PEEK/UltraPek materials classification, Interbody Fusion cages, Rod/ Screw constructs, PLA cervical cages, Autograft bone cages, and mesh cages. • Performed gait analysis on a cadaveric knee specimen at Purdue University. Knee was mounted to a knee gait simulator fixture and was controlled by an Instron Test Frame.
-
-
Education
-
Northeastern University
BS, Mechanical Engineering
Community
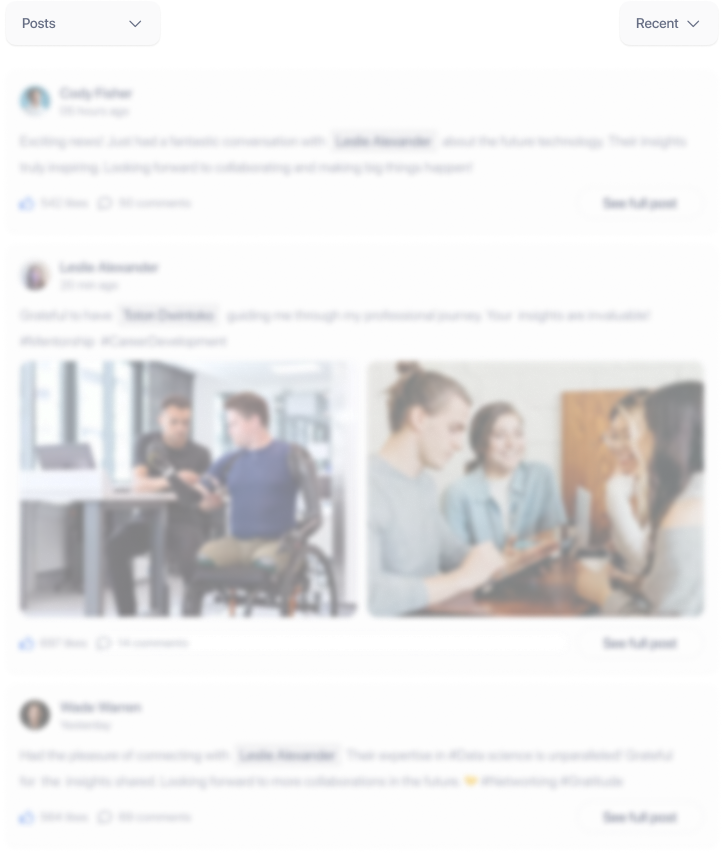