Johan Twaalfhoven
NPD Project Manager at SC Johnson Europlant- Claim this Profile
Click to upgrade to our gold package
for the full feature experience.
Topline Score
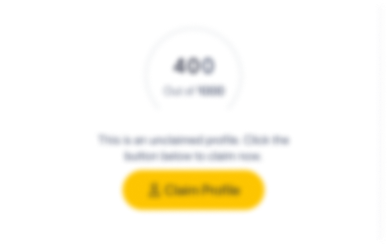
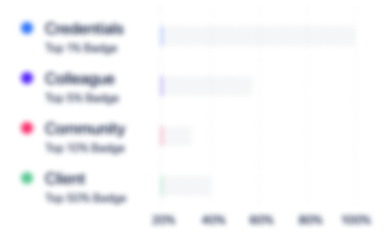
Bio


Experience
-
SC Johnson Europlant
-
Manufacturing
-
300 - 400 Employee
-
NPD Project Manager
-
Jul 2018 - Present
The single point of contact between Europlant and its business partners in relation to New Product Development and other external driven projects, such as supplier changes and cost savings.Also responsible for coordinating Europlant personal and activities to ensure NPD's and projects are completed correctly and on time. Primary Accountabilities:- Build key relationships with customers and stakeholders related to their projects.- Field all external questions about Europlant EP manufacturing capabilities and properly direct questions to correct people/departments.- Attending monthly meetings with regards to S&OP and Tech reviews.- Enter projects in MOC system- Indentify which EP resources are needed to ensure succesfully implementation.- Coordinate resource utilization- Coordinate project teams and manage project timelines to ensure projects are completed on time.- Scheduled line trials in coordination with Planning Department. Show less
-
-
Jr Quality Improvement Engineer
-
Jun 2015 - Jun 2018
Moved to the Quality Department and received an internal training to become a Jr Quality Improvement Engineer reporting to the Quality Manager.In this new role I was responsible for:- the quality insurance of incoming components.- contact with suppliers when delivered components did not meet the specifications.- Finding out the root cause when components caused issues in production and sharing this with the relevant suppliers and Engineering/Maintenance.
-
-
PAC planner / Artwork Coordinator
-
Jun 1999 - May 2015
PAC - Production Activity Control PlannerPrimary tasks as PAC Planner: - smooth daily production planning- create optimal weekly production plan per line- create, improve & update efficiency/capacity figures that support management & team leader decisions- control maintenance & quality issues- daily contact with workforce for overall output improvements- continuous improvement of the Planning Wheel- backup for Vendor Scheduler Primary tasks as Artwork Coordinator:- mapping new artwork related projects- sharing new artwork project details and timelines with the Business Team members- monitoring time -and deadlines of the artwork availability- regular contact with design and repro houses with regards to issue solving and timings- regular contact with printers/suppliers of printed components in collaboration with the Vendor Scheduler - deliver data to Vendor Scheduler for Vendor rating- responsible for setting up print & apply artworks and online printed artworks Show less
-
-
Superuser implementation ERP package BPCS
-
Aug 1997 - May 1999
As a superuser I was responsible for mapping the logistics processes (Finished Goods from production area via palletizing, storage, export planning and loading) for both Manufacturing SCJ Europlant in Mijdrecht as Manufacturing SCJ Frimley UK. Based on mapped processes I wrote prototype scenarios to be tested in BPCS test environment.After prototyping I was also responible for training the logistic colleagues, go live and aftercare.
-
-
Export Planner
-
Jul 1996 - Jul 1997
Responsible for compiling and booking Finished Goods, including shipping and customs documents, to various distribution centers within Europe based on production vs customer orders.
-
-
-
Multifill, Masters in Mixing & Filling
-
Netherlands
-
Chemical Manufacturing
-
1 - 100 Employee
-
Export expert
-
Sep 1994 - Aug 1996
Multifill is a contract filler for, among others, SC Johnson. I was responsible for setting up the distribution process, especially for SC Johnson-produced products, after SCJ had indicated that the central transport planning for all contract fillers, done from Mijdrecht, would end. Purchased software package for making the required export documents needed for shipping products to various countries plus a package to plan and execute the freight. Multifill is a contract filler for, among others, SC Johnson. I was responsible for setting up the distribution process, especially for SC Johnson-produced products, after SCJ had indicated that the central transport planning for all contract fillers, done from Mijdrecht, would end. Purchased software package for making the required export documents needed for shipping products to various countries plus a package to plan and execute the freight.
-
-
-
Amtron BV
-
Houten
-
Warehouse Manager
-
Jan 1992 - Aug 1994
Amtron was a distributor for various major computer brands, hardware and software. Responsible for incoming goods, warehouse management, repair and service department. Amtron was a distributor for various major computer brands, hardware and software. Responsible for incoming goods, warehouse management, repair and service department.
