John Condon
Manager, GMP Quality Assurance at Blueprint Medicines- Claim this Profile
Click to upgrade to our gold package
for the full feature experience.
Topline Score
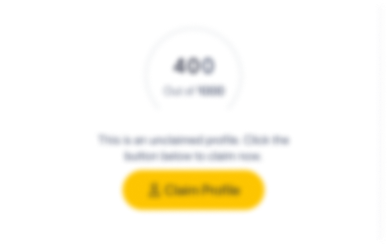
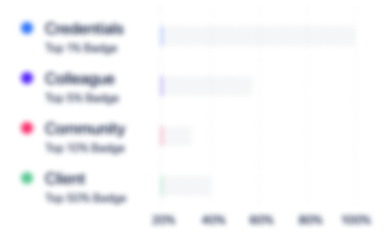
Bio


Experience
-
Blueprint Medicines
-
United States
-
Biotechnology Research
-
400 - 500 Employee
-
Manager, GMP Quality Assurance
-
Mar 2022 - Present
-
-
-
Deciphera Pharmaceuticals
-
United States
-
Pharmaceutical Manufacturing
-
200 - 300 Employee
-
Manager GMP Quality Assurance
-
Nov 2019 - May 2022
• Managed and executed the review, approval and release of clinical trial drug products • Review and approval of drug product master batch records and executed batch records for bulk drug product manufacturing and primary packaging. • Change control management, review, approval and closure • Primary contact with Contract Manufacturing Organizations (CMO,) Project Management teams and Quality Assurance teams • Primary contact with internal Supply Chain teams for product release and distribution scheduling • Represented Quality Assurance on project team meetings to provide GMP guidance on change control requirements, batch review and release timelines, and clinical product expiry extension requirements • Responsible for clinical trial product deviation reviews root cause analysis, corrective and preventive actions, product impact assessment, trend analysis, approval and closure
-
-
-
Alkermes
-
Ireland
-
Biotechnology Research
-
700 & Above Employee
-
Sr. Quality Assurance Associate
-
Mar 2014 - Oct 2019
• Managed and executed the review, approval and release of six clinical trial drug products • Active Pharmaceutical Ingredient (API) master and executed batch records • Drug Product master and executed batch records for primary packaging, final packaging, kitting and labeling • Deviation assessment, review and approval • Change order/Change control review and approval • QP release support for European Union (EU) distribution • Labeling review and approval for multiple countries • Primary contact with contract manufacturing organizations’ (CMO) Project Management teams and Quality Assurance teams • Primary contact with internal Supply Chain teams for product production scheduling, product release and distribution scheduling • Manage clinical trial product complaints system • Prepare and present monthly Quality Metrics to senior management • Quality Assurance representative to the site team implementing TrackWise systems (electronic deviations and product complaints databases) including internal change control requirements, computer system validation (CSV) support, and training of site personnel on system use and requirements • Responsible for clinical trial product deviations, manufacturing investigations, root cause analysis, corrective and preventive actions, product impact assessments, trend analysis and closure • Lead Auditor on Contract Manufacturing Organization (CMO) auditing and vendor/supplier auditing
-
-
-
Sanofi Pasteur Biologics
-
Canton, Ma
-
Manager, Quality Assurance
-
Aug 2009 - Feb 2014
