John Byers
Operations Manager at Summit Packaging Solutions- Claim this Profile
Click to upgrade to our gold package
for the full feature experience.
-
English -
Topline Score
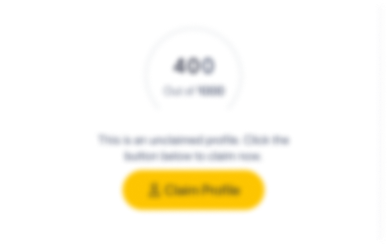
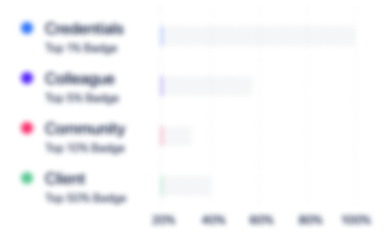
Bio


Experience
-
Summit Packaging Solutions
-
United States
-
Packaging & Containers
-
1 - 100 Employee
-
Operations Manager
-
Nov 2022 - Present
Business Responsibility · Leading 3rd shift co-pack operation within Procter and Gamble location. · The scope of operation is building/assembling and packing promotional displays varying in size from shelf displays to full pallet displays. · Mentoring and leading multiple salaried leaders, agency supervisors, company employees. (Salaried 2 direct/3 indirect, 2 agency supervisors, and 15 summit leads/indirect positions.) · Managing and planning for widely fluctuating volume, from 45 individuals running 4 operational lines up to 85+ individuals running 7 operational lines during peak. Operations/Compliance/General Management · Corrected and calibrated safety culture of 3rd shift to correct negative trend. · Established clear handoff expectations and feedback process with 1st shift team. · Established culture of communication and accountability regarding efficiency and quality metrics. Metrics updated and provided to team daily. · Adapted to working in an environment in which the majority of the workforce is from multiple temp agencies, bringing in individuals with a wide variety of life experiences and challenges. Show less
-
-
-
-
Production Supervisor
-
Jun 2020 - Nov 2022
Business Responsibility · Adapted to and effectively managed a diverse workforce of many ethnic groups, speaking in excess of 7 different languages. Leveraged technology and bilingual team members. · Supported the successful startup of 2 production lines on newly created 3rd shift, from training through running 2 lines from picking through loading of finished goods. · Manages and oversees backorder process and dynamic fulfillment for dealer channel product line for our entire service area. · Actively contributes to Gemba meetings, Kaizens, operational changes, and project planning by giving direct feedback, using logical reasoning, demanding accountability, taking ownership, challenging processes, and developing solutions. Operations/Compliance · Led new/less senior 3rd shift team to successfully ramp up to consistently out perform more experienced teams on 1st and 2nd shift. (35-65 team members) · Led dealer channel production lines through pandemic related challenges while, reinstating 6S standards, improving working conditions, and ramping up volume. (30-35 team members) · Actively monitored finished goods quality through direct observations, real-time feedback, and close partnership with Quality Assurance team. General Management · Partners effectively and mentors new leads and supervisors particularly in regards to feedback, development, problem-solving, and addressing team member issues and conflicts. · Seeks and promotes innovative solutions/improvements in own area as well as in other departments/project areas. Examples: packaging waste disposal, scanner utilization, label control, and development of tools in excel and Thingworx systems. · Coordinates and communicates effectively across departments and functional areas. i.e. Operations, Customer service (HQ), QA, CI, Maintenance, and 3PL partners. Show less
-
-
-
Schreiber Foods
-
Food and Beverage Manufacturing
-
700 & Above Employee
-
Production Supervisor
-
Mar 2017 - May 2020
Business Responsibility · Developed and led a successful center line project to address PE deficiencies after changeovers, between different format packaging. · Simplified finished goods scrap reporting based on systemic processes and equipment capacity to increase accuracy, reduce waste and limit partner errors. · Participated in the successful integration of a non-dairy product line into a dairy facility. · Supported the relocation and startup of a bottle production line to local plant from across the country. Operations/Compliance · Leads filling and packaging department in a dynamic co-manufacturing operation that produces various types of yogurt in a variety of formats. (25- 30 partners depending on volume) · Conducts daily update meetings with partners in addition to coaching by walking around. · Monitors and drives accountability of preventative controls as well quality procedures through partner interactions and auditing of production documentation. General Management · Partners effectively with quality team, maintenance, and engineering to address issues and adapt to an ever changing manufacturing environment. · Efficient at addressing and mitigating risk during foreign material incidents. Show less