-
-
-
SC Johnson Europlant
-
Manufacturing
-
300 - 400 Employee
-
Export Planner
-
Jan 1991 - Jan 1992
Responsible for compiling and booking Finished Goods, including shipping and customs documents, to various distribution centers within Europe based on production vs customer orders. Responsible for compiling and booking Finished Goods, including shipping and customs documents, to various distribution centers within Europe based on production vs customer orders.
-
-
-
Indesit Company
-
Manufacturing
-
700 & Above Employee
-
Distribution Manager
-
Jan 1989 - Dec 1990
Responsible for incoming goods from factories in Portugal and Italy. Responsible for distribution of customer orders within the Benelux and contacts with carrier. Responsible for stock management with 3 warehouse staff reporting to me. Responsible for incoming goods from factories in Portugal and Italy. Responsible for distribution of customer orders within the Benelux and contacts with carrier. Responsible for stock management with 3 warehouse staff reporting to me.
-
-
-
Via Randstad at SC Johnson Europlant
-
Mijdrecht
-
Logistics Employee
-
May 1988 - Jan 1989
Responsible for stock management of finished goods. Being the backup at export planning department during holidays or illness. Responsible for stock management of finished goods. Being the backup at export planning department during holidays or illness.
-
-
-
Various Steel Fix companies
-
Various
-
Steel Fixer
-
Oct 1979 - Jul 1986
Construction projects worked on: Architectural Cube houses Rotterdam Headquarters Rabobank Utrecht Railway connection/bridge from Muiderberg to Flevoland Sluice Almere Haven Construction projects worked on: Architectural Cube houses Rotterdam Headquarters Rabobank Utrecht Railway connection/bridge from Muiderberg to Flevoland Sluice Almere Haven
-
-
-
Ringeling Engineering Works BV
-
Mijdrecht
-
Engine Fitter
-
Jul 1976 - Oct 1979
Making of various machine parts for agriculture and paint industry based on technical working drawings. Making of various machine parts for agriculture and paint industry based on technical working drawings.
-
-
Education
-
Gevaarlijke Stoffen Training & Advies BV
Bewustmakingstraining ADR/CLP/PGS, Gevaarlijke Stoffen -
PBNA
VOL-VCA, Safety -
CoThink
Kaizen Facilitator Training, Geslaagd -
ProQua
APICS CPIM BASICS, Logistiek en supply chain -
ISWB Opleiding en Training
Logistiek Management, Logistiek en supply chain -
Administrative Reintegration retraining
Secretary, Successful -
Smecoma
Smecoma Vakbekwaamheid metaalbewerking, 8 -
Lagere Technische School
Metaalbewerking, Geslaagd
Community
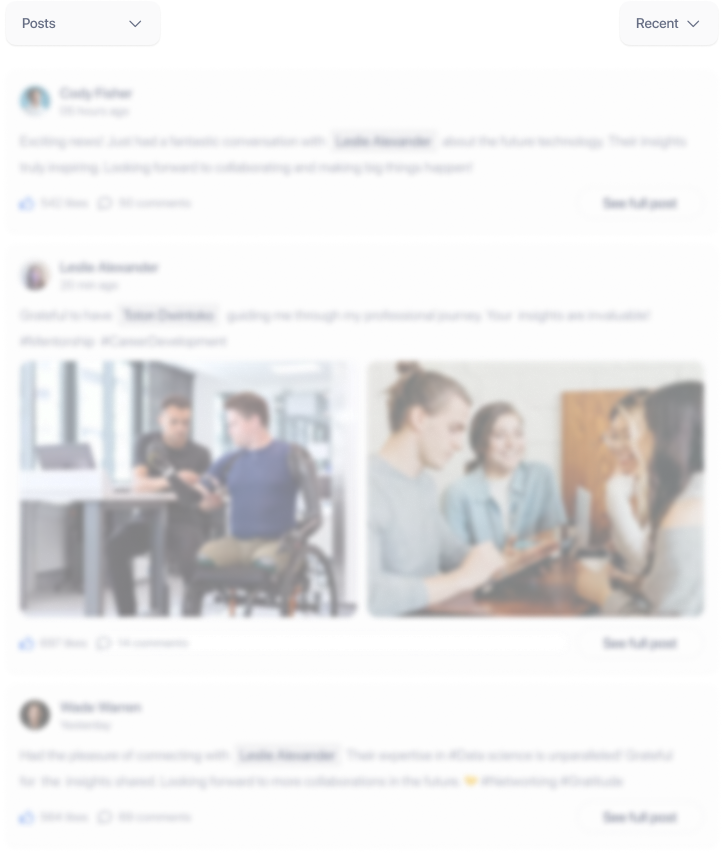