• Managed direct reports/associate level staff for Quality Assurance product release responsibilities • Managed and executed batch release to meet project timelines and customer commitments • Managed review and disposition of raw materials and manufacturing components, issuance of Quality release documentation and product certificates of analysis • Managed and executed product intermediate (bulk drug substance and bulk drug product) review and release including batch record closure, QC test result review, deviation and change control closure • Performed cGMP auditing of external vendors, suppliers and contract manufacturing organizations (CMO) and contract test laboratories • Supported Compliance activities through execution of the following systems: • Deviation investigations, CAPA resolution and closure • Change Control review and closure • Review of IQ/OQ/PQ Validation protocols and reports for process validation, equipment validation, cleaning validation, QC test method validation • Product Complaints Officer for the site • Investigation leader for product complaint driven Manufacturing Investigations • Monitoring, tracking, reporting Quality metrics for continuous improvement • Participate in FDA inspections including: • Training staff on inspection procedures and guidance • Subject matter expert on QA release systems, batch record review, Product Complaint handling, Raw Materials systems • 483 Response development, execution and closure
-
-
-
Acambis,, Inc
-
Canton, MA
-
Supervisor, Quality Assurance
-
Aug 2001 - Feb 2014
Supervisor, Quality Assurance; Product Quality • Supervise QA Associate level staff responsible for Product Release systems including review of Batch Production Records, QC test results, Environmental Monitoring data and Deviation closure • Oversee CMO/Person-in-plant QA responsibilities including role development, immediate action and communication responsibilities, real-time batch review, deviation resolution • Manage Raw Materials review and release systems including QC test results review and electronic inventory management system (SAP) operations • Manage the Material Review Board function • Ensure timely lot release to meet project timelines, and customer commitments • Continuous improvement initiatives: • Reduce lot release cycle times • Conduct training/guidance sessions to improve compliance with QA and Manufacturing procedures and systems • Improve lot release data capture and metrics reporting • Support Compliance related activities through execution of the following systems: • Deviation resolution and closure • External CMO, Test Lab and Vendor auditing • Internal cGMP Auditing • Participate in FDA inspections including: • FDA Inspector escort and scribe responsibilities • SME responsibilities for QA Release systems • 483 Response team Aug. 2001 to Acambis, Inc July 2007 Canton, Ma Associate II, III, IV, Quality Assurance • Co-develop and implement product release systems including review of manufacturing batch records, media and solution prep. records, QC results, contract manufacturer (CMO) records and deviations • Develop, review and revise QA and manufacturing documentation in support of the above functions • Develop product labeling materials • Prepare and issue product CoAs • Internal cGMP auditing and vendor and contractor auditing • Review and release of raw materials • Operate quality systems including deviation reporting and investigations
-
-
Education
-
Massasoit Community College
Associate of Arts - AA, Honors, Liberal Arts and Sciences/Liberal Studies
Community
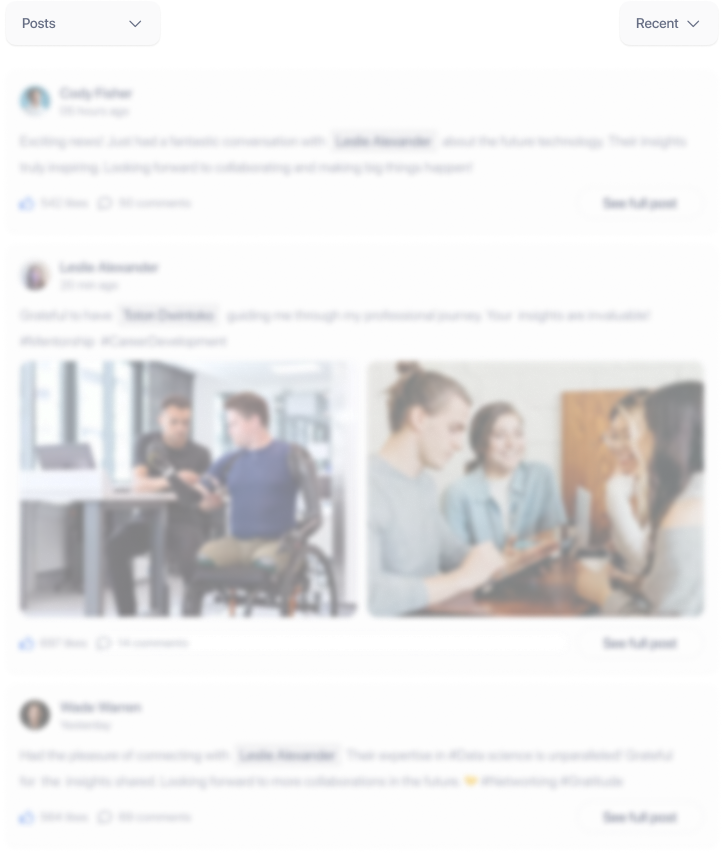