-
-
-
Ventura Foods
-
United States
-
Food and Beverage Manufacturing
-
700 & Above Employee
-
Production Supervisor
-
Dec 2015 - Mar 2017
Business Responsibility · Created a digital cut batch tracking system to increase raw ingredient inventory accuracy, expedite ingredient use, and reduce waste. · Improved overall pre-weigh efficiency across shifts in the spice room by developing a sustainable performance tracking system to evaluate unmonitored processes. · Key partner in the development and roll out of multi-level bill of materials inventory project. · Supported the roll out of automated Informance/IFA system for real-time tracking of OEE% Operations/Compliance · Lead the Spice Room and Bulk oils departments. (21 employees and one lead) · Transitioned to lead the Portion Control (Pouches and Cups) and Bulk oils teams through rapid expansion. (45 employees and two leads) · Active member of the safety team. · Conducts daily safety and performance meetings with production team. General Management · Communicates effectively across departments and shifts. · Coordinates daily with quality assurance, maintenance, and contractors to balance building expansion/construction with production requirements. · Coaches by walking around. Show less
-
-
-
-
Distribution Area Supervisor
-
Apr 2013 - Nov 2015
Operations · Manages a team of 40-55 union associates (manual and automated line receivers, equipment operators, researchers and support personnel). · Main area of responsibility is managing, trouble shooting, and maintaining twelve automated receiving lines. · Coordinates trailers between manual and automated operation to ensure maximum cost savings and efficiency. · Cross trained in high volume repack department for operational support during peak season. Business Responsibility · Continuous Improvement committee member · Administering associate recognition program “Notice of Distinction” · Executing the barcode graphics compliance program to ensure and improve vendor integrity. · Leading problem freight research initiative to expedite getting product to the stores, while root causing issues and evaluating processes to limit future issues. · Administering “Logistics Performance Program” to address performance deficiencies to common expectation. Operations/Compliance · Manages a team of 40-55 union associates (manual and automated line receivers, equipment operators, researchers and support personnel). · Main area of responsibility is managing, trouble shooting, and maintaining twelve automated receiving lines. · Coordinates trailers between manual and automated operation to ensure maximum cost savings and efficiency. · Cross trained in high volume repack department for operational support during peak season. Show less
-
-
-
Office Depot
-
France
-
Retail Office Equipment
-
Area Operations Manager
-
Feb 2010 - Mar 2013
Business Responsibility · Implementation and continuous improvement of exceptional 5S program and standards. · Trained in Kaizen process / Co-lead of major Kaizen event which provided a 52% increase in value added tasks in addition to increased performance. · Improved and maintained positive PI improvements month over month and year and year over year, reducing labor and increasing performance. · Areas of responsibility include Outbound manager, Batch Cage manager (Technology division supporting high dollar retail sales), and Receiving/Chain of Custody manager. · Actively supports a culture of continuous improvement in operations, 5S and Safety. Operations/Compliance · Developed and implemented a building wide communication program. · Developed and implemented a safety/compliance walk for all group leaders to complete and report on daily, to address increasing concerns in building. · Responsible for Retail operations scorecard for our service area. Researching and resolving any inventory discrepancies. · Managed Dematic sortation system during building setup and through ongoing updates. Also played a key role in maintaining numerous technical components of Warehouse Management systems, Inventory Management systems, and Smart Label printers and applications. Show less
-
-
Education
-
Shippensburg University of Pennsylvania
Bachelor's degree, Psychology
Community
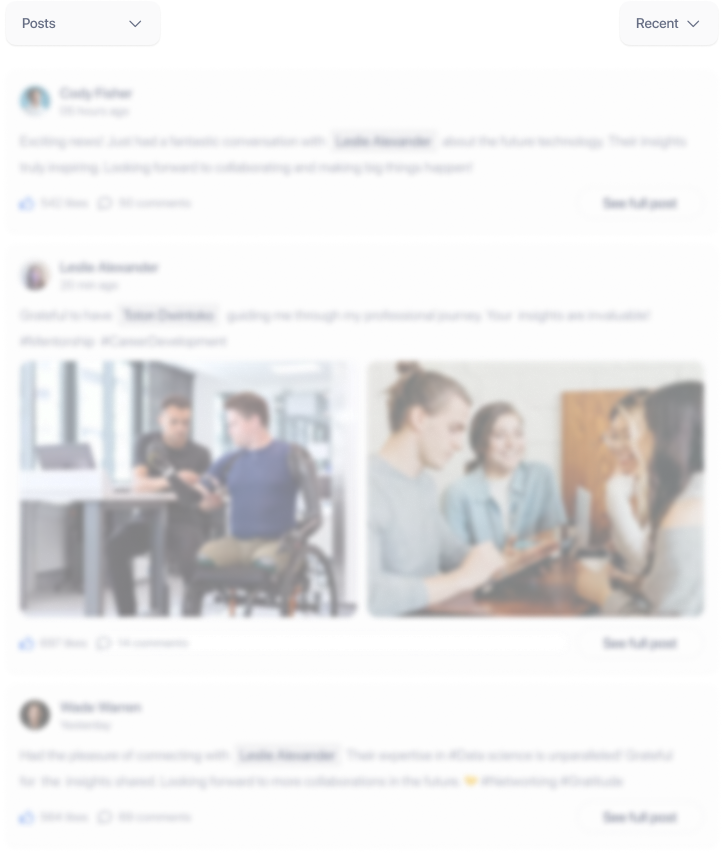